Сейчас ваша корзина пуста!
Совершенствование Конструкции Болтового Крепления Рельсов к Железобетонным Брусьям
Цикл статей:
Глава 1 — Виды железобетонных подрельсовых оснований для стрелочных переводов
Глава 2 — Разработка методики расчета и проектирования железобетонных брусьев для стрелочных переводов
Глава 3 — Совершенствование конструкции болтового прикрепления
Глава 4 — Исследование шурупно-дюбельного способа прикрепления рельсов к железобетонным брусьям
Глава 5 — Эффективность применения железобетонного основания на стрелочном переводе
Для крепления металлических частей стрелочных переводов к железобетонному основанию используются типовые скрепления для железобетонных шпал.
В качестве прикрепителей в этих скреплениях применяются:
а) съемные закладные болты, вставляемые через отверстия в бетоне в металлические шайбы в теле брусьев;
б) шурупы, завинчиваемые в дюбели из дерева или полимерного материала или в металлические спирали в теле брусьев;
в) скобы или клеммы, вставляемые в металлические детали (анкеры) в теле брусьев.
На зарубежных дорогах в большинстве случаев применяется шурупно- дюбельное прикрепление (см. рис. 1.7-1.10). Известно также применение болтового прикрепления, а на некоторых дорогах анкерного способа крепления деталей стрелочных переводов (скрепление 8ВЗ, Пандрол, Сейфлок см. рис. 1.6).
На отечественных дорогах для крепления рельсовых и стрелочных подкладок к железобетонным переводным брусьям с самого начала применяется болтовое скрепление КБ раздельного типа с жесткими клеммами и пружинными шайбами.
Скрепление КБ, разработанное в 50-60 годах, по-прежнему остается основным видом скрепления для железобетонных шпал и брусьев на дорогах России и обеспечивает в целом надежную работу пути. Недостатки скрепления типа КБ известны и отмечены в литературе, что определило стремление к разработке новых вариантов болтового скрепления, как с металлическими подкладками, так и без них (БП, БПУ, ЖБР и др.). Некоторые из этих разработок на отечественных дорогах уже доведены до стадии эксплуатационных испытаний в масштабах десятков километров пути, но еще не получили полного признания для возможной замены ими скрепления КБ.
В 2000 году на стрелочных переводах в опытном порядке также было применено новое болтовое скрепление ЖБР-65 нераздельного типа без подкладок с упругими клеммами. Полная эксплуатационная оценка опытных переводов пока не получена, из-за недостаточной наработки пропущенного тоннажа.
Путеобследовательские станции ЦП МПС, ведущие эксплуатационные наблюдения за работой новых конструкций стрелочных переводов [59,82-85], отмечают, что при общей положительной оценке работы стрелочных переводов с железобетонными брусьями на них имеется нестабильность ширины рельсовой колеи и возникают отступления от нее за пределы допусков. Отмечена тенденция к уширению рельсовой колеи, особенно в переднем вылете рамного рельса, у острия остряков, в корне остряков и в переводной кривой. При этом кромка резиновой прокладки, которая должна удерживать ширину колеи, в процессе эксплуатации под действием поперечных сил перерезается подкладкой.
Для удержания ширины колеи в пределах допусков линейные работники службы пути применяют различные искусственные приемы. Так, например, применяют деревянные распорки между рельсами соединительных путей или ставят металлические стяжки. Временный положительный эффект дает установка фиксаторов в виде костылей, металлических деталей или деревянных пробок, забиваемых в каналы для закладных болтов. Применяют и другие способы, нарушающие нормальную работу брусьев.
При анализе отчетных материалов из них были взяты значения ширины колеи в разных зонах стрелочного перевода (стык рамных рельсов, острие и корень остряка, середина переводной кривой по прямому и боковому пути), измеряемые после пропуска того или иного тоннажа до 250 млн. т. брутто.
Переводы были выбраны произвольно на ряде станций Свердловской ж.д. с различными характеристиками по грузонапряженности, осевым нагрузкам и характеру движения поездов.
В результате анализа собранных статистических данных по 140 переводам получены зависимости между шириной колеи и пропущенным тоннажем в разных зонах перевода.
Примеры таких зависимостей представлены на рис. 3.1-3.3. Эти данные наглядно подтверждают наличие на стрелочных переводах тенденций к изменению ширины рельсовой колеи по мере увеличения пропущенного тоннажа, в том числе и за пределы допусков.
Четкая тенденция к уширению колеи в зависимости от тоннажа явно просматривается в острие, корне остряков и зоне переводной кривой по прямому пути. Коэффициент корреляции зависимостей на этих участках составляет от 0,6 до 0,8.
Это показывает, что существующие скрепления не в полной мере обеспечивают стабильность ширины рельсовой колеи и в настоящее время наиболее актуальной задачей при дальнейшем совершенствовании железобетонных брусьев является обеспечение стабильности ширины рельсовой колеи на переводах в процессе их эксплуатации.
В отличие от перегонных участков, путь на стрелочных переводах работает в более трудных условиях: радиус кривой составляет всего 200-300 м, отсутствует увеличение ширины колеи в кривой, подуклонка рельсов и возвышение наружного рельса кривой. Все это значительно увеличивает динамические поперечные силы, действующие на рельс при проходе подвижного состава по переводу и вписывании колес тележек в колею. Повышенные поперечные силы приводят к износу упругих прокладок и расстройству прикрепления рельсов и стрелочных деталей к брусу. В скреплении типа КБ, при повышенных поперечных силах, происходит более быстрый износ и срез кромок резиновых прокладок, сдвижка подкладок, в зависимости от пропущенного тоннажа (Т)ослабление затяжки и изгиб закладных болтов, уширение колеи вплоть до скола упорных бетонных кромок углублений в брусьях.
Возможность уменьшения силового воздействия на рельсы, в поперечном к оси пути направлении при помощи таких мероприятий, как уширение колеи в кривой, устройство подуклонки рельсов или возвышения наружного рельса в пределах стрелочного перевода нецелесообразно, т.к. это значительно увеличило бы количество типоразмеров брусьев и стоимость их изготовления, усложнило укладку и эксплуатацию стрелочных переводов.
Так, устройство разной ширины колеи и подуклонки рельсов на брусьях сразу исключает возможность унификации брусьев для переводов правого и левого направлений, т.е. в два раза увеличило бы число типоразмеров брусьев, подлежащих изготовлению и поставке железным дорогам и, соответственно, вдвое увеличило бы потребность в оснастке для их производства. По этим причинам такое конструктивное направление не получило применение на отечественных дорогах.
Наиболее целесообразным направлением следует считать совершенствование конструкции узла прикрепления рельсов или стрелочных деталей к брусьям, путем повышения сопротивления скрепления поперечному сдвигу.
Выбор направлений повышения сопротивления болтового скрепления поперечному сдвигу
В скреплении типа КБ, применяемом на железобетонных шпалах и брусьях, закладной болт непосредственно не участвует в восприятии поперечных сил, действующих в пути. Они воспринимаются трением металлической подкладки по резине, внутренним сопротивлением резины поперечному сдвигу, упором выступающей кромки резиновой прокладки в бетон и сопротивлением бетонной кромки углубления в шпале или брусе. Роль закладного болта заключается в обеспечении взаимного прижатия всех элементов скрепления друг к другу, повышения тем самым сил трения и сопротивления поперечному сдвигу.
При должном обеспечении и контроле затяжки болтов сопротивление сдвигу достаточно высокое. При ослаблении затяжки — оно резко падает. Наиболее слабым элементом в этом комплексе является кромка резиновой прокладки.
Для повышения сопротивления поперечному сдвигу болтового скрепления типа КБ возможны следующие направления:
применение упругих прокладок из более прочного полимерного материала с повышенным сопротивлением сжатию и повышенным упругим сопротивлением сдвигу;
увеличение площади передачи поперечных сил на бетон бруса через упругую прокладку;
дополнительная передача поперечных сил на бетон бруса через упорные элементы из полимерного материала с частичным включением закладного болта в работу на сдвиг.
Рассмотрим указанные направления.
По действующим «Техническим требованиям к промежуточным рельсовым скреплениям» (ЦП 1-86) узел скрепления следует рассчитывать на горизонтальную поперечную силу в 50 кН (5 тс). Ширина стрелочной
прокладки составляет 180 мм, толщина — 20-25 мм. Площадь контакта
1
t »AC X 2
подкладки с кромкой резиновой прокладки составляет 36- 45.мм. f
При неблагоприятном сочетании ослаблении затяжки закладных болтов и полном отсутствии сил внутреннего трения в прокладке напряжения сжатия кромки прокладки могут достигать 110-140 кгс/см2, что намного превышает допустимые для резины значения (35-40 кгс/см2) и является причиной среза и разрушения прокладок.
Одним из путей преодоления существующего недостатка является применение прокладок из полимерного материала с повышенной прочностью
на сжатие. В результате проведенного анализа были намечены материалы, представленные в табл. 3.1, обладающие повышенной прочностью, но имеющие большую жесткость (модуль упругости) и меньший коэффициент трения по сравнению с резиной. Поэтому преимущества, достигнутые повышенной прочностью, могут быть потеряны за счет уменьшения трения и поперечные силы, действующие на прокладку, в конечном счете, возрастут. Кроме того, применение прокладок с повышенным модулем упругости (см. табл. 3.1) приведет к увеличению общей жесткости пути на стрелочных переводах, росту динамических вертикальных нагрузок на элементы перевода, в то время как необходимо стремиться к всемерному снижению жесткости пути.
Таблица 3.1
Наименование материала | Прочность на сжатие, кг/см2 | Модуль упругости, МПа | Коэффициент трения |
Резина | 40 | — | 0,55 |
Армамид ПАСВ30-1Э | 128 | 7300 | 0,3 |
Армамид ПАСВ 30-1ЭТМ | 112 | 6900 | 0,3 |
Технамид АСВ 30-А | 132 | 9500 | 0,3 |
Эраплен | 60 | 3200 | 0,2 |
Исследования по разработке упругих прокладок из полимерных материалов с повышенной прочностью на сжатие и с повышенным
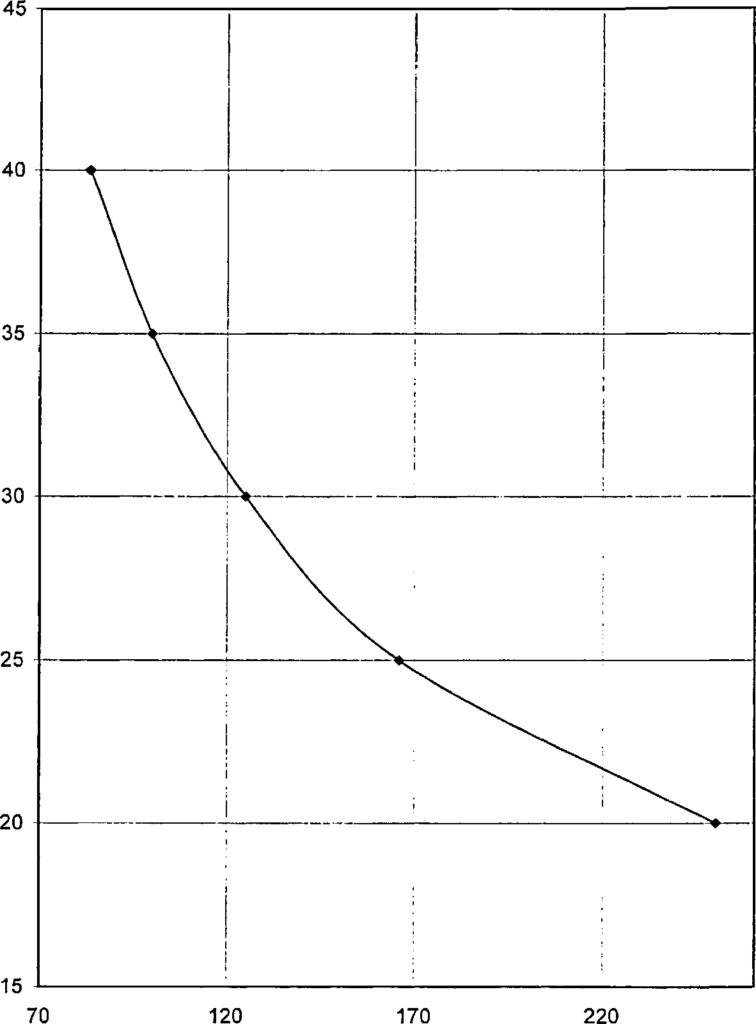
сопротивлением сдвигу в настоящее время ведутся по отдельной программе и поэтому не были предметом данной работы.
Повышение сопротивления поперечным силам путем увеличения поверхностей контакта торца подкладки с резиновой прокладкой и кромки резиновой прокладки с бетоном в углублении подрельсовой площадки, ограничено размерами стрелочных и рельсовых подкладок и невозможностью дальнейшего увеличения глубины выемок в подрельсовых площадках брусьев, так как это приведет к снижению трещиностойкости брусьев.
Для исследования этого вопроса на рис.3.4 показана зависимость сжимающих напряжений (ст) в кромке резиновой прокладки от высоты торца стрелочной подкладки (Аот) и его заглубления (Аз) в бетон бруса. При этом принята наибольшая ширина подкладки в 200 мм (20 см) и необходимость размещения под нее прокладки толщиной (Ая/,) в 10 мм. Величина поперечной силы принята, как указано выше, в 5000 кгс.
Из рис. 3.4 следует, что допустимые для резины значения сжимающих напряжений при ослаблении затяжки закладных болтов могут быть обеспечены только при высоте торца подкладки более 35 мм и глубине выемки более 45 мм.
На рис. 3.5 показано изменение величины предельного изгибающего момента по трешиностойкости подрельсового сечения бруса (Мтр) в зависимости от высоты этого сечения или, соответственно, от заглубления (А3) подрельсовой площадки в бетон.
Для брусьев находящихся в зоне стрелки и соединительных путей, величина Мщ, для подрельсового сечения составляет, по разным проектным разработкам, 14-15 кН-м.
Одним из простых и надежных направлений решения поставленной задачи является повышение сопротивления скрепления типа КБ, действию поперечных сил путем дополнительной передачи их непосредственно на бетон бруса, минуя упругие прокладки.
Технически такое решение может быть достигнуто установкой съемных закладных упорных деталей из полимерного материала между стержнем закладного болта и поверхностью болтового канала в теле бетонного бруса, включая в сопротивление действию поперечных сил также и стержень закладного болта.
Попытки применения съемных упорных деталей, вставляемых между стенкой бетонного канала и стержнем закладного болта для включения его в работу, были и ранее в опытных конструкциях болтовых скреплений для железобетонных шпал и плит [32]. Причиной неудач всех этих попыток в прошлом было несовершенство контакта закладных деталей с поверхностью бетонного канала. Выполнение каналов с помощью примитивных вкладышей из древесного шпона приводило к несоблюдению размеров и образованию неровных поверхностей в каналах, заполнению их бетоном. Из-за неровности поверхностей контакта упорные детали занимали неправильное положение и при затяжке болта ломались.
Поэтому первой задачей настоящих исследований была разработка мер, обеспечивающих проектные и стабильные размеры каналов в шпалах и брусьях, а также гладкость поверхностей контакта путем применения вкладышей из полимерного материала.
Разработка технических требований к конструкции полимерных вкладышей
Вкладыши из полимерных материалов должны обладать формоустойчивостью при различных термо-влажностных состояниях, возникающих в процессе производства и эксплуатации железобетонных шпал и брусьев при этом они должны сохранять форму и размеры каналов при обработке бетона в пропарочных камерах при температуре до + 95°С и влажностью 95%, а при работе в пути сохранять прочность и формоустойчивость как при повышенных температурах до плюс 50°С, так и при замораживании до минус 50°С.
Форма и габаритные размеры должны обеспечивать беспрепятственный проход головки закладного болта, а нижняя поверхность вкладышей должна полностью повторять очертание закладных седловидных шайб.
На основании анализа способов производства шпал и брусьев на действующих заводах и перечисленных выше технических требований были разработаны предложения по конструкции двух типов вкладышей, устанавливаемых в оснастку до бетонирования шпал или брусьев:
вкладыши, устанавливаемые в верхней части каналов над металлической закладной шайбой (рис. 3.6);
вкладыши-пустотообразователи, устанавливаемые по всей высоте каналов и охватывающие металлическую закладную шайбу (рис.3.7).
Вкладыши первого типа не воспринимают нагрузки от затяжки закладного болта и от них не требуется обеспечение электроизоляции. Их задача — соблюдение проектных размеров по ширине болтового канала на всех стадиях изготовления и эксплуатации брусьев.
Вкладыши-пустотообразователи второго типа при безусловном обеспечении необходимой электроизоляции кроме этого должны воспринимать нагрузки от затяжки закладных болтов, передаваемые через металлические закладные шайбы. Поэтому они должны сохранять не только форму и размеры канала, но достаточную прочность на сжатие во всем диапазоне возможных температур, указанных выше, а также препятствовать падению закладных болтов при сборке на звеносборочных базах и при необходимой разборке скреплений в эксплуатации.
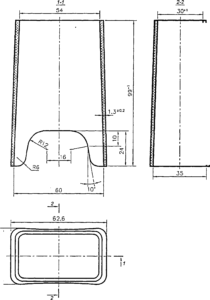
3.6. Вкладыш из полимерного материала
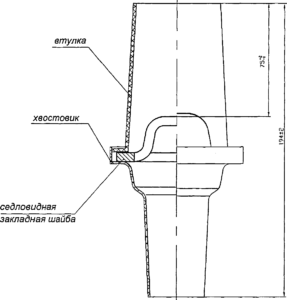
3.7. Вкладыш-пустотообразователь электроизолирующий
При разработке вкладышей предусмотрено применение новых седловидных закладных шайб, разработанных ВНИИЖТом [55] и вошедших в новый стандарт (ОСТ 32.179-2001).
Разработанные по техническим требованиям, изложенным выше, конструкции вкладышей и технические условия на их изготовление утверждены Департаментом пути и сооружений МПС России, включены в стандарты на железобетонные брусья (ОСТ 32.134-99) [54],
шпалы (ОСТ 32.152-2000) [56]. Эти изделия защищены патентами на изобретение №2121028 и №2169226 [38, 39].
Применение пластмассовых вкладышей на всех заводах ЖБШ уже, повысило качество шпал и брусьев и сократило трудозатраты при монтаже скреплений на звеносборочных базах.
Разработка технических требований к конструкции упорной закладной детали
После решения вопросов по конструкции вкладышей были проведены исследования по разработке технических требований к конструкции упорной закладной детали — втулки из полимерного материала, вставляемой между стержнем закладного болта и стенкой бетонного канала в теле бруса или шпалы. Упорная втулка должна воспринимать основную часть горизонтальной поперечной силы от подвижного состава, передавать ее непосредственно на бетон шпалы в верхней части болтового канала и служить упором для стержня закладного болта. Закладной болт, участвуя в восприятии поперечной силы, не должен подвергаться значительному изгибу.
В типовом скреплении КБ закладной болт свободно проходит в отверстиях подкладки и упорной прокладки. Растягивающие напряжения в стержне болта возникают только от затяжки гайкой, а также от внецентренного контакта с закладной и пружинной шайбами. Изгибные напряжения в стержне болта возникают лишь при большом смещении подкладки и давлении ее на болт при ослабленной его затяжке. Поэтому излом закладных болтов в скреплении КБ на железных дорогах практически отсутствует.
При разработке модели упорной втулки необходимо было обеспечить нормальные условия работы на изгиб стержня закладного болта при действии на него горизонтальной поперечной силы, передаваемой подкладкой и упорной втулкой.
Для уменьшения изгибающих напряжений в стержне болта необходимо, чтобы изгибающий момент в нем от действия поперечных сил был минимальным. Как показано ниже на рис. 3.8, это достигается при наименьшем расстоянии от точки приложения поперечной силы Н (середины толщины подкладки) и серединой высоты той части упорной втулки, которая непосредственно входит в канал бруса и контактирует с бетоном. Этому условию соответствует расположение упорной втулки у самого верха болтового канала в брусе или шпале.
Для раздельного скрепления поперечные размеры упорной втулки определяются тем, что при установке она должна входить в отверстие в типовой металлической подкладке скрепления КБ при существующих размерах этого отверстия. Большая сторона отверстия в подкладке КБ направлена поперек оси шпалы или бруса, т.е. перпендикулярно действию поперечной силы, что и определяет размер упорной втулки по ширине в направлении действия поперечной силы.
Высота упорной втулки и площадь контакта ее с бетоном определяются прочностью полимерного материала втулки.
Если исходить из размеров существующих подкладок скрепления КБ (толщина и размеры отверстий) и принять размеры упорной втулки, указанные на рис. 3.4, то площадь контакта упорной втулки с бетоном составит 4,4×4,0 = л 17,6 см . При величине поперечной силы Н = 5000 кг, установленной в технических требованиях ЦПТ-1-86, и без учета сопротивления сдвигу по прокладке напряжения сжатия по поверхности контакта втулки с бетоном могут составлять 5000: 17,6 = 286 кгс/см2, что вполне приемлемо и для бетона и для многих современных полимерных материалов.
В направлении действия поперечной силы (вдоль оси шпалы или бруса) упорная втулка предложена несимметричной. Толщина упорных стенок различна. Это облегчает установку втулки в совмещенные отверстия подкладки и шпалы, а также в некоторых пределах дает возможность производить регулировку ширины рельсовой колеи поворотом упорной втулки на 180°.
Кроме требований по прочности на сжатие полимерный материал должен обладать формоустойчивостью и прочностью при плюсовых и минусовых температурах, указанных выше (см. стр. <30 ), возникающих при изготовлении и эксплуатации шпал или брусьев.
В необходимых случаях, например, при использовании упорных втулок в шпалах на участках с автоблокировкой без изолирующих втулок) к ним могут предъявляться требования по электрическому сопротивлению.
Исходя, из всех этих условий была разработана модель узла скрепления типа КБ для брусьев и шпал с упорной пластмассовой изолирующей втулкой, представленная на рис. 3.8, и модель упорной втулки (рис.3.9). Модель узла скрепления включает в себя пластмассовый вкладыш (см. рис. 3.6), забетонированный в брусе при его формовании, и упорную изолирующую втулку, вставляемую в отверстие подкладки и канал бруса при сборке скрепления. В скреплении типа КБ размеры упорной втулки сильно ограничены размерами отверстия в подкладке. Эффективным может быть применение упорных втулок в бесподкладочных болтовых скреплениях (например, ЖБР, БПУ), где эти ограничения снимаются.
Выводы
- В болтовом рельсовом скреплении типа КБ закладной болт практически не участвует в сопротивлении поперечным нагрузкам от подвижного состава. В отдельных зонах стрелочного перевода (стрелка, переводная кривая) возникают повышенные поперечные силы, под действием которых происходит быстрый износ упругих прокладок этого скрепления, и появляются отклонения в ширине рельсовой колеи.
- Разработанные, с целью обеспечения возможности применения упорных втулок, пластмассовые вкладыши-пустотообразователи, обеспечивающие стабильные размеры болтовых каналов и повышающие точность соблюдения ширины рельсовой колеи при одновременном улучшении качества изготовления подрельсовых частей железобетонных брусьев и шпал, включены в действующие стандарты на эти изделия (ОСТ 32.134-99 и ОСТ 32.152-2000).
- Установка упорных втулок из полимерного материала на стержне закладного болта, с целью передачи части горизонтальной поперечной нагрузки от подвижного состава непосредственно на бетон в верхней части болтового канала бруса, является одним из эффективных способов повышения стабильности ширины рельсовой колеи при болтовом способе прикрепления рельсов к железобетонным брусьям.
- Предложенная конструкция упорной изолирующей втулки прошла циклические лабораторные испытания в результате которых доказано ее положительное влияние на стабильность ширины колеи. Полученные положительные результаты позволяют рекомендовать втулку для широких испытаний в эксплуатационных условиях.
Список Литературы
- Золотарский А.Ф. — Конструкции прикрепления рельсов к железобетонным шпалам. — В кн. Железнодорожный путь на железобетонных шпалах. Под ред. А.Ф.Золотарского. М. Транспорт. 1967. С. 75-114
- Закладной узел железобетонной шпалы. Пат. № RU 2121028 С 1 / Серебренников В.В., Акимов В.П., Рессина Н.В. № 96115733/28: Заяв. 09.11.2000; Опубл. 20.06.2001. Бюл. №30.
- Закладной узел железобетонной шпалы (Варианты). Пат. № RU 2169226 С1 / Серебренников В.В., Акимов В.П., Рессина Н.В. № 2000127882/28; Заявл. 09.11.2000; Опубл. 20.06.2001. Бюл. № 17.
- ОСТ 32. 179-2001. Шайбы закладные седловидные. Общие технические условия. Взамен ТУ 14-125-730-97. Введ. 09.01.02.- М., МПС России. 2002. 12 с.
- ОСТ 32.152-2000. Шпалы железобетонные предварительно напряженные для железных дорог колеи 1520 мм Российской Федерации. Общие технические требования. Взамен ТУ 5864-024-11337151-96, ТУ 5864-12300284807-93, ТУ 5864-019-11337151-95, ТУ 5864-010-11337151-96. Введ. 8.11.000. М., МПС России. 2002. 32 с.