Сейчас ваша корзина пуста!
Анализ эксплуатационной стойкости рельсов и факторов, влияющих на нее
Цикл статей:
Введение
Глава 1 — Анализ особенностей промежуточных рельсовых скреплений
Глава 2 — Анализ эксплуатационной стойкости рельсов и факторов, влияющих на нее
Глава 3 — Оценка влияния конструкции и состояния промежуточных скреплений на состояние рельсов в эксплуатации
Глава 4 — Расчет влияния жесткости промежуточного рельсового скрепления на накопление контактно-усталостных повреждений
Глава 5 — Оценка эффективности функционирования конструкций верхнего строения пути
Заключение
Эксплуатационная стойкость рельсов, ее составляющие
В рельсах в процессе эксплуатации по мере наработки тоннажа, измеряемого в млн т брутто, происходят процессы износа, смятия, коррозии и усталости, в том числе контактной, крутильной и коррозионной усталости. В результате протекания этих процессов в рельсах образуются различные повреждения и дефекты[9]. Дефект рельса характеризуется отклонениями от установленных норм его геометрических параметров или прочности, соблюдение которых обеспечивает работоспособное состояние рельса в установленных условиях эксплуатации. К дефектам рельсов относятся: выкрашивания, выколы, трещины, изломы, все виды износа, пластические деформации в виде смятия, сплывов металла головки рельса, коррозия, механические повреждения, величины которых превышают нормированные значения.
Отказ рельса вызывается дефектом, при котором исключается пропуск поездов (полный отказ, например, при изломе рельса) или возникает необходимость в ограничении скоростей движения поездов (частичный отказ, например, образование волнообразных неровностей сверх нормируемых значений на поверхности катания головки рельса и т.п.)[31].
Повреждаемость рельсов контактно-усталостными дефектами и износом зависит от совокупности факторов: конструкции пути, радиуса кривой, уклона пути, режима торможения подвижного состава, нагрузок от колесной пары на рельс, скоростей движения и т.д.
Интенсификация условий эксплуатации конструкции верхнего строения пути сопровождается повышенным одиночным изъятием рельсов. При этом увеличивается не только удельный выход рельсов, но и изменяется характер преобладающих причин их повреждений. Так, если в прямых и пологих кривых основным видом повреждений рельсов являются дефекты контактно-усталостного происхождения, то в кривых малого радиуса — боковой износ по упорной нити и вертикальный — по внутренней нити [33].
Наиболее значимыми факторами, определяющим эксплуатационную стойкость рельсов, являются их контактно-усталостная долговечность и износостойкость.
В общем виде величина наработки тоннажа рельсов до изъятия может быть представлена зависимостью, где
РИ — доля отказов, приходящаяся на износ;
Рп — доля отказов, приходящаяся на КУД.
Р<у — доля отказов, приходящаяся на прочие дефекты
Ри + 1Р + Ра = 1
Появление и развитие контактно-усталостных дефектов в головке рельса больше характерно для участков, на которых интенсивность износа, и, в первую очередь бокового, незначительна.
Интенсивный износ головки рельса снижает вероятность образования поверхностных усталостных трещин, не давая им развиться и стать причиной изломов и изъятий рельсов при сверхнормативных размерах трещин и выкрашиваний в головке рельса.
От воздействия колес в головке рельса в месте контакта возникают значительные знакопеременные напряжения, которые в зонах концентрации превышают предел выносливости рельсовой стали. После определенной наработки в этих зонах от поверхности катания возникают трещины контактной усталости, приводящие к изломам и отказам рельсов.
На основании содержащихся в электронных базах данных сформированы совокупности одиночных изъятий по группам дефектов объемно и дифференцированно термоупрочненных рельсов типа Р65 контактно-усталостного происхождения на сети железных дорог ОАО «РЖД».
К учету прияты изъятия рельсов по кодам дефектов [6]:
- код дефекта 10 — Трещины и выкрашивания металла на поверхности катания головки из-за нарушений технологии изготовления рельсов (закатов, волосовин, плен и т.п.), развивающиеся на ранних стадиях эксплуатации. После пропуска более 150-250 млн т брутто продольные горизонтальные трещины и выкрашивания образуются при глубине залегания до 8 мм в результате воздействий высоких контактных напряжений;
- код дефекта 12/11 — Трещины и выкрашивания металла на боковой рабочей выкружке или на средней части головки, возникшие изнутри от местных скоплений неметаллических включений, вытянутых вдоль направления прокатки в виде дорожек-строчек или возникшие от наружной поверхности рельса при глубине залегания до 8 мм из-за недостаточной контактно-усталостной прочности рельсового металла;
- код дефекта 19 — Контроленепригодность из-за наличия выкрашиваний, трещин на поверхности катания, и других образований, мешающих обнаружению внутренних дефектов при ультразвуковом контроле рельса.
- код дефекта 22/21 — Поперечные усталостные трещины в головке в виде светлого или темного пятна, возникшие от внутренней или наружной продольной трещины, образовавшейся вследствие недостаточной контактно-усталостной прочности металла. Поперечные усталостные трещины могут образовываться от поверхностной продольной трещины (код дефекта 11).
Для сравнительного анализа эксплуатационной стойкости рельсов и выявления участков с интенсивным изъятием рельсов по контактноусталостным видам дефектов использована система статистических показателей:
- Удельное одиночное изъятие рельсов, снятых по отдельной группе дефектов или по всем дефектам вместе за отчетный год (п), представляющая собой отношение суммарного числа одиночно изъятых рельсов (К) к общему протяжению путей с рельсами соответствующих типов и качественных категорий, выраженному в километрах (I/) [шт./100км].
Отказы рельсов, выбранные из учетной документации, группировались в соответствии со следующим алгоритмом:
- полигон (Западный или Восточный);
- категория качества рельсов:
- конструкция пути: бесстыковой и звеньевой;
- тип скрепления на железобетонных шпалах
- код дефекта в соответствии с Инструкцией «Дефекты рельсов» [6].
- Накопленный удельный выход — пу. Определяется как сумма количества изъятий рельсов в зависимости от наработки.
Пу = Ег®пу, (2.3)
- Средневзвешенная величина наработки тоннажа, пропущенного по одиночно изъятым рельсам за весь их срок службы (Тср). Этот вспомогательный показатель определяется для рельсов каждого типа или качественной категории по формуле:
ТсР = 1 ™ Т 1 (2.4)
Ы — количество рельсов, рассматриваемых типов или качественных категорий, вышедших из эксплуатации по дефектам в отчетном году при определенной наработке ТЁ
Для установления закономерностей возникновения и развития дефектов контактно-усталостного характера (КУД) и, в дальнейшем, разработки математической модели определения влияния конструкции скрепления на возникновение в рельсах дефектов контактно-усталостного происхождения сформирована отдельная группа (КУД), включающая одиночное изъятие рельсов по кодам дефектов: 10, 12(11), 19, 22 (21) [6].
Для оценки эксплуатационной надежности верхнего строения пути в целом и его элементов используются вероятностные характеристики случайной величины — наработки пути или его элементов от начала его эксплуатации до первого отказа.
Вероятность безотказной работы Р (!) — это вероятность того, что при определенных условиях эксплуатации в заданном интервале времени или в пределах заданной наработки не произойдет ни одного отказа, определяется по формуле
где !- время или наработка, в течение которой определяется вероятность безотказной работы;
Т — время или наработка от начала до первого отказа.
Вероятность безотказной работы по данным статистики об отказах оценивается по формуле [7].
Несмотря на то, что интенсивная укладка дифференцированно термоупрочненных рельсов (далее -ДТ) типа Р65 производства АО «ЕВРАЗ ЗСМК» и ПАО «ЧМК» в последние годы обеспечила протяженность пути с рельсами ДТ порядка 22 650 км, в первую очередь на участках грузового и тяжеловесного движения, основная часть находящихся в эксплуатации рельсов является объемно термоупрочненными (далее — ОТ)производства до 2014 года — порядка 60 тыс. км пути[154].
Одной из показательных характеристик эксплуатационной стойкости рельсов является их удельный выход — количество изъятий рельсов в год относительно 100 км пути.
В 2020 году в конструкции бесстыкового пути для ОТ рельсов производства АО «ЕВРАЗ НТМК» эта величина составляет 53,1 шт./100 км, для ОТ рельсов производства АО «ЕВРАЗ ЗСМК» — 66,0 шт./100 км.
Превышение удельного выхода ОТ рельсов производства АО «ЕВРАЗ ЗСМК» над ОТ рельсами производства АО «ЕВРАЗ ЗСМК», которые изготавливались по ГОСТ Р 51685-2000 [8], объясняется различием условий их эксплуатации: полигон укладки рельсов АО «ЕВРАЗ ЗСМК» характеризуется более низкими температурами, большей грузонапряженностью, осевыми нагрузками, сложным планом и профилем пути по сравнению с европейской частью РФ — полигоном укладки рельсов АО «ЕВРАЗ НТМК».
С целью получения результатов, характеризующих изменение эксплуатационной стойкости рельсов в зависимости от наработки тоннажа, и, в дальнейшем, расчета жизненного цикле рельса — ЕЬС, был определен удельный выход и выявлены основные виды дефектов ОТ и ДТ рельсов производства ЕВРАЗа в интервале наработки 0-700, 701-1000, более 1000 (млн т брутто) по данным 2019 г (рисунок 2.1 а) и выполнено сопоставление изъятий ОТ и ДТ рельсов при близких значениях наработки — до 700 млн т брутто (рисунок 2.1. б) [11]
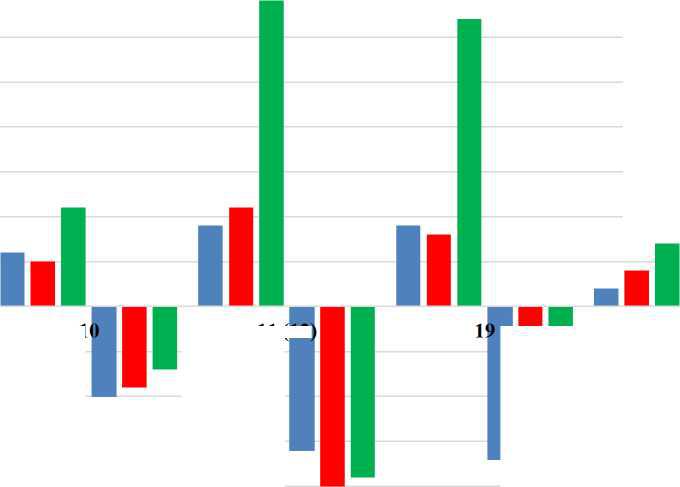
а — ОТ рельсы, б — ОТ рельсы при наработке до 700 млн т брутто и ДТ рельсы
Рисунок 2.1- Распределение удельного выхода рельсов производства ЕВРАЗа по дефектам в зависимости от наработки тоннажа
Сокращение срока службы рельсов приводит к неполному использованию ресурса их работоспособности в отношении прочности против образования дефектов контактно-усталостного происхождения.
Изъятие рельсов по контактно-усталостным видам дефектов
Одним из важнейший показателей работоспособности рельсов является уровень их прочности против образования внутренних дефектов, наиболее распространенными из которых являются дефекты контактноусталостного происхождения.
Контактно-усталостные дефекты изучены достаточно глубоко. В общем случае трещины от усталостных повреждений в местах качения колеса по рельсу возникают из-за чрезмерного воздействия колеса на рельс при недостаточной контактно-усталостной прочности рельсового металла[152].
Силы трения в зоне контакта «колесо — рельс» (в продольном и поперечном направлениях) на поверхности вызывают сжатие и растяжение кристаллической решетки металла. Микротрещины головки образуются и развиваются прежде всего там, где явно выражено основное направление движения (двухпутные линии) или на участках тяги (крутые подъемы и места разгона.
Образование микротрещин, перерастающее впоследствии в выкрашивания, возникает в первую очередь при несоответствии возвышения рельсов скорости движения. При недостатке возвышения — на упорной нити (если интенсивность бокового износа меньше рекомендуемых величин) и при завышенном положении наружного рельса — по внутренней нити.
Высокие контактные напряжения между колесом и рельсом способствуют возникновению микротрещин, и главной причиной в их развитии считается сдвиг между контактирующими поверхностями колеса и рельса. Это происходит и на линиях с преимущественным грузовым движением с большой грузонапряженностью при курсировании современных локомотивов с увеличенной осевой нагрузкой, развивающих большие тяговые усилия.
С уменьшением радиуса кривой точка контакта и, следовательно, место возникновения микротрещин, перемещается в сторону рабочей грани рельса[151].
Микротрещины возникают как на новых рельсах, лежащих в пути менее одного года, так и на эксплуатирующихся более 10 лет.
Микротрещины могут быть одиночными, но более характерно их распространение на длинном участке. Зона трещиноватости образуется как ряд параллельно и близко расположенных трещин, расстояние между которыми составляет 2-3 мм, а более длинные размещаются на расстоянии друг от друга 10.. .20 мм (см. рисунок 2.2).
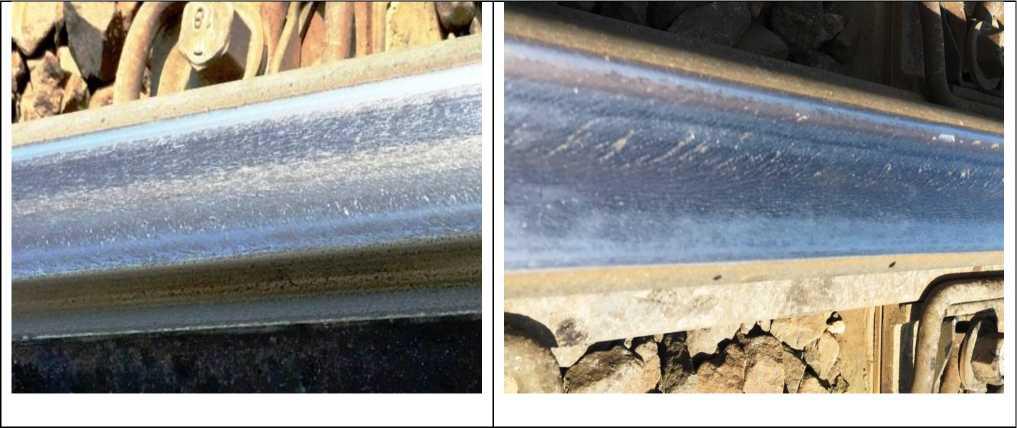
Рисунок 2.2 — Образование микротрещин на поверхности катания рельса
Контактно-усталостные дефекты возникают в первую очередь на участках, где имеются большие касательные напряжения колеса и рельса, сопровождающиеся проскальзыванием в сухих, с большим трением условиях, в то же время рост трещин предполагает наличие жидкости (вода, смазка)[106,107]. На пути вода появляется после осадков и может остаться в трещинах головки рельса, тогда как поверхность рельса кажется сухой. Смазка попадает на рельс из лубрикаторов или из двигателей локомотивов.
Если вследствие высоких контактных напряжений сдвига уже появились микротрещины, присутствие жидкости при прохождении поездов будет провоцировать их рост. Закрытая в трещинах жидкость обуславливает очень высокие местные растягивающее напряжения[105].
По результатам анализа данных выхода термоупрочненных рельсов на сети ж.д. ОАО «РЖД» составлена выборка (см. таблицу 2.1), характеризующая процент изъятия рельсов по контактно-усталостным видам дефектов от общего количества изъятий в 2018 — 2020 гг. в конструкции бесстыкового и звеньевого пути.
Таблица 2.1 — Изъятие термоупрочненных рельсов, %
Года | Код дефект а | ОТ (ЕНТМК) | ОТ (ЕЗСМК) | ДТ (ЕЗСМК) |
2018 | 10 | 9.5 | 5.3 | 1.6 |
11 (12) | 21.8 | 17.6 | 6 | |
19 | 16.3 | 6.4 | 9 | |
21 (22) | 4.5 | 8.2 | 6.9 | |
Итого | 52.1 | 37.5 | 23.5 |
2019 | 10 | 11.5 | 7.4 | 2.8 |
11 (12) | 20.2 | 15.8 | 5.3 | |
19 | 18.6 | 14.5 | 8.4 | |
21 (22) | 2.1 | 5.1 | 2.9 | |
Итого | 52.4 | 42.8 | 19.4 |
2020 | 10 | 9.3 | 8.7 | 2.8 |
11 (12) | 19.8 | 14 | 7.6 | |
19 | 12.8 | 9.5 | 7 | |
21 (22) | 3.1 | 4.9 | 2.9 | |
Итого | 45 | 37.1 | 20.3 |
Изъятие рельсов по пяти кодам дефектов составляет от 20 до 50% от общего количества изъятий, что свидетельствует о высокой значимости результатов научно-технических решений, способных уменьшить удельный выход рельсов по дефектам контактно-усталостного происхождения.
Трещины и выкрашивание металла на рабочей поверхности головки и боковой износ являются основной причиной изъятия и дифференцированно термоупрочненных рельсов (Помимо рассмотренных дефектов, отмечается высокий удельный выход рельсов ОТ и ДТ рельсов по причине отклонений в технологии сварки — более 30%.).
При сравнительной оценке удельного количества изъятий по дефектам рельсов категорий ОТ350 (категории Т1) и ДТ350, имеющих близкий средний пропущенный тоннаж (до 500 млн т брутто), удельный выход рельсов ДТ350 составляет 0,35 шт./км, а удельный выход рельсов ОТ350 (категории Т1) — 0,54 шт./км, что в 1,5 раза больше, чем для рельсов категории ДТ350.
Наибольший выход рельсов отмечается по дефектам 11.2 (12.2) и 19.0-1-2 из-за недостаточной контактно-усталостной прочности рельсового металла в условиях повышенных нагрузок от составов на участках грузового тяжеловесного движения на участках Восточного полигона.
При сравнительном анализе наиболее объективные результаты достигаются при комплексном использовании нескольких показателей[7]:
- Удельный выход рельсов (пу), характеризует количество изъятий рельсов на единицу протяженности их укладки за единицу времени, шт./100 км в год и является одной из наиболее показательных характеристик эксплуатационной стойкости рельсов.
- Процентное отношение изъятий рельсов по определенным кодам (группе кодов) дефектов к общему количеству изъятий является сравнительным показателем, характеризующим степень соответствия свойств рельсов условиям эксплуатации.
Для установления степени влияния дефектов контактно-усталостного характера на долговечность рельсов и, в дальнейшем, разработки математической модели определения влияния типа и состояния скрепления на возникновение в рельсах дефектов контактно-усталостного происхождения сформирована отдельная группа (КУД), включающая одиночное изъятие рельсов по кодам дефектов: 10, 12(11), 19, 22 (21).
На основании содержащихся в электронных базах данных сформированы совокупности одиночных изъятий по группам дефектов объемно (ОТ) и дифференцированно (ДТ) термоупрочненных рельсов типа Р65 контактно-усталостного происхождения на сети железных дорог ОАО «РЖД».
Изъятие рельсов по рассматриваемым кодам дефектов составляет от 20 до 40% от общего количества изъятий, что свидетельствует о высокой значимости результатов научно-технических решений, способных уменьшить удельный выход рельсов по дефектам происхождения, что показано на рисунке 2.3
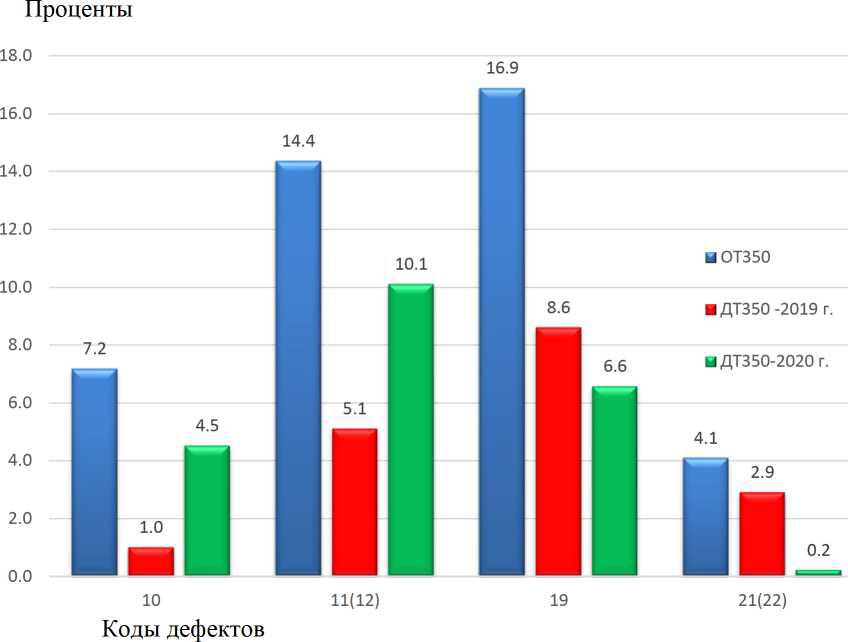
Данные, получаемые по одному году, не в полной мере характеризуют фактическое состояние по одиночному изъятию рельсов. На рисунке 2.4 представлены графики, иллюстрирующие различие в результатах при рассмотрении данных по рельсам ДТ за один и три года. Итоговые графики (данные усреднены по трем годам выборки) изъятий ДТ рельсов наглядно демонстрируют, что наиболее интенсивно изъятия рельсов по дефектам контактно-усталостного происхождения происходят на ранней стадии эксплуатации при наработке до 100 млн т брутто с последующим всплеском при наработке порядка 600 млн т брутто.
Если в начале эксплуатации, при приработке, эти изъятия рельсов следует относить, как правило, к металлургическим недостаткам самих рельсов, то при наработке 500 — 600 млн т брутто эти дефекты возникают от отступлений в содержании, в том числе при изменении вертикальной и горизонтальной жесткости конструкции верхнего строения пути.
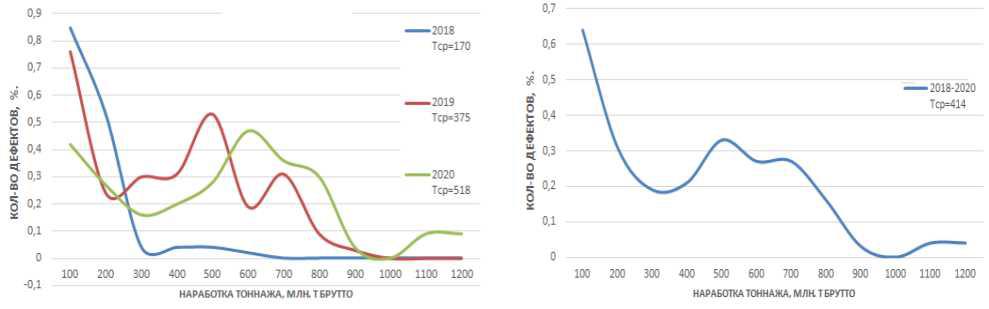
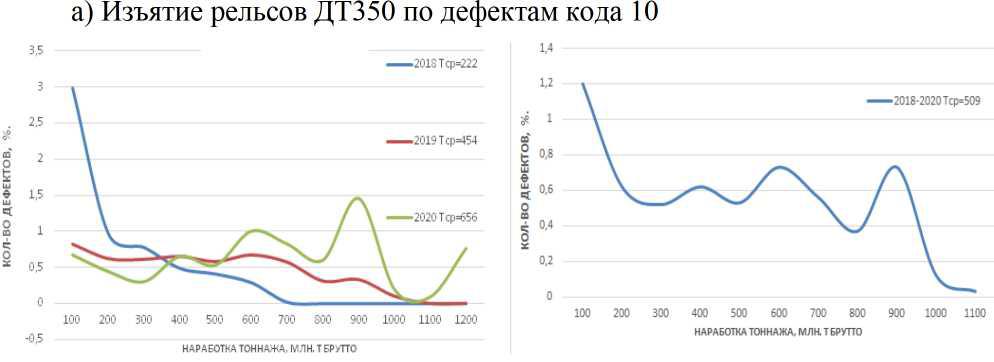
Рисунок 2.4 — Изъятие рельсов ДТ350 по отдельным дефектам
С целью получения результатов, характеризующих изменение эксплуатационной стойкости рельсов в зависимости от наработки тоннажа, и, в дальнейшем, расчета стоимости жизненного цикла конструкции верхнего строения пути, был определен удельный выход и выявлены основные виды дефектов ОТ и ДТ рельсов в интервале наработки 0-700, 701-1000, более 1000 млн т брутто (рисунок 2.5 а) и выполнено сопоставление изъятий ОТ и ДТ рельсов при близких значениях наработки — до 700 млн т брутто (рисунок 2.5 б).
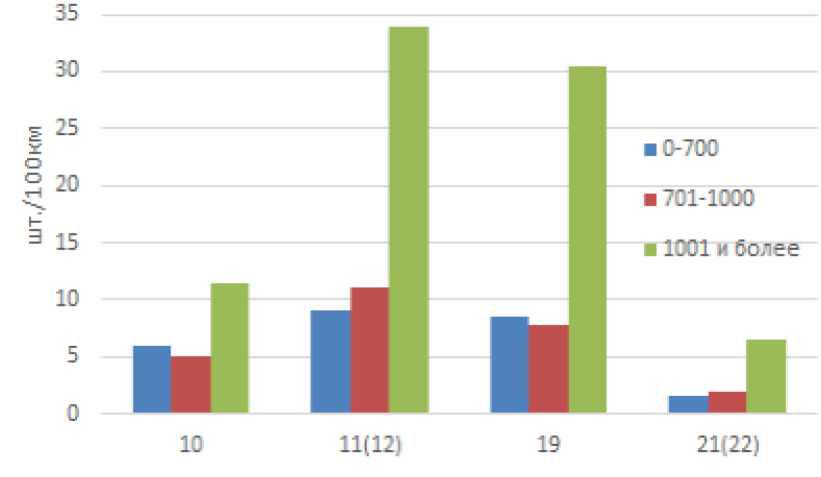
а) рельсы категории ОТ и ДТ в интервале наработки 0-700, 701-1000, более 1000 млн т брутто
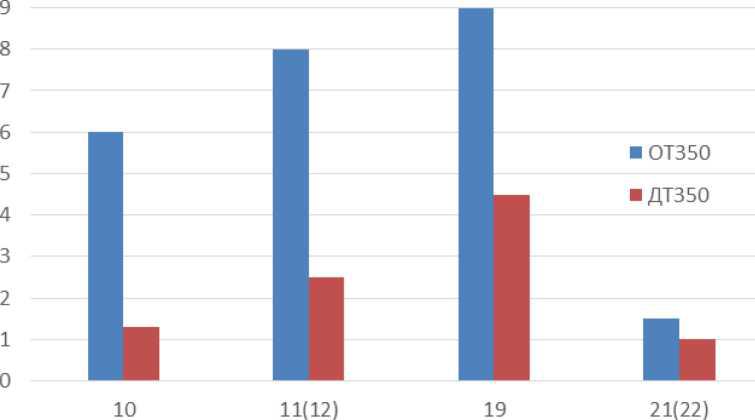
- рельсы категорий ОТ и ДТ при наработке до 700 млн т брутто
Рисунок 2.5 — Распределение удельного выхода рельсов по дефектам в зависимости от наработки тоннажа
Выводы
При анализе величин удельного выхода рельсов установлено, что при наработке, превышающей нормативную, определяемую периодичностью проведения капитальных ремонтов, значительно увеличивается удельный выход рельсов по контактно-усталостным видам дефектов, образующимся на поверхности катания.
Наибольший выход рельсов по дефектам кодов 11 и 19 отмечается в условиях повышенных нагрузок от составов на участках грузового тяжеловесного движения на участках Восточного полигона, где в основном применяются скрепления типа ЖБР-65Ш и его подкладочные модификации.
На возникновение и развитие дефектов рельсов контактно-усталостного характера оказывает значительное влияние изменяющееся и практически не прогнозируемое состояние подрельсовых элементов ВСП: увеличенная вертикальная жесткость скреплений за счет применения прокладок-амортизаторов с номинальной вертикальной жесткостью свыше 150 МН/м; увеличение модуля упругости пути в зимнее время при снижении эластичных свойств прокладок-амортизаторов промежуточных скреплений и замерзании балласта.
Сокращение срока службы рельсов по причине интенсивного развития дефектов контактно-усталостного происхождения приводит к неполному использованию ресурса их работоспособности.
Используемая Литература
- Борц, А. И. Исследования инновационной рельсовой продукции и перспективы ее дальнейшего развития / А. И. Борц // Улучшение качества и условий эксплуатации рельсов и рельсовых скреплений: сборник научных докладов о материалам 130 заседания некоммерческого партнерства «Рельсовая комиссия» (Новокузнецк, 7-9 октября 2014 г.). — Санкт-Петербург, 2015. — С. 107-120.
- ГОСТ 32192-2013. Надежность в железнодорожной технике. Основные понятия. Термины и определения. — Москва: Стандартинформ. — 2014. — 27 с.
- Абдурашитов, А.Ю. Определение величин интегральных спектров распределения вертикальных и боковых сил от воздействия подвижного состава на железнодорожный путь / А.Ю. Абдурашитов, А.В. Сычева, Н.В. Кузнецова, П.В. Сычев // Вестник транспорта Поволжья. -2020. — № 1
- Пат. 2746554 Российская Федерация, МПК Е01В 3/00, Е01В 3/20, Е01В 3/46. Подрельсовое устройство железнодорожного пути и способ укладки по меньшей мере одного подрельсового устройства железнодорожного пути/ Сычев В.П., Локтев А.А., Сычева А.В., Кузнецова Н.В., Сычев П.В.; заявитель и патентообладатель Общество с ограниченной ответственностью «Вагонпутьмашпроект». — № 2020124286; заявл. 22.07.2020; опубл.
- Кузнецова, Н. В. Особенности влияния промежуточных рельсовых скреплений на эксплуатационную стойкость рельсов / Н.В. Кузнецова, Е.А. Сидорова // Вестник научно-исследовательского института
железнодорожного транспорта. — 2021. — №4. — С. 201 — 208 - ГОСТ Р 51685-2013. Рельсы железнодорожные. Общие технические
условия (с изменением № 1). — Москва: Стандартинформ, 2014. — 95 с - ГОСТ Р 50779.10-2000 (ИСО 3534.1-93) Статистические методы. Вероятность и основы статистики. Термины и определения. — Москва: Стандартинформ, 2005. — 46 с.
- Савоськин, А.Н. Вертикальные и горизонтальные возмущения на рельсовом полотне / А.Н. Савоськин, В.В. Кочергин, А.И. Поляков // Мир транспорта — 04-2015. — С.4-14.
- Инструкция по текущему содержанию пути: утверждена распоряжением ОАО «РЖД» от 14.11.2016 № 2288р (взамен утратившей силу 2791р). — Москва, 2016. — 286 с.
- Дефекты рельсов. Классификация, каталог и параметры дефектных и остродефектных рельсов: инструкция: утверждена распоряжением ОАО «РЖД»от 23.10.2014 № 2499р.
- Обобщение мирового опыта тяжеловесного движения. Управление
содержанием системы колесо — рельс. / пер. с англ. под. ред. С.М. Захарова — Москва: Интекст, 2017. — 420 с.