Сейчас ваша корзина пуста!
Разработка состава композитных растворов с заменой цемента золой от сжигания шпал
Цикл статей:
Глава 1 — Разработка технологии композитных цементно — бентонитовых систем с добавкой золы от сжигания шпал и применение их при строительстве и эксплуатации объектов инфраструктуры железнодорожного транспорта
Глава 2 — Исходные материалы и методы исследования
Глава 3 — Разработка состава композитных растворов с заменой цемента золой от сжигания шпал
Глава 4 — Экологическая безопасность композитного раствора содержащего золу Глава 5 — Эколого-экономическое обоснование использования золы в производстве композитных растворов
Выбор композитных растворов применительно к инженерно- геологическим условиям основывается на оценке их реологических и технологических свойств. Исследование структурообразования в композитных растворах содержащих золу проводили путем замены цемента различными количествами золы во времени. Выделяли два временных промежутка. В первом находили, временя отверждения растворов, то есть до перехода его в твердое состояние путем измерения прочности. Второй временной промежуток соответствовал исследованию нарастания прочности при длительном хранении в течение 28 суток.
Исследование структурообразования композитных растворов
содержащих золу в процессе отверждения
Влияние добавок золы на изменение реологических свойств цементно — бентонитовых растворов в процессе хранения изучали при водоцементном соотношении 2:1 в присутствии 5% жидкого стекла. При этом заменяли цемент золой, количество которой варьировали от 2 до 50%.
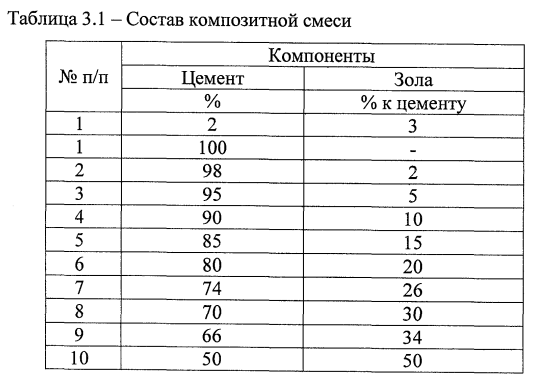
Для этого в предварительно замоченную 5%-ную суспензию бентонита вводили золу, после чего при перемешивании вносили рассчитанное количество цемента и жидкое стекло.
На рис. 3.1 приведены микрофотографии блочного строения монтмориллонита с плотными включениями золы, которые имеют более контрастный вид.
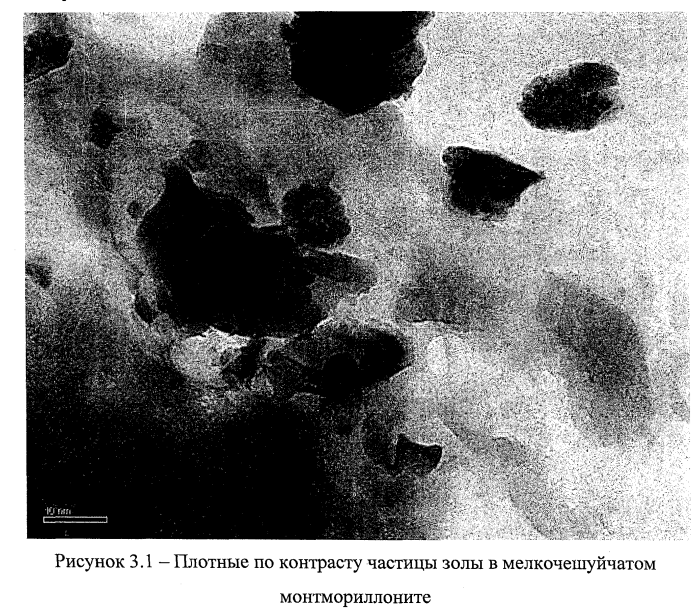
Прочность образцов в течение двух часов от начала приготовления измеряли на пластометре Ребиндера с конусом 90 градусов (табл. 3.2). В полученных растворах определяли прочность во времени на приборе Ребиндера. Полученные данные приведены в табл. 3.2 и на рис. 3.2.
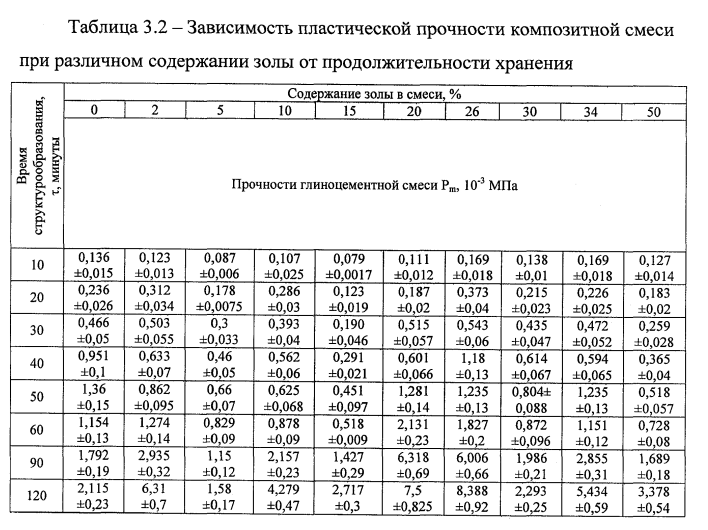
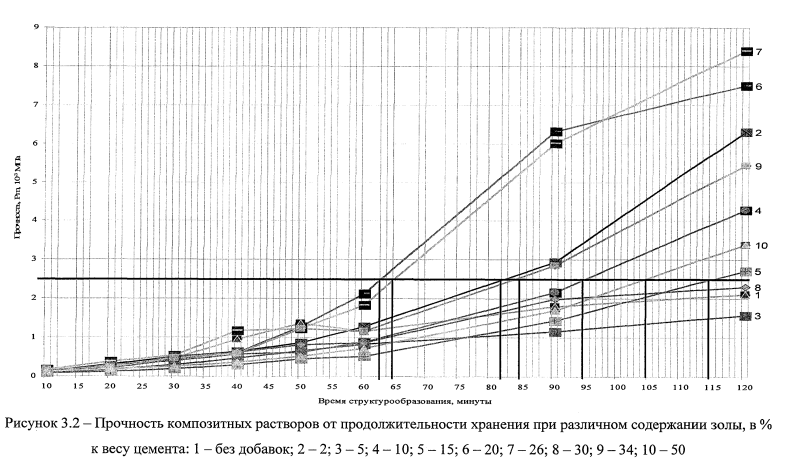
На рис. 3.2 показана начальная стадия структурообразования композитного раствора при различном содержании золы. С увеличением концентрации ингредиента прочность раствора во времени уменьшается. Время достижения потери текучести раствора при добавлении золы увеличивается.
Исследование структурообразования композитных растворов при
длительном хранении
Во всех образцах композитных растворов определяли прочность в течение 28 суток на приборе Ребиндера — Гороздовского и на гидравлическом прессе ИП-100 через 7, 14 и 28 суток (табл. 3.3, рис 3.3). По данным табл. 3.3 построены графики изменения прочности композитных растворов через 1,3,7, 9, 14 и 28 суток хранения (рис. 3.4 — 3.9).
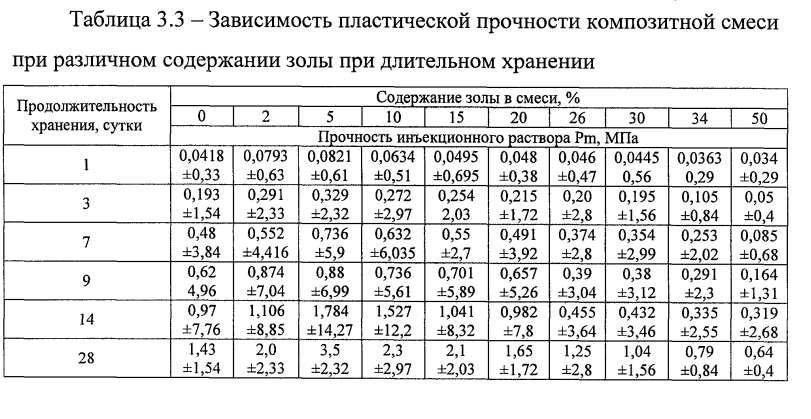
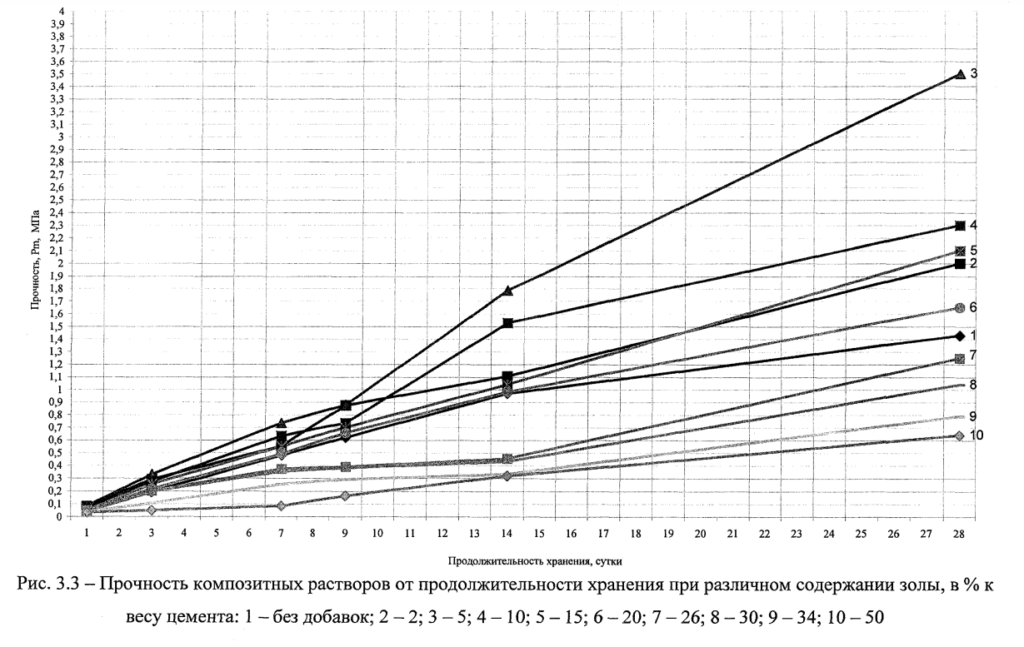
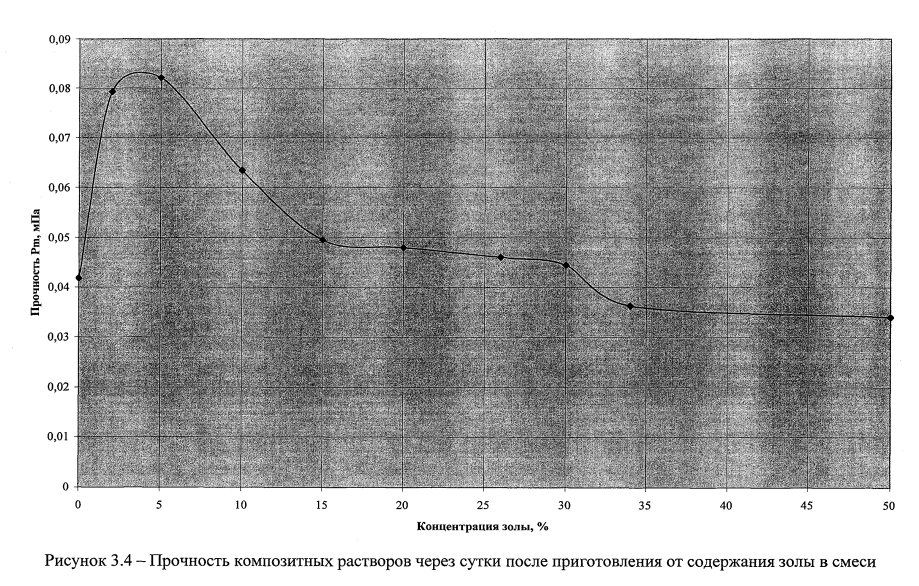
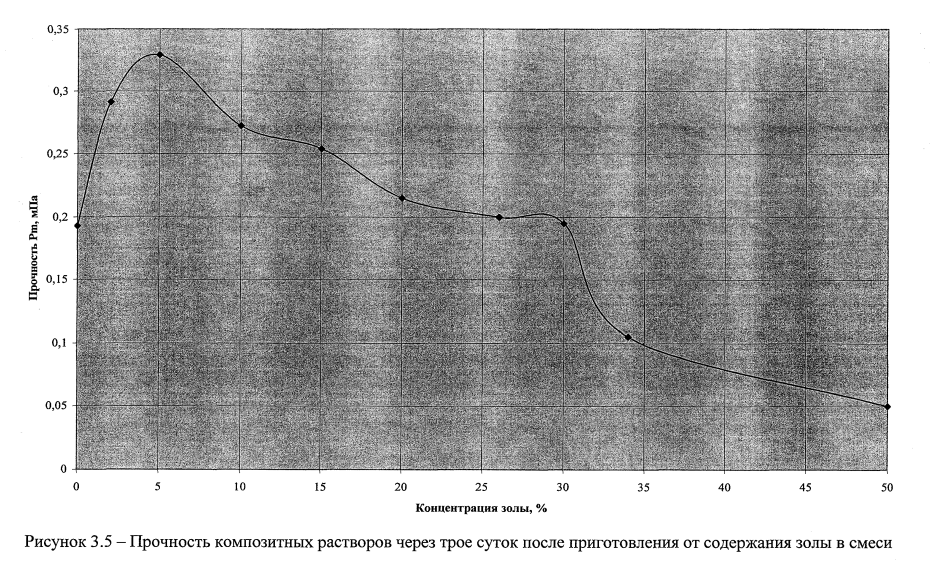
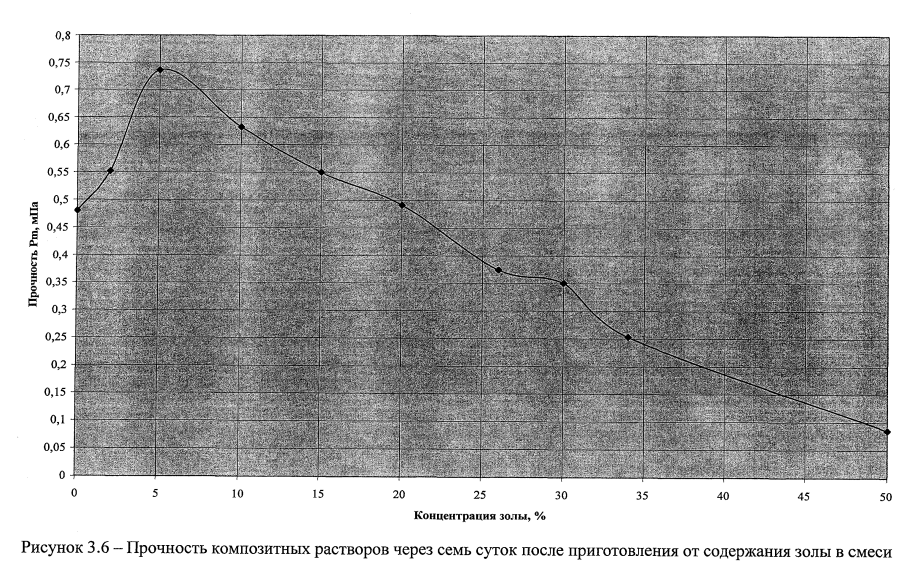
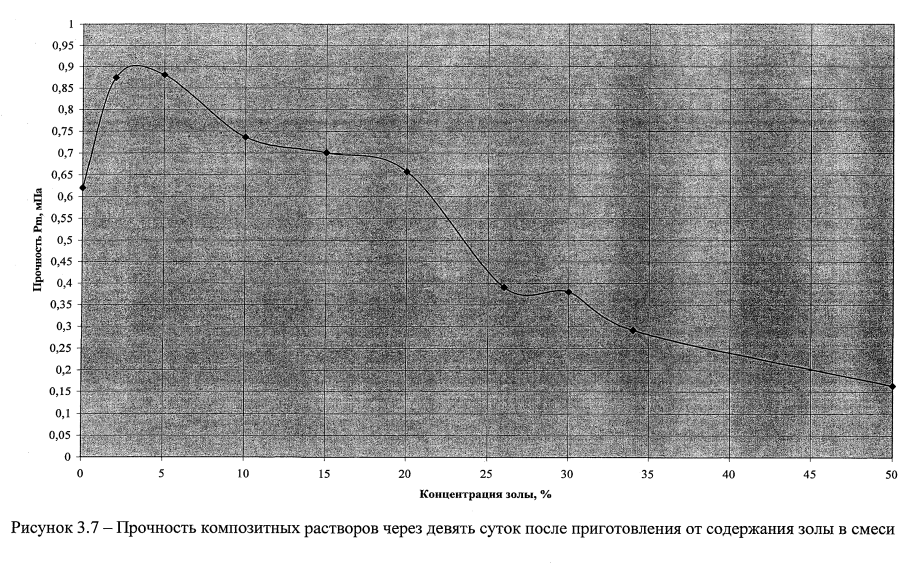
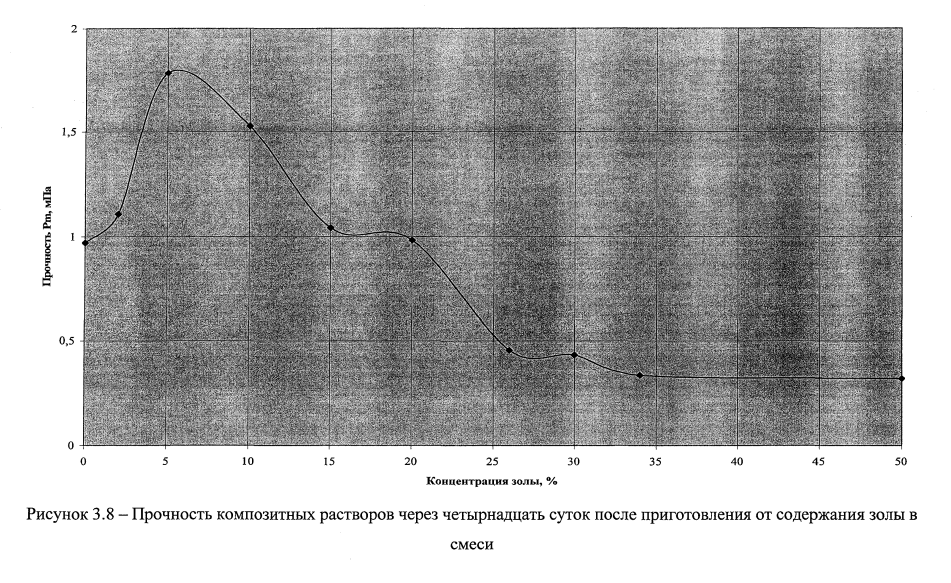
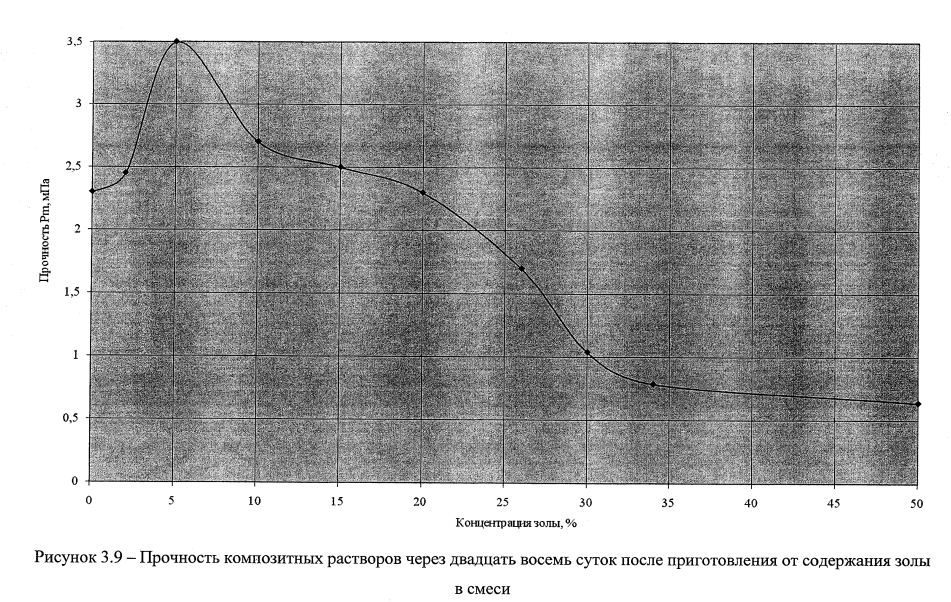
При замене цемента золой структурообразование отверженных композитных растворов в зависимости от содержания золы имеет различный характер. При этом прочность образцов уменьшается не линейно с увеличением содержания золы. В процессе хранения через 1, 3, 7, 9, 14 и 28 сутки после приготовления наблюдается аномальное увеличение прочности по отношении к контрольному образцу при 5% замены цемента золой примерно в два раза.
Водопоглощение цементо — бентонитовых композитных растворов без добавок золы и с 20 % замены цемента определяли через 28 сутки с помощью горизонтальных и вертикальных трубок Карстена. Полученные данные приведены в табл. 3.4 и на рис. 3.10 и 3.11
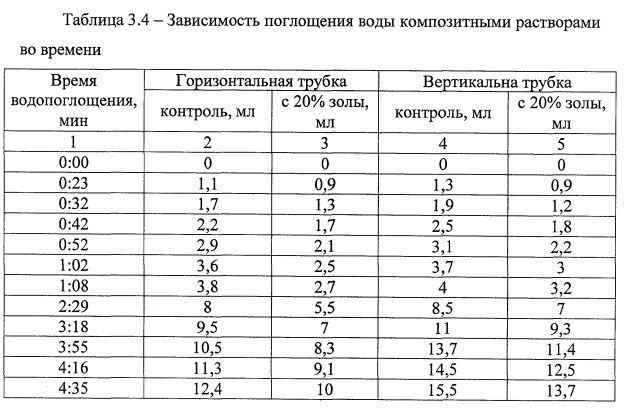
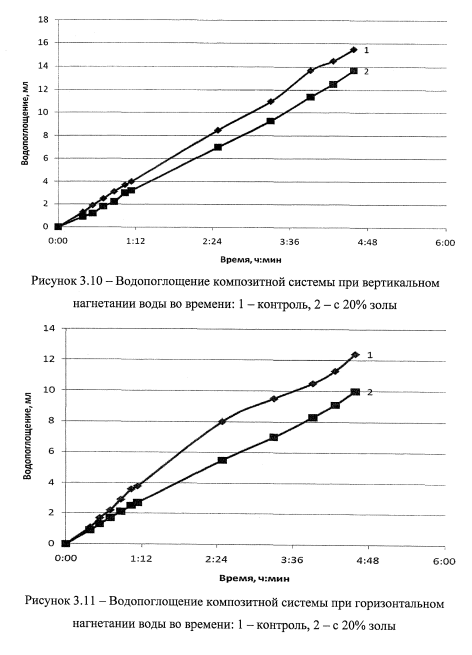
Водопоглощение в присутствии золы снижается по сравнению с контрольным образцом. При вертикальном нагнетании воды водопоглощение композитного раствора без добавок составляет 1,3 см/мин, а в присутствии золы — 1,1 см/мин, а при горизонтальном без добавок — 1,3 см/мин, а в присутствии золы — 0,9 см/мин, то есть в это случае снижается на 30%.
Исследование добавок золы на структуру композитной системы
С увеличением содержания золы сначала происходит рост прочности, а затем ее снижение. Прочность системы возрастает при замене 5% цемента золой на 50% по сравнению с контрольным образцом. Микрофотография контрольного образца и с заменой 5% замены цемента золой приведена на рис. 3.12 и 3.13. На рис. 3.12 видны большие пустоты и разрывы в структуре цементного камня, а при введении золы происходит их заполнение (рис. 3.13), что приводит к повышению прочности композитной системы.
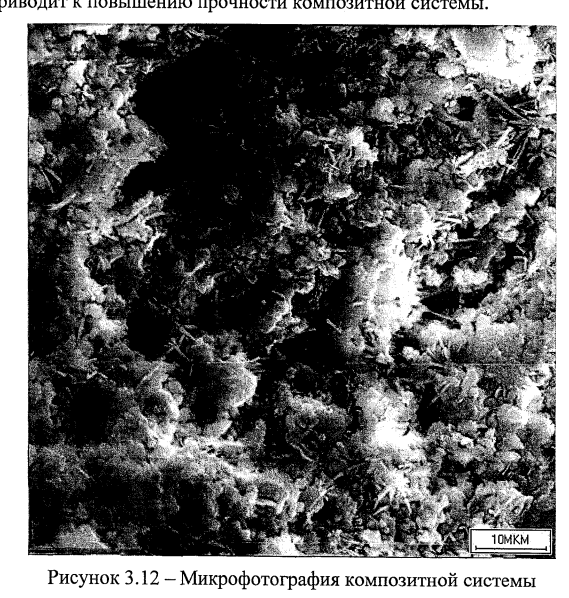
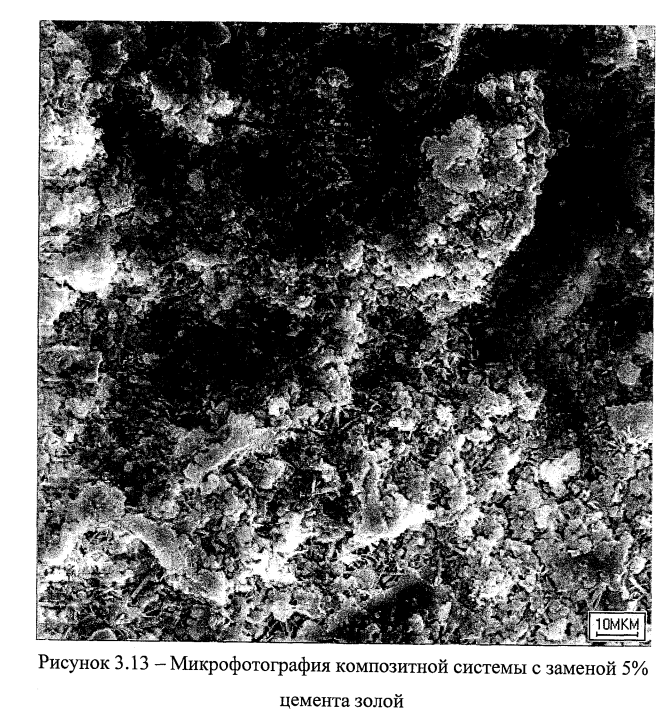
При замене 20% цемента золой прочность композитной системы снижается и достигает уровня контрольного образца. На рис. 3.14 приведена микрофотография в просвечивающем микроскопе с увеличением в 1380 раз композитной системы с заменой 20% цемента золой. Образец исследовался в растровом электронном микроскопе В8-301 (Чехия). На рис 3.14 выделены четыре элемента, в которых определен элементный состав. Рентгеновский спектр с выделенного участка (в виде квадрата) показан на рис. 3.14 а.
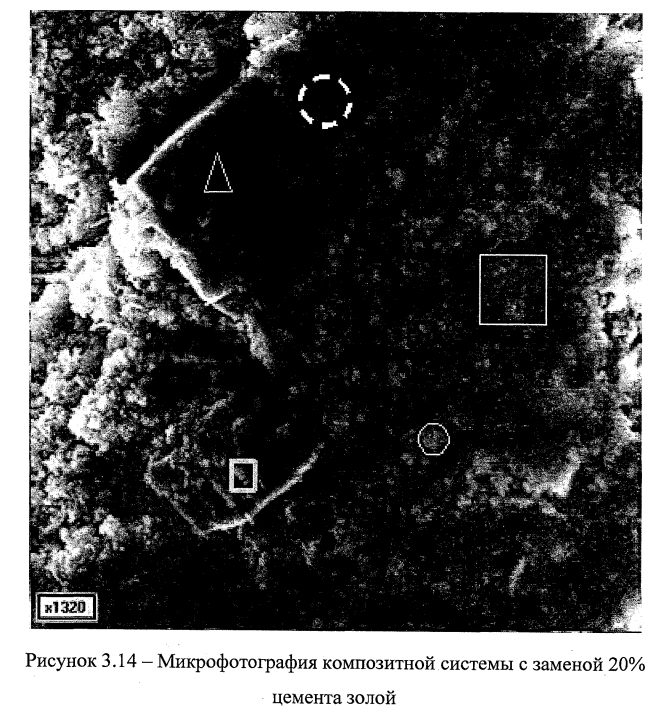
Композитная система представлена мелкими по размеру коагулянтами с включенными более крупными частицами. Квадратом выделен участок, где представлен небольшой агрегат мелких округлых частиц в просвечивающем микроскопе их размер представляет десятые и сотые доли мкм. В состав этих частичек входят масс. %: 7,65 оксида алюминия; 21,22 диоксида кремния, 2,88 оксида калия; 46,51 оксида кальция; 3,01 оксида марганца и 14,22 трехвалентного оксида железа. Таким образом, на этом участке находится состав обогащенный кальцием и диоксидом кремния.
Спектр с другого агрегата рис 3.14 б (в виде круга) по составу не отличается от первого участка, только лишь здесь изменяется соотношения элементов. Можно предположить, что эти коагулянты представляют собой агрегаты кристаллических образований цемента. В спектре с крупной частицы (в виде треугольника) наблюдается повышенное содержание окиси алюминия, содержание которого составляет 77,99 масс. %, то есть, эта частица представляет собой минерал корунд, в то время как наличие других элементов обусловлено прилипанием их на поверхность образца. Спектр с меньшей частицы, показанной на рис. 3.14 в виде утолщенных линий квадрата), (приведенный на рис 3.14 г) представляет собой породообразующий минерал — полевой шпат. Участок над квадратной частичкой (прерывистый круг) представлен более однородной массой слипшихся частиц, но его элементный состав характеризует золу (рис 3.14 д). Силикатную часть вместе с калием и частично с железом можно отнести к монтмориллониту (рис 3.14 а) кальций и серу — к сульфату кальция, а остальные элементы относятся к приместным элементам.
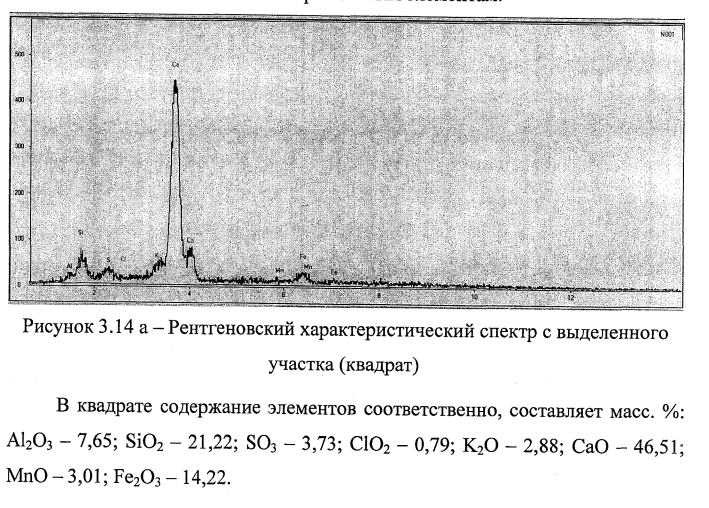
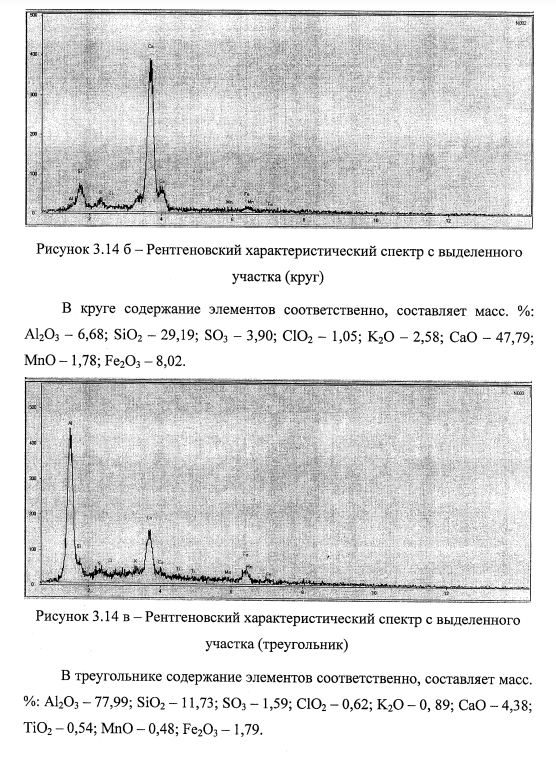
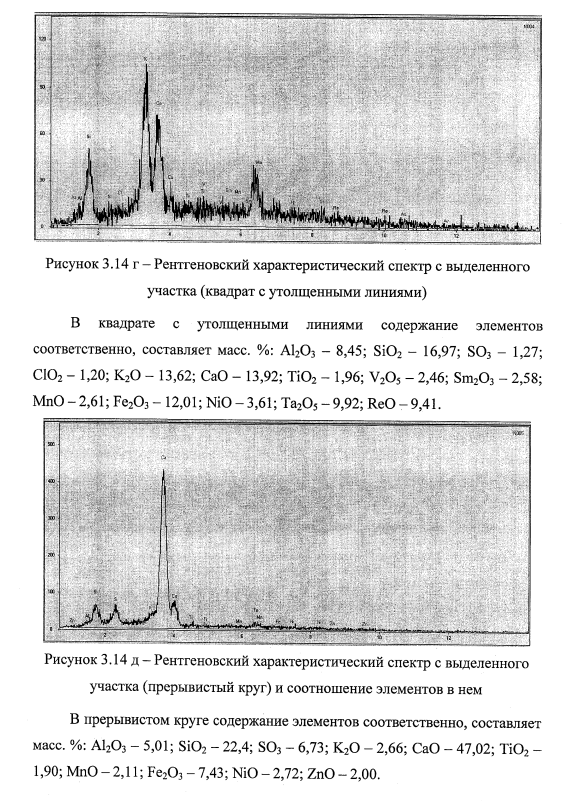
Общая картина композитного раствора содержащего золу приведена на рис 3.15. Жидкое стекло насыщено мелкими частичками (часть показана). С выбранного участка, показанного в виде квадрата, получен спектр (рис. 3.15 а), состав этого участка состоит в основном и кальция, железа и кремния, что позволяет отнести его к жидкому стеклу. Из рисунка видно, что стекло насыщено рядом мелких элементов. Обрамляется жидкое стекло крупными поликомпонентными частицами (кристаллами цементного камня и золы). С этого же участка получена микродифракционная картина (рис. 3.15 б), на которой отмечаются слабые отражения тонкодисперсного графита.
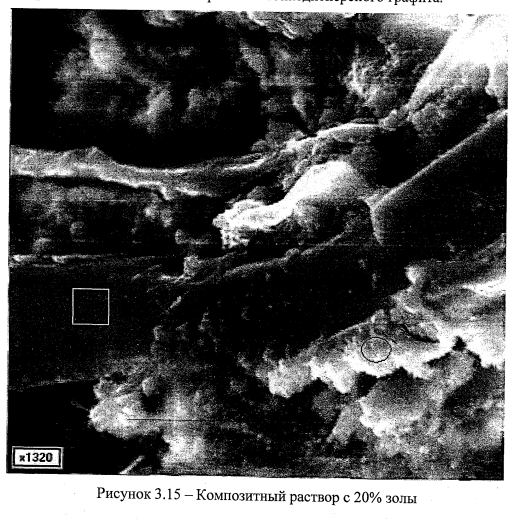
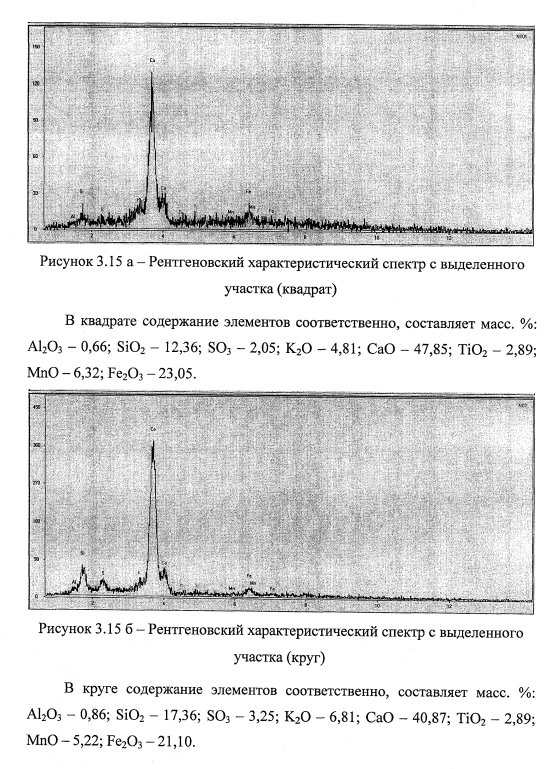
На рис 3.16 стрелкой показана частичка золы, несмотря на ее маленькие размеры это участок представляет собой агрегат частичек. С частички получен спектр, который приведен на рис 3.16 а. Пунктирными стрелками показаны пленочные обособления стекла, насыщенного разными элементами. Спектр, который получен с участка обозначенного квадратом, приведен на рис 3.16 б. Микродифракционная картина с пленки отвечает полуэлементному карбонату с сильным диффузным отражением 2,78А, по которому можно определить, что эта частичка относится к цементу.
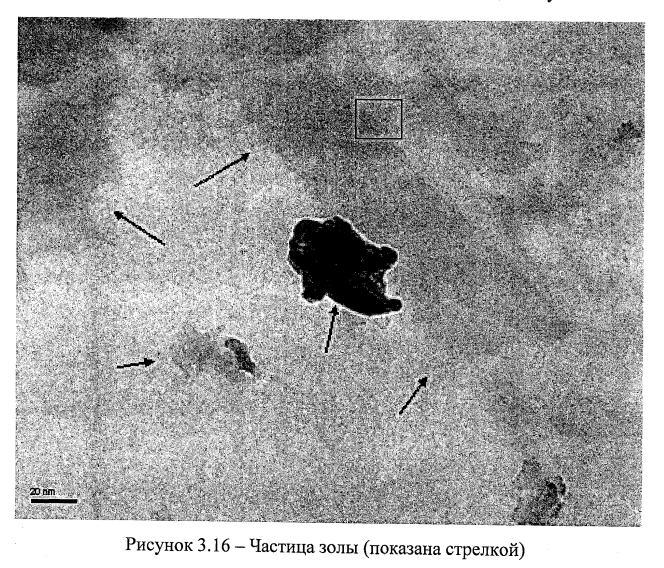
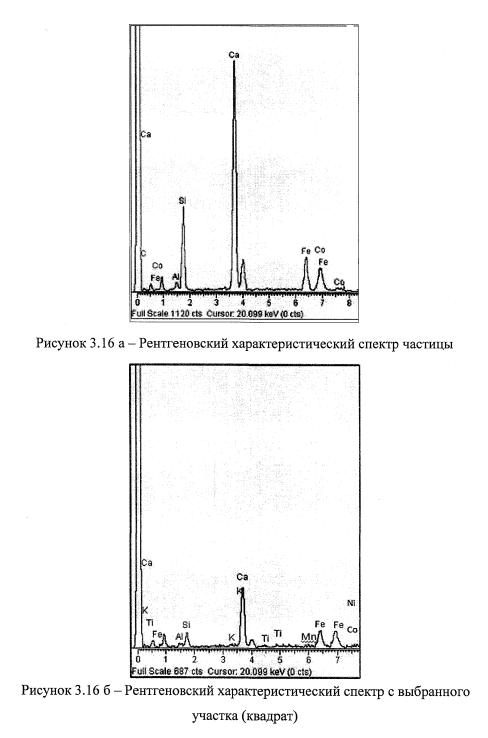
На рис 3.17 приведены крупные призмы цемента в среде частиц золы. С призм получен спектр рис 3.17 а, необходимо отметить, что призмы покрываются жидким стеклом и мелкими частицами золы. Это характерно для более крупных призматических образований, представляющих собой новую техногенную фазу, состоящую из кристаллов цементного образования и золы.
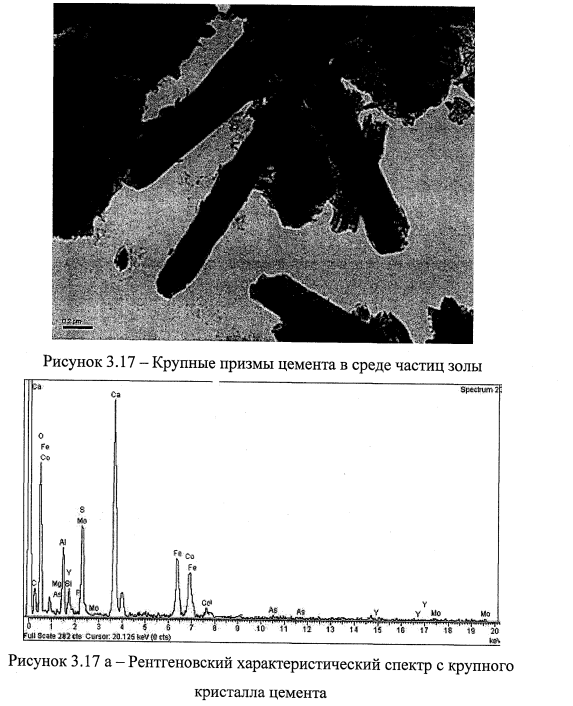
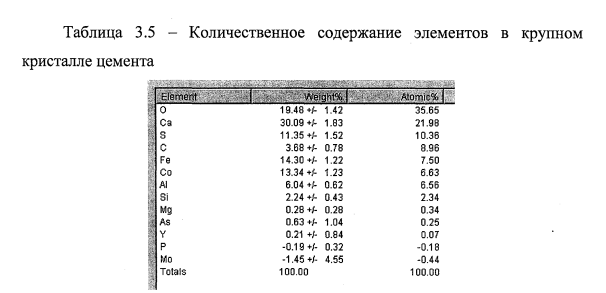
В зависимости от насыщенности жидкое стекло имеет разную плотность и конфигурацию (рис. 3.18). Здесь видна тончайшая островная пленка, и наиболее чистая (показана стрелками). Более плотная составляющая включает в себя крупные и мелкие частицы, и представляет собой конгломерат жидкого стекла и золы. Спектр с выбранного участка приведен нарис3.18а.
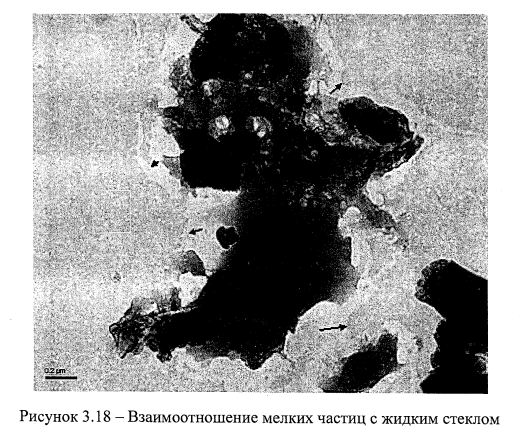

Приведенные микрофотографии композиционного раствора описывают общую картину взаимодействия золы, жидкого стекла, бентонита и минералов цемента.
На рис. 3.19 приведена микрофотография композитной системы в просвечивающем микроскопе при меньшем увеличении. Здесь минералы цемента образует округлые микроструктуры, в которых располагаются частички золы (показаны стрелками). Остальная масса вещества состоит из механической смеси цемента и частичек золы. Эти выделенные частички отличаются от остальных большим содержанием металлов. Повышенное количество кальция объясняется тем, что в зону возбуждения рентгеновского характеристического излучения попадает частичка цемента.
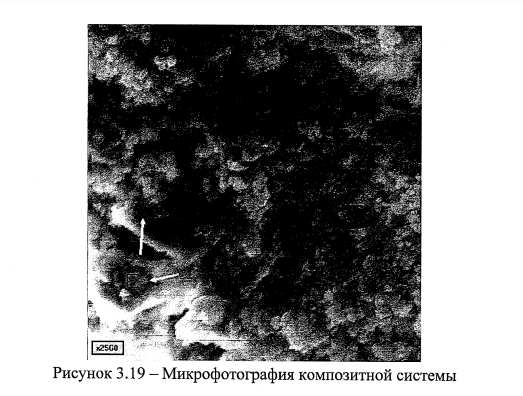
На рис. 3.20 приведено значительное скопление зольных частиц, которые приводят к нарушению однородности системы. С участка выделения (квадрат) получен спектр, в котором, как и в предыдущем случае присутствует значительное количество металлов по сравнению с матрицей (цементом). Спектр приведен на рис 3.20 а.
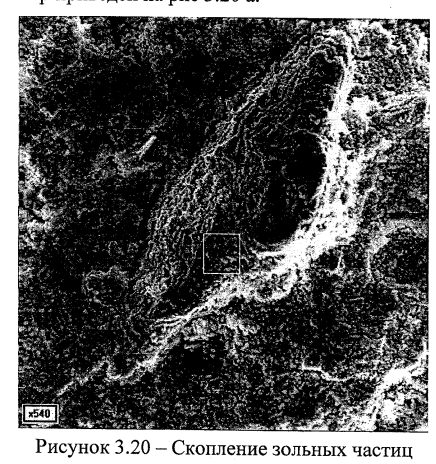
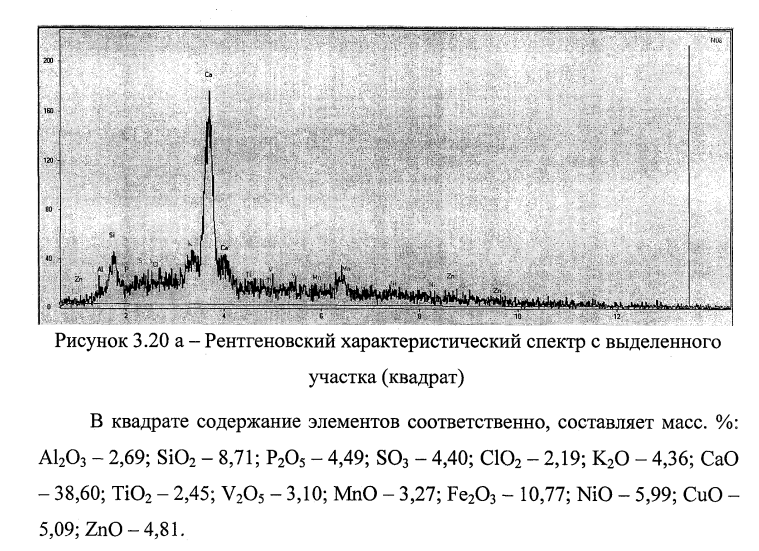
Пористость отвержденных композитных растворов без добавки и с 20% замены цемента золой определяли на основе изотерм адсорбции и десорбции бензола (табл. 3.6, 3.7 и рис. 3.21, 3.22) с использованием программного расчета по уравнению Дубинина — Радушкевича [157].
Для анализа микропористой структуры образцов использовали уравнения теории объемного заполнения микропор (ТОЗМ): Уравнение Дубинина — Радушкевича (ДР):

Уравнение (3.1) применимо для описания изотерм адсорбции в интервале малых и средних давлений (р/р8 от МО»4 до 0,3) на адсорбентах с однородной микропористой структурой и в полулогарифических координатах [lna~A2] имеет линейный вид. Для оценки размеров микропор, исходя из модели щелевидной микропоры с ограниченными боковыми стенками, использовано соотношение, устанавливающее связь между характеристической энергией адсорбции паров бензола в микропорах Е0 (выраженной в кДж/моль) и их полушириной х0 (выраженной в нм):
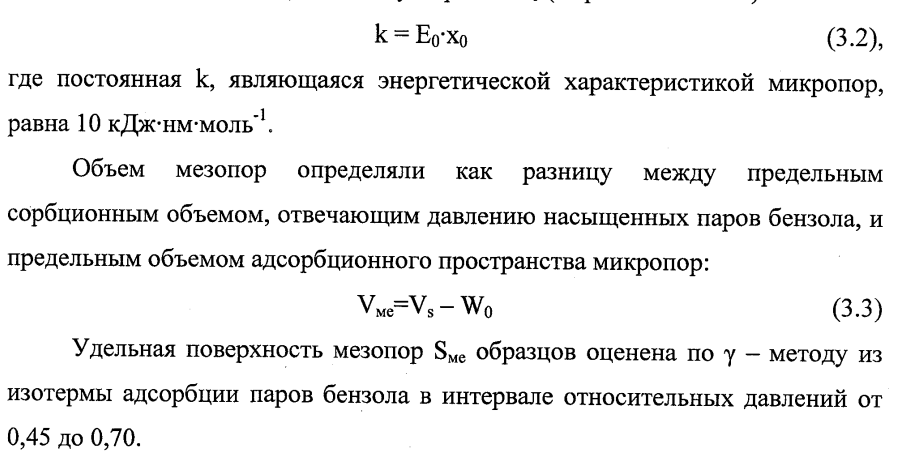
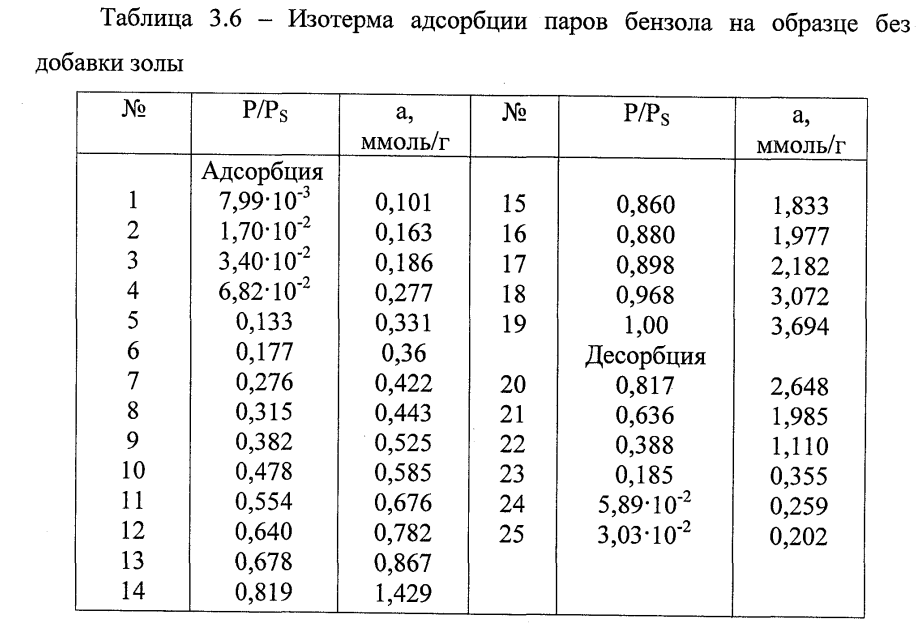
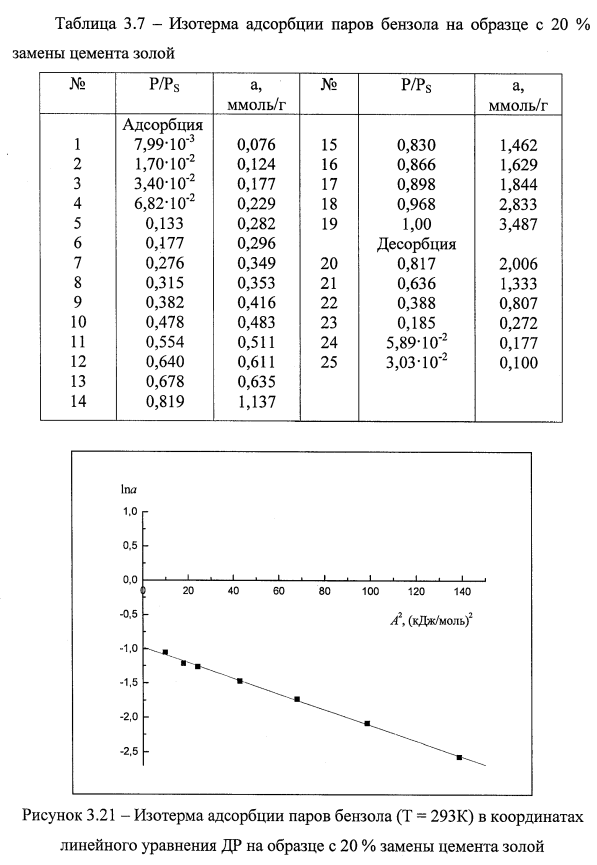
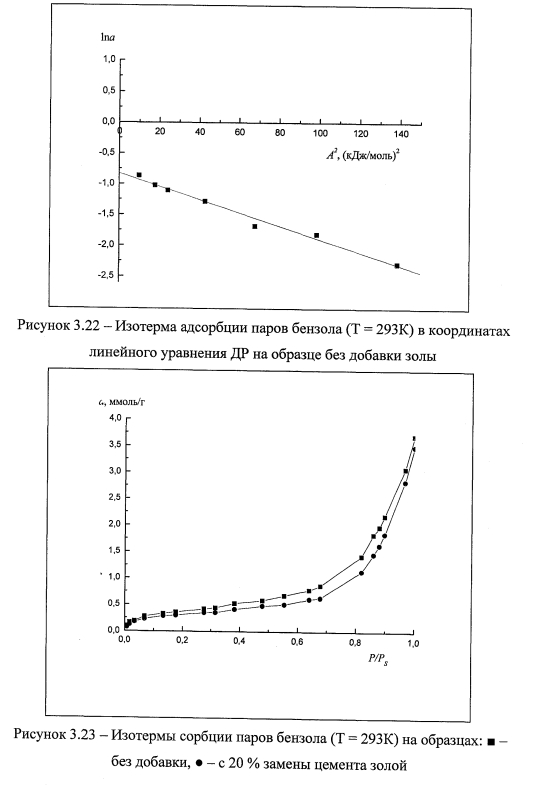
В табл.3.8 приведены основные параметры микропор, объем мезопор и их площадь.
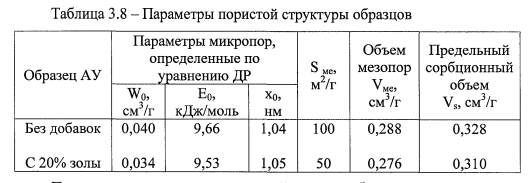
При введении золы в композитный раствор объем мезопор несколько уменьшается, а их площадь сокращается в два раза, что приводит к получению более монолитной системы.
Проведенные исследования показали, что добавление высокодисперсной золы приводит к проникновению частиц в мелкие поры цементного камня, что приводит к упрочнению композитной системы.
Выводы
- Исследовано влияние добавок золы от сжигания шпал на начальную структуру образования и физико-химические свойства глиноцементных растворов с водоцементными соотношениями 2:1. Установлено, что с увеличением содержания золы скорость структурообразования уменьшается, а время потери текучести образцов увеличивается.
- Изучено влияние золы на структуру образования и прочностные показатели композитных растворов с водоцементным соотношением 2:1. При замене 5% цемента золой скорость структурообразования увеличивается, и прочность системы возрастает примерно на 50% по сравнению с контрольным образцом.
- На основании метода микрозондирования на просвечивающемся микроскопе было установлено, что введение золы приводит к получению однородной системы с полным заполнением трещин в цементном камне, улучшению прочности и снижению водопоглощения. Экспериментально доказано, что можно заменить 20% цемента золой без потери технологических показателей раствора. При введении золы в композитный раствор объем мезопор несколько уменьшается, а их площадь сокращается в два раза, что приводит к получению более монолитной системы.
- Установлено, что водопоглощение в присутствии золы снижается по сравнению с композитным раствором без добавок. При нагнетании воды для композитных систем с заменой 20% цемента золой водопоглощение снижается примерно на 30%.
Список литературы
- Луканина Т.М., Фридман A.A. К вопросу расширения использования грунтов, укрепленных органическими вяжущими, для дорожных одежд. — В сб.: Материалы VI Всесоюзного совещания по основным направлениям научно-технического прогресса в дорожном строительстве, вып. 7 «Применение каменных материалов и укрепленных грунтов в дорожных одеждах». — М., 1976. — с. 36-42
- Состав и свойства золы и шлака. Справочное пособие./Под ред. В.А. Мелентьева. — Л., Энергоиздат, 1985.-208 с.
- Использование зол — уноса, золошлаковых смесей и шлаков тепловых электростанций в дорожном строительстве // Тр. СоюздорНИИ. Вып. 82.-М.: СоюздорНИИ, 1975. — 186. с.
- Укрепленные грунты // Свойства и применение в дорожном строительстве и аэродромном строительстве. — М.: Транспорт, 1982. — 400 с.
- Воробьев Х.С. Безотходные технологии и использование отходов и вторичных продуктов в производстве строительных материалов // Строительные материалы, 1989, №8. — 5-8с.
- Опыт использования активных и неактивных зол уноса ТЭС Франции в дорожном строительстве (по материалам зарубежного опыта)./Экспресс-информация, вып. 18 «Повышение эффективности производства и качества дорожных работ». ЦБНТИ Минавтодора РСФСР.-М., 1977.-56 с.
- Elks A.D., Redman G.T.R.Site control and the construction of embanknents using pulverised fuel ash from Lagoons. «The Surveyor and Municipal Engineer». 1965, Juli.
- Proceedings of the Institute of Civil Engineers. 1989. Vol 89. June.
- Новейшие отечественные опыты применения зол в дорожном строительстве. Перевод Союздорнии 84/36829
- Использование отходов тепловой энергетики и угольной промышленности для производства строительных материалов в странах СЭВ. /Экспресс-информация ВНИИЭСМ. 1981г., сер.20, зарубежный опыт, вып. 5.
- Шустер Дж.С., Хансен P.JI. Зола уноса, как строительный материал для насыпных сооружений. American Society of Civil Engineers Gournal of Power Division. 1972 torn 98.
- Добавки в бетон: Справочное пособие // B.C. Раманчандран, Р.Ф. Фельдман, М. Колленпарди и др. Под редакцией B.C. Раманчандран. Пер. с англ. — М.: Стройиздат, 1988. — 575с.
- Haga N., Ohkawa V., Kawamoto Т., Konno M., Mizoguchi J Utilisation of blast furnace and steel slags in road construction. NipponSteel Techn.Rept. 1981/N 17.
- Construczioni. 1987.vol 36. N384.
- Liu Hongjun, Yuan Feng, Yang Donghai. The strenghth varieti-esof the seibsurface made of lime and fine coal ash of the Hingwaj from Changba to Baichengt. Dongbei linye daxue xuehao = J. Nort-East Forest. Univ. 2000. 28, N1.
- Chen Xiaotong,Shao Jiexicn,Zhang Jun,ChenRongsheng, Don Yoimian, Zhang Fan. Dongnan daxue xuebao. Ziran kexue ban = J.Soulheast Univ. Natur. Sci.Ed.2001.31. N3.
- Bredel G. Tackling India’s coal ashproblem Mining Eng. (USA). 1995. — 51. N10.
- «Flat as a Pancake» pavement meets tough spees in Kansas. ENR: Eng.Ncws-Rec. 1997 — 238, N 18.
- Применение порошковых отходов промышленности в асфальтобетоне. ЦБНТИ Минавтодора РСФСР. — М., 1990.
- Сватовская Л.Б., Сычев A.M., Макарова Е.И. и др. Новые экозащитные технологии на железнодорожном транспорте: Монография / Сватовская Л.Б. [и др.]; под ред. Сватовской Л.Б. — М.: ГОУ «Учебно- методический центр по образованию на железнодорожном транспорте», 2007. — 159с.
- ВСН 185-75 Технические указания по использованию зол уноса и золошлаковых смесей от сжигания различных видов твердого топлива для сооружения земляного полотна и устройства дорожных оснований и покрытий, автомобильных дорог. Минтрансстрой — М., 1976. — 22 с.
- Кнатько В.М., Кнатько М.В., Щербакова Е.В. ИММ — технология против отходов (Искусственное воспроизводство природных процессов минералообразования — перспективное направление обезвреживания и
утилизации промышленных отходов)//Энергия: экономика, техника, экология. -№12, 2001. — с. 29-35. - Albino et al. Stabilization. Solidification of Hazardous Waste before Landfill Disposal // Journal of Environmental Science and Health. 1994. № 2 A.
- Evans, P.T. Williams. Heavy metal adsorption onto flyash in waste incineration flue gases // Process Safety and Environmental Protection. 2000. V. 78. P. 40-47.
- Riemann D.O. Heavy metals teach ability from solid waste incineration residues // Waste management and research/ 1989/ №7
- Кикава О.Ш. Утилизация золы и шлака мусоросжигательных заводов в области экологии — М.: Издательство «Сигнал», 2000. — 44 с.
- Ицкович С.М., Чумаков Л.Д., Баженов Ю.М. Технология заполнителей бетона: Учебник для строительных вузов. — М.: Высшая школа, 1991. — 272 с.
- Бутовский М.Э. Использование отходов Рубцовской ТЭЦ для производства строительных материалов // Всерос. научно — техн. конф. «Сырьевые ресурсы регионов и производство на их основе строительных материалов» // Сб. статей, октябрь, 2008. — Пенза, 2008. — с. 9-12
- Бутовский М.Э., Фок Н.А. Использование отходов Рубцовской ТЭЦ для производства строительных материалов // Строительные материалы. 2009, №6. — с. 90-91
- Бутовский М.Э. Неутилизированные отходы теплоэлектростанции в г. Рубцовске — источник экологической опасности. Экология промышленного производства №2, 2010. — с. 36-40
- Бурак В.Е. Результаты эколого-биологической оценки золы Белобережской ТЭЦ на пригодность к применению в качестве компонента строительных материалов // Проблемы природообустройства и экологической безопасности. — Брянск: БГСХА, 1997.-с. 46-50
- Бурак В.Е., Вишневская В.В., Федоренко Е.А. Экологическая оценка портландцемента и сырья для его производства методом биотестирования. Вестник: Научно — технический журнал. — №2. — Т.8. — Санкт-Петербург, МАНЭБ, 2003. — с. 51-54
- Веллингтон П. Методика оценки проростков семян. — М.: Колос, 1973. -с. 75-98
- Доспехов Б.А. Методика полевого опыта: (С основами статистической обработки результатов исследований). — Изд. 4-е, перераб. и доп. М.: Колос, 1979.-416 с.
- Kojima Y., Usuki A., Kawasumi М., Okada A., Kurauchi Т., Kamigaito О. Synthesis of nylon 6-clay hybrid by montmorillonite intercalated with e- caprolactam. // J. Polym. Sci., Part A, 1993, V.31. — P. 983-986
- Kojima Y., Usuki A., Kawasumi M., Okada A., Kurauchi Т., Kamigaito O. One-pot synthesis of nylon 6-clay hybrid. // J. Polym. Sci., Part A, 1993, V.31.-P. 1755-1758
- Yano K., Usuki A., Okada A., Kurauchi Т., Kamigaito O. Synthesis and properties of polyimide-clay hybrid. // J. Polym. Sci., Part A, 1993, V.31. — P. 2493-2498