Сейчас ваша корзина пуста!
Исследование шурупно-дюбельного способа прикрепления рельсов к железобетонным брусьям
Цикл статей:
Глава 1 — Виды железобетонных подрельсовых оснований для стрелочных переводов
Глава 2 — Разработка методики расчета и проектирования железобетонных брусьев для стрелочных переводов
Глава 3 — Совершенствование конструкции болтового прикрепления
Глава 4 — Исследование шурупно-дюбельного способа прикрепления рельсов к железобетонным брусьям
Глава 5 — Эффективность применения железобетонного основания на стрелочном переводе
Исследование возможности применения шурупно-дюбельного скрепления для железобетонных брусьев стрелочных переводов, как одного из направлений решения задачи повышения стабильности ширины рельсовой колеи представляется актуальным по следующим соображениям.
Шуруп, диаметр стержня которого в верхней цилиндрической части равен диаметру стержня типового закладного болта, в случае упора в дюбель из прочного полимерного материала с высоким сопротивлением смятию может воспринять и передать на бетон значительную поперечную силу, в то время как закладной болт размещен в болтовом канале свободно и поперечных сил не воспринимает.
Незначительные поперечные размеры полимерного дюбеля (диаметр около 35 мм) позволяют разместить в поперечном сечении железобетонного бруса два дюбеля, не касаясь продольной напряженной арматуры. Таким образом, число прикрепителей, воспринимающих поперечную силу, при применении шурупов может быть увеличено вдвое по сравнению с закладными болтами с установленными на них упорными втулками. Для размещения закладного болта и закладной седловидной шайбы необходимо иметь по середине поперечного сечения бруса свободную от арматуры зону шириной не менее 85 мм, поэтому разместить два закладных болта в сечении бруса невозможно.
Малый диаметр полимерного дюбеля позволяет без дополнительных отклонений крепить к брусьям длинные стрелочные подкладки, требующие разворота в плане и соответствующего смещения прикрепителей от продольной оси бруса, чему сейчас препятствует продольная арматура.
Дюбель из полимерного материала обеспечивает надежную внутреннюю изоляцию рельсовых цепей электрического тока без применения изолирующих втулок в скреплении.
Для реализации указанных выше преимуществ необходимо решение следующих вопросов:
- изменить конструкцию шурупа, повысив его сопротивление излому при действии поперечных сил;
- разработать конструкцию дюбеля, обеспечивающую правильное взаимодействие с шурупом, в том числе при проведении выправки пути по уровню;
- подобрать полимерный материал дюбеля, обеспечивающий его прочность, долговечность, отсутствие остаточных деформаций при высоких и низких температурах.
Взаимодействие шурупа и дюбеля. Разработка технических требований к конструкции шурупа.
Взаимодействие шурупа и дюбеля в железобетонном брусе или шпале принято таким же, как взаимодействие болта и гайки в резьбовом соединении.
Болт, затянутый гайкой в резьбовом соединении, способен обеспечить восприятие значительных горизонтальных усилий на сдвиг как от плотного сжатия и повышения трения между сдвигаемыми плоскостями, так и от включения в работу на сдвиг стержня болта. При этом в стержне болта возникают только растягивающие напряжения от силы затяжки болта.
При частичном вывинчивании болта из гайки и передаче на него горизонтальных усилий не только снижается сопротивление сдвигу из-за уменьшения сжатия и трения сдвигаемых плоскостей, но и возникает изгиб стержня болта. Изгибные напряжения способны вызвать излом стержня болта в наиболее слабом сечении по его резьбе.
Как указано в 1-й главе, ранее выход типовых шурупов в пути с железобетонными шпалами тоже связан с изломом их в зоне резьбы, где рабочий диаметр стержня шурупа уменьшается с 24 до 15 мм. Излом шурупов вызван изгибом их под действием поперечных сил, приложенных через подкладку к верхней части шурупа, и отсутствием упора и поддержки этой части шурупа со стороны дюбеля и шпалы.
Другим недостатком применяемых в настоящее время шурупов является то, что их головка не унифицирована с болтовым вариантом прикрепления подкладки к железобетонному основанию. Так, например, головка немецкого шурупа оформлена в виде усеченной четырехугольной пирамиды имеющей в основании прямоугольник, а отечественный шуруп имеет в основании квадрат. Конусность пирамиды приводит к проскальзыванию ключа при завинчивании и вывинчивании, притуплению его углов. При обращении с таким шурупом требуются специальные ключи, а при применении механических гайковертов потребуются дополнительные специальные насадки. Всех этих недостатков можно избежать, если запроектировать головку шурупа в виде обычной шестигранной гайки унифицированной с головкой болтов в болтовом скреплении. Такая возможность была проанализирована и реализована в варианте конструкции шурупа, представленном на рис. 4.1.
Наиболее неблагоприятные условия для работы шурупа возникают при выправке пути с помощью прокладок с вывинчиванием шурупа на высоту выправки. В этом случае верхняя часть резьбы типового шурупа выходит из зацепления с резьбой дюбеля, между шурупом и дюбелем образуется зазор и происходит изгиб шурупа в зоне резьбы.
Дтя обеспечения правильного взаимодействия шурупа и дюбеля необходимо выполнение главного требования, чтобы при выправке пути по уровню и вывинчивании шурупа на всю высоту подъемки сохранялся контакт между стержнем шурупа и внутренней стенкой дюбеля, т.е. чтобы резьба шурупа не выходила из дюбеля.
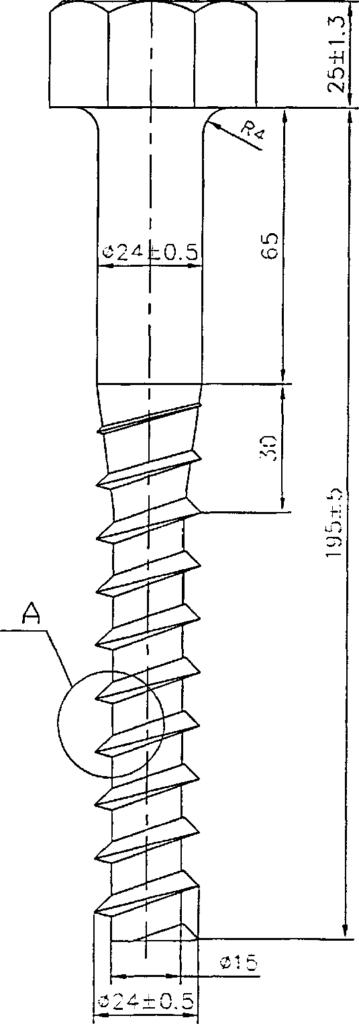
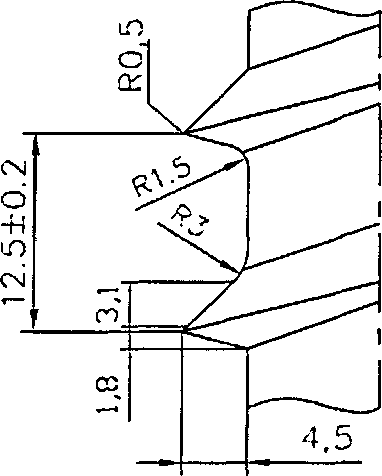
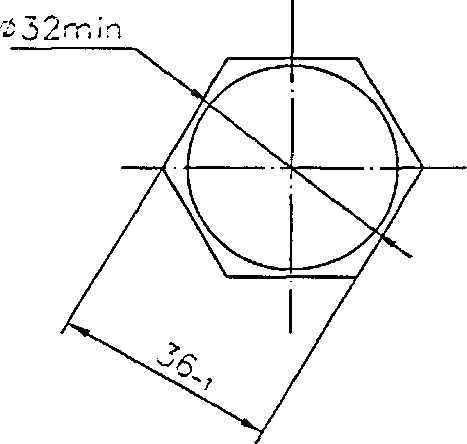
Для выполнения этого требования необходимо:
- По конструкции шурупа — не меняя длины и параметров резьбовой части шурупа, определяемых усилием затяжки, увеличить длину подголовочного цилиндрического участка стержня шурупа на расчетную величину подъемки в 20-25 мм, установленную техническими требованиями ЦП 1-86 на проектирование рельсовых скреплений.
- По конструкции дюбеля:
а) увеличить длину верхнего цилиндрического без резьбы участка внутреннего канала дюбеля до такого значения, чтобы вывинчивание шурупа на всю высоту подъемки при выправке пути не приводило бы к выходу резьбовой части стержня шурупа из канала дюбеля;
б) параметры резьбы во внутреннем канале дюбеля должны соответствовать параметрам резьбы шурупа.
Этим требованиям удовлетворяет новый шуруп (рис.4.1), разработанный совместно с ПТКБ ЦП МПС. В этом шурупе длина подголовочного цилиндрического участка стержня шурупа увеличена с 40 мм (у стандартного путевого шурупа) до 65 мм. Для повышения сопротивления выдергиванию и с учетом более прочного материала дюбеля в новом шурупе при сохранении высоты зуба увеличен угол наклона профиля резьбы до 35° против 22° в стандартном шурупе. Это увеличило поверхность контакта резьбы шурупа с дюбелем на 13%. Кроме того применена головка, имеющая форму гайки закладного болта, что позволяет использовать для завинчивания шурупов типовые гайковерты. Конструкция шурупа утверждена ЦП МПС (ЦП 54).
Разработанная на основании этих принципов новая конструкция дюбеля из полимерного материала показана на рис. 4.2. Особенностью этого дюбеля является то, что размеры внутреннего канала по длине верхней цилиндрической без резьбы, средней конической с началом резьбы на ней и нижней цилиндрической с резьбой соответствуют аналогичным участкам шурупа. При вывинчивании шурупа из дюбеля на высоту подъемки сохраняется объемлющий контакт (без зазора) цилиндрической части стержня шурупа с внутренней поверхностью верхней цилиндрической части дюбеля. При этом площади поверхностей контакта шурупа и дюбеля остаются достаточными для обеспечения прочности дюбеля при действии на его материал напряжений от поперечных сил, при соответствующем выборе материала дюбеля.
Внутренняя резьба дюбеля выполнена под резьбу шурупа с шагом 12,5 мм. Число витков резьбы дюбеля 9-10. Наружная поверхность дюбеля для улучшения сцеплением с бетоном также выполнена в виде цилиндрической поверхности с винтовой резьбой с тем же шагом, что и внутренняя. Дюбель в случае необходимости может быть заменен новым.
Конструкция дюбеля утверждена Департаментом пути и сооружений МПС России для проведения эксплуатационных испытаний. На крепежный узел рельсовых скреплений с использованием указанных выше конструкций шурупа и дюбеля получено свидетельство на полезную модель (свидетельство №26501 от 18.06 2002г.).
Разработка технических требований к конструкции и материалу дюбелей
Исходя из принятой модели взаимодействия шурупа и дюбеля как болта и гайки в резьбовых соединениях, для определения технических требований к конструкции дюбеля и его материалу были приняты методы расчета резьбовых (болтовых) соединений.
Действовавшая до 2000 г. «Инструкция по текущему содержанию железнодорожного пути ЦП/2913» [40] предусматривала применение шурупов в раздельных скреплениях для деревянных и железобетонных шпал. Соответственно были даны нормативные значения крутящего момента для затяжки шурупов при обоих видах шпал — не менее 2500 кгс-см. В новой «Инструкции по текущему содержанию железнодорожного пути ЦПТ-744» нормативные требования по затяжке шурупов отсутствуют.
В действующих «Технических указаниях по ведению шпального хозяйства с железобетонными шпалами ЦПТ-17» [88] нормативные требования по затяжке шурупов также отсутствуют, но имеются указания о нормативных значениях крутящих моментов для затяжки закладных болтов при скреплении КБ. Нормально эти болты следует затягивать крутящим моментом 120-150 Н-м (1200-1500 кгс-см), но допускается усиленная затяжка до 180-200 Н-м (1800-2200 кг-см).
По аналогии с приведенными нормативными значениями для закладных болтов при определении расчетных значений показателей прочности полимерных дюбелей могут быть приняты следующие нормативные значения крутящих моментов (Мкр):
для нормальной затяжки — 1500 кгс-см; при усиленной затяжке — 2200 кгс-см; в исключительных случаях до 2600 кгс-см.
По современным методам расчета резьбовых соединений [43] для расчетов при отсутствии специальной обработки и смазки контактирующих поверхностей гайки и клеммы или подкладки может быть принято соотношение
где : М^ — величина крутящего момента кгс-см, Р0 — осевая сила затяжки болта, кгс, 11 — наружный диаметр резьбы шурупа, см.
Исходя из этой зависимости,
(4.2)
0 0.2-г/ 4
Для й= 2,4 см и указанных выше значениях Мкр получим, следующие расчетные значения сил затяжки болта:
нормальная Р„ = 3125 кг -3,0 тс, усиленная = 45 83 кг ~ 4,6 тс,
предельная /г/иаг=5417 кг ~ 5,4 тс.
Исходя из этих значений = 3,0 тс) было принято нормативное значение сопротивления дюбеля выдергиванию из него шурупа с коэффициентом запаса два Ртах = 6 тс, которое рассматривалось как критерий для оценки прочности дюбелей из различных полимерных материалов при дальнейших их лабораторных испытаниях.
По этим расчетным значениям сил затяжки шурупа могут быть определены требования к прочности материала резьбы дюбеля при вытягивании из него шурупа.
Для расчета дюбеля как элемента резьбового соединения могут быть использованы следующие зависимости [43]: а) по срезу витков резьбы дюбеля
б) по смятию витков резьбы дюбеля
|
(Тем = -ттз—ГГГ — (4.4
В этих формулах обозначено: Т7 — сила затяжки,
коэффициент полноты заполнения резьбы, принимаемый по аналогии с метрической резьбой, равным 0,8, Н-Р г- высота дюбеля, Р — шаг резьбы дюбеля, г — число витков резьбы дюбеля, И — внутренний диаметр резьбы дюбеля, 1>1 = й\ — внутренний диаметр резьбы шурупа, I г| — предел прочности материала дюбеля при срезе, I сгсчI — предел прочности материала дюбеля на смятие.
Исходя из условия соответствия резьбы шурупа (см. рис. 4.1) и дюбеля была разработана удовлетворяющая вышеперечисленным требованиям конструкция резьбы дюбеля (см. рис. 4.2) со следующими параметрами: Р = 12,5 мм= 1,25 см,
Z= 8 — число полных витков в цилиндрической части дюбеля, Н= 1,25-8= 10 см, Я = 24,25 мм = 2,42 см Х>1 = й\ = 15 мм = 1,5 см.
По формулам (4.3) и (4.4) были определены необходимые параметры прочности материала дюбеля исходя из нормативного и предельного значения затяжки шурупа.
При нормальной затяжке:
О т= ,,, . ^ =50.9 кг/см2;
‘ 3,14 • 0,8 • 10-2,425
->л 4-3100 2
2) сгсч = т ; —= 135,9 кг/см .
3,14(2,425 -1,5 )• 8
При предельной затяжке:
1^°З.Н.0,85Ш.2,425 = 90‘2КГ/СМ2;
ол 5500-4 2
2) <Усм~ 7 ; л—=241,1 кг/см .
3,14(2,425 -1,5 )• 8
Полученные значения напряжений в материале были приведены к значениям, позволяющим производить выбор материала по следующим соотношениям [43]: гср. = 0,2ат, где ат — сопротивление текучести при растяжении; <Усм. = 0,4 ат
Таким образом, предельная прочность материала дюбеля по сопротивлению на растяжение (егг) должна составлять не менее: 90 2
по срезу -^у = 451 кг/см = 45 МПа 2411
по смятию —= 602 кг/см = 60 МПа 0,4
Для практической проверки прочности дюбелей при работе их в пути и назначения полимерного материала для них была проведена серия испытаний опытных дюбелей.
Лабораторные испытания опытных дюбелей на прочность
Для оценки соответствия опытных дюбелей условиям работы их в действующем пути была разработана методика испытаний шурупно-дюбельного скрепления на прочность и по ней проведена серия лабораторных испытаний.
При разработке методики этих испытаний были учтены и частично использованы методики ранее проводившихся аналогичных испытаний деревянных дюбелей во ВНИИЖТе [65] и пластмассовых дюбелей во ВНИИжелезобетоне [9].
Для лабораторных испытаний были изготовлены опытные образцы дюбелей из применяемых в России полимерных материалов. Был испытан также типовой дюбель, применяемый в ФРГ.
Испытания проводились с использованием стандартных бетонных кубов 200x200x200 мм с забетонированными в них опытными дюбелями, а также блоки подрельсовой части типовой шпалы с опытными дюбелями.
При лабораторных испытаниях были исследованы следующие вопросы:
- а) сопротивление дюбеля выдергиванию из него шурупа;
- б) сопротивление шурупа и дюбеля боковому отжатию;
- в) испытание подрельсового блока шпалы с шурупно-дюбельным рельсовым скреплением на действие циклических вертикальных и поперечных сил.
Испытание дюбелей на выдергивание
Испытания дюбелей на сопротивление выдергиванию шурупа были выполнены по схеме, показанной на рис. 4.3, а, на лабораторной установке, представленной на рис. 4.4. Величину выдергивающей статической силы определяли по манометру пресса, а величину вытягивания шурупа из дюбеля — индикатором часового типа.
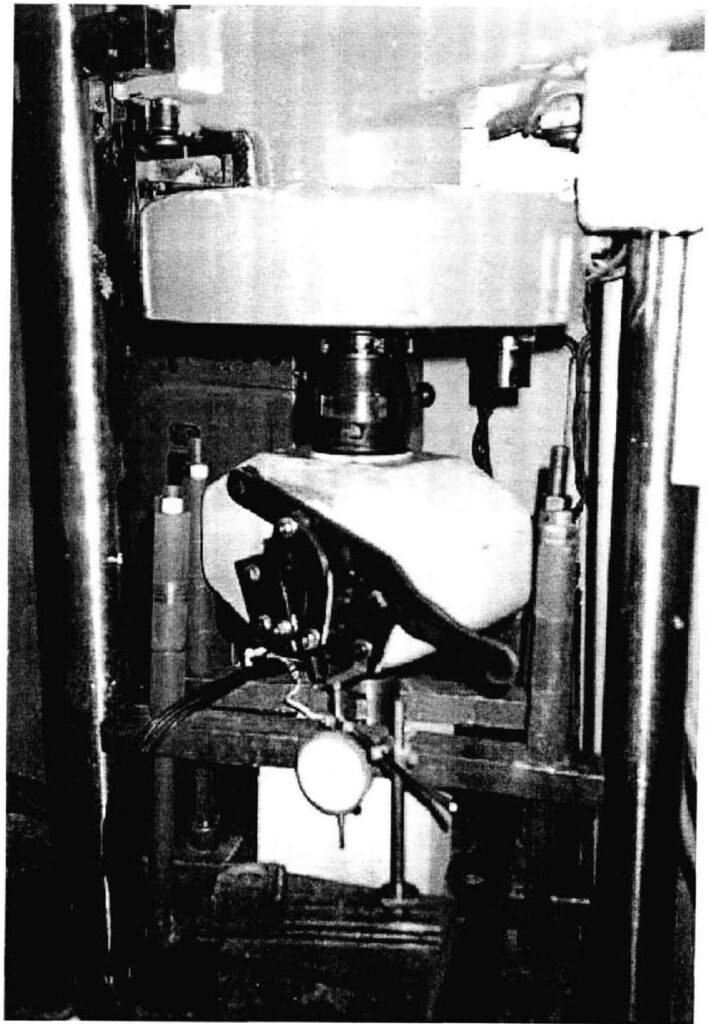
Рис. 4.4. Испытание дюбеля, забетонированного в бетонном кубе,
на вырывание шурупа
Завинчивание шурупа проводили на всю высоту резьбовой части шурупа, а для оценки возможности использования шурупов при выправке пути на прокладках два шурупа были завинчены на глубину, меньшую на 25 мм нормальной.
Для сравнения был испытан на выдергивание дюбель, применяемый на дорогах ФРГ, забетонированный в отрезке шпалы (рис.4.5).
Выдергивание шурупа производили статической нагрузкой ступенями в 1 тс с выдержкой на каждой ступени не менее 1 мин. Индикатором часового типа измеряли величину перемещения головки шурупа относительно поверхности куба. Испытания проводили до выдергивания шурупа или достижения предельной силы. Испытания прекращали в случае раскола бетонного куба по вертикальным и поперечным трещинам (рис.4.6).
В этом случае, за расчетную величину силы принимали значение, при котором наступил раскол бетонного куба.
С целью ускорения и увеличения объема испытаний, а также для исключения преждевременного раскола бетона, часть опытных дюбелей не бетонировали в кубах, а устанавливали в металлический разъемный стакан, профиль внутренней поверхности которого соответствовал профилю наружной поверхности дюбеля (рис. 4.7). Для повышения трения и обеспечения надежной связи наружной пластмассовой поверхности дюбеля с внутренней металлической поверхностью стакана резьбу стакана покрывали слоем клея и абразивного материала. После установки дюбеля внутрь стакана половинки его стягивали болтами, создающими обжатие дюбеля. Стакан с дюбелем устанавливали на лабораторный стенд и закрепляли к основанию (рис. 4.8). Дальнейшее испытание проводили тем же порядком.
При испытании дюбелей в кубах не было случаев выдергивания шурупа из дюбеля. Все образцы разрушились из-за раскола бетона (см. рис. 4.6). Внутренняя резьба дюбеля оставалась неповрежденной и после испытаний шуруп легко вывинчивался.
При испытаниях всех образцов дюбелей, заделанных в стакан, также не было ни одного случая выдергивания шурупа из дюбеля. Во всех случаях испытание было прекращено из-за вытягивания дюбеля из стакана (см. рис. 4.7) или достижения предельной силы, принятой в 10 тс. Внутренняя резьба дюбеля осталась неповрежденной и шуруп легко вывинчивался из дюбеля. В соответствии с «Методикой», за расчетную величину принимали максимальное значение, при котором наступило вытягивание дюбеля.
Примечание: В скобках указаны номера опытных образцов, испытанных в стакане без усиления трения абразивным материалом
Анализ всех результатов испытаний на вырывание шурупа показал следующее. При испытании дюбелей из полиэтилена в кубах максимальная величина силы составила 8,0-9,0 тс и ограничивалась расколом по трещинам, т.е. предельное сопротивление вырыву не было достигнуто. Это позволяет утверждать, что фактическое сопротивление дюбелей из полиэтилена вырыву шурупа превышает нормативное значение в 6 тс в 1,3-1,5 раза.
При испытании этих дюбелей в стакане во всех случаях происходило вытягивание дюбеля без вырыва шурупа, т.е. предельное значение силы сопротивления полиэтилена вырыванию тоже не было достигнуто. При обеспечении заделки дюбеля в стакане сила, при которой происходило вытягивание, превышала нормативное значение в 6 тс.
При испытании дюбелей из блоксополимера в стакане во всех случаях происходило вытягивание дюбеля без вырыва шурупа. При обеспечении заделки дюбеля в стакане абразивной прослойкой сила вытягивания дюбеля составляла 8,0-8,5 тс, т.е. превышала нормативное значение в 1,3-1,4 раза, и предельное сопротивление блоксополимера выдергиванию шурупа еще не было достигнуто.
При испытании дюбелей из полиамида, полиамида стеклонаполненного, армамида и армлена со стекловолокном, обеспечивалось надежное закрепление дюбеля в стакане даже при предельно установленной нагрузке в 10 тс, с коэффициентом запаса 1,7 к нормативному значению. Вытягивания дюбеля из стакана и вырыва шурупа из дюбеля при этой нагрузке не было, а при нагрузке в 11 тс был случай разрыв шурупа по резьбе. Все шурупы после окончания испытания легко вывинчивались из резьбы в дюбеле. Таким образом, сопротивление указанных материалов выдергиванию шурупа намного выше нормативного значения в 6 тс.
При испытании этих же дюбелей в бетонных кубах были получены сравнительно невысокие значения максимальной силы от 5,0 до 6,0 тс из-за раскола бетона по трещинам.
При испытании в стакане дюбелей из армлена со стекловолокном и с каучуком наблюдалось вытягивание дюбеля при небольшой нагрузке из-за недостаточно надежного закрепления дюбеля в стакане, что не определило действительного значения сопротивления этих материалов вырыванию шурупа.
Во всех испытанных образцах резьба дюбеля оставалась неповрежденной, и шуруп легко вывинчивался из дюбеля.
Испытания показали, что для всех исследованных материалов предельное сопротивление вырыванию шурупа из дюбеля не было достигнуто и действительное сопротивление их превышает сопротивление в минимальный необходимый предел 6 тс.
Испытание на отжатие шурупа
Рис. 4.9. Испытание шурупа на боковое отжатие
При испытании поперечную силу Н прикладывали на уровне головки шурупа и измеряли величину бокового отжатия Л У. График этой зависимости для дюбеля из полипропилена показан на рис. 4.10.
Зависимость Л У= /(Н) близкая к линейной после выбора люфтов сохранялась примерно до Н = 1 тс. При снятии нагрузки шуруп полностью возвращался в первоначальное положение.
Заметное увеличение изгиба стержня шурупа начинается при Н> 1,4 тс, а после Н > 2 тс верхний цилиндрический участок стержня шурупа приобрел значительный остаточный изгиб. В пределах нижней нарезанной части шурупа изгиб стержня отсутствовал. Если пересчитать изгибающий момент на реальное сечение приложения бокового усилия через упорную скобу, то плечо должно быть уменьшено примерно с 40 до 12 мм, что приводит к увеличению реального момента вызывавшего изгиб болта с 1 тс до 3.5 тс. Это дает основание считать, что в эксплуатации изломы шурупов в зоне резьбы маловероятны.
Испытание циклической нагрузкой
Испытание подрельсового блока с шурупно-дюбельным рельсовым скреплением на действие циклических нагрузок было выполнено на лабораторном стенде (см. рис.3.12). Общий вид стенда и методика испытаний были описаны в разделе 3.2.
На одной половине стенда была установлена подрельсовая часть шпалы ШЗ-Д с опытным шурупно-дюбельным скреплением ЖБР-65Ш, а на другой половине стенда по очереди устанавливали полушпалы с двумя другими вариантами скрепления:
а) ЖБР-65 с болтовым прикреплением рельса к шпале опытного, но уже получившего применение на отечественных дорогах,
б) \V-14 «Фоссло» с шурупно-дюбельным прикреплением рельса к шпале типового для железных дорог ФРГ.
Циклическая динамическая нагрузка, передаваемая на каждый темплет скрепления, составляла: вертикальная 10 тс, поперечная — 4,6 тс.
Испытания проводили при двух режимах работы: при обычном положении узла скрепления и при выправке пути на прокладках с подъемкой по высоте до 15 мм.
Испытания проводились до наработки 4 млн. циклических нагружений скрепления ЖБР-65Ш, в том числе 1,5 млн. циклов параллельно со скреплением 14 и 2,5 млн. циклов — со скреплением ЖБР-65 с болтом.
По результатам испытаний можно отметить следующие закономерности:
- а) поперечные перемещения подошвы рельсов при всех видах скреплений были практически равнозначны и не превышали 1 мм;
- б) полностью отсутствовали признаки выдергивания или отжатия шурупов при циклической нагрузке, как в опытном, так и в типовых конструкциях дюбелей;
- в) ослабление затяжки шурупов по показаниям динамометрического ключа было вызвано исключительно обжатием подрельсовых прокладок, а не выдергиванием шурупов из дюбелей.
Результаты стендовых испытаний дают основание утверждать, что показатели стабильности ширины рельсовой колеи при скреплении ЖБР-65 с опытными конструкциями шурупов и дюбелей не ниже аналогичных показателей для скреплений ЖБР-65 с болтами и \V-14 «Фоссло».
Исследования и лабораторные испытания материала для дюбелей
Кроме испытаний дюбелей из различных видов полимерных материалов на выдергивание шурупа и для проверки выполнения требований к их прочности (п. 4.2)были определены и другие физико-механические свойства, которым должен отвечать материал дюбеля в процессе изготовления шпал и брусьев, а также при длительной эксплуатации в пути.
При изготовлении железобетонных брусьев с применением пропаривания бетона дюбели будут подвергаться нагреву до 95°С, поэтому должна быть обеспечена формоустойчивость их конструкции при такой температуре.
В процессе эксплуатации дюбели не должны давать остаточных деформаций от ползучести материала при затяжке шурупов. Дюбели не должны снижать необходимой прочности на удержание шурупа при действии многочисленных климатических факторов, в том числе при замораживании и оттаивании, обладать необходимой стойкостью против старения.
С целью проверки соответствия выше перечисленным требованиям все намеченные полимерные материалы были подвергнуты лабораторным испытаниям по специально разработанной методике «Методические положения по испытанию полимерного материала для железобетонных шпал типа ШЗ-Д с рельсовым скреплением ЖБР-65Ш», утвержденной Департаментом пути и сооружений МПС России.
Методика предусматривала проведение лабораторных испытаний дюбелей:
- на формоустойчивость,
- на ползучесть,
- на морозостойкость,
- на стойкость против старения.
Испытание на формоустойчивость
Для испытания на формоустойчивость были изготовлены бетонные кубы с замоноличенными дюбелями из следующих материалов: полиэтилен, блоксо- полимер, полиамид, армамид и армлен. После изготовления кубы были помещены в термокамеру с температурой 95°С при влажности среды 95% и выдерживались в течение 6 часов.
После извлечения из камеры и остывания кубов в дюбели завинчивали шурупы без применения ключа. Во все дюбели, кроме изготовленных из полиэтилена, шуруп свободно завинчивался на всю высоту. Выступающая над бетоном часть шурупа составляла 15-30 мм, что свидетельствовало об отсутствии внутри дюбеля деформации его резьбы, т.е. обеспечивалась формоустойчивость конструкции.
В дюбели, изготовленные из полиэтилена, шуруп завинчивался с большим трудом и выступающая над бетоном часть шурупа составляла 80-84 мм, что указывало на деформацию внутренней резьбы дюбеля под действием высокой температуры. Разрезание дюбеля по высоте подтвердило это заключение. Из этого следует, что дюбели из полиэтилена могут применяться только при производстве брусьев с естественным твердением бетона или пропариванием при температуре не выше 70-80°С, а остальные материалы отвечают установленным требованиям на формоустойчивость.
Испытание на ползучесть
Для испытания материала на ползучесть в бетонные кубы были замоно- личены дюбели из материалов, указанные в таблице 4.2. В дюбели были завинчены шурупы на глубину отверстия, уменьшенную на 15 мм — высоту вывинчивания шурупов вверх при выправке пути по уровню на такую величину. Между головкой шурупа и поверхностью куба были помещены отрезки трубы соответствующей длины и пружинные тарельчатые шайбы (рис.4.11).
Шуруп был завинчен динамометрическим ключом с усилием в стержне 4,5 тс, которое оставалось постоянно приложенным благодаря наличию пружинной тарельчатой шайбы. Штангенциркулем в 3-4 местах по кругу были измерены с точностью до 0,1 мм расстояния между головкой шурупа и поверхностью бетона. Эти измерения продолжались в течение 5 суток.
Результаты испытаний на ползучесть Результаты измерений, представленные в таблице 4.2, свидетельствуют о практически полном отсутствии остаточных деформаций материалов от ползучести и тенденции к их появлению.
Испытания на старение
Стойкость материала против теплового старения была оценена путем ускоренного испытания на климатическое старение по Методу 3 ГОСТ 9.707-81 [19]. Эти испытания, требующие специального оборудования и квалифицированных исполнителей, были выполнены на оборудовании ЗАО НИИ «Полипластик-Технопол».
Испытаниям были подвергнуты образцы полимерных материалов на основе полиамида (армамид) и полипропилена (армлен).
По методике, установленной стандартом, оценка теплового старения материала делается на основании результатов испытаний по трем режимам:
- режим 1 — тепловое старение при максимальной температуре для данного материала (температура кристаллизации) 180 ±5° в течение до 30 суток;
- режим 2 — тепловое старение при температуре на 20° ниже максимальной в течение 60 суток;
- режим 3 — имитация воздействий перепадов температуры от минус 50°С до плюс 60° в течение 30 циклов.
Для работы материала дюбелей наиболее значимым является 3-й режим, при котором один цикл испытания имитирует 1 год работы в любом климатическом районе.
В результате испытаний материалов по 3-му режиму были получены основные сравнительные показатели, представленные в таблице 4.4, наглядно свидетельствующие о преимуществе армлена перед армамидом по изгибной прочности и модулю упругости материала, хотя оба материала показали стабильность, достаточную для работы в течение 30 лет.
По совокупности всех результатов испытаний по старению материалов установлено, что стеклонаполненный композиционный материал на основе полипропилена (Армлен СВ 30-2Т) по величине снижения физико-механических свойств, моделирующих длительную эксплуатацию в условиях умеренного и холодного климата, превосходит армамид ПА ТМ и поэтому по рассматриваемой характеристике он рекомендован для изготовления дюбелей.
Реализация разработок по шурупно-дюбельному скреплению
С учетом результатов всего комплекса лабораторных испытаний материалов, наиболее целесообразным материалом для изготовления дюбелей является армлен. Эта рекомендация принята Департаментом пути и сооружений МПС для опытно-промышленной партии дюбелей.
Ввиду сложности изготовления брусьев и специфичности скреплений на переводных брусьях, для ускорения результатов, полигонные и эксплуатационные испытания были проведены на железобетонных шпалах.
Для полигонных испытаний на Экспериментальном кольце ГУП ВНИ- ИЖТ на Вяземском заводе ЖБШ была изготовлена опытная партия шпал (в количестве 50 штук). Участок пути с шурупно-дюбельным скреплением был уложен в кривой радиусом 420 мм. К настоящему времени (1.08.2003 г.) по нему пропущено на 270 млн. т. брутто. Полигонные испытания опытного участка показали положительный результат и поэтому принято решение о расширении испытаний на базе опытно-промышленной партии. С этой целью для выпуска опытно-промышленной партии железобетонных оснований с шурупно- дюбельным прикреплением, была разработана конструкторская документация на шпалу, дюбель и шуруп, которые согласованы с изготовителями и утверждены в МПС России.
Объем опытной партии — 5 км. Дюбели были изготовлены ЗАО «Полимер» и Люберецким заводом «Пластмасс», которые направлены на Вяземский завод для изготовления шпал ШЗ-Д.
Шурупы изготовлены ОАО «Магнитогорский метизно-металлургический завод» холодным способом. Качество их недостаточно хорошее, поэтому одновременно решается вопрос об изготовлении партии шурупов на ОАО «Череповецкий сталепрокатный завод» горячим способом.
Остальные элементы скреплений были аналогичны болтовому скреплению ЖБР-65. Все необходимое для сборки было реализовано на ОПМС-27 города Армавир на Северо-Кавказской железной дороге.
Вывод
- Применение шурупно-дюбельного скрепления следует считать одним из вариантов решения проблемы обеспечения стабильности ширины рельсовой колеи на стрелочных переводах с железобетонными брусьями. При этом скреплении может быть достигнуто повышенное сопротивление колеи действию горизонтальных поперечных нагрузок от подвижного состава включением в работу на сдвиг стержней шурупов, имеющих увеличенную площадь контакта с дюбелем из полимерного материала.
- Обеспечение нормального взаимодействия шурупа с дюбелем и исключение излома шурупа под действием поперечных нагрузок подвижного состава, в том числе при выправке пути по уровню подъемкой, может быть достигнуто:
увеличением длины подголовочного цилиндрического участка стержня шурупа на расчетную высоту подъемки (20-25 мм);
увеличением длины верхнего цилиндрического участка внутреннего канала в дюбеле на ту же величину, чтобы при подъемке резьбовая часть шурупа не выходила из канала дюбеля. Исходя, из этих условий разработаны новые конструкции шурупа и дюбеля. - В качестве материала дюбеля по результатам лабораторных испытаний и физико-механических свойств может быть рекомендован армлен (полипропилен, армированный стекловолокном).
Результаты исследований и лабораторных испытаний свидетельствуют о целесообразности проведения широких полигонных и эксплуатационных испытаний пути с шурупно-дюбельным способом прикрепления рельсов к железобетонным шпалам и брусьям с использованием шурупов типа ЦП-54 и дюбелей по проекту ВНИИЖТ 2002-10 из армлена (или аналогичного материала).
Применение дюбеля в шпалах типа ШЗД с бесподкладочным упругим скреплением типа ЖБР-65Ш уже утверждено соответствующими нормативными документами для эксплуатационных испытаний в 2003 году. В конце 2002 г. на экспериментальном кольце заложен опытный участок пути с таким скреплением. - Шурупно-дюбельный способ прикрепления стрелочных подкладок и рельсовых подкладок раздельного скрепления к железобетонным переводным брусьям с установкой двух шурупов типа ЦП-54 и двух дюбелей типа 2002-10 в одном поперечном сечении бруса позволит увеличить сопротивление пути действию горизонтальных поперечных сил от подвижного состава и позволит повысить стабильность ширины рельсовой колеи.
Используемая литература
- ГОСТ 9.707-81. Материалы полимерные. Методы ускоренных испытаний на климатическое старение. Изд-во стандартов. 1982. 19 с.
- Коган А .Я. Веритикальные динамические силы, действующие на путь. М.: Транспорт. 1996. 206 с.
- Краткий справочник конструктора нестандартного оборудования, В 2-х томах. T.l/В.И.Бакуменко, В.А.Бондаренко, С.Н.Косоруков и др.; Пол общ. ред. В.И.Бакуменко. М. Машиностроение. 1997. 539 с.