Сейчас ваша корзина пуста!
ОЦЕНКА И ПРОГНОЗИРОВАНИЕ НАДЕЖНОСТИ СТРЕЛОЧНЫХ ПЕРЕВОДОВ
Цикл статей:
Глава 1 — ОСНОВНЫЕ ПОЛОЖЕНИЯ СИСТЕМЫ ВЕДЕНИЯ ПУТЕВОГО ХОЗЯЙСТВА НА СТАНЦИЯХ
Глава 2 — ОЦЕНКА И ПРОГНОЗИРОВАНИЕ НАДЕЖНОСТИ СТРЕЛОЧНЫХ ПЕРЕВОДОВ
Глава 3 — ТЕКУЩЕЕ СОДЕРЖАНИЕ И РЕМОНТЫ СТРЕЛОЧНЫХ ПЕРЕВОДОВ
Глава 4 — ОЦЕНКА НАДЕЖНОСТИ РЕЛЬСОВЫХ ЦЕПЕЙ
Основные факторы, определяющие надежность стрелочных переводов
Стрелочные переводы являются многодетальной и сложной конструкцией железнодорожного пути. Отличаются они и сложностью взаимодействия с подвижным составом. Наличие неровностей в стыках и в зонах перекатывания колес с усовиков на сердечники и с рамных рельсов на остряки, не- равножесткостью и переменной массой пути по длине перевода, наличием направляющих элементов и коротких переводных кривых без возвышения рельсов вызывают нестабильность движения, искажение траектории перемещения колес, как в вертикальной, так и в горизонтальной плоскостях и высокий уровень динамических сил. Так вертикальные динамические силы от одного колеса в зоне перекатывания жесткой крестовины достигают 400…500 кН. С ростом осевой нагрузки и скорости эти силы увеличиваются.
Все это усложняет обеспечение необходимого уровня работоспособности узлов и элементов стрелочных переводов. Срок службы стрелочных переводов по этим причинам в 2…3 раза ниже, чем рельсов, а срок службы типовых крестовин в 3…4 раза ниже срока службы стрелочных переводов. Несмотря на это необходимо обеспечить выполнение заданных функций стрелочными переводами при сохранении эксплуатационных показателей в заданных нормативно-технической документацией пределах в течение требуемой наработки. Надежность стрелочного перевода, как всякого технического объекта, включает в себя понятия безотказности, долговечности и ремонтопригодности. Событие, заключающееся в нарушении работоспособности стрелочного перевода, называется отказом. При полном отказе объект перестает выполнять свои функции — пропускать поезда. При частичном отказе объект выполняет свои функции с пониженными параметрами (поезда пропускаются с пониженными скоростями).
Полным отказом стрелочного перевода следует считать те случаи, при которых любой из несущих или направляющих элементов согласно действующей классификации дефектов и повреждений становится остродефектным. Полным отказом стрелочного перевода следует считать и нарушение параметров ширины колеи, положения в плане и профиле, при которых создается угроза безопасности движения. /
Частичные отказы ухудшают работу стрелочного перевода, но позволяют продолжать его эксплуатацию. Они возникают в тех случаях, когда от
ступления выходят за допуски, установленные нормативно-технической документацией. Это относится к величинам износов элементов, размерам колеи, ординат, ширине желобов, состоянию по уровню. К частичным отказам целесообразно отнести гнилость переводных брусьев, износ промежуточных скреплений.
С позиций безопасности движения поездов наибольшего внимания требуют такие события, как появление трещин и изломов: остряков, рамных рельсов, крестовин, рельсов соединительных путей, контррельсов, деталей скреплений и прежде всего серьговых, контррельсовых, корневых и кресто- винных болтов, а также болтов, соединяющих рельсы подвижных сердечников; рабочих и контрольных тяг. Эти отказы являются внезапными, значительная часть которых обнаруживается только визуально, так как методы и средства диагностики и прогнозирования состояния перечисленных элементов и соединений не отработаны.
В общем случае стрелочный перевод следует считать восстанавливаемым объектом, однако, ввиду того, что вопросы восстановления переводов являются самостоятельной комплексной проблемой, показатели надежности элементов переводов принимаются, как для невосстанавливаемых объектов, или восстанавливаемых, работающих до первого отказа. Что касается последующей работы восстанавливаемого объекта, то она существенно отличается от невосстанавливаемого.
Критериями надежности невосстанавливаемых объектов являются:
- вероятность безотказной работы Р(1)\
- плотность распределения наработки до отказа
- интенсивность отказов
- средняя наработка до первого отказа Тср.
Вероятностью безотказной работы называется вероятность того, что при определенных условиях эксплуатации в заданном интервале времени или в пределах заданной наработки не произойдет ни одного отказа. Согласно определению
Р{0 = Р(Т>0 ,
(2.1)
где ^ — время или наработка, в течение которой определяется вероятность безотказной работы; Т — время или наработка от начала до первого отказа.
Вероятность безотказной работы по статистическим данным об отказах оценивается выражением:
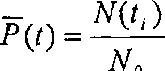
где N0 — число изделий в начале испытаний;N(t{) — число безотказно проработавших изделий к моменту времени При большом числе изделий N0 статистическая оценка
Р(0 практически совпадает с вероятностью безотказной работы P(t). На практике иногда более удобной характеристикой является вероятность отказа F(t).
Вероятностью отказа называется вероятность того, что при определенных условиях эксплуатации в заданном интервале времени возникнет хотя бы один отказ. Отказ и безотказная работа являются событиями несовместимыми и противоположными, поэтому
F(t) = P(t<T) ,— r(t)
F(t) = \-P(t), = N0
(2.3)
гдеr(tj) ЧИСЛО отказов К моменту времени tj.
Плотностью распределения наработки до отказа называется отношение числа отказавших изделий в единицу времени к первоначальному числу испытываемых изделий при условии, что все вышедшие из строя изделия не восстанавливаются.
Плотность распределения наработки до отказа f(t) является дифференциальной формой закона распределения наработки до отказа:
f(t) = -P\t) = F(t) ,
F{t)=\f{t)dt , P{t) = \-\f{t)dt
(2.4)
График f(t) часто называют кривой распределения наработки до отказа. Статистическая оценка плотности вероятности безотказной работы имеет вид
I(I) = л,/W0Л‘ >
(2.5)
где w — число отказавших изделий в интервале времени At. Интенсивностью отказов называется отношение числа отказавших изделий в единицу наработки к числу изделий, безотказно работающих к рассматриваемому моменту времени:
I(t) = ni/AtN(tt)
(2.6)
Вероятностная оценка интенсивности отказов находится из выражения
m =NoIP(t)
(2.7)
Интенсивность отказов представляет собой условную плотность вероятности возникновения отказа невосстанавливаемого объекта, определяемую для рассматриваемого момента времени или наработки при условии, что до этого момента отказа не произошло.
Интенсивность отказов и вероятность безотказной работы связаны между собой зависимостью
Р(0 = -е °
(2.8)
Важнейшей из характеристик является средняя наработка до первого отказа, которая определяется как математическое ожидание величины V.
мг = ТсР = \PiOdt
(2.9)
По статистическим данным об отказах средняя наработка до первого отказа вычисляется по формуле
где — время (наработка) безотказной работы /’-го образца изделия; N0 — число испытуемых образцов.
Основной характеристикой рассеивания случайной величины ? является дисперсия этой величины, определяемая как
За меру рассеивания принимают также среднее квадратическое отклонение (или стандарт), равное квадратному корню из дисперсии, взятому с положительным знаком.
Если нужно оценить степень рассеивания ряда при помощи безразмерной характеристики, то в этом случае используют коэффициент вариации.
Рассмотренные критерии надежности позволяют достаточно полно оценить надежность невосстанавливаемых изделий. Они также позволяют оценить надежность восстанавливаемых изделий до первого отказа.
Модели отказов элементов стрелочных переводов
Отказы элементов стрелочных переводов — нарушение нормальной их работы вследствие износа, превышающего установленные допуски, или возникновения дефектов, нарушающих безопасность движения поездов.
При совместном действии постепенных и внезапных отказов значение Р может быть подсчитано по теореме умножения вероятностей, так как событие — безотказность работы элемента за время t заключается в выполнении двух условий: безотказности от износовых повреждений Ри (0 и безотказности от внезапных выходов из строя Рв (У). При независимости этих отказов
Р(0 = Ри(с)Рв(0
(2.15)
Таким образом, если известны параметры законов распределения ( Тср , а,, X ), можно подсчитать вероятность безотказной работы элемента или узла стрелочного перевода.
Модель процесса изнашивания детали до предельного состояния приведена на рисунке 2.1. Здесь показаны отдельные кривые износа однотипных изделий. Предполагается, что по достижении износа, равного предельно допустимому т]пр, ресурс детали Т исчерпывается и наступает состояние отказа.
В связи с различием кривых наблюдается рассеивание ресурса Т. Случайные величины ресурса имеют плотность рассеивания /(?). Такая модель может быть использована для приближенного описания всех видов изнашивания за исключением усталостного выкрашивания и схватывания. В общем случае зависимость износа детали как случайной функции наработки может быть представлена в виде
//(О = аТр
(2.16)
Проведенные исследования изнашивания деталей переводов позволяют считать коэффициент детерминированной величиной для определенного конструктивного решения деталей.
Случайная величина а зависит от конструкции переводов и условий их работы. При коэффициенте вариации уа=5а1та в пределах у= 0.1 … 0.4 можно с достаточной точностью считать, что она подчиняется нормальному закону распределения. При к> 0,4 можно принимать распределение Вейбул- ла.
Зависимость для определения наработки до отказа запишется в виде
Т = {т1пр!а)»‘
(2.17)
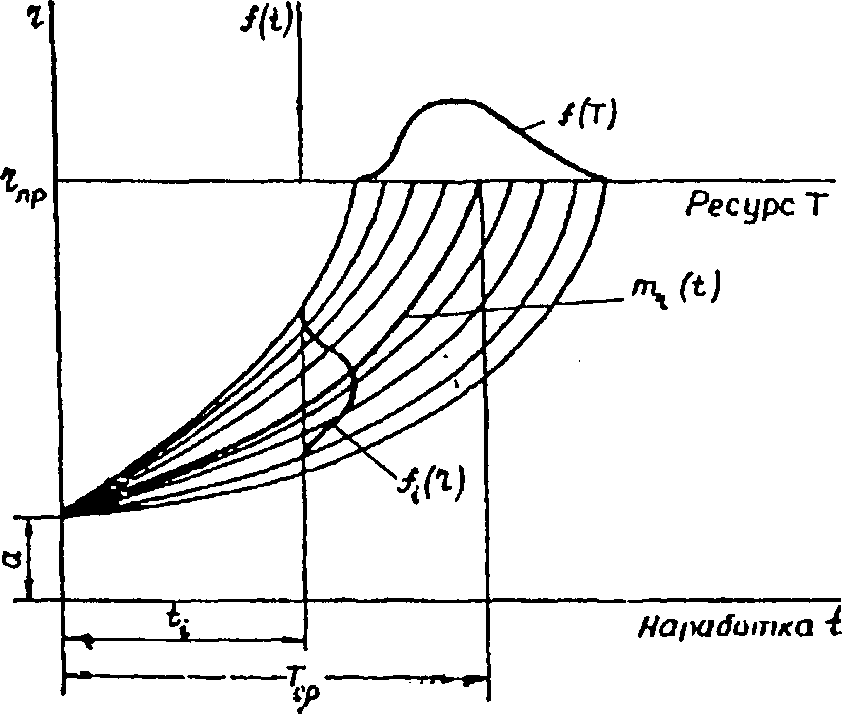
Рисунок 2.1 — Схема формирования постепенных отказов
При этом случайным аргументом является а , т.е. Т = ср(а) .Выражение для плотности вероятности распределения наработки до отказа может быть получено из известного соотношения
с1а
(2.18)
Л, где — функция, обратная (2.17). Используя зависимость (2.18), получим
Т/ + \ ЛпрР
Д0 = —,—ехР
Лпр = у?-™< Vі у
(2.19)
Функцию надежности определим из выражения (2.4). 1 г -Здесь (г) = -= Ге 2 ¿/л — табулированная нормальная функция распределения.
Параметры та, 5аи определяются на основе обработки статистических данных, собранных с конкретных стрелочных переводов.
Имея параметры та и можно определить гамма-процентный ресурс. Это наработка, при которой на 100 — у процента элементов износ превысит Т]пр.
Внезапные отказы составляют простой поток и вероятны в любой момент службы элементов стрелочных переводов. Распределение плотности вероятности сроков службы /в (г) при внезапных отказах подчиняется экспоненциальному закону, где Тср — средний тоннаж, наработанный элементом перевода до внезапного отказа в млн. т бр. Или Мт.
Вероятность безотказной работы в этом случае
Износ элементов стрелочных переводов
Изменившиеся условия эксплуатации пути и подвижного состава вызывают интенсивный боковой износ не только рельсов и гребней колес, но и элементов стрелочных переводов.
Для определения основных факторов, влияющих на интенсивность износа стрелочных переводов, в 2000 г. проведена работа по измерению износа их элементов на четырех станциях Западно-Сибирской железной дороги:
- ст. Инская в нечетной горловине парка «А и 3» прибытия поездов с Востока и Кузбасса;
- ст. Чулымская восточная горловина парка прибытия нечетных поездов;
- ст. Московка в нечетной горловине парка прибытия нечетных поездов;
- ст. Входная в четной горловине парка «А» прибытия четных поездов направлений из Исиль-Куля и Петрушенко.
Поток поездов, прибывающий на ст. Инская с Кузбаса, имел грузонапряженность около 60 млн. т-км бр. и среднюю осевую нагрузку 180 кНУось. Поток поездов с Востока имел грузонапряженность около 40 млн. т-км бр. и среднюю осевую нагрузку 140 кН/ось.
Нечетный поток поездов, проходящий через станции Чулымская и Московка, имел грузонапряженность около 100 млн. т-км бр. и среднюю осевую нагрузку 164 кН/ось.
Поток поездов, прибывающий в четную горловину станции Входная, имел грузонапряженность 55 млн. т-км бр. и среднюю осевую нагрузку 114 кН/ось.
При помощи штангенциркуля для измерения износа элементов стрелочного перевода проводились измерения вертикального и бокового износа рамных рельсов, сердечников и у совиков крестовины, наружного рельса переводной кривой стрелочных переводов типа Р65, 1/11 и 1/9 в сечениях: у острия остряка рамных рельсов, в середине переводной кривой. Вертикальный износ сердечника измерялся в сечении 40 мм и усовиков в сечении 20 мм. Периодичность контрольных промеров износа элементов стрелочных переводов по станциям составила в среднем 5.5 месяцев. Пропущенный тоннаж принят по данным учета выполненной тонно-километровой работы службы статистики Западно-Сибирской железной дороги.
По результатам наблюдений за износом элементов стрелочных переводов произведено определение приращений вертикального и бокового из- носов рамных рельсов, упорной рельсовой нити переводной кривой и крестовин за контрольный период. Определен удельный износ элементов стрелочных переводов в мм на 100 млн. т бр. прошедшего груза, приведенный в таблице 2.1.
Таблица 2.1 — Средний удельный износ элементов стрелочных переводов по станциям Западно-Сибирской дороги в мм на 100 млн. т бр. грузаЭлементы стрелочных переводов | Ст. Чулымская | Ст. Инская | Ст. Московка | Ст. Входная | ||||
верт. | бок. | верт. | бок. | верт. | бок. | верт. | бок. | |
Рамные рельсы | 7.6 | 9.4 | 7.0 | 8.5 | 6.1 | 7.6 | 6.9 | 7.9 |
Упорная нить переводной кривой | 8.3 | 14.6 | 12.8 | 15 | 8.4 | 12.7 | 6.9 | 7.9 |
Сердечник крестовины | 10.8 | — | 14.6 | — | 10.1 | — | 9.6 | — |
Зависимость износа сердечника крестовины, рамных рельсов и упорной нити переводной кривой от пропущенного тоннажа представлена на рисунках 2.2, 2.3 и 2.4.
Эти данные показывают, что износ элементов стрелочных переводов происходит весьма интенсивно. При этом боковой износ рамных рельсов на 20 %, а боковой износ криволинейных остряков на 40 % происходит интенсивнее, чем вертикальный износ соответствующих элементов, поэтому их заменяют по износу практически одновременно. Предельно допустимый боковой износ рельсов упорной нити переводной кривой 15 мм достигается при пропуске 100 — 120 млн. т бр. пропущенного груза, что соответствует сроку службы в течение 2-4 лет, в зависимости от грузонапряженности участка (ст. Чулымская, Инская, Московка).
Рисунок 2.2 — Зависимость износа сердечника крестовины от пропущенного тоннажа
Рисунок 2.4 — Зависимость износа упорной нити переводной кривой от пропущенного тоннажа: а — вертикальный износ; б — боковой износ
Установленный норматив бокового износа рамных рельсов в острие остряка 8 мм значительно сократил срок их службы. Сердечники крестовин приходится неоднократно наплавлять по мере достижения предельного износа.
Одной из основных причин увеличивающейся интенсивности износа элементов стрелочных переводов является отсутствие смазки, которая ранее осуществлялась из букс с подшипниками скольжения. Переход подвижного состава на буксы с подшипниками качения отрицательно сказался на сроке службы элементов стрелочных переводов.
В таблице 2.2 приведены величины интенсивности износа элементов стрелочных переводов, полученные на основании данных рисунков 2.2 — 2.4, допустимые величины износа, принятые согласно РТМ/ЦП-3-93 /120/ и средние сроки службы элементов стрелочных переводов, определенные по формуле (2.17) при ¡5 = 1. Реальные сроки службы крестовин будут больше, так как их изношенные сердечники и усовики подвергаются наплавке, а срок службы остряков и рамных рельсов будет меньше, приведенных в таблице 2.2, так как они выходят из строя еще и по выкрашиванию.
Таблица 2.2 — Интенсивность износа и средние сроки службы (наработка тоннажа) основных элементов стрелочных переводов типа Р65Наименование | Интенсивность износа, мм/Мт бр. | Допустимые величины износа, мм, на путях | Средняя наработка тоннажа, Мт бр., на путях | ||||
главных при К=101- 120 км/ч | прие- мо- отправочных | прочих | главных | прие- мо- отпра- воч- ных | прочих | ||
Вертикальный износ рамных рельсов и остряков | 0.07 | 6 | 10 | 12 | 86 | 143 | 171 |
Боковой износ рамных рельсов и остряков | 0.10 | 6 | 8 | 11 | 60 | 80 | 110 |
Вертикальный износ сердечника крестовины | 0.136 | 5 | 10 | 12 | 37 | 59 | 74 |
Боковой износ рельсов на переводной кривой | 0.14 | 15 | 15 | 18 | 107 | 107 | 129 |
2.4 Надежность работы крестовин
Количественно надежность работы крестовин определяется вероятностью того, что при определенных условиях эксплуатации в пределах заданной наработки не произойдет ни одного отказа.
Отказ крестовины — нарушение ее работоспособности вследствие износа элементов (усовиков и сердечника), превышающего установленные допуски или возникновения дефектов, нарушающих безопасность движения поездов. Постепенные отказы крестовин возникают в результате плавного изнашивания усовиков и сердечников (рисунок 2.5). Внезапные отказы (рисунок 2.6) вызываются образованием дефектов: выколов в переднем стыке врезки, горизонтальных и вертикальных расслоений, а также поперечных трещин сердечников и усовиков, выкрашиваний в зоне перекатывания колес с усовика на сердечник и обратно.
Из всех основных элементов верхнего строения пути жесткие крестовины имеют наименьший срок службы. Зависимость интенсивности выхода из строя крестовин типа общей отливки от наработки имеет монотонно возрастающий характер (рисунок 2.7). На момент нормативной наработки (90 Мт брутто) выходит из строя 36 % крестовин.
Такой характер зависимости свидетельствует о том, что ведущим процессом должен являться процесс накопления повреждении в металле крестовин. Это подтверждается теоретическими и экспериментальными исследованиями, выполнявшимися во ВНИИЖТ и ЛИИЖТ (ПГУПС) и других исследовательских организациях.
Наиболее частой причиной отказов крестовин является износ. По причине износа отказы получает большая часть крестовин 60 — 80 %.
Первоначальная стадия (ее при хорошо подогнанных литой и рельсовой частях крестовины может не быть) это осадка литой части относительно рельсовых усовиков. Осадка происходит в основном под первыми же проходящими поездами. Обычно величина осадки в зоне перекатывания колеблется от 0.5 до 1.5 мм. В отдельных случаях она может достигать 2 мм и более.
Вторая стадия работы крестовины — период интенсивного наклепа металла. При этом возникает поверхностный слой уплотненного металла с твердостью на поверхности до 400 НВ и более. Эта стадия длится до наработки 15-20 млн. т бр. Зависимость износа от наработки в этот период имеет экспоненциальный характер.
Ведущий процесс формирования износа на этой стадии пластическая деформация. Величина износа в нормируемых сечениях к концу периода наклепа-смятия достигает 1.5 — 2.5 мм, иногда 3.0 мм.
После завершения периода наклепа зависимость износа крестовин от наработки приобретает близкий к линейному вид. Ведущими процессами, определяющими износ крестовин, являются истирание металла и образование поверхностных выкрашиваний.
Выкрашивания на сердечниках и усовиках в зоне перекатывания составляют основную часть причин отказов крестовин, вышедших из строя по дефектам. Совместно с рядом других дефектов зоны перекатывания число отказов крестовин по этой группе дефектов составляет 17-20 %.
Другой зоной крестовины, подверженной образованию дефектов в виде выкрашиваний рабочих поверхностей, является зона передней врезки. В эксплуатации этими дефектами поражается значительное число крестовин — до 30 — 50 % при больших износах крестовин.
Весьма опасный вид дефектов крестовин типа общей отливки сердечника с наиболее изнашиваемой частью усовиков — трещины, возникающие в подошве и развивающиеся от дефектов литья или концентраторов напряжений, образующихся в процессе обработки литой части.
На рисунке 2.8 в обобщенном виде представлены данные по вероятности безотказной работы крестовин. Здесь особенно выделяются крестовины с подвижным сердечником, которые начали внедряться с 1985 г. К настоящему времени объем ежегодных поставок увеличен более чем в 2 раза. Из рисунка видна высокая (более 0.8) вероятность соблюдения нормативных сроков службы крестовин с поворотным сердечником, который стал одинаковым с таким же сроком службы стрелок и примерно в 3.5 раза превышает этот срок службы типовых крестовин. По мере завершения испытаний эта вероятность будет увеличена, так как более 50 % крестовин с поворотным сердечником, взятых под наблюдение, продолжает эксплуатироваться, и отказ их еще не наступил / 83 /.
Еще более полно соблюдаются гарантийные сроки службы этих крестовин. Вероятность безотказной работы для этих сроков достигает предельно высокого уровня — она практически равна единице.
Заметны преимущества по вероятности безотказной работы и крестовин с неподвижными элементами, упрочненных взрывом: эта вероятность несколько ниже, чем у крестовин с поворотным сердечником для гарантийного тоннажа (80 млн. т брутто) и приближается к такому же показателю для нормативного срока, составляя 0.8. Хотя преимущества крестовин с припуском на наклеп и упрочненных взрывом по сравнении с типовыми крестовинами по рассматриваемому здесь показателю менее значительны, чем по кре?- стовинам с подвижным сердечником, в целом они дают большой эффект, так
как объемы их выпуска более чем в 25 раз превышают объемы выпуска крестовин с НПК.
(2.27)
Теоретическая модель формирования постепенных отказов крестовин износового характера должна отражать зависимость величины износа от пропущенного тоннажа и осевой — нагрузки. Наиболее адекватно процесс износа крестовин можно описать зависимостью
ґРл«
г/ = аТр
J
где Т— наработанный тоннаж, млн. т бр.; Р и го — средняя осевая нагрузка подвижного состава на рассматриваемом участке и стандартная (обычно среднесетевая); а, ¡3 и у— эмпирические коэффициенты.
Для Западно-Сибирской дороги Р0—150 кН. Согласно исследованиям ДИИТа / 47 / 0.5. Для определения количественных значений а и ¡5 были взяты под наблюдение 270 крестовин типа Р65 марки 1/11 в главных путях с грузонапряженностью от 30 до 100 млн. т бр., средними осевыми нагрузками 100 … 190 кН. Наблюдения велись в период всего срока службы крестовин.
Обработка полученных данных позволила определить значения эмпирических коэффициентов, которые приведены в таблице 2.3.
Таблица 2.3 — Величины эмпирических коэффициентов | Характеристики | Наименования | Значения коэффициентов | |
Подстрелочное основание | крестовин | элементов | а | Р |
стандартные | сердечник | 0.136 | 1 | |
Деревянные брусья | усовик | 0.085 | 0.9 | |
упрочненные | сердечник | 0.118 | 1 | |
взрывом | усовик | 0.072 | 0.9 | |
Железобетонные брусья | стандартные | сердечник | 0.203 | 1 |
усовик | 0.127 | 0.9 |
По модели работы крестовин при одновременном действии всех типов отказов построены зависимости среднего срока службы крестовин с различной технологией их изготовления от осевой нагрузки (рисунок 2.9).Анализ графиков, приведенных на этом рисунке подтверждает квадратичную зависимость срока службы крестовин от осевой нагрузки. Упрочнение крестовин взрывом, осуществляемое на Новосибирском стрелочном заводе (НСЗ), повышает срок их службы на 15 %.
На дорогах России применяется практически единственный вид контррельсовых узлов. В качестве контррельса в таком узле используется прокатный спецпрофиль который с помощью болтов и вкладышей крепится к ходовому рельсу. Высокий уровень бокового динамического воздействия колес на контррельсы сопровождается возникновением в наиболее нагруженных точках и сечениях спецпрофилей напряжений величиной до 330 МПа.
На дорогах имеют место три вида дефектов контррельсов, служащие причиной их отказов: дефект в виде продольных трещин головки контррельса (возникают в нижней части головки); поперечные трещины головки контррельса, развивающиеся от ее верхней кромки; трещины, развивающиеся от отверстий для крепления контррельса к ходовому рельсу.
Направляющее действие контррельсов вызывает резкие сдвижки колесных пар при прохождении подвижным составом крестовинных узлов. В результате этого, а также из-за наведенных ударов, вызванных неровностями на крестовинах, на ходовых рельсах образуются вертикальные неровности в виде седловин. Развиваясь седловины служат причиной их отказов.
Надежность работы стрелки
Интенсивность отказов нарастает весь период работы остряков в пути (рисунок 2.10). Вид зависимости — пунктирная линия, свидетельствует о логарифмически нормальном характере этой зависимости, однако в основной период работы остряков зависимость интенсивности отказов остряков от наработки с достаточной для практической цели точностью можно считать линейной.
Характерно, что завершение «линейного периода» интенсивности отказов совпадает с завершением периода относительного постоянства удельной частости отказов что также свидетельствует о смене ведущего механизма отказов к моменту наработки 430 — 450 млн. т бр.
В целом не менее 65 % остряков изымается из пути по причинам недостаточной прочности и несовершенства технологии изготовления.
Основная причина отказов рамных рельсов характерные для стрелочных переводов дефекты I и II группы связанные с недостаточной контактно- усталостной прочностью металла.
Наиболее слабый конструктивный узел стрелки — корневое крепление остряка вкладышево-накладочного типа. В результате динамических воздействий в корне, дефекты возникают и в непосредственно примыкающей к нему зоне выпрессовки остряка и достигают 23 %. Этих недостатков лишены стрелки с гибкими остряками. Освоение массового производства стрелок с гибкими остряками потребовало переработки технологии производства остряков и переделки сборочных стендов, что окупилось в эксплуатации.
На момент достижения нормативной наработки 320 Мт, как видно из рисунка 2.11, основной показатель надежности — вероятность безотказной работы таких стрелок составляет 0.595, что в 1.1 раз превышает аналогичный показатель для стрелок с поворотными остряками. Однако применение гибких остряков не полностью решает вопросы создания высоконадежных стрелок, около 9 % отказов остряков происходит из-за выколов головки в стыках. Для решения этих вопросов была разработана стрелка с удлиненными гибкими остряками с приварными рельсовыми окончаниями, технология производства которой освоена Муромским стрелочным заводом в 1996 г.
Конструкция упругого прикрепления рамного рельса позволяет перераспределять энергию воздействия колес в упругую деформацию, что уменьшает боковой износ и накопление расстройств колеи на стрелке в процессе эксплуатации. Приварное рельсовое окончание позволяет сделать корневой стык обычным рельсовым стыком, допускающим сварку в пути и постановку изолирующего стыка в корне остряка, что дает возможность разработать современную двухблочную схему стрелочного перевода.
Эксплуатационная проверка на ст. Ильино, где стрелка проходит испытания в составе головного образца стрелочного перевода для путей 1 и 2 классов, показала работоспособность конструкции в целом и высокое качество сварных стыков рельсовых окончаний остряков / 57 /.
Стрелки горочных стрелочных переводов в процессе эксплуатации испытывают интенсивное боковое воздействие, что часто усугубляется плохим качеством укладки переводов в путь. На интенсивно работающих стрелках замену остряков приходится производить 3-4 раза в год.
Для продления срока службы стрелок горочных стрелочных переводов на Муромском стрелочном заводе создана новая конструкция стрелки. Головка остряка в зоне наибольших выкрашиваний почти в 2 раза шире, чем на стандартных. Изменена также и конфигурация рамных рельсов.
Основные размеры новой стрелки совпадают с размерами типовой, они являются взаимозаменяемыми, что обеспечивает их укладку в путь без реконструкции сортировочных парков.Частота и интенсивность отказов рельсовых элементов соединительных путей не превышает соответствующие величины для рельсов обычного пути такого же плана и профиля. Отсутствие подуклонки рельсовых нитей в пределах стрелочных переводов не вызывает образования специфический дефектов.
Анализ случаев браков и аварий на стрелочных переводах показывает, * что около 25 % всех случаев нарушения безопасности движения поездов относится к слабости подрельсового основания, а с учетом случаев нарушения норм содержания переводов, которые напрямую связаны с состоянием основания и скреплении, доля таких случаев в общей статистике нарушений безопасности движения поездов по стрелочным переводам превышает 36 %.
Несовершенство конструкции и качества промежуточных скреплений на стрелочных переводах является одной из наиболее неблагоприятных особенностей современных конструкций переводов, применяемых на российских железных дорогах.
Основные недостатки скреплений в этих зонах — повышенная жесткость, приводящая к быстрому расстройству узлов, недостаточное закрепление рельсовых элементов в горизонтальной поперечной плоскости, ухудшающее стабильность колеи, малые опорные поверхности для клемм и болтов, устаревший (заклепочный) способ соединения элементов. Помимо этих общих недостатков конструкции скреплений в пути имеют место изломы башмаков, трещины лафетов, расстройство корневых стыков остряков и хвостовых стыков подвижных и неподвижных сердечников крестовин, ускоряющих выход из строя стрелочных переводов по причинам недостатков конструкции и технологии изготовления.
Анализ работы и предложения по совершенствованию стрелочных переводов проекта 2750
На сети дорог интенсивно укладывают стрелочные переводы типа Р65 щ марки 1/11, проекта 2750, па железобетонном подрельсовом основании
(стрелка с гибкими остряками длиной 13320 мм, крестовина с приварными рельсовыми окончаниями длиной 6995 мм). На Западно-Сибирской магистрали эту работу выполняют с июля 1998 г. и в настоящее время эксплуатируют свыше 250 таких переводов / 83 /.
Крестовину с приварными рельсовыми окончаниями изготавливают в двух вариантах. Первый вариант — сваренные между собой продольной электродуговой сваркой рельсовые окончания, последующая контактная их сварка через промежуточный элемент с сердечником крестовины. Второй вариант — сваренный контактной сваркой сердечник крестовины с одним рельсовым окончанием (второе рельсовое окончание соединяется при помощи болтов); его используют только для лево- или правосторонних переводов.
Применяют сборные крестовины с врезной и неврезной конструкциями рельсовой и литой частей усовиков, контррельсовый узел с контррельсом, вкладышами не связанный с путевым рельсом.
Наряду с корневым предусмотрено промежуточное, в средней зоне остряков, кулачковое противоугонное устройство. Для плотного прилегания остряков к рамным рельсам и соблюдения минимального желоба между отведенным остряком и рамным рельсом имеется дополнительное переводное устройство с продольной тягой.
По стрелочным переводам прошло в основном от 0.2 до 120.0 млн. т груза, а у одного наработка достигла примерно 300 и у шести — 200 млн. т груза. Условия эксплуатации: грузонапряженность достигает примерно 90 млн. т-км брутто на 1 км в год, скорость движения грузовых и пассажирских поездов по прямому направлению переводов соответственно 80 и 100 км/ч, по боковому — 40 км/ч.
За время эксплуатационных испытаний изъято 44 крестовины, два остряка и один рамный рельс (таблицы 2.4 и 2.5).
Таблица 2.4 — Статистика отказов крестовинПропущенный тоннаж, млн. т груза | Количество изъятых крестовин | Нарастание изъятия | Средний тоннаж наработки, млн. т | ||
шт. | % | шт. | % | ||
0-10.0 | — | — | — | — | — |
10.1-20.0 | 1 | 2.27 | 1 | 2.27 | 14.6 |
20.1 -30.0 | 3 | 6.82 | 4 | 9.09 | 24.35 |
30.1 -40.0 | и | 25.00 | 15 | 34.09 | 32.15 |
40.1 -50.0 | 9 | 20.45 | 24 | 54.54 | 37.03 |
50.1 -60.0 | 6 | 13.63 | 30 | 68.17 | 40.04 |
60.1 -70.0 | 5 | 11.36 | 35 | 79.53 | 43.48 |
70.1 -80.0 | 3 | 6.82 | 38 | 86.35 | 45.88 |
80.1 -90.0 | 2 | 4.55 | 40 | 90.90 | 47.96 |
90.1 — 100.0 | 2 | 4.55 | 42 | 95.45 | 50.22 |
100.1 — 110.0 | 2 | 4.55 | 44 | 100.00 | 52.80 |
Таблица 2.5 — Причины изъятия крестовинДефекты | Количество изъятых крестовин, шт. | Доля от общего количества изъятых, % | Наработка, млн. т груза | |
средняя | минимальная/максимальная | |||
У.41.2 С.46.2 | 4 | 9.09 | 67.98 | 50.3/107.1 |
ДС.13.2 ДС.14.2 | 13 | 29.55 | 53.58 | 29.8/94.2 |
ДУ.12.2 ДУ.13.2 | 18 | 40.91 | 55.79 | 14.6/106.9 |
В зоне сварного шва (выкрашивание, С.26.3, С.56.3) | 8 | 18.18 | 38.08 | 27.4/43.8 |
ДС.60.1 | 1 | 2.27 | 46.0 |
Как видно из таблиц, средняя наработка 44-х крестовин составила 52.8 млн. т груза, наименьшая 14.6 и наибольшая 107.1 млн. т груза. До пропуска 30.0 млн. т изъяли четыре крестовины (14.6; 25.6; 27.4 и 29.8 млн. т) или 9.09 % общего количества изъятых со средним пропущенным тоннажом 24.35 млн. т груза. После наработки более 90 млн. т (средняя 101.28 млн. т) вышло из строя также четыре крестовины (94.2; 96.9: 106.9; 107.1 млн. т).
В диапазоне от 30.1 до 50.0 млн. т и от ЗОЛ до 70 млн. т пропущенного груза вышло из строя соответственно 45.45 и 70.44 %, а с наработкой до 80.0 млн. т — 86.35 % после пропуска в среднем 45.88 млн. т груза. Больше всего крестовин (25 %) изъяли в интервале 30 — 40 млн. т груза.
Из 44-х крестовин из-за износа, выкрашивания поверхности усовиков и сердечников, дефектов сварного шва и трещин хвостовой литой части сердечника сняли соответственно 4 (9.09 %), 31 (70.46 %), 8(18.18%) и 1(2.17%) крестовин.
Глубина выкрашивания поверхности катания усовиков и сердечников достигает 5 мм, наибольший износ (усовиков) составляет 8 мм и более. Вышли из строя два остряка (дефекты ДО.20.2, тоннажи отказа 69.2 и 75.7 млн. т груза) и один рамный рельс (дефект ДР.21.2, тоннаж отказа 53.6 млн. т груза).
Крестовины с врезной конструкцией литой и рельсовой частей усовиков поражаются дефектами выкрашивания по врезке. На отдельных крестовинах с одним приварным рельсовым окончанием имеются выколы головки окончания в заднем торце крестовины.
Ранее испытанные на Западно-Сибирской дороге две крестовины с приварными рельсовыми окончаниями неврезной конструкции (стрелочные переводы на деревянных брусьях проектов 2717 и 2718) изъяли после пропуска 135 и 136 млн. т груза, а третью — 51 млн. т в связи с заменой перевода. Наибольший износ усовиков отказавших крестовин не превысил 8 мм.
Длительный опыт эксплуатации на дороге в аналогичных условиях стрелочных переводов типа Р65 марки 1/11 проекта 2193 на деревянных брусьях показал, что по обычным крестовинам сборной конструкции можно пропустить не менее 100 млн. т груза и даже 150 млн. т и более.
Поверхность катания рамных рельсов, остряков и ходовых рельсов переводов проекта 2750 дефектами выкрашивания повреждается после пропуска примерно 50 — 80 млн. т груза. Стрелочные башмаки с приварными подушками и выштампованными ребордами служили безотказно. Отмечен массовый выход из своих рабочих гнезд П-образных клемм. Иногда реборды без вертикальной стенки отрывались в зоне выштамповки. Упругие прутковые клеммы повреждались при укладке переводов и были заменены на жесткие. Опыта эксплуатации стрелочных переводов проекта 2750 с упругими клеммами пока что мало.
Угон рельсовых элементов стрелок не наблюдается. Из-за зазоров в зоне стыков появляются смятия поверхности головки рельсов, а также разрушение подрельсового основания и самих брусьев. Нарушается порядок использования проектов гарнитур. Вместо гарнитур проекта 17425 применяются гарнитуры проектов 16762 и 16739. Элементы скреплений контррельсового узла с вы штампованными ребордами не выходили из строя.
Половина обследованных переводов не оборудована продольными тягами. Не соблюдаются размеры минимального желоба между отведенным остряком и рамным рельсом, остряки не прилегают к рамным рельсам.
Имеются отступления в содержании элементов крестовинного узла по уровню. Понижения обеих контррельсовых нитей от уровня крестовины достигают 21 и 4 мм (станция Калачинская), 16 и 7 мм (станция Колония). Выправить на балласте такие отступления невозможно (для их ликвидации используют подрельсовые и нашпальные прокладки).
Нестандартные нашпальные прокладки при укладке порой обрезают так, что не остаются буртики с одного торца. Железобетонные брусья в целом повышают стабильность продольного профиля стрелочных переводов, a Taк же их положение в плане.
Для повышения качества стрелочных переводов типа Р65 марки 1/11 проекта 2750 намечено сделать следующее.
Предполагается рассмотреть возможность внедрения конструкций крестовин НПК при грузонапряженности свыше 40 млн. т-км брутто на 1 км в год (это касается также переводов проектов 2717 и 2718). Для снижения жесткости подрельсового основания будут предусмотрены демпфирующие прокладки повышенной, по сравнению с применяемыми, упругости, в том числе и большей толщины (в первую очередь для зон стрелки, крестовины и контррельсового узла). Намечено внести изменения в геометрию железобетонных брусьев, создать новые и усовершенствовать существующие конструкции узлов скреплений, в том числе с упругими элементами (это же касается переводов проектов 2717 и 2718), а для снижения динамических воздействий на
1 стрелочные переводы применить аллюмотермитную сварку рельсовых элементов в зоне переводов (то же проектов 2717 и 2718) / 83 /.
Предстоит внедрить разработанные ВНИИЖТом и ПТКБ ЦП контррельсовые узлы с контррельсовым уголком, разработать способы регулировки ширины колеи и повышения ее стабильности, в связи с широким применением железобетонного подрельсового основания выполнить исследования по созданию оптимальных норм и допусков устройства и содержания колеи в пределах переводов.
Качество изготовления переводов не обеспечивает заданное укрытие остряков, что приводит к изъятию стрелок из эксплуатации. Поэтому заводу нужно строго соблюдать требования конструкторской документации.
По нашему мнению, важно провести исследования, связанные с оптимальными механическими характеристиками, в том числе твердости металл а при упрочнении крестовин, предназначенных для эксплуатации на железобетонном подрельсовом основании, а также откорректировать конструкторскую документацию с целью размещения болтов упорных накладок и клеммных болтов, исключающего их соприкосновение. Для продления сроков службы крестовин, остряков, рамных рельсов, рельсов соединительных путей следует своевременно шлифовать накаты на них.
Имеется существенный дефект брусьев — изгиб в вертикальной плоскости, который невозможно исправить в эксплуатационных условиях, поэтому надо усовершенствовать технологии их изготовления. Кроме того, в железобетонных брусьях необходимо предусмотреть отверстия для соединителей и арматуры пневмообдувки переводов.
Учитывая особенности движения поездов в пределах крупных узлов А специализированных парков (ограниченные скорости движения, интенсивное движение по боковому направлению переводов), намечено усовершенствовать конструкцию стрелочных переводов применительно к этим условиям. Созданные для скорости 100 — 120 км/ч переводы вряд ли оправданно использовать при скорости не более 50 — 60 км/ч, хотя не следует сильно расширять номенклатуру проектов.
При движении поездов преимущественно по ответвленному направлению переводов быстро появляется боковой износ элементов на упорной нити. Поэтому важно усилить, укрыть и защитить криволинейные остряки, усилить передние вылеты рамных рельсов, а также повысить стабильность колеи, в том числе в зоне передних вылетов рамных рельсов. Соответствующие работы выполняются. Крестовины с криволинейной геометрией также будут лучше соответствовать условиям эксплуатации.
Интенсивному износу подвергаются стрелочные переводы, уложенные по схеме примыкания переднего стыка рамного рельса одного перевода к переднему стыку рамного рельса другого перевода с одно- и разносторонним ответвлениями при интенсивном движении поездов по боковым направлениям с одного перевода на другой. Решений, связанных с упрощением схемы укладки, пока нет, поэтому предполагается усилить зоны передних вылетов рамных рельсов и защитить их, в частности контррельсами-протекторами, усилить и укрыть остряки, из-за которых возникает больший боковой износ рамных рельсов. Разрабатываются меры повышения стабильности колеи и более совершенные, соответствующие условиям эксплуатации, нормы и допуски ее содержания.
У обычных стрелочных переводов типа Р65 марки 1/11 при таком неблагоприятном вписывании подвижного состава даже при костыльном скреплении боковой износ рамных рельсов в передних вылетах достигает 14-15 мм уже поело пропуска примерно 15-20 млн. т груза. Кроме совершенствования самих конструкций, предназначенных для таких условий, целесообразно внести изменения в нормы бокового износа рельсовых элементов, в нормы и допуски содержания колеи в зоне передних вылетов рамных рельсов, а также увеличить укрытие остряков.
Вновь созданные и улучшенные элементы переводов — контррельсы- протекторы, контррельсы, не связанные вкладышами с путевыми рельсами, крестовины с приварными рельсовыми окончаниями, усиленные стрелочные, контррельсовые и крестовинные подкладки с приварными и вы- штампованными подушками и ребордами, раздельное с повышенными ребордами скрепление в пределах соединительных путей — усилили в целом конструкцию в сложных условиях эксплуатации. Исключение стяжных пс*- лос и изолирующих стыков в зонах стрелки и крестовинного узла повысило надежность рельсовых цепей.
Переводы, во-первых, для небольших скоростей движения, во- вторых, с интенсивным движением по боковому направлению, и, в-третьих, с укладкой рамных рельсов стык в стык, можно объединить в одну группу. Отдельная группа — переводы для кривых участков пути.
Один из основных недостатков, связанный с использованием обычных переводов в кривых, — неприлегание остряков к рамным рельсам. Оба остряка и оба рамных рельса должны иметь криволинейные очертания. Прямой остряк приходится выгибать в обратную сторону, в результате чего такой ответственный элемент работает в режиме упругого отжатия. В крестовинном узле видны следы набегания и ударов колес в отводы усовиков и контррельсов. Следовательно, нужны специальные переводы для кривых.
Первые опытные образцы переводов односторонней кривизны типа Р65 марки 1/11 на деревянных брусьях изготовил Новосибирский стрелочный завод, причем в двух вариантах — с радиусами основных направлений 350 м и 600 м (соответственно ответвленных направлений — 165 м и 200 м). Они предназначены для скоростей по основному направлению соответственно 40 и 70 км/ч (по ответвленному — 25 и 30 км/ч). В последующем сделали опытный образец с радиусом 600 м на Муромском стрелочном заводе.
Анализ работы более 200 обычных переводов, уложенных в кривых на Южно-Уральской и Свердловской дорогах показал, что 95 % из них эксплуатируются в кривых радиусами от 150 м до 800 — 850 м, остальные 5 % — радиусами свыше 850 м.
Конструкции с радиусом 350 м предназначены для кривых от минимальных радиусов до 400 — 450 м, а с радиусом 600 м — от 400 — 450 м до 850 м. В кривых радиусами 350 и 600 м (± 50 м) эксплуатируется примерно по 30 — 35 % переводов общего количества уложенных в кривых, в кривых радиусами от минимального до 400 — 450 м и от 400 — 450 до 800 — 850 м тоже примерно поровну.
Разрабатывается также программа внедрения переводов типа Р65 марки 1/11 с железобетонным подрельсовым основанием в кривых участках скоростных линий и линий I — II классов. В зависимости от крутизны кривых будут укладываться или обычные конструкции или создаваться специальные с соответствующей корректировкой эпюр укладки.
Ликвидация стыков в пределах стрелочных переводов за счет сварки рельсовых элементов снижает динамические воздействия и повышает cpei- ки службы конструкций. Известны работы, связанные с термитной сваркой, выполняемые немецкой фирмой «Электро-Термит», словацкой — «Сна- га», чешско-французской — «Рельтех». Создается отечественная технология. Полигонные испытания (при средних статических осевых нагрузках 27 тс) сваренных алюмотермитной сваркой десяти стыков в пределах перевода типа Р65 марки 1/11 по технологии словацкой фирмы «Снага» (использовали термитную смесь марки 900) дали следующие результаты: четыре стыка вышли из строя после пропуска 343.5 млн. т груза, пять — после пропуска 224.3 млн. т, один стык — после пропуска 165.5 млн. т и еще один, испытывавшийся вне перевода, — после пропуска 625.0 млн. т. Гарантийный срок — 100 млн. т груза.
Все стыки «изъяты» из-за дефектов в элементах стрелочных переводов и рельсов. Выхода из строя сварных стыков по причинам, связанным с технологией сварки, не было. Стыки сварили, в том числе в переднем и заднем вылетах рамных рельсов, в переднем вылете крестовины НПК и в корне гибких остряков / 84 /.
Сотни стыков, сваренных термитным способом по технологии фирмы «Снага», проходят эксплуатационные испытания более четырех лет на сети дорог, в том числе и в суровых климатических условиях. Отказов в их работе не наблюдалось. Сварка стыков в пределах стрелочных переводов и использование крестовин НПК в переводах проекта 2750 повысят срок службы крестовинного узла и сделают весь перевод равнопрочным.
Сроки службы элементов стрелочных переводов
Средние сроки службы крестовин и ремкомплектов (остряков и рамных рельсов) установлены на основе оценки их надежности для прямых участков пути (таблице 2.6):
- со средней грузонапряженностью 60 млн. т бр.;
- со скоростями движения грузовых поездов — 80 км/ч;
- со средней статической осевой нагрузкой подвижного состава — 150 кН;
- соотношением грузопотоков по прямому и боковому направлениям стрелочных переводов, лежащих на главных путях, 75 и 25 % и 25 % и 75 % — на приемо-отправочных путях.
Влияние осевых нагрузок учитывается умножением нормативного срока службы стрелок и крестовин на коэффициент
Кр=(150/Рст)°\
(2.28)
где Рст — статическая осевая нагрузка подвижного состава.
Упрочнение крестовин взрывом повышает срок их службы на деревянных брусьях на 15 %, на железобетонных — на 13 %.
Таблица 2.6 — Средние сроки службы крестовин и ремкомплектов обыкновенных стрелочных переводов типа Р65 для условий Западно-Сибирской дороги Наименование элементов стрелочных переводов | Тип, марка перевода | Значения нормативного тоннажа для средних условий эксплуатации, млн т бр. | ||
на главных путях | на приемо- отправочных путях | |||
Крестовины с литым сердечником из высокомарганцовистой стали | Деревянные брусья | |||
Р65;1/9 | 90 | 115 | ||
Р65; 1/11 | 105 | 125 | ||
Железобетонные брусья | ||||
Р65;1/9 | 55 | 75 | ||
Р65; 1/11 | 65 | 85 | ||
Ремкомплекты (остряки и рамные рельсы) | Деревянные брусья | |||
Р65; 1/9; 1/11 | 110 | 130 | ||
Железобетонные брусья | ||||
Р65; 1/9; 1/11 | 65 | 85 |
Примечание: нормативные сроки крестовин указаны с учетом их ремонта.
При грузонапряженности более 25 млн. т бр. и осевых нагрузках более 210 кН стрелочные переводы типа Р50 не соответствуют условиям эксплуатации и подлежат замене в плановом порядке.
Продление срока службы крестовин
Основным способом продления службы крестовин является ремонт их наплавкой. Крестовины из стали Г13Л ремонтируют в пути электродуговой наплавкой в соответствии с требованиями технических условий ТУ 32ЦП — 671 — 92. К восстановлению наплавкой допускаются крестовины до достижения наибольшего износа, допускаемого инструкцией по текущему содержанию пути, а также при образовании на поверхности катания дефектов, которые требуется устранить наплавкой.
Не допускаются к восстановлению наплавкой острые крестовины с трещинами, отслоениями, выкрашиванием металла, раковинами, пленами, если после снятия дефектного металла на глубину 2 мм свыше допускаемого износа указанные дефекты остаются в металле.
В случае если дефект распространяется на большую глубину, крестовина должна быть заменена.
Наплавку крестовин производят на длину местного износа: сердечника — в пределах участка до сечения, где ширина сердечника 60 мм, а усовиков всех марок — на всю его длину.
При подготовке крестовин под наплавку используют переносные станки для обработки шлифовкой. После вышлифовки дефектного металла в сердечнике или на усовике местное углубление в нем, допускаемое на период наплавки, измеренное от поверхности перед восстановлением наплавкой, не должно превышать 7 мм. На длине 40 мм в крестовинах, эксплуатируемых на главных путях, и соответственно 10 и 50 мм — на приемо-отправочных и сортировочных.
Наплавка крестовин может выполняться при отрицательной и положительной температурах воздуха.
Наплавку крестовин производят только электродами марки ЦНИИН-4 по ГОСТ 10051 — 75 диаметром 4 мм постоянным током обратной полярности (плюс на электроде), короткой дугой притоке 120 — 140 А или переменным током 130 — 150 А. Работу выполняют только от исправного источника сварочного тока, имеющего амперметр и вольтметр.
Требуемую величину сварочного тока дополнительно контролируют плавлением электрода марки ЦНИИН-4 на куске металла. Время расплавления электрода диаметром 4 мм и длиной 300 мм должно составлять, при постоянном токе 60 — 70 с, при переменном — 50 — 60 с. Если электрод расплавился быстрее, ток нужно уменьшить, если медленнее — увеличить.
Запрещается подбирать режимы наплавки и опробование электродов непосредственно на крестовине, это разрешается выполнять только на куске металла.
При наплавке первого и второго слоев острых и тупых крестовин длина наплавленных валиков должна быть 90 — 100 мм, ширина 12-15 мм, высота 2.5 — 3.0 мм
Наплавку третьего и последующих слоев следует производить валиками шириной 18-22 мм и высотой не менее 3 мм. Кратер каждого валика должен быть выведен на наплавленный металл и заплавлен металлом электрода.
Наплавку первого и последующих слоев на сердечнике и усовиках ocf- рой крестовины производят с последовательным чередованием валиков как показано на рисунке 2.12.
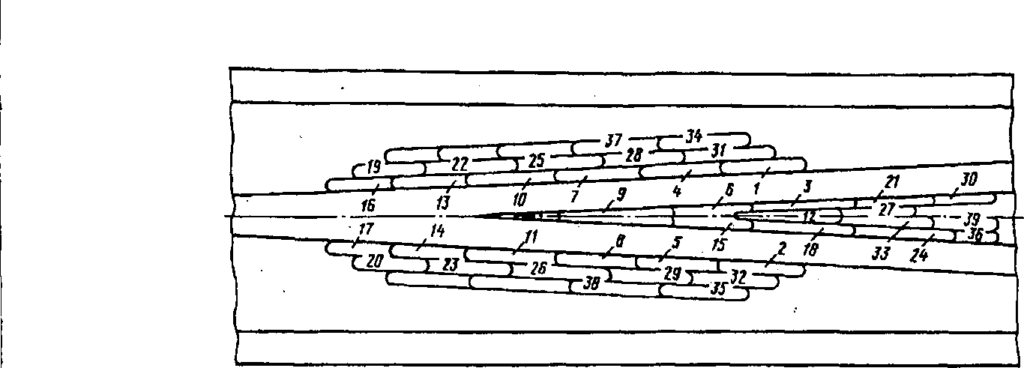
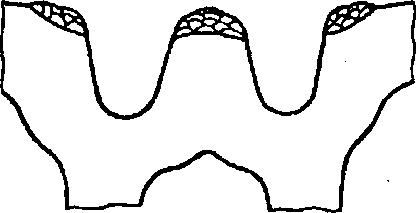
Рисунок 2.12 — Схема расположения валиков при наплавке крестовин (1 — 39 — слои наплавки)
Новым способом продления срока службы крестовин является упрочнение их науглероживанием / 79 /. Новая технология состоит в насыщении поверхности изнашиваемой части крестовины из стали марки Г13Л потоком атомарного углерода за счет обработки сварочной дугой угольного электрода при обратной полярности источника питания постоянного тока. Образующиеся карбиды железа и марганца высокой твердости располагаются по границам зерен аустенитного металла и предохраняют металл крестовины от износа на глубину науглероживания 1 … 1.5 мм.
Упрочнять поверхности сердечника и изнашиваемых частей усовиков из высокомарганцовистой стали марки Г13Л типов Р50 и Р65 марок 1/9 и 1/11 методом науглероживания можно как в пути, так и в стационарных условиях. Обрабатывать крестовины в пути рекомендуется после пропуска по ним не менее 5… 10 млн. т груза. Максимальный износ упрочняемых поверхностей крестовин (в сечении сердечника 40 мм) не должен превышать 2 мм. Науглероживать крестовины вне пути следует непосредственно перед укладкой.
Поверхности крестовин, подлежащих упрочнению, должны быть очищены от грязи, масла и следов коррозии. Поверхности крестовин, продолжительное время изъятых из эксплуатации, должны защищаться до металлического блеска. При шлифовании нельзя допускать местный поджог обрабатываемой поверхности.
Упрочнению подлежат участки крестовины в зоне перекатывания колеса, где происходит наиболее интенсивный износ (рисунок 2.13). Упрочнение участков поверхности крестовины с наиболее интенсивным износом производится отдельными точками (пятнами), в зоне которых металл крестовины расплавляется угольной дугой (рисунок 2.14).
Упрочнение выполняется электродами, соответствующими ТУ 1986 г. ИЛЕА 757351.0.35, диаметром 6 мм марки СК — 6. Не допускается применение электродов с омедненной поверхностью.
Упрочнение производится на постоянном токе обратной полярности (плюс на электроде) силой 150 … 160 А. Для этого используются сварочные агрегаты постоянного тока. Длительность горения угольной дуги после ее возбуждения должна составлять 2…4 с. При случайном преждевременном обрыве дуги допускается повторное зажигание ее по тому же пятну.
Диаметр точки (пятна) упрочнения на поверхности крестовины должен иметь размер 8 … 10 мм, допускается отклонение указанного диаметра на величину ± 2 мм. г
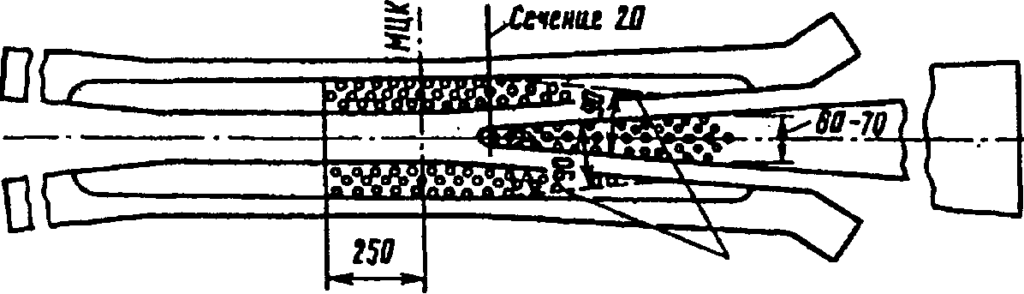
Рисунок 2.13 — Участки крестовин, подлежащие упрочнению
Расстояние между краями соседних точек (пятен) должно быть в пределах 3 … 8 мм. Допускается наличие не более 3 … 4 пар пятен упрочнения на каждом усовике и сердечнике при расстоянии между ними не менее 1 мм. Пятна упрочнения целесообразно располагать в шахматном порядке. Не допускается перекрытие одного пятна другим. Нанесение пятен должно производиться сначала по его осевой линии. Не допускается нанесение пятен упрочнения на металле рельсовых усовиков. Расстояние от пятна упрочнения (рисунок 2.14) до границы врезки литой части усовика должно быть не менее 5 мм.
По краям поверхности пятен упрочнения допускаются небольшие возвышения высотой до 0.5 … 0.7 мм. При большей их высоте они вышлифовываются заподлицо с основной поверхностью сердечника или усовика. Допускается углубление величиной до 1.5 мм в кратерной части пятен упрочнения.
При упрочнении крестовин в пути без перерыва движения поездов после каждого прохода поезда поверхность крестовины следует очистить от грязи и масла.
Упрочнение следует выполнять при температуре не ниже — 10°С. Во время дождя и снегопада производить упрочнение крестовины запрещается.
Экономическая эффективность наплавки и науглероживания крестовин
Для продления срока службы крестовин изнашиваемую часть усовиков и сердечников при небольшой густоте движения поездов наплавляли непосредственно в пути, а при большой — в стационарных условиях. В настоящее время при спаде объема перевозок в 2 — 3 раза, делают это преимущественно в пути с проковыванием наплавленного слоя проходящими поездами. Однако и после наплавки за срок службы стрелки все равно приходится 1 — 2 раза заменять крестовины.
В 1992 г. специалисты ВЗИИТа и ВНИИЖТа / 79, 80 / предложили новую технологию с использованием науглероживания.
В последние годы методом науглероживания обрабатывают 30 % крестовин, а остальные 70 % наплавляют. Какой же способ наиболее эффективный? Чтобы ответить на этот вопрос в 1997 г. мы собрали соответствующие данные в дистанциях и ПМС, подсчитали капитальные вложения и эксплуатационные расходы, определили сроки окупаемости и др.
В приведенных ниже примерах цены были приведены к ценам 2000 г. В таблице 2.7 дана стоимость упрочнения одной крестовины типа Р65 марки 1/11 методом науглероживания, в таблице 2.8 — стоимость материалов, необходимых для этой работы, в таблице 2.9 — затраты по основной заработной
плате рабочих, в таблице 2.10 — затраты на замену крестовины с деревянными брусьями. (В этих и следующих таблицах стоимость показана округленно.) Срок службы обыкновенных крестовин приняли в 3 раза меньшим, чем стрелки (стрелка рассчитана на пропуск 230 млн. т, а крестовина — 85 млн. т груза).
Таблица 2.7 — Стоимость упрочнения крестовины типа Р65 марки 1/11 методом науглероживанияНаименование затрат | Стоимость, руб. |
Сырье и материалы (см. расчет в таблице 2.8) | 41.8 |
Транспортно- складские расходы | 12.2 |
Основная заработная плата (см. расчет в таблице 2.9) | 35.8 |
в том числе премиальные | 17.9 |
Дополнительная заработная плата | 8.6 |
Отчисления на социальное страхование | 17.3 |
Расходы на содержание и эксплуатацию оборудования | 10.7 |
Общезаводские расходы | 107.5 |
Накладные расходы (15 %) | 35.0 |
Прибыль (15 %) | 46.2 |
НДС (20 %) | 61.6 |
Всего | 369.8 |
• Таблица 2.8 — Стоимость материалов для упрочнения крестовины
Стоимость, руб. | |||
Наименование затрат | Количество | Единичная | Общая |
Электроды С 6, кг Клеймы для клеймения, компл. Круги шлифовальные, шт. Материалы обтирочные, кг Транспортно-складские расходы, % | 4 0.01 0.9 0.06 30 | 2.1 336 0.4 40.8 | 8.40 0.03 32.4 0.02 12.2 |
Всего | — | — | 53.15 / |
Таблица 2.9 — Заработная плата при упрочнении одной крестовиныНаименование затрат | Количество | Стоимость, руб. | |
Единичная | Общая | ||
Наплавка или науглероживание кре | 7.32 | 1.763 | 12.9 |
стовины, чел.-ч | |||
Шлифовка крестовины, чел.-ч | 3.66 | 1.37 | 5.0 |
Премиальные, % | 100 | 17.9 | 17.9 |
Всего | — | — | 35.8 |
Таблица 2.10 — Затраты на замену одной крестовиныНаименование затрат | Количество | Стоимость, руб. 1 | |
Единичная | Общая | ||
Затраты труда, чел.-ч | 9.15 | 2.47 | 22.5 |
Эксплуатация машины ДГКу, маш.-см. | 0.5 | 54.73 | 27.3 |
Материалы, руб. | — | — | 963.0 |
Накладные расходы, % | 15 | 1013 | 151.9 |
Начисления на зарплату, % | 130 | 22.6 | 29.3 |
НДС, % | 20 | 1194.8 | 238.8 |
Всего | — | — | 1432.8 |
Расчет сделали с условием, что при трехкратном науглероживании срок службы крестовин увеличивается «до уровня» стрелки, а к моменту смены стрелочного перевода (стрелки) потребуется либо дважды заменить крестовину, либо трижды ее науглеродить. Смена крестовины за срок службы стрелки стоит 1432.8×2 = 2865.6 руб., а науглероживание (3 раза за срок службы стрелки) — 369.8×3 = 1109.4 руб., т.е. экономическая эффективность науглероживания за срок службы стрелочного перевода составит 1856.2 руб., а за год (при грузонапряженности 20 млн. т км брутто на 1 км в год и расчетном пропуске по стрелке 230 млн. т груза) будет равна (1856.2х20)/230 = 161.5 руб.
Стоимость одной наплавки (таблица 2.11) примерно такая же, как стоимость одного науглероживания (соответственно 364.2 руб. и 369.8руб.). 43 целом наплавка (3 раза за срок службы стрелки) немного дешевле: 364.2×3 = 1092.6 руб. Следовательно, экономический эффект наплавки одного стрелочного перевода за весь срок службы стрелки составит 2865.6 — 1092.6 = 1773 руб., а за год при тех же грузонапряженности и тоннаже — (1773×20)7230= 154 руб.
Таблица 2.11 — Стоимость наплавки одной крестовиныНаименование затрат | Количество, | Стоимость, руб. | |
% | Единичная | Общая | |
Стоимость материалов (см. расчет в | — | — | 50.56 |
таблице 2.12) | |||
Основная заработная плата рабочих | — | — | 35.6 |
в т.ч. премии (см. расчет в таблице 2.9) | — | — | 17.8 |
Дополнительная заработная плата | — | — | 8.6 |
Отчисления на социальное страхование | — | — | 17.3 |
Расходы на содержание и эксплуатацию | — | — | 10.7 |
оборудования | |||
Общезаводские расходы | — | — | 107.5 |
Внепроизводственные расходы | — | — | — |
Накладные расходы | 15 | 230.6 | 34.5 |
Прибыль | 15 | 265.2 | 39.8 |
НДС | 20 | 305.0 | 61.0 |
Всего | — | — | 364.2 |
Таблица 2.12 — Стоимость материалов для наплавки одной крестовиныНаименование затрат | Количество | Стоимость, руб. | |
Единичная | Общая | ||
Электроды ЦНИИ-4, кг | 4 | 1.61 | 6.44 |
Клеймы для клеймения, компл. | 0.01 | 3.6 | 0.03 |
Круги шлифовальные ПП 250x32x32, шт. | 0.9 | 36 | 32.40 |
Материалы обтирочные, кг | 0.06 | 0.38 | 0.023 |
Транспортно-складские расходы, % | 30 | 38.89 | П.67/, |
Всего | — | — | 50.56 |
Вывод таков. Методом науглероживания по возможности целесообразно упрочнять до 50 — 60 % крестовин — в первой половине их срока службы. Затем, когда необходимо восстановить профиль крестовин, лучше применять наплавку. Во всех случаях оба метода надо использовать своевременно. Нельзя запускать крестовины, доводя их состояние до предельной изношенности. Отправлять крестовины на ремонт в РСП только после того, как они выработали весь свой ресурс, экономически невыгодно. Своевременным оздоровлением усовиков и сердечников можно выровнять сроки службы крестовин и стрелок.
Продление срока службы остряков
Ремонт остряков выполняется в условиях ремонтных предприятий или специализированных участков, оснащенных технологическим, подъемно- транспортным и вспомогательным оборудованием, способным обеспечить ремонт остряков и удовлетворяющим санитарным нормам и правилам.
В состав ремонта остряков входят:
- очистка остряков;
- технический контроль годности остряков, в том числе дефектоскопи- рованием;
- восстановление и шлифовкой до ремонтных размеров изношенных и поврежденных наплывами и выкрашиванием поверхности остряков;
- устранение выкрашиваний на поверхности корня остряка наплавкой;
- шлифовка наплавленной поверхности корня остряка;
- дефектоскопный, геометрический и визуальный контроль отремонтированных остряков;
- маркировка отремонтированных остряков.
Остряки, имеющие износ более 2 мм должны обрабатываться строжкой.
Остряки с износом до 2 мм не подвергаются строжке, на них устраняются местные неровности шлифовкой.
Седловины глубиной до 2 мм уполаживаются шлифовкой с уклоном 1 мм на 1 м.
Перед восстановлением производится продольная пологая шлифовка выкрашиваний, волнообразных деформаций, седловин и других неровностей глубиной до 2 мм. При этом длина шлифуемого участка должна быть не менее чем на 4 мм больше длины дефекта. / Остряки, имеющие отслоения и выкрашивания (дефекты 0.17.1 и 0.18.1), а также смятия и вертикальный износ (дефект 0.41.1) на поверхности головки в торце корня остряка глубиной более 3 мм (не менее 1 мм) и длиной более 25 мм ремонтируются электродуговой наплавкой по технологии согласно ТУ 32.ЦП-533-88 с последующей шлифовкой наплавленного слоя.
Замер величины износа и разметка под наплавку головки корня остряка производится клиновым щупом с помощью металлической линейки длиной 1 м, точность измерения — 0.25 мм. При измерении глубины дефекта линейку устанавливают так, чтобы ее середина совпадала с наибольшей глубиной дефекта. Конец наплавки определяется местом, где износ не менее 0.5 мм.
Электродуговая наплавка выполняется электродом марки НР-70 по ГОСТ 10051-75 диаметром 5мм. До наплавки электроды прокаливаются в сушильном шкафу при температуре 160°С в течение 1 ч. Наплавку производить при постоянном токе (обратной полярности) 1 св = 200…240 А поперечными колебательными движениями электрода в направлении к оси остряка. Начинать наплавку со стороны нерабочей грани головки корня остряка, ширина валика 25 —30 мм, каждый последующий валик должен перекрывать предыдущий на 4 -5 мм так, чтобы не было подрезов и неровностей. Очередной валик наплавляется после удаления со смежного валика брызг металла и окалины. Толщина наплавляемого слоя металла должна быть не менее 3 мм. Кратер выводить на наплавленный металл и заплавить.
С целью выбора режима наплавки периодически производить контрольную наплавку на куске рельса длиной 70 мм на всю ширину головки.
Обработку наплавленных участков остряка производить абразивным инструментом после естественного охлаждения, не допуская прижогов.
Наплавленные концы остряков очищают металлической щеткой, на торце головки обрубают надтеки металла и под линейку шлифуют наплавленную поверхность и торец.
Наплавленные поверхности подвергают отпуску. Нагрев наплавленного слоя производят газопламенным или электроконтактным способом до I = 650°С.
При выполнении наплавочных работ по ремонту остряков учитывать следующий температурный режим:
- при температуре I = +5°С и выше наплавочные работы разрешается выполнять без предварительного подогрева;
- при температуре I = -Ю…+5°С подвергать зону наплавки предварительному подогреву до I = 250…300°С;
- при температуре ниже -10°С наплавка остряков запрещается.
Наплавленная и обработанная поверхность катания должна отвечать
следующим требованиям:
- поверхность головки должна быть ровной сплавным переходом от наплавленного к основному металлу;
- глубина местных неровностей наплавленного металла допускается не более 0.5 мм;
- предел твердости наплавленного металла должен быть не ниже твердости основного металла и не выше 359 НВ;
- повторная наплавка допускается при условии, что вертикальный износ головки конца остряка не более 3 мм, и металл первой наплавки не имеет дефектов, при наличии трещин, выкрашиваний и отслоений, металл первой наплавки полностью снимается. К технологическому режиму и качеству повторной наплавки предъявляются те же требования, что и к первичной наплавке;
- поверхность наплавки должна соответствовать поперечному профилю не наплавленной части остряка.
Остряки, имеющие изгибы в вертикальной и горизонтальной плоскостях (дефект 0.80), подвергаются правке прессами или другими приспособлениями.
После восстановления остряков допускаются следующие отступления:
- выкрашивания глубиной до 1 мм;
- седловины глубиной до 1 мм на 1 м длины;
- отклонения стрел прогиба до 1 мм.
Восстановление изношенных остряков подгорочных путей
Срок службы стрелочного перевода зависит от условий работы и долговечности его отдельных элементов — остряков, рамных рельсов и др. Одна из причин изъятия остряков из эксплуатации — износ и выкрашивание металла. Обследование горочных путей на сортировочной станции Инская показало, что остряки типа Р65 марки 1/6 изнашиваются на отрезке длиной до 2000 мм на глубину до 8 мм, а выкрашивание металла достигает соответственно 400 и 6 мм. При износе остряка и рамного рельса, превышающем допускаемые нормы, нарушаются оптимальные условия взаимодействия колес подвижного состава с элементами стрелочного перевода, что может привести к сходу поезда. Замена остряка на новый или старогодный не только экономически невыгодна, но и сложна. Трудность заключается в подборе остряка под изношенный рамный рельс. Или же необходимо заменять остряк и рамный рельс одновременно.
По данным ВНИИЖТа / 57 / ежегодно на железных дорогах России заменяют около 6000 стрелочных переводов. Поэтому восстановление наплавкой остряков с выкрашиванием или износом металла — один из наиболее экономически целесообразных способов продления срока службы переводов. Это особенно важно в связи с существенным повышением не только стоимости новых остряков и рамных рельсов, но и их замены в пути. Следует отметить, что ранее на наших дорогах ремонт остряков наплавкой не выполнялся.
Потребовалось разработать оптимальный способ наплавки, обеспечивающий минимальное тепловложение в основной металл при незначительном перемешивании наплавленного и основного металла. В основном металле не должно быть неблагоприятных структурных превращений, чего добиться особенно сложно для переменного поперечного профиля острия по длине. Кроме того, необходимо достигнуть высокой механической прочности того и другого металла.
Исследовав ручной дуговой и механизированный способы наплавки остряков и применив различные присадочные материалы, лучшие результаты получили с использованием электродуговой наплавки, когда при малом диаметре электрода глубина проплавления и деформация остряка наименьшие. Применяли два типа электродов, создающих структуру наплавленного металла перлитного и аустенитного классов с твердостью основного металла HV 284 — 351. Необходимую структуру в околошовной зоне основного металла получали, создавая требуемую температуру предварительного подогрева остряка перед наплавкой с последующим медленным охлаждением. Подогрев делали специальной многопламенной горелкой с применением пропана и кислорода /81/.
Режимы наплавки и нужную температуру предварительного подогрева остряка подбирали на основании серии экспериментов с опытными образцами при различных силе тока и напряжения, марки и диаметра наплавочного материала. Отремонтированные остряки исследовали металлографическим способом с измерением твердости наплавленного и основного металла в околошовной зоне. Во время наплавки ставили задачу: получить в ней основной металл остряка исходной структуры — сорбит закалки, при которой лучше сочетаются механические свойства металла — достаточно высокая прочность, пластичность и износостойкость. Удалось добиться структуры сорбита отпуска с обрывками ферритной сетки (твердость HV 299). Для этого надо предварительно подогревать остряк. Без такого подогрева структурные превращения в околошовной зоне и зоне термического влияния происходят по мартенситному типу.
Изношенные остряки восстанавливали непосредственно в пути. Перед наплавкой их очищали от мазута и грязи. Находили сечения 20; 30; 40 и 50 мм. В этих местах замеряли боковой и вертикальный износ. Поверхность катания/и бока остряка до сечения 40 мм обрабатывали с помощью шлифовального станка, затем тщательно осматривали и приступали к предварительному подогреву.
В зависимости от характера износа (работа остряка по боковому или прямому пути) восстанавливали либо боковую сторону, либо поверхность катания, при большом износе наплавляли обе его поверхности. После этого остряки обрабатывали шлифовальным станком.
В результате исследований разработали технологию по восстановлению электродуговой наплавкой изношенных остряков типа Р65 марки 1/6, эксплуатирующихся на горочных путях. За последнее время восстановлено около 100 остряков. Наблюдения показали, что в зависимости от расположения стрелочных переводов на сортировочной горке срок их службы увеличился в 1.5 — 2.5 раза за счет повышения твердости наплавленного металла на 60 — 80 единиц НУ благодаря наклепу. Восстановление наплавкой одного остряка (с учетом всех расходов) не превышает 7 — 10 % стоимости нового. При одновременном ремонте остряка и рамного рельса экономический эффект от наплавки удваивается.
Выводы
- Решение проблемы обеспечения необходимого уровня работоспособности и сроков службы стрелочных переводов, повышения эффективности выполнения или требуемых функций при современных и перспективных условиях эксплуатации вызывает потребность изыскания соответствующих критериев оценки работы указанных конструкций. Выявлено, что наиболее полную и объективную оценку работы стрелочных переводов можно выполнить с помощью критериев надежности, отличающихся необходимой полнотой и конкретностью.
- В работе сформулированы показатели надежности стрелочных переводов и их элементов, разработана математическая модель их функционирования в различных условиях эксплуатации. Установлено, что качество функционирования стрелочных переводов в наибольшей мере зависит от последствий отказов с позиции обеспечения безопасности движения и, в первую очередь, — внезапных, так как постепенные могут быть устранены в плановом порядке. Наибольшего внимания требуют такие события, как появление трещин и изломов несущих и направляющих элементов переводов, деталей скреплений, рабочих и контрольных тяг. Вместе с тем постепенные отказы в виде выхода параметров рельсовой колеи за допустимые пределы, ослабления креплений деталей часто нарушают нормальную работу переводов и снижают уровень безопасности движения поездов. /
- Изменившиеся условия эксплуатации стрелочных переводов вызывают интенсивный износ их элементов. Для оценки интенсивности износа остряков, рамных рельсов, крестовин и рельсов переводной кривой были проведены измерения их износа на стрелочных переводах типа Р65 марки 1/11 и 1/9. По результатам наблюдений построены эмпирические зависимости вертикального и бокового износа элементов стрелочных переводов в функции пропущенного тоннажа и осевых нагрузок подвижного состава. Эти зависимости позволяют прогнозировать срок службы элементов стрелочных переводов по износу.
Одной из основных причин увеличившейся интенсивности износа элементов стрелочных переводов является отсутствие смазки, которая ранее осуществлялась из букс с подшипниками скольжения.
- На основании анализа полученных результатов наблюдений установлено, что 74 % крестовин и 53 % остряков отказывают по причине достижения предельного износа, 17 % крестовин отказывают из-за выкрашиваний сердечника и усовиков в зоне перекатывания колес.
Рекомендуемые нормативные сроки службы элементов стрелок и крестовин установлены на основе оценки их надежности для прямых участков пути и приведены в таблице 2.6 для участков со скоростями движения поездов 80 км/ч по прямому направлению, со средней статической осевой нагрузкой подвижного состава 150 кН при соотношении грузопотоков по прямому и боковому направлениям стрелочных переводов 75 и 25 %.
- На сети дорог интенсивно укладывают стрелочные переводы типа Р65 марки 1/11, проекта 2750, на железобетонном подрельсовом основании, на Западно-Сибирской дороге начиная с 1998 г. эксплуатируется свыше 250 таких переводов.
Более жесткое подрельсовое основание с железобетонными брусьями в сочетании с суровыми климатическими условиями снижает стойкость сборных крестовин. Причины отказа — вертикальный износ и выкрашивание поверхности катания сердечника и усовиков. Глубина выкрашивания достигает 5 мм, наибольший износ составляет 8 мм и более.
Средний срок службы таких крестовин составляет 53 млн. т брутто наработанного тоннажа, в то время как стрелочные крестовины на деревянных брусьях пропускают до изъятия 100 млн. т груза и более.
Для снижения жесткости подрельсового основания предусмотрены ди- намико-прочностные испытания резиновых прокладок повышенной упругости. В переводах проекта 2750 намечено использовать крестовины с непрерывной поверхностью катания, существенно снижающие динамическое воздействие на путь. ‘
- Учитывая особенности движения поездов в пределах крупных узлов и специализированных парков (ограниченные скорости движения, интенсивное движение по боковому направлению переводов), необходимо усовершенствовать конструкцию стрелочных переводов применительно к этим условиям. При движении поездов преимущественно по боковому направлению быстро прогрессирует боковой износ элементов на упорной нити. Поэтому важно усилить, укрыть и защитить криволинейные остряки, усилить передние вылеты рамных рельсов, а также повысить стабильность колеи за счет применения более надежных промежуточных скреплений.
7. Основными направлениями повышения эксплуатационной надежности стрелочных переводов следует считать расширение производства стрелок с гибкими удлиненными остряками, применение в конструкции стрелок упругих скреплений, башмаков и подкладок с приварными подушками и высокими ребордами, контррельсов-протекторов, внешних замыкателей.
Существенным (в 3 — 4 раза) продлением срока службы крестовин является переход на конструкцию с непрерывной поверхностью катания.
Для продления срока службы жестких крестовин необходимо применять методы их наплавки и науглероживания. Рекомендации по совершенствованию технологии этих работ приведены во втором разделе диссертации.
В работе сделана оценка эффективности применения наплавки и науглероживания крестовин. Методом науглероживания по возможности целесообразно упрочнять до 50 — 60 % крестовин — в первой половине их срока службы. Затем, когда необходимо восстановить профиль крестовин, лучше применять наплавку. Во всех случаях оба метода надо использовать своевременно. Нельзя запускать крестовины, доводя их состояние до предельной изношенности.
Используемая Литература
- Рыбкин В.В., Васильев А.С. Надежность работы крестовин стрелочных переводов при повышенной осевой нагрузке // К 150-летию железных дорог СССР. — Иркутск: ИрИИТ, 1987. — С. 11-13.
- Шарапов C.H., Тейтель A.M., Глюзберг Б.Э. Перспективы развития стрелочного хозяйства // Путь и путевое хозяйство. — 1998, № 9. — С. 17-20.
- Радыгин Ю.Н. Крестовины, упрочненные методом науглероживания // Путь и путевое хозяйство. — 1994, № 2. — С. 6-11.
- Шульга В.Я. Что выгоднее: наплавка или науглероживание крестовин? // Путь и путевое хозяйство. — 1998, № 12. — С. 16-17.
- Восстановление и использование старогодных остряков стрелочных переводов типов Р65 и Р50 марок 1/9 и 1/11. Технологическая инструкция // Путь и путевое хозяйство. — 1999, № 1. — С. 28-30.
- Титаренко М.И., Сорочихин Н.С., Червяков В.Ю., Вишняков А.Г., Хвостик М.Ю. Стрелочные переводы проекта 2750. Анализ работы и предложения по совершенствованию // Путь и путевое хозяйство. — 2002, №8. -С. 9-10.