Сейчас ваша корзина пуста!
ОЦЕНКА НАДЕЖНОСТИ РЕЛЬСОВЫХ ЦЕПЕЙ
Цикл статей:
Глава 1 — ОСНОВНЫЕ ПОЛОЖЕНИЯ СИСТЕМЫ ВЕДЕНИЯ ПУТЕВОГО ХОЗЯЙСТВА НА СТАНЦИЯХ
Глава 2 — ОЦЕНКА И ПРОГНОЗИРОВАНИЕ НАДЕЖНОСТИ СТРЕЛОЧНЫХ ПЕРЕВОДОВ
Глава 3 — ТЕКУЩЕЕ СОДЕРЖАНИЕ И РЕМОНТЫ СТРЕЛОЧНЫХ ПЕРЕВОДОВ
Глава 4 — ОЦЕНКА НАДЕЖНОСТИ РЕЛЬСОВЫХ ЦЕПЕЙ
Аппаратура рельсовых цепей
Электрическую цепь, состоящую из рельсов железнодорожного пути, по которым протекает ток от источника к потребителю, называют рельсовой цепью. Чтобы проложить рельсовую цепь, путь делят на отдельные участки, и на их границах устраивают изолирующие стыки. Путь в пределах рельсовой цепи называют изолированным участком. К началу рельсовой цепи подключают источник электрического тока (путевой трансформатор), к концу — приемник электрического тока (путевое реле) / 65 /.
В рельсовой цепи (рисунок 4.1) могут быть выделены три составные части: питающий конец, на котором находится вся аппаратура и питающая рельсовая цепь; участок пути (рельсовая линия), ограниченный по концам изолирующими стыками и используемый для передачи электрического тока от источника к приемнику, объект контроля рельсовой цепи; релейный конец, где расположены путевое реле и другая аппаратура, необходимая для его работы.
В связи с использованием на дорогах постоянного тока в рельсовых цепях применяют переменный ток. Питающий конец рельсовой цепи включает: путевой трансформатор (ПТ), конденсаторный блок (КБ) и дроссель- трансформатор (ДТ). От путевого трансформатора рельсовая цепь питается переменным током промышленной частоты. Его первичная обмотка через предохранители подключена к сети напряжением 220 В. Со вторичной обмотки в цепь подастся напряжение, значение которого определяется длиной рельсовой цепи.
Конденсаторный блок выполняет роль ограничителя тока во вторичной обмотке трансформатора при шунтировании рельсовой цепи поездом, а также с помощью него компенсируется индуктивная составляющая входного сопротивления рельсовой цепи, что позволяет снизить до минимума потребляемую мощность. Емкость КБ зависит от длины рельсовой цепи, может находиться в пределах 8-16 мкф. Конденсаторный блок позволяет получить требуемое фазовое соотношение между напряжениями на обмотках путевого реле и улучшить шунтовую чувствительность. Рельсовые цепи с емкостными ограничителями называют резонансными. Дроссель-трансформатор типа ДТ-0.6-500 имеет коэффициент трансформации п = 40. Дополнительная обмотка подключена в контур с путевым трансформатором. Крайние выводы основной обмотки с помощью дроссельных соединителей (джемперов) подключены к рельсам.
Дроссель-трансформатор на питающем конце (ДТп) рельсовой цепи выполняет роль понижающего трансформатора.
На релейном конце рельсовой цепи включены: путевое реле (П), конденсаторный блок (КБ) и дроссель-трансформатор (ДТр). Дроссель- трансформатор такого же типа, что и на питающем конце, но здесь он выполняет роль повышающего трансформатора. Используют путевое реле типа ДСШ-12 на 50 Гц или ДСШ-13А на 25 Гц. Путевой элемент подключают к рельсовой цепи, местный элемент питается от сети напряжением 220 В. Для работы этих реле необходимо, чтобы угол сдвига фаз между напряжениями путевой и местной обмоток составлял 90°. Требуемое фазовое соотношение на реле достигают подбором емкости конденсатора на питающем и релейном концах.
Напряжение со вторичной обмотки трансформатора подается на дополнительную обмотку дроссель-трансформатора. Конденсаторный блок, последовательно включенный в цепь, компенсирует индуктивную составляющую рельсовой цепи и устанавливает резонанс напряжений в контуре питающего конца. На основной обмотке ДТ индуцируется напряжение, которое в п раз меньше, чем на дополнительной обмотке (в соответствии с коэффициентом трансформации дроссель-трансформатора). В контуре, состоящем из основных обмоток дроссель-трансформатора питающего и релейного концов, а также из рельсовых нитей, протекает ток. На дополнительной обмотке ДТр индуцируется напряжение, равное 30 — 40 В. Сектор путевого реле занимает верхнее положение и замыкает фронтовые контакты. Параллельно ему включен КБ емкостью 8 — 16 мкф, которым компенсируется индуктивная составляющая сопротивления релейного конца и улучшается фазовое соотношение на реле.
Замыкание фронтовых контактов путевого реле является признаком незанятости участка в пределах рельсовой цепи, что контролируется на табло. Режим работы рельсовой цепи при свободном участке называют нормальным.
При въезде поезда на изолированный участок происходит следующее. Рельсовая цепь шунтируется, так как параллельно аппаратуре релейного конца подключается шунт — колесная пара с очень малым сопротивлением. Ток в рельсовой цепи проходит в основном через колесные пары, лишь незначительно ответвляясь через аппаратуру релейного конца. В путевом реле значение тока резко падает. Кроме того, вследствие нарушенная условий резонанса на питающем конце, ухудшаются фазовые соотношения между током в путевой и напряжением в местной обмотках путевого реле. В результате вращающий момент реле уменьшается, и сектор под собственным весом опускается в нижнее положение, размыкая фронтовые контакты и замыкая тыловые. Такой режим работы рельсовой цепи называется шунтовым.
Размыкание фронтовых контактов путевого реле является признаком наличия на рельсовой цепи препятствий для движения. Рельсовая цепь также контролирует целость рельсовой линии — выявляет излом или изъятие рельсов. Режим работы рельсовой цепи при поврежденной рельсовой линии называют контрольным.
Техническое обслуживание рельсовых цепей
Изоляцию стыков проверяют вольтметром с внутренним сопротивлением (50±0.5) Ом, соизмеримым с принятым условно минимальным сопротивлением изоляции стыка 50 Ом. Сначала измеряют напряжение на рельсах Ур (рисунок 4.2), а затем измеряют напряжение VI и У2 между рельсом и накладками противоположного стыка. Если значение VI (У2) меньше половины Ур, то изолирующий стык исправен, если больше, — стык неисправен.
Такие же измерения выполняют с другой стороны стыка на смежной рельсовой цепи.В рельсовых цепях с дроссель-трансформаторами измерения проводят сначала на изолирующем стыке (Ур) (рисунок 4.3), а затем между рельсами и накладками (V] и У2). Исправность изолирующего стыка определяется так же, как в первом случае.Для проверки изоляции стрелочных сережек и фундаментальных угольников стрелочных гарнитур сначала измеряют напряжение Ур между рельсами (рисунок 4.4), а затем между связной тягой и обоими рельсами (V] и У2). Если значение VI (У2) больше Ур, то неисправна изоляция со стороны противоположного рельса. В случае если V] (У2) меньше половины Ур, — изоляция исправна.
Для определения места пробоя изоляции в сережках и угольниках сторону с исправной изоляцией замыкают накоротко (путевое реле обесточивается) и, пользуясь индикатором рельсовой цепи, находят неисправную изоляцию.
В практике существует простейший способ проверки изолирующих стыков и элементов стрелочного перевода, позволяющий быстро определить неисправную изоляцию (рисунок 4.5). Приспособление состоит из круглого напильника и стальной полосы, на которой смонтированы переключатель, лампа и питающий элемент (последние рассчитаны на напряжение 12 В). Они соединены последовательно, и при соприкосновении напильника и стальной полосы лампа загорается. Если напильником плотно коснуться накладки изостыка, а стальную полосу прижать к рельсу, то при неисправности изоляции лампа горит в полнакала. При полном пробое изоляции лампа горит ярко. Так же быстро можно проверить изоляцию фундаментальных гарнитур и сережек стрелочного перевода в обеих его сторонах.
Стрелочные электроприводы
Посредством стрелочных электроприводов переводятся и запираются централизованные стрелки, контролируется их положение.
Согласно ПТЭ, стрелочные электроприводы всех видов должны:
- обеспечивать при крайних положениях стрелки плотное прилегание прижатого остряка к рамному рельсу;
- не допускать запирание стрелки при зазоре между прижатым остряком и рамным рельсом 4 мм и более;
- отводить другой остряк от рамного рельса на расстояние не менее 125мм.
Перечисленные положения являются исходными для определения технических требований к стрелочным приводам.
Плотное прилегание прижатого остряка в крайних положениях стрелки при се исправном состоянии и нормальной ширине колеи зависит, прежде всего, от точности обеспечения приводом рабочего хода стрелки, гарантирующего зазор между остряком и рамным рельсом менее 4 мм. Такой зазор исключает набегание гребня колеса на остряк и удар в его острие при противошерстном движении поезда.
При следовании составов по стрелке на остряки воздействуют вертикальные и горизонтальные силы, возникает тряска, вибрация и т.д. В этих условиях может происходить отжатие остряка от рамного рельса и, как следствие, попадание гребней колес в пространство между остряком и рамным рельсом, что ведет к аварии. Поэтому надежное запирание остряков, и в особенности прижатого, является важным требованием к стрелочным приводам.
Условно различают три положения стрелки: плюсовое крайнее, среднее и минусовое крайнее. Крайним называют такое положение стрелки, при котором прижатый остряк заперт и прилегает к рамному рельсу с зазором менее 4 мм, а отжатый остряк отстоит от своего рамного рельса на расстоянии не менее 125 мм. Следует отметить, что в зависимости от конструкции привода отжатый остряк в крайнем положении может запираться или не запираться. Средним называют положение стрелки, при котором прижатый остряк отстоит от рамного на 4 мм и более.
Важнейшим условием дистанционного управления стрелками является возможность проверки их положения на посту управления. В связи с этим стрелочные приводы должны иметь датчик контроля (автопереключатель), позволяющий определить положение стрелки и преобразующий информацию об этом в электрический сигнал для передачи ее в орган управления. Датчик должен выдавать соответствующие сведения как при перемещении остряков электроприводом, так и гребнями колес состава, т.е. при взрезе стрелки.
При эксплуатации стрелок возможно попадание посторонних предметов между остряком и рамным рельсом, препятствующих нормальной работе перевода. Если при этом автоматическое реверсирование не предусмотрено, то привод оснащают защитой от перегрузок. Стрелочные приводы, кроме силового, допускают возможность перевода стрелки вручную. При этом а также при вскрытии привода должно автоматически отключаться питание во избежание несчастных случаев.
Крепление привода на стрелках должно быть надежным, предупреждающим их смещения в процессе работы.
Структурная схема устройств управления стрелкой приведена на рисунке 4.6. Жирными линиями на схеме обозначены электрические связи, тонкими — механические.
Наиболее распространенный стрелочный электропривод типа СП-6 имеет следующие показатели: электропитание постоянным током при номинальных напряжениях 30, 110 и 160 В и переменным током частотой 50 Гц и напряжением 110, 127, 190 и 220 В; тяговые усилия — номинальное 3500 Н и максимальное 6000 Н; максимальное время перевода — до 7 с, ход шибера — 154±2 мм.
Электропривод типа СП-6 имеет три основных блока — электродвигатель, редуктор с фрикционом и автопереключатель, помещенные в чугунный корпус. На боковых стенках корпуса расположены блокировочное устройство, замок привода, направляющая плита, кожух, прикрывающий шибер и контрольные линейки, панель для освещения привода. Обогреватели, предотвращающие обледенение контактов автопереключателя, расположены над контрольными контактами.
Запирающий механизм электропривода обеспечивает запирание стрелки за счет зацепления зубьев кулачков специальной формы, расположенных на шибере и шиберной шестерне (рисунок 4.7).
Рисунок 4.6 — Структурная схема управления стрелкой: ИП — источник питания, БУ — блок управления стрелкой, АП — автопереключатель, ЭД — электродвигатель, Р — редуктор, ЗМ — запирающий механизм, С — стрелка
Рисунок 4.7 — Запирающий механизм электропривода
Основным параметром запирающего механизма является угол запирания. При его определении должно быть выполнено необходимое и достаточное условие. Необходимое условие заключается в том, что угол запирания а должен превышать угол заклинивания при выполнении неравенства.
Стрелочные гарнитуры
Для обеспечения максимальной безопасности обслуживающего персонала конструкция стрелочных гарнитур предусматривает установку приводов вне рельсовой колеи. Стрелочный привод монтируется на двух фундаментальных угольниках, подвешенных и закрепленных непосредственно на рамных рельсах, что уменьшает влияние угонов и прогибов элементов стрелки.
Рельсовые цепи требуют детальной электрической изоляции рельсовых нитей друг от друга, для чего стрелочные гарнитуры и установленные на них приводы полностью изолируют от рамных рельсов и остряков.
На рисунке 4.8 представлена в качестве примера гарнитура с электроприводом типа СП-6. Фундаментальные угольники правый 4 и левый 12 изготавливают из уголковой стали. Угловая форма сечения выбрана, чтобы исключить изгиб и уменьшить вибрацию под тяжестью привода, консольно расположенного на угольниках. Для той же цели к вертикальным сторонам фундаментальных угольников прикреплены дополнительные угольники 11. Фундаментальные угольники подвешиваются к рамным рельсам в соседних шпальных ящиках с помощью четырех угольников 7. Такое крепление создаст дополнительное усилие на рамные рельсы, которое компенсируется установкой поперечной связной полосы 8, прикрепленной шурупами к шпалам и болтами к каждому угольнику. Связная полоса 8 способствует уменьшению вибрации привода при проходе подвижного состава по стрелке. Каркас гарнитуры, таким образом, состоит из двух фундаментальных угольников 4 и 12 и продольной связной полосы 8. Жесткость каркаса обеспечивается так же корпусом самого привода, закрепленного четырьмя болтами 10 на угольниках.
Ближний и дальний остряки стрелки соединены между собой связной тягой 5, конфигурация которой хорошо видна на профильной проекции стрелки (разрез А — А). Тяга имеет проушины: на одном конце — двойную в виде вилки, на другом — одинарную (лопатку). Тяга проходит под рамным рельсом и остряком в шпальном ящике и прикрепляется концом в виде вилки к ушку рабочей тяги 6, а лопаткой — к шарниру Гука. Такое соединение рабочей тяги с шибером исключает влияние перекосов, возникающих при установке привода, на работу стрелки. Короткая 9 и длинная 3 контрольные тяги связывают левую и правую контрольные линейки привода с остряками стрелки. По обеим сторонам тяги имеются проушины для крепления с помощью пальцев непосредственно к линейкам и серьгам 2 остряков. Соединение связной тяги с остряками осуществляется с помощью двух серег 1.
На рисунке 4.9, а показана электроизоляция связной полосы, на рисунке 4.9, б — стрелочной тяги, соединяющей остряки.
Конструкции токопроводящих и изолирующих рельсовых стыков
Токопроводящие рельсовые стыки
В рельсовых стыках электрический ток проходит через накладки, поэтому необходимо обеспечить хороший контакт между рельсом и стыковой накладкой или установить в стыке рельсовый соединитель. Рельсовые соединители по способу прикрепления к рельсам делятся на штепсельные и приварные / 82 /.
Штепсельные соединители, изображенные на рисунке 4.10, а, применяют на неэлектрифицированных участках, оборудованных устройствами автоматики и телемеханики. Штепсельный соединитель ставится снаружи рельсовой колеи. Он состоит из двух стальных проволок диаметром 5 мм.
Для установки штепсельного соединителя в шейке рельсов на расстоянии около 80 мм от торцов накладок сверлят отверстия. Электрическое сопротивление таких соединителей около 0.0042 Ом.
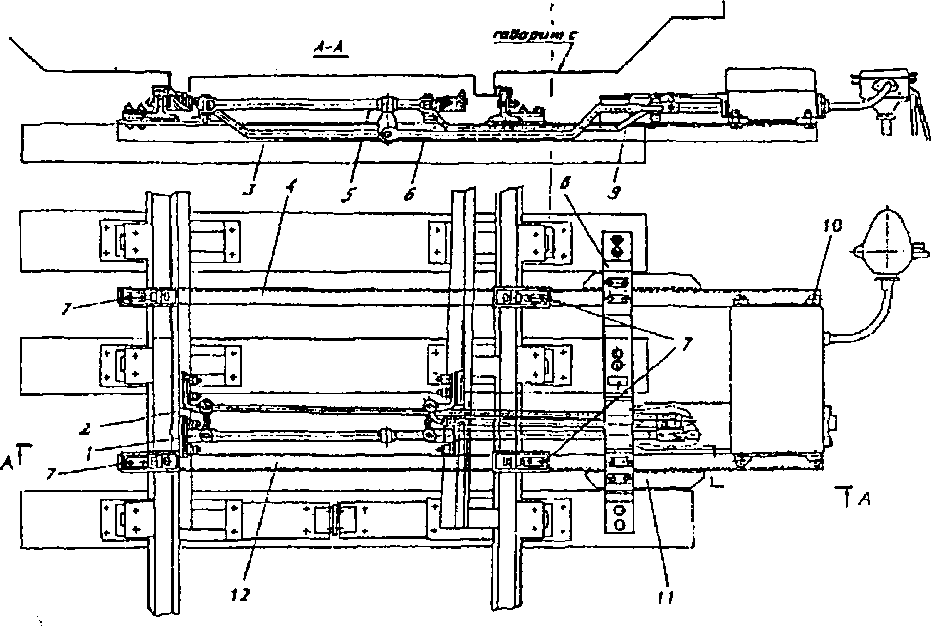
Рисунок 4.8 — Стрелочные гарнитуры
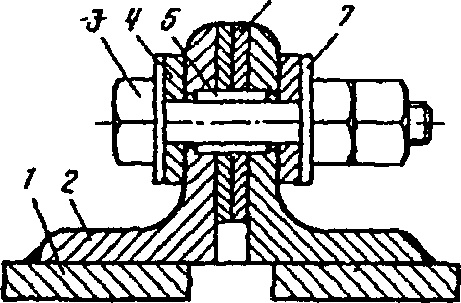
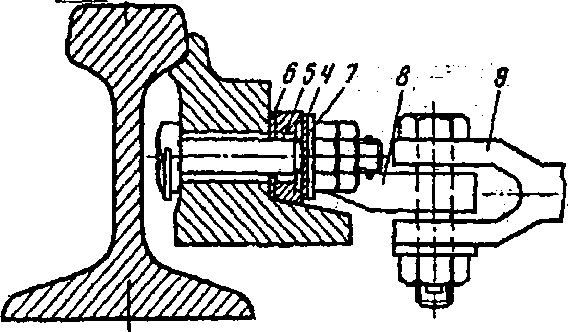
Рисунок 4.9 — Детали электрической изоляции на стрелочных переводах: 1 — связная полоса; 2 — уголок; 3 — соединительный болт; 4 — изолирующая шайба; 5 — изолирующая втулка; 6 — изолирующая прокладка; 7 — металлическая шайба; 8 — серьга; 9 — стрелочная тяга.
На электрифицированных железнодорожных путях по рельсам проходит ток большой силы, поэтому на них применяют только приварные соединители из медного троса сечением не менее 50 мм при электрической тяге на переменном токе и не менее 70 мм при электрической тяге на постоянном токе с поверхностью контакта в месте приварки не менее 250 мм2 (рисунок 4.10, б, в).
Междупутные и междурельсовые соединители (рисунок 4.10, г) обеспечивают параллельное соединение рельсовых нитей на участках с электрической тягой для уменьшения общего омического сопротивления цепи. Их сечение такое же, как и стыковых соединителей.
На участках бесстыкового пути с рельсовыми цепями длиной 200 м и более применяют пружинные рельсовые соединители (рисунок 4.11).
На не электрифицированных участках с автономной тягой также устанавливают пружинные соединители.
Приварка соединителей осуществляется согласно техническим указаниям на электродуговую приварку рельсовых стыковых соединителей. Приварка основных соединителей производится к головке рельса так, как показано на рисунке 4.12 выгнутой частью вниз и с расположением манжетов таким образом, чтобы после приварки их не могли касаться бандажи колес подвижного состава, и они не препятствовали бы снятию накладок.
Концы гибкого троса приварного соединителя должны быть оплавлены и приварены к манжете для обеспечения более тесного и надежного контактирования между собой тросовых проволок и манжеты.
Рельсовые цепи оборудуются дублирующими соединителями: на перегонах — на участках приближения к переездам и станциям, приближения и удаления от станций, на главных путях станций, а также по маршрутам безостановочного пропуска и приема (отправления) пассажирских поездов — согласно технико-распорядительному акту (ТРА) станции.
Обязательна установка основных и дублирующих стыковых соединителей (приварных или штепсельных) на ответвлениях, которые не обтекаются током рельсовых цепей, а также в стыках тяговой нити однониточных рельсовых цепей / 82 /.
В качестве дублирующих применяются приварные рельсовые соединители того же типа, что и основные, приварка которых производится к подошве рельса (рисунок 4.13). Кроме того, на электрифицированных участках могут устанавливаться электротяговые соединители длиной 1200 мм с болтовыми креплениями (медные или равноценные по электрическому сопротивлению из другого материала), а также пружинные соединители.
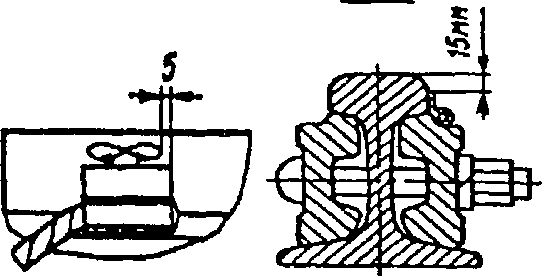
Г)
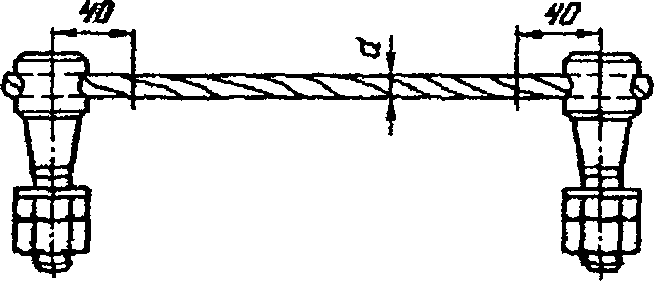
Рисунок 4.3 — Рельсовые соединители: 1 — штепсель; 2 — оцинкованная проволока диаметром 5 мм; 3 — стальной трос; 4 — манжета; 5 — медный трос
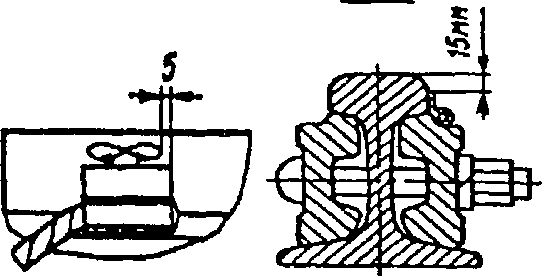
Рисунок 4.11 — Пружинный рельсовый соединитель
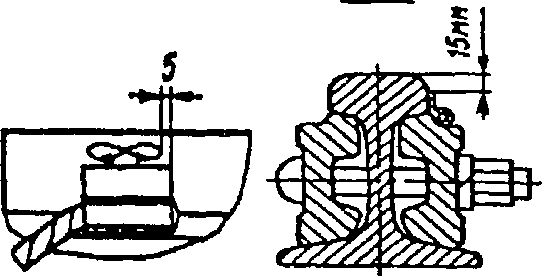
Рисунок 4.12 — Схема установки (а) и приварки (б) медного соединителя фартучного типа к головке рельса: 1 — шов, выполняемый ручной электродуговой сваркой; 2 — фартук; 3 — наконечник (манжета); 4 — гибкий трос МГГ-70
На участках с электротягой переменного тока в качестве дублирующих допускается также применение стальных приварных или штепсельных соединителей (рисунок 4.14).
При производстве работ по установке соединителей, сварке и наплавке рельсов или крестовин электродуговым методом должны соблюдаться правила, исключающие повреждение устройств сигнализации, централизации и блокировки (СЦБ) током сварочного агрегата.
Рельсовые стыки, имеющие дополнительные приспособления для уменьшения электрического сопротивления, оборудуются стыковыми соединителями согласно утвержденным техническим условиям / 82 /.
Пути отстоя вагонов с электроотоплением, участки пути и все рельсовые цепи, по которым проходит ток электроотопления, должен иметь дублирующие соединители и не менее двух отводов в соответствии с утвержденными нормами.
Для разделения рельсовых цепей на электрически изолированные друг от друга участки применяются изолирующие стыки следующих конструкций:
- сборные с объемлющими металлическими накладками (рисунок 4.15);
- сборные с двухголовыми металлическими накладками (рисунок 4.16);
- клееболтовые с двухголовыми металлическими накладками (рисунок 4.17, а);
- клееболтовые с полнопрофильными металлическими накладками (рисунок 4.17, б);
- клееболтовые с металлокомпозитными накладками (рисунок 4.18, а);
- сборные с композитными накладками (рисунок 4.18, б).
Клееболтовые изолирующие стыки маркируют следующим образом: на
расстоянии 0.5 м от торца накладки на шейке рельса с каждой стороны несмываемой белой краской указывается дата склеивания и условное обозначение предприятия-изготовителя.
Изолирующие стыки должны располагаться над серединой шпального ящика. При деревянных шпалах с костыльным скреплением рельсы, стыкующиеся в изолирующем стыке, закрепляются по каждой рельсовой нити противоугонами в «замок» на 13-ти шпалах с обеих сторон стыка.
Торцы рельсов в изолирующем стыке не должны иметь наката. Зазор в стыке по всей высоте рельса должен составлять 5—10 мм. Все изолирующие детали стыка должны быть типовых форм и размеров, соответствующих типу рельсов.Места выхода изолирующих прокладок из-под металлических частей должны быть очищены от грязи, мазута, металлической пыли и других загрязнителей.
Рисунок 4.13 — Схема установки (а) и приварки (б) соединителя к подошве объемно-закаленных рельсов типа Р65 (Р75)
Рисунок 4.14 — Рельсовый стык со штепсельным соединителем: 1 штепсельный соединитель
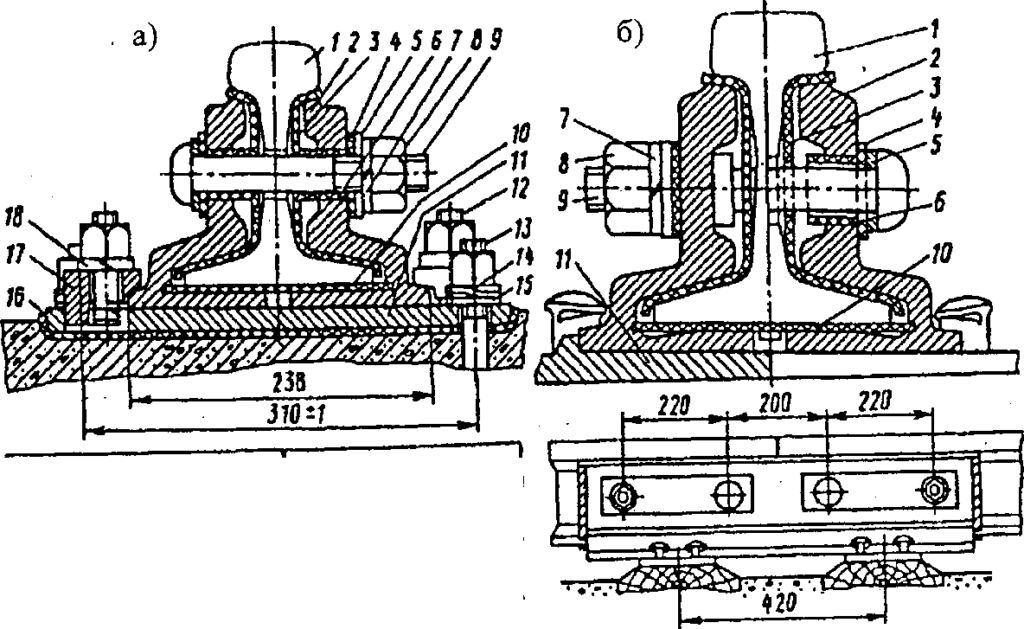
Рисунок 4.16 — Изолирующий стык с двухголовыми металлическими накладками для пути с деревянными шпалами: боковая прокладка; 1 — боковая прокладка; 2 — накладка; 3 — втулка; 4 — изолирующая планка под болт; 5 — стопорная планка; 6 — торцовая прокладка
а)
б)
Рисунок 4.18 — Изолирующий стык: а — клееболтовой с металлокомпозитными накладками; б — сборный с композитными накладками из стеклопластика; 1 — изолирующий слой; 2 — стыковой болт, 3 — металлокомпозитная накладка; 4 — изолирующая втулка; 5 — гайка; 6 — боковая изоляция; 7 — композитная накладка из стеклопластика; 8 — стопорная планка; 9 — тарельчатая пружина (пружинная шайба)
Анализ отказов рельсовых цепей
Опыт эксплуатации железнодорожного пути показывает, что одной из основных причин отказов элементов верхнего строения и устройств автоматики, является нарушение работы рельсовой цепи /91 /.
Наиболее характерными причинами отказов рельсовой цепи являются: обрыв стыковых соединителей, перемычек, тяговых и блокировочных соединительных проводов, нарушение изоляции изолирующего стыка, стрелочной гарнитуры, понижение сопротивления балласта, влияние посторонних источников тока, излом рельса и т.д.
Особенно опасна ситуация, когда рельсовая цепь показывает ложную свободность путевого участка. Наиболее вероятны случаи ложной свободности в результате следующих причин: появление обходных цепей для сигнального тока через опоры контактной сети, металлические конструкции, междупутные соединения и т. д.; потеря шунта вследствие загрязнения поверхности головок рельсов; следование подвижных единиц с плохим шунтом; подпитка или переворачивание путевых реле обслуживающим персоналом; неисправности перемычек или соединителей.
Неисправности соединителей происходят из-за коррозии, некачественной приварки, из-за повреждений при путевых работах / 91 /. Отказы стыковых соединителей приварного типа происходят в основном из-за обрыва соединителя в месте его приварки к рельсу вследствие нарушения технологии приварки или ненадежного контакта между тросом и наконечником. Основным недостатком штепсельных соединителей является нестабильное сопротивление в контактной паре штепсель-рельс. Это сопротивление зависит от состояния контактирующих поверхностей и плотности контакта.
Опыт эксплуатации железнодорожного пути показывает, что основное число отказов рельсовых цепей падает на изолирующие стыки в стрелочном переводе. Нарушение изоляции в изолирующем стыке происходит как из-за дефектности торцовой изоляции при угоне пути, смятия боковой фибры, продавливания втулок и шайб. Факторами, способствующими нарушению изоляции изолирующего стыка, являются угон рельсов, некачественная подбивка шпал, замыкание стыка металлической стружкой.
Понижение изоляция рельсовой цепи происходит из-за повышенного загрязнения и увлажнения балластной призмы, гниения деревянных шпал.
Основные элементы железнодорожного пути сделаны из металла (рельсы, скрепления), которые являются хорошими проводниками тока. Шпалы и балласт при наличии влаги работают как электролит, обладающий определенной проводимостью. С ростом температуры и влажности балласта интенсивность электрохимических процессов возрастает, что приводит к снижению сопротивления изоляции. На активизацию процесса большое влияние оказывает наличие в грунте и балластной призме солей, которые даже в малых количествах приводят к снижению сопротивления изоляции.
На уровень утечки тока в рельсовой цепи оказывают влияние типы и материалы шпал, а также конструкция промежуточных скреплений.
На железнодорожном пути с деревянными шпалами и скреплениями ДО рельсовая цепь имеет изоляцию в виде деревянных шпал. При длительной эксплуатации костыли начинают надергиваться, а металлические подкладки втапливаются в шпалы от поездной нагрузки, в результате чего шпалы при увлажнении проводят электрический ток.
На железнодорожном пути с железобетонными шпалами и скреплениями типа КБ утечка тока происходит за счет нарушения электроизоляционных элементов скрепления, неисправной арматуры шпалы.
Сопротивление цепи «рельс-металлическая подрельсовая подкладка — шпала» на новых сухих деревянных шпалах Я = 100 кОм, а на старых и увлажненных Я = 500 Ом. Как видно из этих данных сопротивление изоляции рельсов снижается от увлажнения шпалы и деталей скрепления.
При эксплуатации железобетонных шпал со скреплениями КБ снижение изоляции происходит при касании стопорной шайбы закладного болта с зажимом клеммного болта, стирании резиновой прокладки, выкрашивании изолирующей втулки закладного болта, заполнения пространства между болтами балластной пылью, грязью, мазутом.
При применении на железобетонных шпалах скреплений типа ЖБР сопротивления цепей утечки тока сильно уменьшаются от увлажнений и разрушений изолирующих элементов скрепления.
В условиях эксплуатации важно поддерживать в хорошем состоянии шпалы и балласт.
Положительные качества балласта для рельсовых цепей определяются в основном дренирующейся способностью. К сожалению эти качества проявляются только в начальный период эксплуатации, так как при загрязнении балласта дренирующая способность снижается. Величина и характер изменения сопротивления балласта от влажности в сильной мере определяются видом балластных материалов, их составом, чистотой и расстоянием между поверхностью балласта и подошвой рельса.
Кратковременное замыкание рельсовой цепи посторонними предметами обычно связано с производственной деятельностью монтеров пути и наблюдается чаще всего при выполнении следующих путевых работ: замена рельсов; разгонка и регулировка зазоров; замена стрелочного перевода; проезд дефектоскопной и путеизмерительной тележек, модеронов с неисправной изоляцией; при работе электроизмерительными путевыми инструментами с неисправной изоляцией проводов; замена шпал и перешивка пути.
При коротких замыканиях, носящих постоянный или периодический характер, отыскание точного места замыкания представляет значительные трудности, особенно в разветвленных рельсовых цепях.
В системах электроснабжения рельсы используются в качестве обратного провода для тягового тока.
Одним из условий надежной работы рельсовых цепей является соблюдение требований защиты от посторонних источников питания. Главным источником как мешающих, так и опасных влияний является тяговый ток на электрифицированных участках дорог / 127, 130 /. В отдельных случаях источником влияния могут являться продольные линии электропередачи, осветительные сети и цепи поездного освещения там, где сохранился подвижной состав с неизолированными источниками питания.
Влияние контактной сети постоянного тока на рельсовые цепи может проявляться как в нормальном режиме ее работы, так и в режиме короткого замыкания.
Основной причиной влияния постоянного тягового тока на рельсовые цепи является наличие в нем гармонических составляющих, частота и амплитуда которых зависят от схемы выпрямления и состояния фильтров на тяговой подстанции. Основные гармоники шестифазной схемы выпрямления 300, 600, 900, 1200 Гц, как правило, не оказывают мешающего действия на работу рельсовых цепей. Наиболее опасное влияние на рельсовые цепи частотой 50 Гц может оказать гармоника постоянного тока той же частоты, которая появляется в контактной сети при некоторых повреждениях в схеме выпрямления на тяговой подстанции, например при неполнофазном выпрямлении.
Влияние тягового тока особенно опасно на станциях, оборудованных фазочувствительными рельсовыми цепями. Анализ работы таких рельсовых цепей показал, что при последовательном повреждении дроссельной перемычки и изолирующего стыка, ставится под угрозу безопасность движения поездов / 129 /. А именно при повышении сопротивления дроссельной перемычки и коротком замыкании изолирующего стыка происходит переворот фаз путевого реле.
Эксплуатационная надежность существующих рельсовых цепей
Известно, что эффективность функционирования систем железнодорожной автоматики и телемеханики во многом определяется эксплуатационной надежностью электрических рельсовых цепей. Анализ повреждений устройств СЦБ на сети дорог показывает, что на долю существующих рельсовых цепей приходится примерно 50 % всех отказов, а на отдельных дорогах этот показатель еще выше / 92-94 /.
В таблице 4.1 приведены средние показатели надежности основных элементов систем железнодорожной автоматики и телемеханики, рассчитанные по различным источникам / 69, 79, 88, 91-106 /.
Таблица 4.1 — Средние показатели надежности укрупненных элементов существующих систем железнодорожной автоматики и телемеханики Укрупненные элементы автоматики и телемеханики | Средние показатели надежности | |||
1/год | Кот, % | р | Т, лет | |
Рельсовые цепи | 0.204 | 50 | 0.815 | 4.90 |
Приборы | 0.091 | 23 | 0.913 | 10.98 |
Сигнальные цепи | 0.059 | 15 | 0.942 | 16.95 |
Прочие элементы | 0.047 | 12 | 0.954 | 21.28 |
Итого | 0.401 | 100 | 0.673 | 2.49 |
Из таблицы 4.1 следует, что коэффициент отказов Кот (относительная доля отказов) существующих рельсовых цепей по отношению к другим элементам железнодорожной автоматики и телемеханики составляет в среднем 50 %. Интенсивность отказов одной существующей рельсовой цепи составляет в год 0.204, а среднее время безотказной работы 4.9 года. Отсюда следует, что на каждые пять существующих рельсовых цепей приходится в среднем один отказ в год. Известно / 91, 92 /, что надежность отдельных элементов существующих рельсовых цепей значительно отличается друг от друга.
Исходя из этого, в таблице 4.2 приведены средние показатели надежности основных элементов существующих рельсовых цепей рассчитанные по тем же источникам.
Таблица 4.2 — Среднее показатели надежности укрупненных элементов существующих рельсовых цепейУкрупненные элементы существующих рельсовых цепей | Средние показатели надежности | |||
Л , 1/год | Кот, % | Р | Т, лет | |
Рельсовые линии | 0.098 | 50 | 0.906 | 10.20 |
Изолирующие стыки | 0.075 | 35 | 0.928 | 13.33 |
Коммутирующие приборы | 0.021 | 10 | 0.979 | 47.62 |
Прочие элементы | 0.010 | 5 | 0.990 | 100.00 |
Итого | 0.204 | 100 | 0.815 | 4.90 |
Из таблицы 4.2 следует, что наибольшее количество отказов 50 % приходится на рельсовые линии, что объясняется сложностью условий их работы: распределенностью параметров по длине, зависимостью сопротивления изоляции от погодных условий и степени загрязнения различными сыпучими грузами, а также зависимостью сопротивления рельсов от наличия стыковых соединителей и качества их приварки / 117/.
На долю изолирующих стыков приходится 35 % всех отказов рельсовых цепей, что объясняется постепенным износом изоляции, а также закорачиванием стыков металлической стружкой / 118/.
Отказы приборов составляют в среднем 10 % от общего количества отказов рельсовых цепей. Большинство этих отказов приходится на трансмиттерные реле, рабочие контакты которых, особенно в длинных рельсовых цепях, коммутируют значительные мощности и разрушаются под действием электрической дуги, возникающей в момент коммутации / 118, 119/.
Отказы прочих элементов рельсовых цепей составляют примерно 5 от общего количества отказов, причем наибольшее их количество (до 4 ) приходится на дроссельные перемычки. Остальные отказы падают на трансформаторы, дроссель-трансформаторы, путевые фильтры и конденсаторные блоки.
Опыт эксплуатации / 117, 118 / и статистические данные /110, 111/ за последние 10-15 лет показывают, что существует четко выраженная зависимость между количеством отказов существующих рельсовых цепей от их длины, сопротивления изоляции рельсовых линий, а также напряжений источников питания.
Общее количество отказов в работе рельсовых цепей непрерывно возрастает, что связано с несовершенством конструкции изолирующих стыков и ростом протяженности линий, оборудованных автоблокировкой.
Одной из основных причин отказов рельсовых цепей являются неисправности изолирующих стыков на сети дорог М^™ .
Общее количество изолирующих СТЫКОВ на сети дорог N изменяется практически пропорционально приросту протяженности линий, оборудованных автоблокировкой.
Удельный вес нарушений, связанных с отказом изолирующих стыков ( откЛц ), непрерывно возрастает и составляет в настоящее время свыше половины всех отказов в работе рельсовых цепей по путейским причинам (рисунок 4.19).
Рост удельной величины ( отк/м ) обуславливается рядом факторов: с одной стороны возрастает количество отказов в работе изолирующих СТЫКОВ, приходящееся на ОДИН СТЫК ( °тк/х ), с другой стороны несколько уменьшается количество неисправностей, связанных с рельсовыми соединителями (составляет 20-30 % от всех отказов). Снижение неисправностей рельсовых соединителей связано с расширением полигона бесстыкового пути, а также с повышением надежности соединителей, с применением новых конструкций / 109 /.
Интенсивное увеличение (более чем в 2.5 раза за рассматриваемый с 1977 г. по 1988 г. период) величины ( отк/^ ) объясняется влиянием различных причин, основными среди которых являются: повышение скорости движения поездов; рост нагрузок на ось подвижного состава:
- увеличение средне сетевой грузонапряженности;
- оборудование системой автоблокировки ряда северных участков дорог, на которых действуют значительные отрицательные температуры, снижающие изолирующие и прочностные свойства фибры и полиэтилена;
- нехватка рабочей силы и как следствие, недостатки текущего содержания пути в целом и рельсовых цепей в частности; недостаточное внедрение клееболтовых стыков;
- волевое (не всегда рациональное) распределение по дорогам изолирующих комплектов для стыков сборной конструкции.
В период до 1985 года удельное количество отказов ( отк/^ ) изменилось незначительно, несмотря на присутствие всех вышеперечисленных факторов. Причиной относительной стабильности величины в данный период явилось начавшееся массовое применение в качестве изолирующего материала в сборных стыках полиэтилена, имеющего срок службы в 2 — 2.5 раза больше чем фибра.
Однако применение полиэтилена не могло долго сдерживать тенденцию к росту количества отказов изолирующих стыков, приходящегося на один стык, так как не устраняло многочисленных недостатков конструкции сборных изолирующих стыков с объемлющими накладками. В течение последующих 13-ти лет рассматриваемая величина увеличилась более чем в 3 раза. На основании приведенных данных можно говорить о том, что сборные изолирующие стыки с изоляцией из полиэтилена и фибры, являющиеся достаточно распространенной конструкцией, далеко не в полной мере соответствуют требованиям надежности эксплуатации дорог, а также требованиям к изолирующим стыкам как к конструкции в целом. Данный вывод подтверждается анализом изменения величины характеризующий количество отказов в работе одного изолирующего стыка, возникающее после пропуска 1 Мт брутто (рисунок 4.20).
За 1985-1998 годы это величина возросла более чем в 2.1 раза и имеет тенденцию к дальнейшему росту. Удельный вес отказов в изолирующих стыках продолжает быть высоким и в последние годы достигает 50-60 % от всех отказов в работе рельсовых цепей по путейским причинам. На 1 января 2000 года в целом на сети дорог России в пути находилось более 53 тыс. штук неисправных изолирующих стыков, отсутствовало более 232 тыс. штук рельсовых соединителей / 67 /.
Анализ кривых, представленных на рисунках 4.19 и 4.20 указывает на недостаточную, с точки зрения безопасности движения поездов и технико-экономической эффективности, надежность работы рельсовых цепей и необходимость скорейшего ее повышения, в первую очередь, в части работы изолирующих стыков.
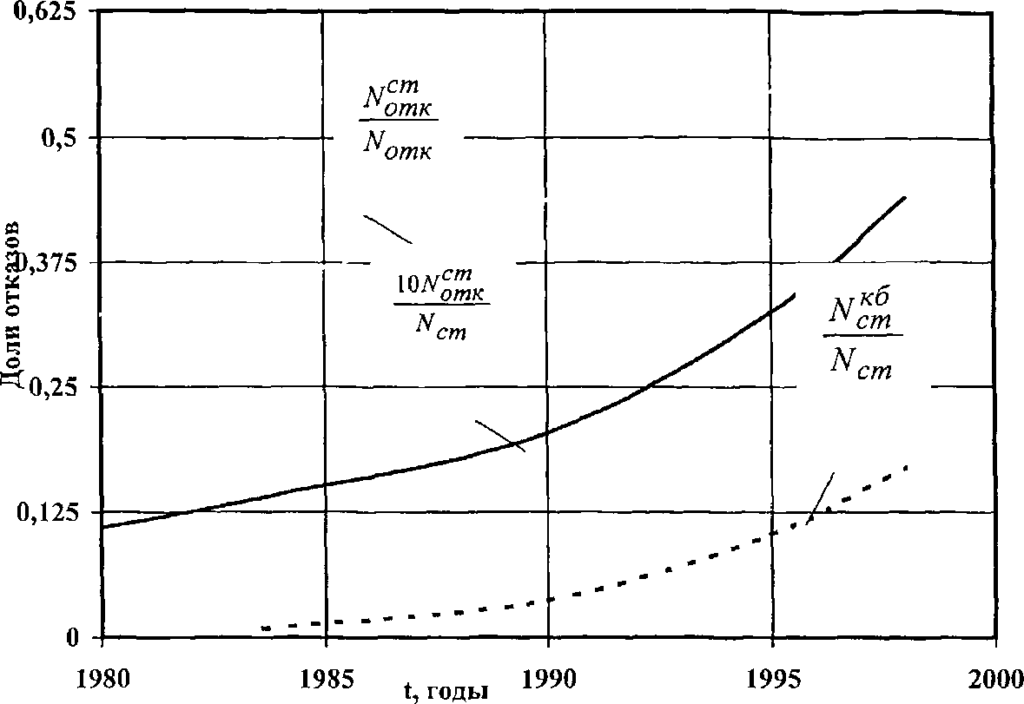
Рисунок 4.19 — Изменение удельных отказов в работе рельсовых цепей
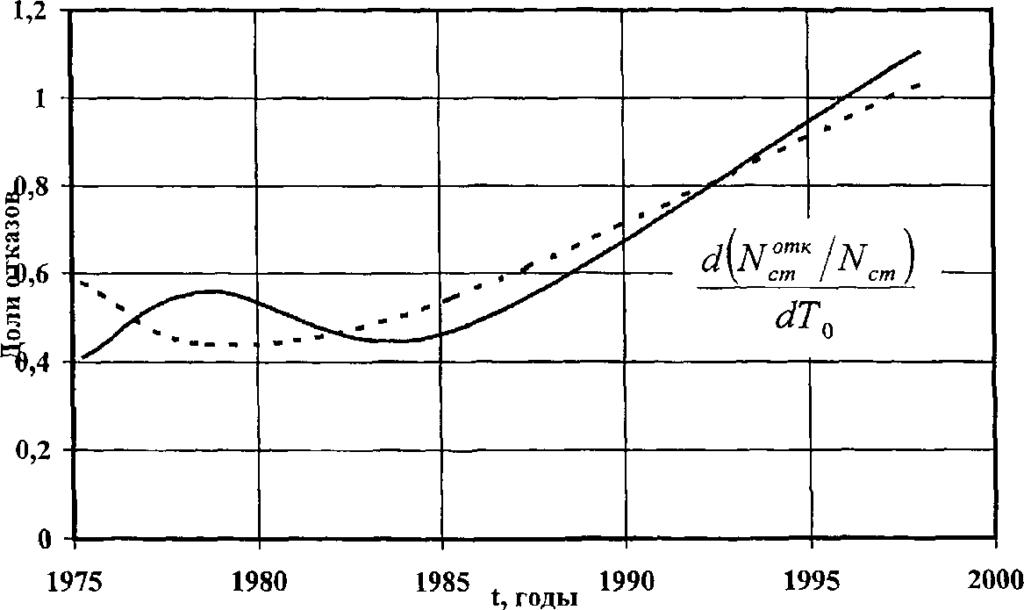
Рисунок 4.20 — Изменение отказов в работе изолирующего стыка после пропуска 1 млн. т. груза
Изолирующие стыки кроме механического соединения рельсов в непрерывную нить, должны в то же время разрывать ее как электрическую цепь. Таким образом, изолирующие стыки являются одним из наиболее напряженно работающих элементов верхнего строения пути / 95 /. По своим прочностным характеристикам он должен приближаться к целому рельсу и вместе с тем обеспечивать надежную электрическую изоляцию стыкуемых концов рельсов.
Быстрое нарушение изоляции стыка, а в результате этого отказ в работе рельсовой цепи нарушает работу устройств железнодорожной автоматики и телемеханики и ставит под угрозу безопасность движения поездов / 96, 97 /. Анализ показывает, что за последние годы доля нарушений в работе рельсовых цепей, вызванных отказами изолирующих стыков практически удвоилась. И связано это, прежде всего, с несовершенством конструкций изолирующих стыков, низким качеством обслуживания ростом протяженности линий оборудованных устройствами сигнализации, централизации и блокировки.
Рассмотрим более подробно характеристики сборных и клееболтовых изолирующих стыков в отдельности.
К группе сборных относятся изолирующие стыки с накладками из электроизолирующих материалов, с металлическими накладками и их изолирующим покрытием, с металлическими накладками объемлющего типа и отдельными деталями изоляции, собираемыми при монтаже стыка.
Для изготовления накладок из электроизолирующих материалов применяли древесину твердых пород, древеснопластик. Однако такие накладки были недолговечны и не отвечали эксплуатационным требованиям. Для устранения этих недостатков были приняты разные решения.
Например, на зарубежных железных дорогах были применены накладки из искусственных изолирующих материалов — мирамида и эпоксидных смол, 6,6 — полиамида, ультрамида А4, сустамида, из эпоксидного ламината с высоким содержанием стекловолокна / 98 /. Применялись также конструкции сборных изолирующих стыков, в которых металлические накладки и болты покрывались предварительно изолирующими материалами. В качестве изолирующего покрытия использовались резина, полиамиды, неопрен и др. Так, в частности на железных дорогах ФРГ применялись плоские металлические накладки с приклеенными к ним рейками из прессованной древесины или из стеклотканевого пластика / 99 /. Проводились работы по созданию гуммированных (обрезиненных) стальных накладок с металлическим защитным покрытием поверх изолирующего резинового слоя.
В США были разработаны изолирующие стыки с двухголовыми металлическими накладками и со слоистой резинометаллической изоляцией /98 /.
На Британских железных дорогах применяются сборные изолирующие стыки, в которых накладки покрываются изолирующим слоем из нейлона на половину длины с перекрытием стыкового зазора. Вторая накладка имеет нормальный профиль без изолирующего слоя / 100 /. В стыке накладки располагаются вразбежку, т.е. на конце рельсовой цепи с одной стороны располагается изолирующая часть накладки, а с другой стороны без изолирующего покрытия.
На железных дорогах Японии в основном применяется конструкция сборного изолирующего стыка типа Н. В этой конструкции изоляционный материал введен в необходимые места обычных стыков. Иными словами, между рельсами устанавливается прокладка, имеющая форму поперечного сечения рельса, между рельсом и стыковой накладкой устанавливается рельсовая прокладка, форма которой соответствует боковой поверхности рельса, а для изоляции болтов от накладки устанавливаются фланцевые трубки.
Кроме того, эксплуатация изолирующего стыка с объемлющими накладками приводит к преждевременному механическому износу стыковых шпал, к неравноупругости стыка.
Применение стопорных планок и изолирующих боковых прокладок для стопорных планок под 2 болта затрудняет и увеличивает продолжительность сборки изолирующего стыка. Уменьшение толщины стопорных планок вызывает их изгиб, в результате боковые изолирующие прокладки под стопорными планками продавливаются подголовками болтов и выходят из строя.
Конструкция объемлющих накладок не вполне отвечает условиям эксплуатации. Так при сборке изолирующего стыка объемлющая накладка упирается в две какие-либо расположенные под углом друг к другу плоскости, поэтому прижать накладку вплотную к третьей плоскости без значительных деформаций изоляции и самой накладки невозможно.
В зависимости от фактических размеров сопрягаемых элементов изолирующего стыка, распределение нормальных давлений на верхние и нижние полки боковых прокладок от натяжения болтов резко изменяется. В результате возникают перенапряжения в одних случаях и образуются зазоры между рельсом и боковой изоляцией в других, что приводит в конечном итоге к преждевременному разрушению изоляции. По этим же причинам при накладках объемлющего типа возникают стыковые дефекты и выколы подошвы рельсов и подошвенной части накладок, которые невозможно обнаружить без разборки стыка.
Ненадежность деталей изоляции объясняется, прежде всего, низкими физико-механическими характеристиками изолирующих материалов.
На железных дорогах с внедрением изолирующих стыков с объемлющими металлическими накладками наиболее распространенным изолирующим материалом была фибра марки ФЭ. Повышенная влагоемкость фибровых прокладок приводит к резкому падению диэлектрических свойств и усталостной прочности изолирующего стыка в процессе эксплуатации / 102 /. Наблюдения показывают, что массовый выход фибровой изоляции происходит весной и осенью, т.е. в периоды с наибольшей влажностью. Изоляция из фибры при хранении на открытом воздухе под влиянием окружающей среды быстро теряет свою первоначальную форму. Работоспособность фибровой изоляции не превышает 20 млн.т брутто, что при среднесетевой грузонапряженности соответствует только полугодовому периоду эксплуатации и требует двухразовой замены в год комплектов изоляции.
С учетом недостатков фибры, с 1964 года широко применяется изоляция из полиэтилена низкого давления, стабилизированная сажей. Конструктивно изоляция из полиэтилена отличается от фибровой только тем, что боковые прокладки изготовлены в виде двух полупрокладок. Преимуществом полиэтиленовых боковых прокладок является то, что они не изменяют своей первоначальной формы / 102 /, а на ее замену требуется на 30 — 40 % меньше времени, чем на замену фибровой изоляции. В то же время изоляция из полиэтилена низкого давления деформируется и выдавливается из стыка при совместном воздействии продолжительных сжимающих температурных сил, сил угона и высокой температуры в летнее время, что затрудняет ее использование на дорогах.
Сборные изолирующие стыки воспринимают продольные усилия не более 130 кН, что в эксплуатации приводит к смятию торцовых изолирующих прокладок в зазоре с замыканием рельсовой цепи.
Анализ работоспособности типовых конструкций сборных изолирующих стыков с объемлющими металлическими накладками и изоляцией из фибры и полиэтилена показывает, что они имеют ряд серьезных недостатков (таблица 4.3).
Существенным недостатком сборных конструкций изолирующего стыка является сравнительно небольшое сопротивление стыка перемещению рельсов. Недостаточное стыковое сопротивление — одна из основных причин интенсивного износа изолирующих деталей, относительно быстрого их разрушения при высоких и низких температурах.
Таблица 4.3 — Характеристика отказов элементов изолирующих стыков Наименование элементов | Виды отказов | Характер Проявления |
Объемлющие накладки | Поперечные изломы, выколы нижней части и трещины. | Внезапный (или постепенный) полный, неявный |
Двухголовые накладки | Поперечные изломы. | Внезапный, полный неявный |
Боковые изолирующие прокладки | Разрушение и выдавливание верхних полок под головкой рельса. | Постепенный, полный неявный |
Стыковые прокладки | Разрушение и выдавливание из стыкового зазора от действия температурных сил и сил угона пути. Изломы по шейке при растянутых зазорах. | Внезапный, полный неявный |
Боковые изолирующие планки | Разрушение (продавливание) от усилий натяжения болтов. | Постепенный, частичный явный |
Втулки-шайбы | Разрушение шайбовой части от усилий натяжения болтов. Разрушение цилиндрической части при растянутых стыках и величине зазоров, превышающих конструктивную. | Постепенный, частичный явный |
Для получения статистических данных об отказах сборных изолирующих стыков были проведены эксплуатационные испытания их с изоляцией из пресс-композиции в виде боковых и стыковых прокладок и втулок-шайб и с изоляцией из полиэтилена. Эксплуатационные испытания опытных изолирующих стыков проводились на экспериментальном кольце ВНИИЖТа и на железных дорогах Октябрьской, Алматинской, Западно-Сибирской и Белорусской. Наблюдения и сбор, данных проводились совместно с ВНИИЖТом, путеобследовательскими станциями ЦП МПС и местными работниками путевого хозяйства по методике ВНИИЖТа. Полученные результаты осмотра изолирующих стыков записывались в специальный журнал наблюдений, где отмечалась дата разрушения изоляции, отказ изолирующего стыка и ресурс, измеряемый в единицах наработки до момента отказа. По результатам проведенных эксплуатационных испытаний изоляции из пресс-композиции составлены графики, отражающие зависимость отказов изолирующих стыков от пропущенного тоннажа (рисунок 4.21), а зависимость сроков службы изоляции из пресс-композиции, полиэтилена и фибры от грузонапряженности приведена на рисунке 4.22.
Недостатки сборных изолирующих стыков с объемлющими накладками в значительной степени устранены в клееболтовых стыках / 105 /. Большая работа в этом направлении была проведена с 1969 года в Московском институте инженеров железнодорожного транспорта и Всесоюзном научно- исследовательском институте железнодорожного транспорта.
Основным преимуществом клееболтовых стыков является монолитность конструкции, которая исключает возможность взаимного перемещения рельсов и накладок при движении поезда. Это достигнуто путем прочного склеивания двухголовых накладок с рельсами.
Наиболее широко используются клееболтовые изолирующие стыки изготовленные на основе эпоксидной модифицированной смолы марки К- 153, полиэтилен-полиамина и стеклопластика Т-11, являющегося наполнителем клеевого соединения. Эта конструкция, хорошо себя зарекомендовавшая на практике, не лишена некоторых недостатков, и поиск новых клеевых составов и тканевых наполнителей продолжается.
В результате исследований была рекомендована конструкция клее- болтового изолирующего стыка, в которой используется клеевой состав ЭЛ-19 (эпоксидная смола ЭД 20 + низкомолекулярная полиамидная смола Л-19). Толщина клеевого соединения обеих конструкций Змм, длина клееболтовых изолирующих стыков 25м, что соответствует длине стандартных рельсов.
Клеевой состав ЭЛ-19 имеет ряд преимуществ и главное из них — нетоксичность. Кроме того, соединения с этим клеем имеют более высокие прочностные характеристики.
Общим недостатком рекомендованных клеевых составов является то, что они могут быть использованы только в жидком виде, и при ручном способе пропитки трудно обеспечить высокое качество клеевого соединения. В результате этого снижается активная площадь склеивания и, как следствие, ухудшаются прочностные характеристики конструкции в целом. Потери площади склеивания при существующем способе пропитки составляют около 25-30 %. На столько же примерно снижается сопротивление сдвигу рельсов. Наличие непроклеев отрицательно сказывается и на пределе выносливости клеевого соединения, так как они являются источником расслоения и развития трещин в стеклопластике.
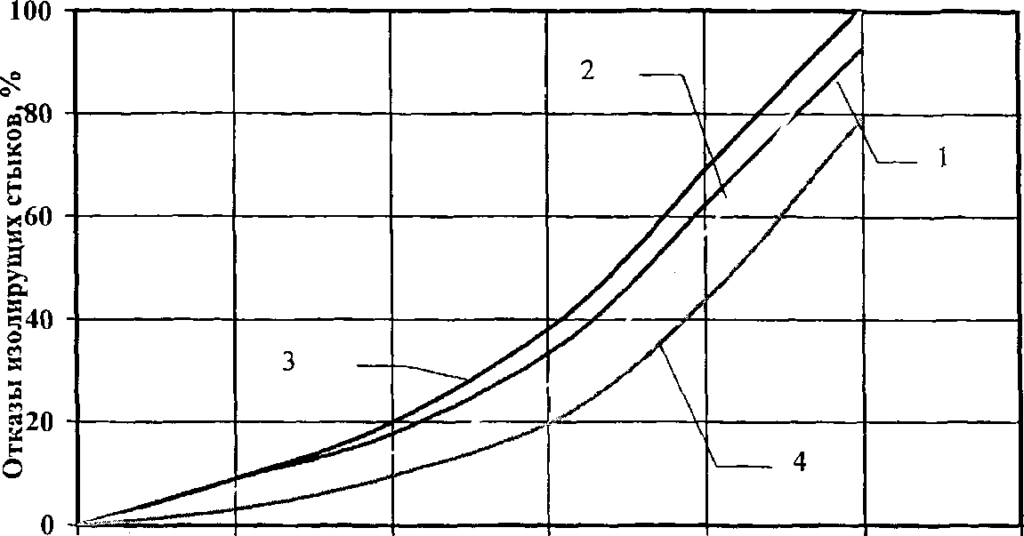
О 40 80 120 160 200 240
Пропущенный тоннаж, млн т
Рисунок 4.21 — Зависимость отказов изолирующих стыков с изоляцией из пресс-композиции от пропущенного тоннажа: 1 — экспериментальное кольцо ВНИИЖТа; 2 — Октябрьская железная дорога; 3 — Алма- Атинская железная дорога; 4 — Западно-Сибирская железная дорога
Грузонапряженность, млн. ткм/км
Продолжаются исследования по использованию в клееболтовых изолирующих стыках синтетических клеящих пленок.
Для оценки эксплуатационной стойкости и надежности различных конструкций были проведены специальные испытания изолирующих стыков. Испытания показали, что клееболтовые изолирующие стыки, изготовленные на основе эпоксидного клея К-153 и ткани Т-11 имеют существенные преимущества перед сборными и среднее время их безотказной работы примерно в 5 раз больше, чем у сборных стыков с изоляцией из полиэтилена.
Клееболтовые изолирующие стыки, изготовленные на основе синтетического эпоксидного клея ЭЛ — 19 и наполнителей ВПР- 10 и Т — 11, испытывали на сети дорог и на экспериментальном кольце ВНИИЖТа.
Опыты на экспериментальном кольце показали, что при 158 млн. т брутто пропущенного груза большинство клееболтовых стыков с тканевым наполнителем ВПР — 10 оказалось разрушенным. В связи с этим отказались от использования этой стеклоткани в стыках, укладываемых на главных путях с высокой грузонапряженностью.
Прочность клеевого соединения двухголовых накладок с рельсами зависит от многих факторов, среди которых большое значение имеют прочностные свойства клеевых составов и тканевых наполнителей, способ подготовки поверхностей под склеивание, режим полимеризации и ряд других.
Отсюда следует, что высокое качество изготовления клееболтовых стыков может быть гарантировано лишь при полном соблюдении технических требований и технологического процесса изготовления. Практика показывает, что отступления от этих требований сокращает время безотказной работы конструкций и эффективность их эксплуатации.
Учитывая трудности, связанные с заменой клееболтовых стыков на новые, очень важно сократить число отказов по дефектам заводского происхождения и обеспечить гарантии, регламентированные специальными техническими условиями. Большое значение имеет способ подготовки склеиваемых поверхностей под склеивание.
Исследования влияния различных способов подготовки склеиваемых поверхностей свидетельствуют о том, что при механической станочной обработке (строгание, фрезерование, шлифование и т.д.) химическая активность поверхности значительно ниже, чем при дробеструйной обработке. /,
Необходимо также учитывать, что накладки строгают заблаговременно, и до сборки стыка проходит время, достаточное для возникновения коррозии металла, развивающейся в дальнейшем в склеенной конструкции. Это подтверждают результаты разборки и осмотра преждевременно отказавших стыков.
В эксплуатации иногда наблюдается замыкание электрических рельсовых цепей из-за пробоя изоляции стыковых болтов. Отказы возникают из-за отсутствия фасок в болтовых отверстиях рельсов и смещения накладок относительно друг друга в продольном направлении при сборке стыка. Появляется перекос болтов, острые кромки болтовых отверстий рельсов соприкасаются с изоляцией болтов, которая при движении поезда постепенно разрушается. Кроме того, смещение накладок не позволяет установить рельсы по расчетным значениям стыковых зазоров: они оказываются больше.
Установлено, что смещение накладок чаще всего происходит из-за несоблюдения расстояний между болтовыми отверстиями при их сверлении.
Наличие надрезов или надрывов полимерного материала, в том числе и стеклопластика, является источником быстрого возникновения и развития трещин и усталостного разрушения конструкций.
Наблюдения за работой клееболтовых стыков показали, что разрушение клеевого соединения начинается в зоне стыкового зазора и постепенно распространяется к концам накладок. В результате этого уменьшается сопротивление стыка перемещениям рельсов и под действием продольных сил происходит отрыв рельсов по поверхностям склеивания, сопровождающийся изменением стыкового зазора.
После разрушения клеевого соединения клееболтовой изолирующий стык работает как сборный и изолирующая прослойка сравнительно быстро разрушается, вызывая отказ в работе устройств сигнализации и централизации.
Для своевременной замены разрушенного стыка резервным и для предотвращения отказов необходимо постоянно наблюдать за стыковыми зазорами клееболтовых стыков, так как они характеризуют плотность клеевого соединения рельсов с накладками.
Отказ изолирующего стыка может возникнуть в результате замыкания электрической цепи сплывами металла с головки рельса в стыковой зазор, замыкания рельсовой цепи скоплениями металлической стружки под подошвой рельса в месте стыкового зазора при намагничивании рельсов. При отказе рельсовых цепей устройств автоблокировки и электрической централизации необходим тщательный осмотр клееболтового изолирующего стыка.
Опыт и результаты лабораторных испытаний клееболтовых изолирующих стыков свидетельствуют о значительном разбросе полученных данных о сроках службы конструкции и сопротивления стыка продольным перемещением рельсов, что объясняется, прежде всего, разными условиями эксплуатации. Анализ причин отказов клееболтовых стыков показывает, что 65.3 % их выходит из строя из-за дефектов изготовления и 34.7 % из-за эксплуатационных дефектов.
Опыт показывает, что надежность действия рельсовой цепи во многом зависит также от слаженности в работе специалистов хозяйств пути и сигнализации и связи, так как в ряде случаев между ними отсутствует необходимая производственная взаимосвязь.
Аналитический обзор существующей литературы и статистических данных, рассмотренной выше, показывает, что нормальная работа рельсовой цепи в значительной мере зависит от надежности изолирующих стыков, а на участках с железобетонными шпалами -изоляции в рельсовых скреплениях. Несмотря на это, в практике не уделяется достаточного внимания анализу показателей, характеризующих надежность функционирования сборных и клееболтовых изолирующих стыков и рельсовых скреплений в различных условиях их эксплуатации. Одной из целей данной работы является повышение надежности рельсовых цепей, изолирующих стыков и рельсовых скреплений на основе оценки их надежности, оптимизации их конструкции, качества функционирования, периодичности ревизии и замены клееболтовых изолирующих стыков на перегоне и повышения прочности и надежности отдельных элементов рельсовых цепей.
Для достижения данной цели решаются следующие задачи:
- разработка методов определения показателей надежности работы рельсовых цепей, изолирующих стыков и рельсовых скреплений на железобетонных шпалах;
- определение оптимального количества резерва сборных и клееболтовых изолирующих стыков с учетом условий их эксплуатации;
- способ повышения прочности и надежности изолирующих и токо- проводящих стыков.
Формулировка проблемы, цели исследования и задачи, которые необходимо решить для достижения поставленной цели, а также структурная схема исследования приведены на рисунке 4.23.
Методология исследования базируется на комплексном подходе к железнодорожному пути, как к сложной, но единой системе, в которой могут быть выделены составляющие ее отдельные подсистемы и задачи. Все задачи тесно связаны друг с другом, как единством цели, так и внут^ ренней монолитностью всей системы.
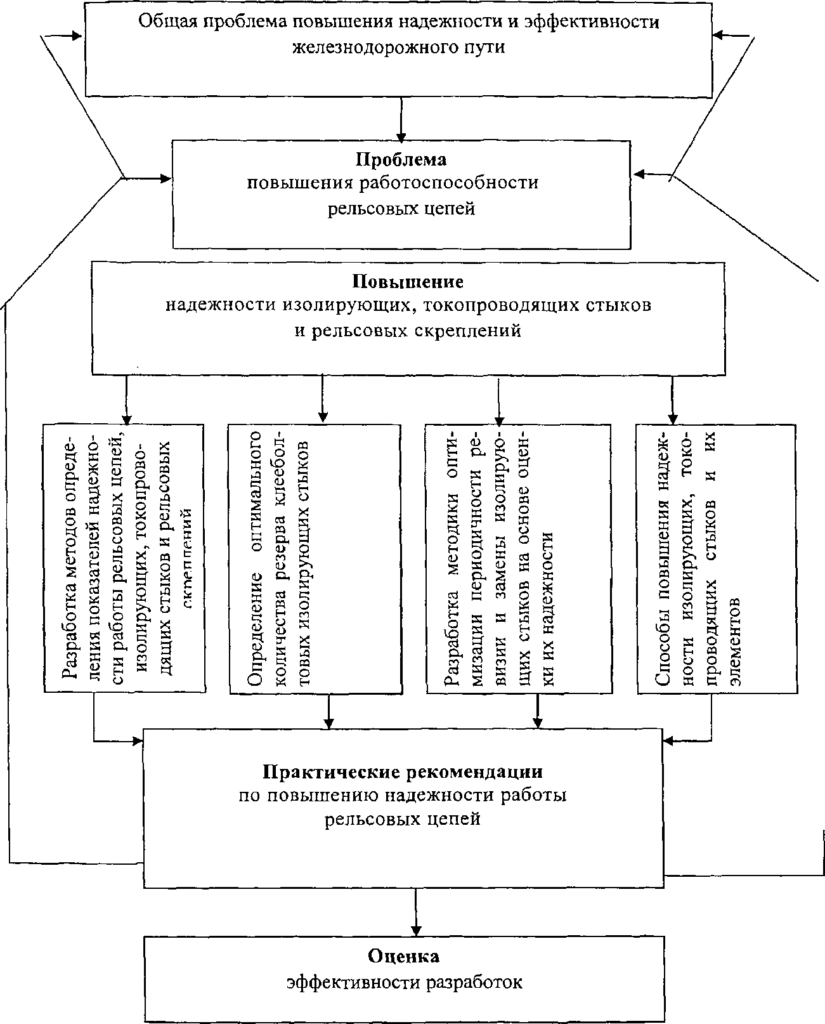
Рисунок 4.23 — Структурная схема исследования
Оценка надежности рельсовых цепей как объектов, восстанавливаемых в процессе применения
Показатели надежности объектов, восстанавливаемых в процессе применения, вычисляются лишь в календарном времени. Такие объекты можно разделить на две группы / 63 /.
К первой группе относятся объекты, для которых в течение заданного времени работы допускаются отказы и вызванные ими кратковременные перерывы в работе. Для объектов этой группы большое значение имеет свойство готовности — способности находиться в процессе эксплуатации значительную долю времени в работоспособном и готовом к применению состоянии.
Ко второй группе относятся объекты, отказы которых в течение заданного времени недопустимы. Если в этих объектах (системах) имеются избыточные элементы, то при отказах некоторых из них объект остается работоспособным и можно проводить ремонт отказавших элементов во время выполнения задачи.
Один и тот же объект может быть отнесен к разным группам в зависимости от режима его применения.
Рассмотрим процесс эксплуатации объектов первой группы. На рисунке 4.24 обозначено: — значения времени работы между отказа, (0 , («) , (‘) ми; tв — значения времени восстановления; — значение времени между (1-1 )-м и ¡-м восстановлениями; ^ моменты времени появления отказов (обозначены крестиками); — моменты времени окончания восстановления (обозначены кружками).
После отказа объект некоторое время находится в неработоспособном состоянии, т. е. восстанавливается. В результате ремонта объект приводят в работоспособное состояние. Периоды выключения объекта, когда он не отказывает и не восстанавливается, исключаются из рассмотрения.
Если случайные величины Т и Те независимы, то плотность распределения их суммы Т0 по известному из теории вероятностей правилу о композиции распределений равна t
где f(t)~ плотность распределения времени безотказной работы; g(t)~ плотность распределения времени восстановления объекта.
По аналогии с объектами, восстанавливаемыми вне процесса применения, можно рассматривать поток восстановлений с параметром t
O>o(0 = fo(t)+ \co0(T)f0(t-r)dr, (4.3)
где f0(t) — плотность распределения времени между очередными восстановлениями.
Параметр потока восстановлений со0(t) и плотность f0n(t) распределения времени до появления п-го восстановления (это время равно сумме Т0 связаны соотношением:
л=/ Надежность объектов первой группы может быть оценена при помощи мгновенных и числовых показателей. Одним из мгновенных показателей является параметр потока восстановлений co0(t). Однако обычно применяют вероятность r(t,) застать объект работоспособным (готовым к применению) в момент времени t, либо вероятность П(t,) = 1 —r(t,) того, что объект в момент времени tj будет
неработоспособным (будет находиться в состоянии вынужденного простоя). Зависимость r(t) называется функцией готовности.
Как r(tj), так и П(tl) определяются в предположении, что при t =0 объект работоспособен, т. е. Г(0) =1, П(0)= 0.
Объект может находиться в момент времени t в работоспособном состоянии при осуществлении одного из двух несовместных событий:
- 1) объект в течение времени (0, t) не отказал;
- 2) объект отказывал и восстанавливался и после последнего восстановления больше не отказывал.
Функция готовности r(t) равна сумме вероятностей появления указанных событий. Вероятность появления первого события равна вероятности безотказной работы p(t) объекта в течение времени (0, t) .
Оценка надежности рельсовой цепи, как невосстанавливаемого объекта
Для оценки надежности невосстанавливаемых объектов используют вероятностные характеристики случайной величины — наработки Т объекта от начала его эксплуатации до первого отказа. Под наработкой понимают продолжительность или объем работы объекта, измеряемые в часах, сутках, годах или в миллионах тонн пропущенного (наработанного) по участку груза.
При этом методе структура объекта изображается в виде специальной логической схемы, характеризующей состояние (работоспособное или неработоспособное) объекта в зависимости от состояний отдельных элементов.
При составлении структурных схем исходным было положение, что система последовательно соединенных элементов работоспособна тогда и только тогда, когда работоспособны все ее элементы (рисунок 4.25).
При параллельном соединении элементов или цепей элементов отказ системы происходит тогда и только тогда, когда откажут все параллельные участки схемы.
Оценка надежности изолирующих стыков
На сети железных дорог в настоящее время применяются сборные и клееболтовые изолирующие стыки. Наиболее распространенной конструкцией сборных изолирующих стыков являются изолирующие стыки с объемлющими накладками и отдельными деталями изоляции, собираемыми при монтаже стыка.
За последние годы доля нарушений, вызванных отказами изолирующих стыков, практически удвоилась, что естественно является не нормальным. Более 50 % отказов в работе рельсовых цепей по путейским причинам происходит из-за неисправности изолирующих стыков, остальная часть падает на рельсовые соединители и замыкание рельсов на балласт. Остается довольно высоким преждевременный выход клееболтовых изолирующих стыков.
Конструкция сборного изолирующего стыка с металлическими накладками объемлющего типа и изоляцией из полиэтилена и фибры не удовлетворяет современным эксплуатационным условиям. Быстрое разрушение изоляции стыка и вследствие этого отказ в работе рельсовых цепей нарушает работу устройств СЦБ, что приводит к сбою в графике движения поездов, нарушению нормального ритма всего перевозочного процесса и ставит под угрозу безопасность движения поездов.
К недостаткам наиболее распространенной конструкции изолирующих стыков с объемлющими накладками в первую очередь следует отнести мно- годетальность, металлоемкость и трудоемкость их сборки. Так изолирующий стык рельсов Р65 состоит из 19 электроизолирующих и 12 металлических деталей общей массой 86.82 кг на деревянных и 94.92 кг на железобетонных шпалах.
Образование зазора в стыке способствует появлению ударов по изоляции при прохождении поездов, от которых она быстро разрушается и выходит из строя. Увеличение натяжения болтов при этом изменяет площадь контакта верхних полок изоляции за счет отклонения накладок от вертикального положения и не параллельности сжатия изоляции. Накладки, смещаясь внутрь пазухи рельса прижимают изоляцию по узкой полоске под выкружкой головки рельса и способствуют ее преждевременному разрушению. По этим же причинам при накладках объемлющего типа возникают стыковые дефекты и выколы подошвы рельсов и подошвенной части накладок, которые невозможно обнаружить без разборки стыка. Такой стык малонадежен.
Срок службы изолирующих элементов от 3 до 6 месяцев (с фибровой прокладкой до 30 млн. т. брутто, с полиэтиленовой — до 70 млн. т. брутто). Стыковое сопротивление сборного стыка продольному сдвигу — 90-150 кН.
Многие недостатки сборных изолирующих стыков с объемлющими накладками устранены в клееболтовом стыке с двухголовыми накладками, количество которых на железных дорогах не превышает 10 %, что явно недостаточно при среднем сроке службы их 250 Мт и сравнительно не высокой стоимости в 65 долларов за 1 штуку. Кроме того, анализ причин отказов клееболтовых стыков показывает, что 65.3 % их выходит из строя из-за дефектов изготовления и 34.7 % из-за эксплуатационных дефектов, основными из которых являются: дефекты рельсов-20.3 %, выход торцевой изоляции — 13.9 %, нарушение изоляции болтов -22.2 %, нарушение боковой изоляции накладок — 25.3 % и прочие — 18.3 %. Производство клееболтовых стыков, как с двухголовыми так и с полнопрофильными накладками в необходимом количестве сдерживается малой производительностью специализированных цехов при рельсосварочных поездах и дефицитностью новых рельсов.
Стыковое сопротивление клееболтового стыка продольному сдвигу равно 1200-1500 кН, а для монолитного соединения не менее 3000 кН.
Изолирующий стык состоит из нескольких металлических и изолирующих элементов, работающих в разных нагрузочных условиях и обладающих разной надежностью- В связи с этим большое значение имеет правильный и наиболее соответствующий условиям работы метод и схема расчета. Для выбора схемы расчета рассмотрим полные электрические схемы замещения изолирующего стыка, как электрической цепи, согласно существующих рекомендаций.
Согласно приведенным схемам в типовой конструкции изолирующего стыка с объемлющими металлическими накладками изоляция стыковых болтов от накладок обеспечивается изолирующими втулками Re и боковой изолирующей планкой Rfa , при чем оба болта соединены между собой стопорной металлической планкой. Изоляция накладок от концов стыкуемых рельсов во всех схемах обеспечивается боковыми изолирующими прокладками Re, а изоляция концов стыкуемых рельсов — стыковыми (торцевыми) прокладками по профилю рельсов. При объемлющих накладках изоляция рельсов от накладок также обеспечивается нижними прокладками под подошву рельсов RHn (рисунок 4.28).
В отличие от конструкции изолирующих стыков с объемлющими накладками в клееболтовых стыках с двухголовыми шестидырными накладками изоляция каждого стыкового болта в отдельности осуществляется стеклотканью (рисунки 4.28 и 4.29).
Из анализа приведенных электрических схем замещения изолирующего стыка видно, что отказ изолирующего стыка, как электрической цепи, происходит, если создается возможность прохождения электрического тока сигнализации непосредственно от одного конца рельса к другому при сбое торцовой изоляции Rc или через одну из накладок при пробое боковой изоляции Re или изоляции стыковых болтов от накладок Re, R6n,RUH, Rue .
Это дает возможность при выборе расчета надежности изолирующего стыка отдельные группы элементов с учетом условий их работы и влияния на надежность в целом объединить в блоки.
Изолирующий стык с точки зрения надежности изоляции можно рассматривать как систему, состоящую из нескольких не
Вероятность безотказной работы изолирующего стыка с объемлющими накладками в соответствии со структурной схемой, приведенной на рисунке 4.30 , определится по формуле:
Рис Реп ‘ РНП бп ‘ Р^вп . (4.26)
Здесь Рсп — вероятность безотказной работы стыковой прокладки. Вероятность безотказной работы нижней прокладки определится по формуле:
где Ркнп — вероятность отказа нижней прокладки на одном конце рельса.
равнонадежных блоков (рисунки 4.30 и 4.31). Некоторые блоки имеют резервные цепи.
Вероятность отказа боковой полупрокладки определится по формуле:
Р6п = 1 — (1-Ркбп)2 , (4.28)
где Рк6п — вероятность отказа боковой полупрокладки на одном конце рельса.
Вероятность отказа участка цепи, состоящей из двух втулок и изолирующей планки, определится по формуле:
Рвп = [1-(1- Р2вPJ2], (4.29)
где Рв и Рт — вероятности безотказной работы соответственно изолирующих втулок и боковых планок.
Вероятность безотказной работы клееболтового изолирующего стыка в соответствии со структурной схемой, приведенной на рисунке 4.31, определится по формуле:
Puc=PcnP2un-P2u6. (4.30)
Вероятность отказа изоляции накладки боковой Рин определится по формуле:
Pu« = 41-PKuj\ (4.31)
где Ркин — вероятность отказа боковой изоляции накладки на одном конце рельса.
Вероятность отказа изоляции болтов определится по формуле:
Риб = Н1-Р\иб)\ (4.32)
где Ркиб — вероятность безотказной работы изоляции одного болта на одном конце рельса.
Вероятность безотказной работы изолирующего стыка с композитными накладками составит:
Рис Реп ‘Р^КН> (4-33)где Ркн — вероятность безотказной работы композитной накладки.
Надежность изолирующих стыков на дорогах СССР
В советский период наиболее глубокие исследования надежности изолирующих стыков выполнены сотрудниками БелИИЖТа / 102 /. Отказы стыков наиболее близко подчиняются закону нормального распределения, что было установлено графическим способом при помощи координатной сетки и аналитическим методом по виду кривой вероятности безотказной работы и закона распределения отказов путем сравнения с соответствующими теоретическими кривыми. Так при нормальном законе распределения случайная величина может принимать любые значения от — сю до +со, а время безоткаэ^ ной работы может быть только положительным, нужно рассматривать усеченное нормальное распределение с плотностью.
Основные характеристики надежности изоляции из пресс-композиции, определенные по статистическим данным результатов эксплуатационных испытаний, приведены в таблице 4.4.
Оценка вероятности безотказной работы изолирующих стыков за время I, выраженное в Мт брутто пропущенного тоннажа определена по формуле.
где Фо(%) — нормированная функция Лапласа, при этом следует учитывать, что Фо(-г)=-Фо(2).
Места эксплуатационных испытаний | Т | що | ЛТ | Т 1 н | т. |
Мт брутто | |||||
Экспериментальное кольцо ВНИИЖТа | 150 | 32.6 | 22 | 128 | 172 |
Октябрьская железная дорога, Калининская дистация пути | 155 | 28.4 | 19 | 136 | 174 |
Алма-Атинская железная дорога, Алма-Атинская дистанция пути | 144 | 31.5 | 21 | 123 | 165 |
Западно-Сибирская железная дорога, Болотинская дистанция пути | 156 | 38.3 | 24 | 132 | 180 |
Результаты расчета вероятности отказов и вероятности безотказной работы Р(г) сборных изолирующих стыков с изоляцией из пресс-композиции и втулок-шайб БелИИЖТа приведены в таблице 4.4. Аналогично определена вероятность безотказной работы сборных изолирующих стыков с изоляцией из фибры и полиэтилена, а вероятность безотказной работы клееболтовых взята на основании исследований ВНИИЖТа. Графическое изображение вероятности безотказной работы изолирующих стыков с различной изоляцией в зависимости от пропущенного тоннажа (наработки) представлено на рисунке 4.32, где обозначены типы изоляции: 1 — из фибры; 2 — из полиэтилена; 3 — торцевая из стеклопластиков АГ- 4; 4, 5 — из пресс-композиции; 6 — втулки- шайбы БелИИЖТа; 7 — клееболтовые по опыту эксплуатации; 8 — клееболтовые по данным ВНИИЖТа.
Из рисунка 4.32 видно, что срок службы (наработка) при уровне вероятности безотказной работы Р = 0.9 изолирующих стыков с объемлющими накладками составляет 30-60 Мт, а стыков с изоляцией из пресс-композиции и втулками-шайбами БелИИЖТа — 100-120 Мт.
Наработка клееболтовых стыков при том же уровне вероятности безотказной работы составляет 160-220 Мт. Разработчики клееболтовых изолирующих стыков декларируют срок службы в размере 250 Мт /102 /.
Анализ надежности работы изолирующих стыков на опытных участках
Для определения вероятности безотказной работы сборных и клееболтовых изолирующих стыков в зависимости от количества пропущенного тоннажа были произведены наблюдения за их работой на различных опытных участках.
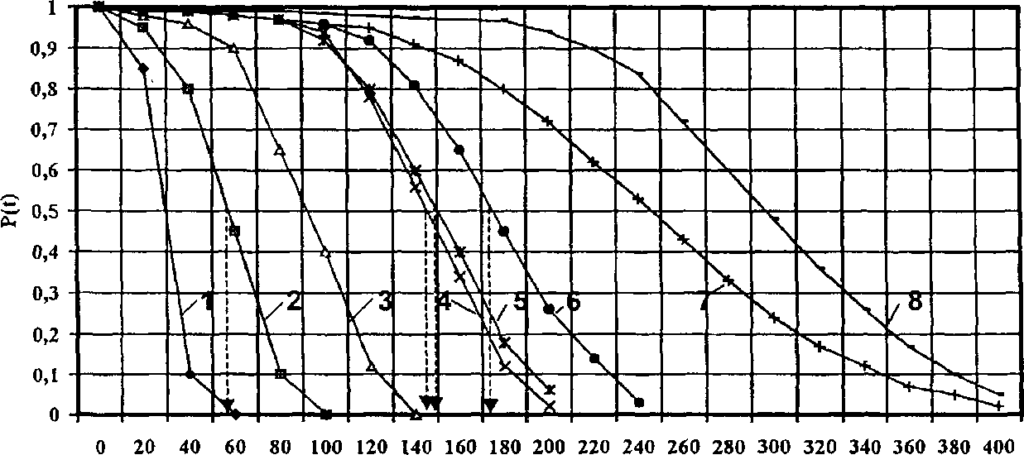
Т, млн. т брутто
Рисунок 4.32 — Эксплуатационная (статистическая) надежность изолирующих стыков: изоляция из: 1 — фибры; 2 — полиэтилена; 3 — торцевая из АГ-4; 4, 5 — пресскомпозиции; 6 — втулки — шайбы БелИИЖТа; 7, 8 — клее- болтовые стыки с двухголовыми накладками
В таблице 4.5 приведены данные для участков, где вероятности безотказной работы подчиняются нормальным законам распределения.
По результатам расчетов были построены графики эмпирической и теоретической плотности распределения вероятности отказов изолирующих стыков в зависимости от пропущенного тоннажа, которые представлены на рисунках 4.33 и 4.34.
Соответствие теоретической и эмпирической плотности распределения вероятности отказов оценивалось для усеченного нормального закона распределения, по критерию %2.
Для усеченного нормального закона были определены значения Тср и сг( с использованием данных таблицы 4.5 по методу квантилей. При этом были получены следующие результаты: для сборных изолирующих стыков Тср = 100 Мт, сг,= 30 Мт; для клееболтовых — Тср = 250 Мт, <т,= 82 Мт.
Исследования соответствия эмпирической и теоретической плотности распределения вероятности отказов для усеченного нормального закона распределения показали, что для сборных изолирующих стыков эксплуатируемых на участке 1 оказался равным 20.62, что меньше теоретического значения xlos равного 23.24. Это означает, что плотность распределения вероятности отказов сборных изолирующих стыков на данном участке подчиняется нормальному усеченному закону.
Этому же закону подчиняется плотность распределения вероятности отказов клееболтовых изолирующих стыков на участке 4, так как экспериментальное значение х2~ 15.53, что меньше чем теоретическое значение ^=23.24.
Тогда срок службы изолирующих стыков с объемлющими накладками составит: 100- 1.65-30 = 50.5 Мт. Срок службы клееболтовых стыков составит: I = 250 — 1.65 • 82 = 115 Мт.
Таблица 4.5 — Данные для определения вероятности безотказной рабо изолирующих стыков в зависимости от пропущенного тоннажа | Сборные изолирующие стыки | Клееболтовые изолирующие стыки | ||
участки железных дорог | ||||
1 | 2 | 3 | 4 | |
Пропущенный тоннаж, млн. т | ||||
1 | 120 | 89 | 102 | 526 |
2 | 157 | 7 | 311 | 387 |
3 | 210 | 126 | 170 | 335 |
4 | 180 | 200 | 92 | 282 |
5 | 160 | 133 | 336 | 240 |
6 | 120 | 150 | 206 | 248 |
7 | 118 | 170 | 293 | 367 |
8 | 200 | 2 00 | 189 | 202 |
9 | 120 | 140 | 228 | 145 |
10 | 97 | 135 | 39 | 444 |
11 | 220 | 180 | 304 | 458 |
12 | 55 | 71 | 330 | 369 |
13 | 110 | 98 | 148 | 474 |
14 | 180 | 154 | 176 | 267 |
15 | 152 | 180 | 188 | 443 |
16 | 154 | 95 | 385 | 206 |
17 | 138 | 99 | 441 | 318 |
18 | 105 | 200 | 240 | 240 |
19 | 178 | 133 | 461 | 260 |
20 | 111 | 155 | 468 | 276 |
21 | 111 | 180 | 317 | 257 |
22 | 200 | 219 | 326 | 367 |
23 | 158 | 78 | 295 | 339 |
24 | 140 | 140 | 280 | 79 |
25 | 201 | 140 | 295 | 302 |
26 | 140 | 160 | 328 | 357 |
27 | 65 | 200 | 344 | 278 |
28 | 151 | 140 | 208 | 378 |
29 | 177 | 119 | 377 | 399 |
30 | 159 | 191 | 291 | 272 |
31 | 44 | 137 | 290 | 316 |
32 | 207 | 200 | 350 | 412 |
33 | 216 | 236 | 381 | 358 |
34 | 156 | 180 | 315 | 385 |
35 | 157 | 180 | 286 | 383 |
36 | 180 | 48 | 293 | 335 |
37 | 18 | 140 | 115 | 287 |
38 | 223 | 219 | 182 | 253 |
39 | 177 | 200 | 94 | 279 |
40 | 171 | 173 | 196 | 368 |
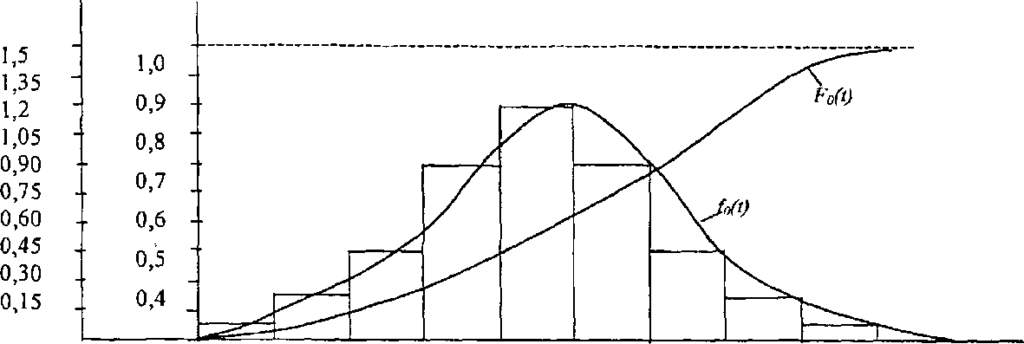
20 40 60 80 100 120 140 160 180 200
Наработанный тоннаж, млн. т брутто
Рисунок 4.33 — Распределение плотности f(t) и вероятности отказов Fo(t) сборных изолирующих стыков
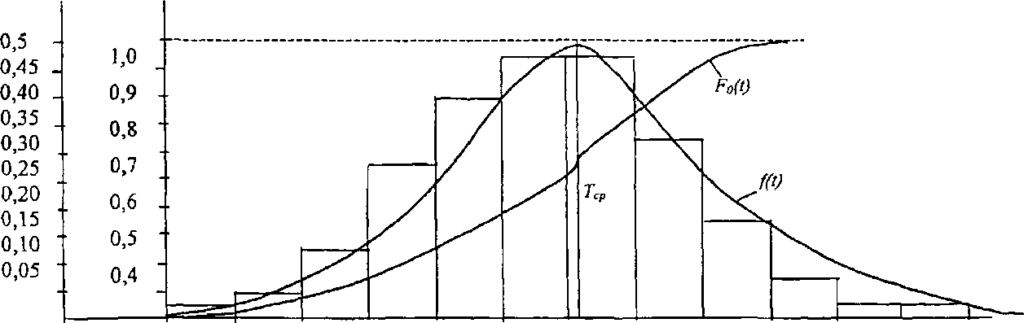
40 80 120 160 200 240 280 320 360 400 440 480
Наработанный тоннаж, млн. т брутто
Рисунок 4.34 — Распределение плотности f(t)и вероятности отказов F0(t) клееболтовых изолирующих стыков
Малый срок службы клееболтовых стыков объясняется низким качеством их изготовления.
Анализ надежности работы изолирующих стыков исходя из надежности их элементов
По результатам обработки статистических данных отказов элементов сборных и клееболтовых изолирующих стыков по методу квантилей были получены значения Тср и а, представленные в таблице 4.6.
По результатам расчетов с использованием данных таблицы 4.6 и в соответствии с логическими схемами для вычисления надежности элементов сборных изолирующих стыков на деревянных шпалах и железобетонных шпалах и клееболтовых изолирующих стыков на железобетонных шпалах построены графики безотказной работы элементов, которые представлены на рисунках 4.35 — 4.37, соответственно.
Таблица 6.4 — Статистические характеристики наработки до отказа элементов изолирующих стыков Элементы изолирующего стыка | Статистические характеристики наработки до отказа элементов изолирующего стыка | |||
Сбо | эный | |||
на деревянных шпалах | на железобетонных шпалах | |||
ТСР | с, | Тср | ||
Накладка | 863 | 160 | 874 | 175 |
Боковая прокладка | 172 | 52 | 176 | 55 |
Втулка | 216 | 68 | 220 | 66 |
Торцовая прокладка | 116 | 36 | 119 | 40 |
Прокладка под рельс | 220 | 66 | 230 | 70 |
Боковая планка | 205 | 60 | 210 | 61 |
Клееболтовой стык | ||||
Накладка | 853 | 170 | ||
Торцовая прокладка | 270 | 907 | ||
Изоляция болтов | 250 | 75 | ||
Стеклотканевая прокладка (боковая) | 310 | 90 / |
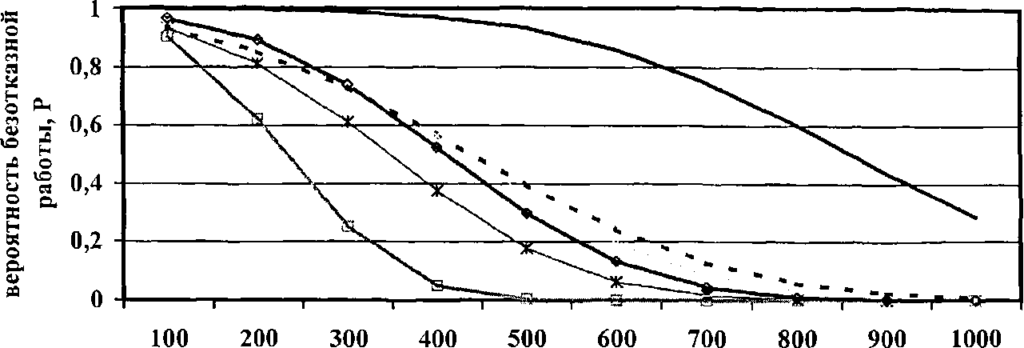
Рисунок 4.35 — Вероятность безотказной работы элементов сборного изолирующего стыка на деревянных шпалах
Рисунок 4.36 — Вероятность безотказной работы элементов сборного изолирующего стыка на железобетонных шпалах
Рисунок 4.37 — Вероятность безотказной работы элементов клееболтового изолирующего стыка на железобетонных шпалах
Из рисунков 4.35 и 4.36 видно, что самым ненадежным элементом сборных изолирующих стыков являются торцовые прокладки. Это объясняется тем, что на них воздействуют большие продольные силы, которые зависят от температурных сил и сил угона. Самым ненадежным элементом клее- болтовых изолирующих стыков является изоляция болтов, что видно из рисунка 4.37.
Для поддержания работоспособности изолирующих стыков за ними должен быть установлен постоянный надзор. Под изолирующими стыками должны находиться здоровые, хорошо подбитые шпалы. В районе изолирующих стыков путь должен быть закреплен от угона по установленным нормам. При соблюдении этих условий периодичность переборки или замены изолирующих стыков, исходя из их надежности, следует производить в соответствии с таблицей 4.7.
Таблица 4.7 — Периодичность (в годах) замены изолирующих стыковКонструкция изолирующих стыков | Грузонапряженность, млн. т. брутто | |||
50 | 25 | 10 | 5 | |
Сборные | 1 | 2 | 5 | 10 |
Клееболтовые | 2 | 4 | 10 | 20 |
Данные таблицы 4.7 в основном совпадают с нормативными документами / 82 /, которые требуют после пропуска каждых 50 млн. т. пропущенного тоннажа, но не реже одного раза в два года на путях 1 -3 класса и в три года на остальных путях осматривать сборные изолирующие стыки. При этом необходимо снятие накладок и замена поврежденных и изношенных деталей.
Если для примера взять длину перегона 20 км, длину блок-участка в среднем 2 км,Nk6= 12, Тср = 250 Мт и <т,= 82 Мт, то выход клееболтовьйс стыков в функции наработанного тоннажа определится данными таблицы 4.8.
Таблица 4.8 — Вероятность отказов Р0 (%) и количество отказавших N0 клееболтовых стыковПоказатели | Наработанный тоннаж, млн. т. брутто | ||||||
40 | 80 | 120 | 160 | 180 | 200 | 240 | |
(і) | 0.005 | 0.019 | 0.057 | 0.136 | 0.270 | 0.452 | 0.644 |
N0 | 0.06 | 0.23 | 0.68 | 1.63 | 3.25 | 5.42 | 7.73 |
Из таблицы 4.8 следует, что до наработки 120 Мт груза на каждом перегоне достаточно иметь один рельс со встроенным клееболтовым стыком. Эксплуатация этих стыков после наработки 160 Мт нецелесообразна и экономически и с позиций безопасности движения поездов.
Анализ отказов подрельсового основания
Опыт эксплуатации рельсовых цепей показывает, что безотказность их работы зависит от сопротивления балласта, которое влияет на регулировочный, шунтовой и контрольный режимы работы, а следовательно, и на безопасность движения поездов.
Измерения показывают, что минимальное сопротивление балласта, особенно на станционных путях, может быть значительно ниже нормативной величины (1.0 Ом • км) и достигает 0.2-0.3 Ом • км. В результате рельсовые цепи, особенно сигнальной частотой 50 и 75 Гц, периодически работают неустойчиво и требуют непрерывной регулировки. В некоторых случаях мощность питающих трансформаторов оказывается недостаточной для обеспечения нормальной работы рельсовых цепей, что вызывает необходимость установки вторых трансформаторов дополнительных регулировочных сопротивлений и т. п.
Таким образом, в практике сложилась довольно сложная ситуация: с одной стороны, разработка рельсовых цепей базируется на нормативных величинах параметров рельсовой линии: сопротивлений балласта и рельсов, причем в их схемах не предусматривается достаточных регулировочных запасов; с другой — эксплуатация этих цепей, особенно на крупных станциях, ведется при пониженных сопротивлениях балласта, что в сильной степени затрудняет регулировку и содержание рельсовых цепей. Поэтому для их анализа и проектирования актуальным является отыскание закона распределения величины сопротивления балласта, с учетом которого можно провести объективный выбор длины рельсовой цепи и параметров элементов ее схемы.
В период между капитальными ремонтами пути сопротивление балласта может значительно отклоняться от установленной нормы и улучшение электрического состояния рельсовых цепей возможно лишь при проведении дополнительных дорогостоящих ремонтных путевых работ. Поэтому наряду
с выполнением таких работ необходимо совершенствовать методы регулировки и синтеза рельсовых цепей при пониженном сопротивлении балласта.
Величина сопротивления балласта в общем случае является случайной функцией ряда случайных переменных: вида и состояния балласта, степени его загрязненности солями, пылью, типа и состояния шпал, климатологических факторов и т. д. Для конкретного вида балласта и шпал факторами, определяющими величину сопротивления балласта рельсовых цепей, являются степень влажности балласта и температура воздуха. Измерения показывают, что сопротивление балласта уменьшается с ростом окружающей температуры, приближаясь к какому-то предельному для конкретного вида балласта и состояния влажности значению. Однако в практических условиях минимальное значение сопротивления балласта наблюдается при некоторых критических значениях влажности и температуры среды, с дальнейшим возрастанием температуры более 25°С сопротивление балласта возрастает, что, можно объяснить ускоренным испарением влаги, а следовательно, непрерывным изменением степени влажности шпал и балласта.
Очевидно, что безотказность работы рельсовых цепей зависит от состояния балласта в наихудших условиях, т. е. при критической температуре и средней влажности балласта (влажный балласт). Следовательно, и вероятность безотказности ее работы должна определяться с учетом распределения сопротивления балласта рельсовых цепей в этих условиях.
Обработка результатов измерений величин сопротивления балласта, проведенных при упомянутых выше условиях на ряде станций железных дорог, позволяет построить функцию плотности распределения вероятностей величин сопротивления балласта (рисунок 4.38).
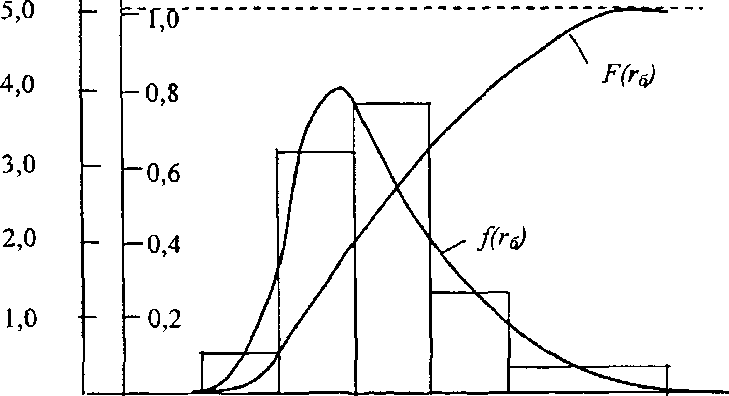
Рисунок 4.38 — Функция и плотность распределения сопротивления балласта
Надежность работы рельсовых скреплений
Численные значения вероятности безотказной работы узлов скреплений в зависимости от наработанного тоннажа указаны в таблице 4.9.
Таблица 4.9 — Вероятности безотказной работы узлов скреплений в зависимости от наработанного тоннажаТоннаж, Мт брутто | Тип узла скрепления | ||
КБ-65 | БП | ЖБР | |
100 | 0.9968 | 0.9749 | 0.9404 |
200 | 0.9838 | 0.9342 | 0.8506 |
300 | 0.9478 | 0.8622 | 0.6989 |
400 | 0.8004 | 0.7632 | 0.5472 |
500 | 0.6498 | 0.6371 | 0.3025 |
600 | 0.3962 | 0.4801 | 0.1274 |
700 | 0.2460 | 0.3205 | — |
Однако отказ узла скрепления еще не означает отказа всей системы связей рельса с основанием. Согласно нормативным документам поперечная устойчивость рельсовых нитей и всей рельсошпальной решетки обеспечивается, если нет кустов из трех негодных шпал, а рельсовая нить не расшита более чем на трех или шести шпалах подряд. Справедливость этих требований подтверждается результатами проведенных в последнее время исследований поперечной устойчивости пути на железобетонных шпалах под поездной нагрузкой. Опыт эксплуатации скреплений КБ на железобетонных шпалах показал, что после пропуска по участку с этими скреплениями 350 — 400 млн. т брутто груза происходит отказ 20-30 % электроизолирующих деталей. Удельное сопротивление подрельсового основания снижается до 0.2 — 0.25 Ом-км, что ведет к отказу рельсовых цепей. Это подтверждается результатами расчетов, приведенных на рисунке 4.39.При этом математическое ожидание срока службы скреплений КБ составляет Тер = 533 Мт, а сг= 160 Мт.
Надежность работы токопроводящих стыков
Как известно, электрическое сопротивление рельсовых стыков — величина переменная и зависит от токопроводности стыкового соединителя и накладки / 127 /. Таким образом, стык имеет две параллельные цепи, электрическое сопротивление которых изменяется по различным законам. В силу этого происходит перераспределение тягового и сигнального тока между стыковым соединителем и накладкой.
В последние годы ведутся работы с целью обеспечить токопроводи- мость стыка «нормальным его содержанием». В качестве альтернативы выдвигается условие надежной затяжки болтов в стыке. Но его электропроводность через накладку зависит не только от степени натяжения болтов, а и от состояния контактируемых поверхностей накладка — рельс в различных эксплуатационных условиях. Для получения надежного электрического соединения в стыке необходимо использовать оба пути: надежный контакт между рельсами и накладками и надежный стыковой соединитель. Тогда токопро- водящий стык будет представлять собой систему с резервом.
Несмотря на то, что проблема улучшения проводимости стыка возникла одновременно с появлением электрических рельсовых цепей, в литературе недостаточно внимания уделено определению основных параметров соединителей и выбору их оптимальных величин. В работе 1X211 приводятся данные по электрическому сопротивлению различных видов соединителей, которые давно уже не применяются на сети дорог. Н. Ф. Котляренко / 127 / в качестве нормативной величины омического сопротивления соединителя дает гс = 300 • 10″6 Ом, В качестве нормы сопротивления токопроводящего стыка принято эквивалентное сопротивление 3 м целого рельса.
На параметры стыков и соединителей влияют следующие показатели:
а) нормативная величина электрического сопротивления, устанавливаемая для длины целого рельса в зависимости от типа;
б) надежности работы рельсовых цепей в различных режимах;
в) предельная температура нагрева провода (соединителя);
г) падение напряжения в обратной цепи контактной сети.
Были проведены исследования с целью определения полного и переходного сопротивления соединителя, а также распределения тока по накладке и соединителю в зависимости от величины сигнального тока, протекающего по рельсовому стыку. Измерения проводились на макете токопроводящего стыка, состоящего из двух отрезков рельсов типа Р65, соединенных двумя накладками и типовым приварным соединителем.
В результате исследований установлено для постоянного тока:
- электрическое сопротивление соединителя составляет — (70-80) • 10″6Ом;
- электрическое сопротивление накладок — (14-20) • 10″6 Ом;
- переходное сопротивление: соединитель — рельс — (35 -40) ■ 10″6 Ом;
- переходное сопротивление: накладка — рельс — 2- 10″6 Ом.
Для переменного тока:
- сопротивление соединителя за счет индуктивной составляющей выше, чем для постоянного тока, и составляет в среднем (250-300) • 10″6 Ом; т. е. находится в пределах установленной в настоящее время нормы;
- величина тока, протекающего через соединитель, составляет 10 % от общего тока, проходящего через стык.
Данные лабораторных исследований подтверждены результатами измерений в реальных рельсовых цепях на грузонапряженных участках дорог. При этом выявлено, что в середине фидерной зоны токи, протекающие в рельсах одного пути, составляют различные величины, а в горловине станции их величины отличаются лишь в момент прохода поезда. Условие равенства токов в рельсах одного пути в горловине станции (в непосредственной близости от дроссель-трансформаторов) использовалось при замере сопротивления стыков и стыкового соединителя, величины которых изменяются в широких пределах и составляют соответственно: (45-750) • 10~6 Ом и (250-410) •10″6 Ом. Следует отметить, что в эксплуатационных условиях сопротивление стыка может намного превышать указанную величину (750-10′6 Ом), что показывает на его ненадежность.
В процессе эксплуатации стыковые соединители могут подвергаться воздействию тяговых токов при следующих временных режимах: а) длительный режим, определяемый средним значением тока за часовой период; б) кратковременный режим, определяемый временем прохождения тяговых токов повышенной величины.
Во всех случаях худшими условиями, когда через стыковые соединители проходит максимальный ток, будут зимние условия работы рельсовых цепей при г б = г б тах , т.е. когда токи утечки минимальные.
Измерения, проведенные непрерывно в течение 8 ч в период максимальных нагрузок на фидерной зоне, показали, что средняя величина тока, протекающего в рельсах, не превышает 700 А, а через соединитель — 30 А. При кратковременном режиме через стыковые соединители проходят тяговые токи повышенной величины. Были зафиксированы максимальные значения тока в рельсах, равные 1280 А, а в стыковом соединителе — 54 А. Однакб такие токи действуют в течение короткого промежутка времени, исчисляемого секундами.
При повышении сопротивления стыка более 750- 1С)»6 Ом следует считать его ненадежным. Можно считать, что критическим для соединителя является режим кратковременного нагрева, для которого допустимой температурой является величина 9 = 250-300°С.
Для достижения оптимального уровня надежности системы необходимо, по меньшей мере, на порядок понизить количество отказов по отдельным ее элементам, имеющим низкую надежность.
Наиболее удобно надежность стыков и стыковых соединителей характеризовать средней частотой отказов:
1 год где An — — число отказов, происходящих в определенные интервалы времени; N — количество элементов.
Анализ статистических данных дорог показывает, что причинами нарушения нормального функционирования стыка являются: 1) повышение переходного сопротивления стыка; 2) сбой стыкового соединителя; 3) неисправность соединителя.
Для быстрого восстановления отказавших соединителей нужно иметь в запасе пружинные или штепсельные (обводные на конических болтах) рельсовые соединители.
Анализ отказов и повышение надежности рельсовых цепей
Рельсовая цепь представляет собой электрическую цепь без специальной внешней изоляции, проложенную в общедоступных местах. Она испытывает на себе постоянные динамические нагрузки от проходящих поездов, колебания температуры и влажности воздуха. Применяемые в рельсовой цепи соединительные и изоляционные элементы имеют недостаточный запас механической прочности. Профилактическое обслуживание рельсовых цепей и оперативное восстановление после отказа выполняют работники нескольких служб (сигнализации и связи, пути, электрификации), причем работники сигнализации и связи, проводящие профилактические измерения и определяющие место отказа, не имеют возможности самостоятельно устранить отказ или выполнить работы по его предотвращению, а работники службы пути, выполняющие работы подобного типа, не имеют возможности выявить место отказа или определить необходимость профилактики.
Таблица 4.10 — Параметры внезапных отказов элементов рельсовых цепейНаименование элементов рельсовых цепей | Интенсивность отказов, 1/год | Средняя наработка до отказа, лет |
Изолирующие стыки сборные | 0.075-0.15 | 13.3-6.7 |
Изолирующие стыки клееболтовые | 0.035-0.08 | 28.6-12.5 |
Приварные соединители | 0.015-0.025 | 66.7- 40 |
Подрельсовые основания | 0.0034-0.0068 | 294- 147 |
Наиболее ненадежными элементами рельсовой цепи являются изолирующие стыки, элементы изоляции стрелок и стыковые соединители.
Подавляющее большинство отказов в рельсовых цепях происходит вследствие повышенного затухания в рельсовой цепи, которое может быть вызвано обрывом или повышением сопротивления в цепи (стыковые соединители, джемпера, перемычки) или же из-за уменьшения сопротивления изоляции до короткого замыкания (изоляция на стрелке, изолирующие стыки, балласт, посторонние предметы).
Среднее время восстановления — это, по существу, среднее время простоя поездов из-за отказа автоблокировки. При этом следует учитывать не только чистое время ремонта, но и время доставки бригады к месту происшествия и время, затрачиваемое на поиск неисправных элементов.
Если на устранение отказов затрачено время t¡, 12,…, tm, то среднее время восстановления:
/ г = т Т =— X г.,
6 171 I = 1 1
где т — число отказов.
По результатам обработки существующих данных и материалов полученных путем наблюдений среднее время восстановления отказавших изолирующих стыков и рельсовых соединителей можно принять Тв = 3 ч.
Определение коэффициента готовности блок-участка кг к пропуску поездов осуществляется по формулам (4.7) и (4.17) с использованием логических схем, приведенных на рисунках 4.30 и 4.31. Результаты расчетов приведены в таблице 4.11.
Таблица 4.11 — Оценка надежности рельсовых цепейКонструкция пути | Коэффициент готовности | |
Одной рельсовой цепи | Участка длиной 100км | |
Звеньевой путь на деревянных шпалах со сборными изолирующими стыками | 0.980 | 0.909 |
То же с клееболтовыми изолирующими стыками | 0.990 | 0.952 |
Бесстыковой путь с железобетонными шпалами и клееболтовыми изолирующими стыками | 0.999 | 0.995 |
Из таблицы 4.11 следует, что наибольшей надежностью рельсовые цепи обладают на бесстыковом пути с клееболтовыми стыками в уравнительных пролетах. При этом предполагается, что своевременно производятся ремонты пути с очисткой щебня, заменой негодных деталей промежуточных скреплений.
Выводы
- Рельсовые цепи относятся к системам, для которых в течение заданного времени работы допускаются отказы и вызванные ими кратковременные перерывы в работе. Для системы этой группы большое значение имеет свойство готовности — способности находиться в процессе эксплуатации значительную долю времени в работоспособном и готовом к применению состоянию. Основным показателем надежности таких систем является — коэффициент готовности.
Наряду с коэффициентом готовности для отдельных блоков системы часто используют показатели надежности невосстанавливаемых (работающих до первого отказа) объектов: вероятность безотказной работы, интенсивность отказов, средняя наработка на отказ.
При этом методе структура объекта изображается в виде специальной логической схемы, характеризующей состояние (работоспособность или неработоспособность) объекта в зависимости от состояний отдельных элементов. - Изолирующий стык с точки зрения надежности изоляции можно рассматривать как систему, состоящую из нескольких неравнонадежных блоков, имеющих параллельные и последовательные цепи элементов. В работе для всех используемых изолирующих стыков (сборных, клееболтовых и с полимерными накладками) построены логические схемы и получены аналитические выражения для оценки их надежности в зависимости от надежности входящих в них элементов.
- Анализ эксплуатационных данных дорог России, Белоруссии и Казахстана показал, что срок службы (наработка) при уровне вероятности безотказной работы Р = 0.9 изолирующих стыков с объемлющими накладками составляет 30 -60 Мт, а стыков с изоляцией из пресскомпозиции и втулками- шайбами БелИИЖТа — 100-120 Мт наработка клееболтовых стыков при том же уровне вероятности безотказной работы составляет 160-220 Мт.
- Анализ надежности работы изолирующих стыков на ЗападноСибирской дороге показал, что отказы имеют плотность распределения вероятности, подчиняющуюся усеченному нормальному закону с параметрами распределения для сборных изолирующих стыков: математическое ожидание Тср = 100 Мт и среднее квадратическое отклонение сг, — 30 Мт, для клееболтовых стыков : Тср = 250 Мт и сг, = 82 Мт.
Наработка тоннажа для уровня надежности Р = 0.95 составила для сборных стыков 50.5 Мт, а для клееболтовых 115 Мт. Малый срок службы клееболтовых стыков объясняется низким качеством их изготовления. - Для поддерживания работоспособности изолирующих стыков за ними должен быть установлен постоянный надзор. Под изолирующими стыками должны быть здоровые, хорошо подбитые шпалы. В районе изолирующих стыков путь должен быть закреплен от угона по установленным нормам. При соблюдении этих условий периодичность переборки или замены изолирующих стыков, исходя из их надежности, следует производить в соответствии с таблицей 4.5. Для этого на каждом перегоне необходимо иметь запас рельсов с клееболтовыми стыками, количество которых можно определить по таблице 4.6.
- Анализ отказов подрельсового основания показал, что минимальное сопротивление шпал и балласта может быть значительно ниже нормативной величины 1.0 Ом-км и составляет 0.2-0.3 Ом-км. В результате рельсовые цепи, особенно сигнальной частоты 50 и 75 Гц, периодически работают неустойчиво и требуют непрерывной регулировки. Для поддержания надежности рельсовых цепей на путях 1-3 классов через 14-16 лет нужно менять 20-30 % негодных деревянных шпал и делать очистку щебеночного слоя.
Опыт эксплуатации участков пути с железобетонными шпалами и скреплением КБ показал, что после пропуска по участку 250-400 Мт грузй происходит отказ 20-30 % электроизолирующих деталей. Удельное сопротивление подрельсового основания снижается до 0.2 — 0.25 Ом-км, что ведет к отказу рельсовых цепей. Для поддержания их надежности необходимо произвести средний или подгоночный ремонт пути с заменой негодных элементов.
Анализ статистических данных дорог показал, что причинами нарушения нормального функционирования токопроводящих стыков является: повышение переходного сопротивления стыка свыше 0.75-10″4 Ом; обрыв стыкового соединителя; неисправность соединителя (плохой контакт в манжете, обрыв более 30 % проволок). Для быстрого восстановления соединителей нужно иметь в запасе пружины или штепсельные (обводные на конических болтах) рельсовые соединители. - Подавляющее большинство отказов рельсовых цепей происходит вследствие повышенного затухания тока, которое может быть вызвано обрывом соединителя или повышением сопротивления стыка, уменьшением сопротивления до короткого замыкания в подрельсовом основании или изолирующем стыке.
Расчеты показали, что наибольшей надежностью рельсовые цепи обладают на бесстыковом пути с клееболтовыми стыками в уравнительных пролетах. При этом предполагалось, что своевременно производятся ремонт пути с очисткой щебня и заменой негодных деталей промежуточных скреплений.
ЗАКЛЮЧЕНИЕ
Работа посвящена актуальной проблеме создания инженерных методов оценки и прогнозирования надежности верхнего строения пути на станциях на основе комплексного изучения процессов формирования их отказов, разработке технических и технологических решении для повышения надежности и совершенствования системы ведения путевого хозяйства.
В работе сформулированы показатели надежности стрелочных переводов, рельсовых цепей и их элементов, разработана математическая модель их функционирования в различных условиях эксплуатации. Установлено, что качество функционирования стрелочных переводов в наибольшей мере зависит от последствий отказов с позиций обеспечения безопасности движения поездов и, в первую очередь, — внезапных, так как постепенные могут быть устранены в плановом порядке. Наибольшего внимания требуют такие события, как появление трещин и изломов несущих и направляющих элементов переводов, деталей скреплений, рабочих и контрольных тяг. Вместе с тем постепенные отказы в виде выхода параметров рельсовой колеи за допустимые пределы, ослабления креплений деталей часто нарушают нормальную работу переводов и снижают уровень безопасности поездов.
Производство усиленных скреплений, в том числе с упругими прикре- пителями, позволяет снизить затраты на текущее содержание стрелочных переводов на 25-30 %.
На основании анализа выполненных работ установлено, что
Не менее 65 % основных элементов стрелки и до 60 % элементов кре- стовинных узлов получают отказы из-за недостатков конструкции, недостатков технологии изготовления и недостаточной прочности металла.
Причины отказов элементов соединительных путей стрелочных переводов аналогичны причинам отказов элементов перегонных путей, работающих в близких условиях.
Конструкции скреплений, широко применяющихся в настоящее время на типовых стрелочных переводах, не полностью отвечают требованиям эксплуатации и нуждаются в значительном усовершенствовании.
Основным направлением повышения эксплуатационных качеств стрелок стрелочных переводов, исходя из особенностей их работы в настоящее время, следует считать расширение производства стрелок с гибкими и удлиненными гибкими остряками, применение в конструкции стрелок упругих скреплений, башмаков и подкладок с приварными подушками и высоким^ ребордами, контррельсов-протекторов, внешних замыкателей. В результате наблюдений за работой 270 крестовин типа Р65марки 1/11 на ЗападноСибирской железной дороге установлена зависимость срока их службы от осевой нагрузки, технологии изготовления и способов упрочнения. В работе даны рекомендации по срокам службы стрелок и крестовин для условий Западно-Сибирской железной дороги.
Исследованы основные факторы повышения надежности крестовин, даны рекомендации по продлению срока их службы за счет ремонта наплавкой и науглероживанием.
В результате проведенных эксплуатационных наблюдений определено фактическое состояние стрелочных переводов в горизонтальной плоскости (по шаблону, ординатам переводных кривых и направлению рельсовых нитей в плане).
Одними из основных параметров, контролируемых на стрелочном переводе, как и в пути, является ширина колеи. Но в отличие от перегонной конструкции верхнего строения пути здесь более строго регламентированы места измерений, порой расположенные очень близко друг от друга. Это касается каждого из направлений на стрелочном переводе. Учитывая опыт эксплуатации, МПС РФ время от времени меняет допуски на содержание стрелочных переводов. Эти допуски проанализированы в работе.
Для изучения соответствия фактического состояния стрелочных переводов по ширине колеи были проведены эксплуатационные наблюдения на 59 стрелочных переводах Р65 марки 1/11 колеи 1520 мм. Наблюдения показали, что в реальных условиях наблюдается весьма существенный разброс значений ширины колеи на переводах, повсеместно превышающий установленные пределы.
В целом нормативным требованиям ширины колеи в пределах стрелочного перевода, оцененные по нормам Инструкции ЦП/774, в 1.8 раз отвечают чаще по сравнению с требованиями Инструкции ЦП/2913. Разброс по отдельным сечениям стрелочного перевода, как в первом, так и во втором случае велик и достигает 4-5 раз.
В работе представлены методы прогнозирования расстройств рельсовой колеи и вероятностная модель накопления расстройств ширины колеи в характерных сечениях стрелочных переводов. Выполненные расчеты показывают, что установленные Инструкцией ЦП/ 2913 плюсовые допуски по ширине колеи во всех исследованных сечениях лежат в зоне приработочных отказов. Интенсивность расстройств колеи по шаблону в этот период значительнее, поэтому «удержать» колею в этих пределах очень трудно. Установив рациональные допуски согласно Инструкции ЦП/774 при безусловном обеспечении безопасности движения поездов можно избежать частых пере- щивок колеи и добиться продления сроков службы переводных брусьев.
За последние годы в путевом хозяйстве внедрены новые технологии укладки стрелочных переводов на железобетонных брусьях блоками как с помощью как путеукладочных, так и восстановительных кранов ЕДК — 300/5 и ЕДК — 500/80. В работе детально проанализирована возможность применения этих кранов в различных условиях эксплуатации и предложена технология укладки стрелочных переводов блоками укладочными кранами УК-25/9- 18 и комплексами КСП на электрифицированном участке под напряжением и без него.
Стрелочный перевод на железобетонных брусьях собирает на базе дистанции пути с применением козлового крана специализированная бригада из 6 монтеров пути.
Сравнительные испытания машины «Унимат» и ВПРС-03 на выправке стрелочных переводов выявили возможность исключения ручного труда (как минимум пятерых рабочих), возможность выправки стрелочного перевода за 1 — 1.5 часа с удовлетворительным качеством.
Изменившиеся условия эксплуатации стрелочных переводов вызывают интенсивный износ их элементов. Для оценки интенсивности износа остряков, рамных рельсов, крестовин и рельсов переводной кривой были проведены измерения их износа на стрелочных переводах типа Р65 марки 1/11 и 1/9. По результатам наблюдений построены эмпирические зависимости вертикального и бокового износа элементов стрелочных переводов в функции пропущенного тоннажа и осевых нагрузок подвижного состава. Эти зависимости позволяют прогнозировать срок службы элементов стрелочных переводов по износу.
Одной из основных причин увеличившейся интенсивности износа элементов стрелочных переводов является отсутствие смазки, которая ранее осуществлялась из букс с подшипниками скольжения.
На основании анализа полученных результатов наблюдений установлено, что 74 % крестовин и 53 % остряков отказывают по причине достижения предельного износа, 17 % крестовин отказывают из-за выкрашиваний сердечника и усовиков в зоне перекатывания колес.
Рекомендуемые нормативные сроки службы элементов стрелок и крестовин установлены на основе оценки их надежности для прямых участков пути и приведены в таблице 2.6 для участков со скоростями движения поездов 80 км/ч по прямому направлению, со средней статической осевой нагрузкой подвижного состава 150 кН при соотношении грузопотоков по прямому и боковому направлениям стрелочных переводов 75 и 25 %.
На сети дорог интенсивно укладывают стрелочные переводы типа Р65 марки 1/11, проекта 2750, на железобетонном подрельсовом основании, н,а Западно-Сибирской дороге начиная с 1998 г. эксплуатируется свыше 250 таких переводов.
Более жесткое подрельсовое основание с железобетонными брусьями в сочетании с суровыми климатическими условиями снижает стойкость сборных крестовин. Причины отказа — вертикальный износ и выкрашивание поверхности катания сердечника и усовиков. Глубина выкрашивания достигает 5 мм, наибольший износ составляет 8 мм и более.
Средний срок службы таких крестовин составляет 53 млн. т брутто наработанного тоннажа, в то время как стрелочные крестовины на деревянных брусьях пропускают до изъятия 100 млн. т груза и более.
Для снижения жесткости подрельсового основания предусмотрены ди- намико-прочностные испытания резиновых прокладок повышенной упругости. В переводах проекта 2750 намечено использовать крестовины с непрерывной поверхностью катания, существенно снижающие динамическое воздействие на путь.
Учитывая особенности движения поездов в пределах крупных узлов и специализированных парков (ограниченные скорости движения, интенсивное движение по боковому направлению переводов), необходимо усовершенствовать конструкцию стрелочных переводов применительно к этим условиям. При движении поездов преимущественно по боковому направлению быстро прогрессирует боковой износ элементов на упорной нити. Поэтому важно усилить, укрыть и защитить криволинейные остряки, усилить передние вылеты рамных рельсов, а также повысить стабильность колеи за счет применения более надежных промежуточных скреплений.
Исключительно важное значение для безопасности и бесперебойности движения поездов имеют рельсовые цепи. Рельсовая цепь включает в себя довольно разнородные элементы: рельсы, токопроводящие рельсовые стыки, изолирующие стыки и подрельсовое основание, которые обладают различными электроизоляционными свойствами.
Рельсовые цепи относятся к системам, для которых в течение заданного времени работы допускаются отказы и вызнанные ими кратковременные перерывы в работе. Для систем этой группы большое значение имеет свойство готовности-способности находиться в процессе эксплуатации значительную долю времени в работоспособном и готовом к применению состоянии. Основным показателем надежности таких систем является коэффициент готовности.
Наряду с коэффициентом готовности, для отдельных блоков системы часто используют показатели надежности невосстанавливаемых (работающих до первого отказа) объектов: вероятность безотказной работы, интенсивности отказов, средняя наработка на отказ.
При этом методе структура объекта изображается в виде специальной логической схемы, характеризующей состояние (работоспособное или неработоспособное) объекта в зависимости от состояний отдельных элементов.
Понижение сопротивления изоляции и утечка тока в рельсовой цепи происходит из-за гниения деревянных шпал, загрязнения и увлажнения балластной призмы, нарушения электроизоляционных элементов промежуточных скреплений на железобетонных шпалах.
Наблюдения за работой рельсовых цепей на сети железных дорог показывают, что свыше 30-50 % отказов устройств сигнализации, централизации и блокировки приходится на рельсовые цепи.
Наибольшее число отказов рельсовых цепей происходит в период большого перепада температур из-за выдавливания торцовой изоляции, нарушения изоляции болтов в изолирующих стыках.
Изолирующий стык с точки зрения надежности изоляции можно рассматривать как систему, состоящую из нескольких неравнонадежных блоков, имеющих параллельные и последовательные цепи элементов. В работе для всех используемых изолирующих стыков (сборных, клееболтовых с полимерным накладками) построены логические схемы и получены аналитические выражения для оценки их надежности в зависимости от надежности входящих в не элементов.
Анализ надежности работы изолирующих стыков показал, что отказы имеют плотность распределения вероятности, подчиняющуюся усеченному нормальному закону с параметрами распределения для сборных изолирующих стыков; математическое ожидание Тср, = 100 Мт и среднее квадратиче- ское отклонение сг, = 30 Мт; для клееболтовых стыков: Тср = 250 Мт и сг, = 82 Мт.
Наработка тоннажа для уровня надежности Р — 0.95 составила для сборных стыков 50.5 Мт, а для клееболтовых 115 Мт. Малый срок службы клееболтовых стыков объясняется низким качеством их изготовления.
Для поддержания работоспособности изолирующих стыков за ними должен быть установлен постоянный надзор. Под изолирующими стыками должны быть здоровые, хорошо подбитые шпалы. В районе изолирующих стыков путь должен быть закреплен от угона по установленным нормам. При соблюдении этих условий периодичность переборки или замены изолирующих стыков, исходя из их надежности, следует производить в соответствии с таблицей4.5. Для этого на каждом перегоне необходимо иметь запас рельсов с клееболтовыми стыками, количество которых можно определить по таблице 4.6.
При текущем содержании бесстыкового пути в зоне изолирующих стыков (по 50 м с обеих сторон) необходимо через каждые 15-20 млн. т брутто прошедшего по пути груза, но не реже 1 раза в год, сплошь подтягивать гайки клеммных и закладных болтов, а стыках выправлять просадки и подбивать стыковые и пред стыковые шпалы.
При осмотрах изоляции железобетонных шпал обращают внимание на отсутствие касания клеммы и закладного болта (зазор между ними должен быть не менее 10 мм), механическое разрушение резиновой прокладки и ее смещение более чем на 10 мм, разрушение изолирующих втулок, ослабление клемм и закладных болтов, загрязнение пространства между закладными болтами и клеммами.
Отказы стыковых соединителей приварного типа происходят в основном из-за их обрыва в месте приварки к рельсу вследствие нарушения технологии приварки или ненадежного контакта между тросом и наконечником, а также из-за повреждений при путевых работах.
Основным недостатком штепсельных соединителей является нестабильное сопротивление в контактной паре штепсель-рельс. Это сопротивление зависит от состояния контактирующих поверхностей и плотности контакта.
Анализ статистических данных дорог показал, что причинами нарушения нормального функционирования токопроводящих стыков является повышение переходного сопротивления стыка свыше 0.25-10″4 Ом; обрыв стыкового соединителя; неисправность соединителя (плохой контакт в монтаже, обрыв более 30 % проволок).
Для быстрого восстановления соединителей нужно иметь в запасе пружинные или штепсельные (обводные на конических болтах) рельсовые соединители.
Анализ отказов подрельсового основания показал, что минимальное сопротивление шпал и балласта может быть значительно ниже нормативной величины 1.0 Ом км и достигает 0.2-0.3 Ом км.
В результате рельсовые цепи, особенно сигнальной частоты 50 Гц, периодически работают неустойчиво и требуют непрерывной регулировки.
Для поддержания надежности рельсовых пеней на путях 1-3 классов через 14-16 лет нужно менять 20-30 % негодных деревянных шпал и делать очистку щебеночного слоя.
Опыт эксплуатации участков пути с железобетонными шпалами и скреплением КБ-65 показал, что после пропуска по участку 350-400 Мт груза происходит отказ 20-30 % электроизолирующих деталей. Удельное сопротивление подрельсового основания снижается до 0.2-0.25 Ом -км^ что ведет к отказу рельсовых цепей. Для поддержания их надежности необходимо произвести ремонт пути с заменой негодных элементов.
Для повышения надежности рельсовых цепей необходимо отказаться от стыков с объемлющими накладками и переходить на сборные и клее- болтовые с полнопрофильными накладками или на изолирующие стыки с полимерными накладками фирмы «АПАТЕК». Последние допускают применение их в бесстыковом пути без уравнительных пролетов, имеют сопротивление разрыву 2.5 МН и гарантийный срок службы 300 млн. т брутто.
Главным фактором, влияющим на скапливание металлических частиц и образования в зоне изолирующих стыков так называемых шунтовых мостиков, приводящих к ложной занятости рельсовых цепей, является высокая намагниченность рельсов в этих зонах. В качестве радикальной меры предлагается создание размагничивающих установок в рельсосварочных поездах, а в качестве временной меры — проведение осмотра изолирующих стыков и удаление металлической пыли с торцовых прокладок.
Список используемой литературы
- Дружинин Г.В. Надежность автоматизированных систем. — М.: Энергия, 1977.-536 с.
- Абусеридзе З.В. О работе рельсовых цепей и электроприводов // Путь и путевое хозяйство. — 2000, № 10. — С. 32-36.
- Путь и безопасность движения поездов / В.И. Болотин, В.А. Лаптев, B.C. Лысюк, В.Я. Шульга. — М.: Транспорт, 1994. — 199 с.
- Старосельский A.A. Электрическое сопротивление балласта // Путь и путевое хозяйство. — 1979, № 10. — С. 15.
- Радыгин Ю.Н. Крестовины, упрочненные методом науглероживания // Путь и путевое хозяйство. — 1994, № 2. — С. 6-11.
- Инструкция по текущему содержанию железнодорожного пути ЦП/774 / МПС РФ. — М: Транспорт, 2001. — 224 с.
- Самарина A.A. Механизированная укладка стрелочных переводов на железобетонных брусьях // Путь и путевое хозяйство. — 1997, № 5. — С. 13-17.
- Перникс Б.Д., Ягудин Р.Ш. Предупреждение и устранение неисправностей в устройствах СЦБ. — М.: Транспорт, 1984. — 224 с.
- Омаров А.Ж., Имандосона М.Б., Ескенов E.H. Защита рельсовых цепей от посторонних источников тока // Проектирование, строительство и эксплуатация транспортно-коммуникационных сооружений / Межвуз. сб. науч. тр. Вып. 4, КазАТК, 1999. — С. 69-71.
- Омаров А.Ж., Имандосова М.Б., Ескенов E.H. Влияние асимметрии тягового тока на работу рельсовых цепей // Проектирование, строительство и эксплуатация транспортно-коммуникационных сооружений. / Межвуз. сб. науч. тр. Вып. 4, КазАТК, 1999. — С. 67-69.
- Кравцов Ю.А., Степенский Б.М. Повышение надежности работы станционных фазочувствительных рельсовых цепей // Автоматика, телемеханика и связь. — 1990, № 6. — С. 5-7.
- Альбрехт В.Г., Золотарский А.Ф. Современные конструкции верхнего строения железнодорожного пути. — М.: Транспорт, 1975. — 276с.
- Дмитренко И.Е. Техническая диагностика и автоконтроль в железнодорожных системах автоматики и телемеханики. — М.: Транспорт, 1976. — 95 с.
- Баташов С.А., Султангазинов С.К., Имандосова М.Б. Анализ факторов надежности устройств СЦБ // Проектирование, строительство и эксплуатация транспортно-коммуникационных сооружений / Межвуз. сб. науч. тр. Вып. 4, КазАТК, 1999. — С. 21-23.
- Куммер П.И., Ковалев А.Г., Коптева Т.В., Аветикян Г.А. Железнодорожная автоматика за рубежом. — М.: Транспорт, 1985. — С.189.
- Айзенман И., Лейкауф Г. Испытания изолирующих стыков // Железные дороги мира. — 1989, № 6. — С. 61-65.
- R.K. Steeie, D.H. Stone. Developments in Railroad Rail Bulletin of the American Railway Engineering Association, 1986, v. 87, № 707.
- Rail technology. Where do we stand ? // Railway Track and Structures. 1991, №11.
- Абражей Э.И. Конструкции и надежность изолирующих стыков. БелИИЖТ. — Гомель, 1977. — 28 с.
- Абражей Э.И, Матвецов В.И. Изолирующие стыки повышенной надежности // Вестник ВНИИЖТа. — 1989, № 1. — С. 48-50.
- Воробьев Э.В., Ковалев И.Ф. и др. Опытные накладки для изолирующих стыков // Путь и путевое хозяйство. — 1989, № 8. — С. 36-37.
- Рубенчик С.А., Донских В.И. Клееболтовой изолирующий стык для бесстыкового пути.-М.: Транспорт, 1984. — С. 77-79.
- Аксенов В.Ф., Донских В.И., Рубенчик С.А. Изолирующие стыки рельсов // Тр. ВНИИЖТа, Вып.616. — С . 104-119.
- Меньшиков Н.Я., Королев А.И., Ягудин Р.Ш. Надежность железнодорожных систем автоматики и телемеханики. — М.: Транспорт, 1976, — 212 с.
- Вопросы повышения надежности и эффективности систем железнодорожной автоматики и телемеханики // Сб. научн. тр., Вып.75, Свердловск, 1985.- 144 с.
- Аркатов B.C., Котляренко Н.Ф., Баженов Л.И., Лебедева Т.Л. Рельсовые цепи магистральных железных дорог. Справочник. — М.: Транспорт, 1982.-360 с.
- Матвеев В.Г. Содержание пути на участках автоблокировки и электротяги. — М.: Транспорт, 1986. — 280 с.
- Котляренко Н.Ф. Рельсовые цепи. — М.: Трансжелдориздат, 1961. —
328 с. - Котельников A.B. и др. Рельсовые цепи в условиях влияния заземляющих устройств. — М.: Транспорт, 1990. — 24 с.