Сейчас ваша корзина пуста!
Разработка химического состава и технологии термической обработки железнодорожных рельсов из стали бейнитного класса
Цикл статей:
Глава 1 — Разработка химического состава и технологии термической обработки железнодорожных рельсов из стали бейнитного класса
Глава 2 — Теоретические предпосылки разработки химического состава сталей бейнитного класса
Глава 3 — Оборудование и методика экспериментальных исследований
Глава 4 — Исследование влияния различных видов термической обработки на структуру и свойства сталей бейнитного класса
Глава 6 — Служба железнодорожных рельсов из сталей бейнитного класса
Введение
Безопасность движения поездов, сохранность людей и грузов в значительной степени зависят от исправного содержания, качества, стойкости железнодорожного полотна, главным элементом которого являются рельсы. В настоящее время проблема повышения работоспособности рельсов, несмотря на достигнутые положительные результаты в обеспечении качества рельсовой стали, стоит как никогда остро не только в России, но и за рубежом. В современных условиях эксплуатации железных дорог при движении тяжелого транспорта нагрузки от оси могут достигать 35 т, а скорости передвижения скоростных поездов до 250 км/ч. Анализ выхода из строя рельсов при службе в пути показывает их высокий уровень по дефектам контактно-усталостного происхождения, смятию, износу, термомеханическим повреждениям.
Эксплуатационная стойкость железнодорожных рельсов, как известно, во многом определяется структурой и механическими свойствами рельсовой стали. В связи с этим возрастает роль исследований в области физики металлов и металловедения в создании новых, более совершенных и прогрессивных сталей, способных обеспечить длительную прочность рельсов в столь сложных условиях эксплуатации.
На основе многочисленных теоретических и экспериментальных исследований установлено, что сопротивление рельсов износу и повреждаемости контактно-усталостными дефектами значительно возрастает с увеличением дисперсности структуры. В настоящее время в структуре стандартных рельсов из сталей перлитного класса межпластиночное расстояние составляет 0,14 0,3 мкм и приближается к своему предельному значению (0,1 мкм). В связи с этим пути дальнейшего повышения эксплуатационной стойкости рельсов из сталей перлитного класса исчерпаны и предполагают переход на производство рельсов из сталей бейнитного класса, отличающихся более дисперсным строением и, следовательно, более высокими механическими свойствами.
В настоящее время проблема создания сталей бейнитного класса для производства рельсов является малоизученной и бурно развивающейся областью научных исследований как в России, так и за рубежом. Переход от традиционных технологий производства рельсов из высокоуглеродистых сталей перлитного класса на низколегированные из сталей бейнитного класса является весьма заманчивым и перспективным как для производителей, так и для потребителей рельсового металла. Рельсы из сталей бейнитного класса обладают повышенным комплексом механических и эксплуатационных свойств, более технологичны, при экономном легировании характеризуются пониженной себестоимостью. Применение сталей на основе бейнитной структуры позволяют также отказаться от экологически вредной технологии объемной закалки в масле. В то же время, как показывает анализ специальной технической литературы, технологии термической обработки рельсов из сталей бейнитного класса, исключающие закалку, находятся в стадии разработки. До настоящего времени не установлены точные связи между составом, микроструктурой и свойствами стали, научно не обоснована их природа. Кроме этого, имеются противоречия в выборе структурного состояния для рельсов, а также в определении возможностей их использования. По данным одних исследователей оптимальной структурой является смешанная структура, состоящая из отпущенного мартенсита и бейнита, другие исследователи утверждают, что структура должна состоять только из нижнего бейнита. По результатам одних исследований установлено, что бейнитные рельсы хорошо зарекомендовали себя по износостойкости, другие исследования показывают, что бейнитные рельсы отличаются повышенной контактно-усталостной прочностью.
В связи с этим, вопрос выбора химического состава и технологии термической обработки в целях достижения требуемых механических и технологических свойств рельсов из сталей бейнитного класса является актуальным и приобретает особо важное народно-хозяйственное значение.
Цель работы: Разработка химического состава и технологии термической обработки стали бейнитного класса, обеспечивающих получение без закалочного охлаждения высокого комплекса механических и технологических свойств железнодорожных рельсов.
Для достижения указанной цели были поставлены следующие задачи:
- Исследовать особенности влияния легирующих элементов: углерода, марганца, кремния и хрома на механические свойства и структурооб- разование сталей бейнитного класса.
- Исследовать влияние различных видов термической обработки на свойства и структуру сталей бейнитного класса.
- Разработать химический состав и технологию термической обработки железнодорожных рельсов из стали бейнитного класса.
- Внедрить и освоить технологию производства железнодорожных рельсов из сталей бейнитного класса в условиях ОАО «НКМК».
- Провести полигонные испытания, установить особенности эволюции структуры и механических свойств стали марки Э30ХГ2САФМ при эксплуатации рельсов в пути.
Научная новизна. Впервые:
- Изучено влияние углерода, марганца, кремния, хрома, комплексного легирования и различных видов термической обработки на механические свойства и структурообразование сталей бейнитного класса для производства железнодорожных рельсов.
- Разработан химический состав и установлена структура стали бейнитного класса, обеспечивающие высокий комплекс механических и технологических свойств железнодорожных рельсов.
- Созданы рациональные режимы термической обработки, обеспечивающие достижение высоких свойств пластичности и вязкости без снижения показателей прочности стали бейнитного класса для производства железнодорожных рельсов.
4. Установлены особенности эволюции структуры и механических свойств стали марки Э30ХГ2САФМ при эксплуатации рельсов в пути.
Практическая значимость.
- Показана высокая эффективность способа легирования стали для повышения качества железнодорожных рельсов, равноценно заменяющего упрочняющую термическую обработку.
- Разработаны химический состав стали бейнитного класса и технология термической обработки, обеспечивающие получение сбалансированного комплекса механических и технологических свойств железнодорожных рельсов.
- Разработана, внедрена в производство и освоена технология термической обработки железнодорожных рельсов из стали бейнитного класса марки Э30ХГ2САФМ.
Реализация результатов.
- На основе полученных результатов изготовлена опытная партия железнодорожных рельсов из стали бейнитного класса марки Э30ХГ2САФМ, которая прошла полигонные и аттестационные испытания на Экспериментальном кольце ВНИИЖТ.
- Разработаны технические условия на производство железнодорожных рельсов типа Р65 высокой прочности из бейнитной стали (ТУ 0921-167оп-01124323-2003).
- Прогнозируемый экономический эффект от производства железнодорожных рельсов из стали бейнитного класса марки Э30ХГ2САФМ при минимальном объеме производства 50 тыс. тонн составил 3 600 тыс. руб. в год.
- Разработаны технические условия на производство железнодорожных рельсов типа Р65 высокой прочности из бейнитной стали (ТУ 0921-167оп-01124323-2003).
Личный вклад автора состоит в проведении экспериментов по изучению влияния химического состава сталей бейнитного класса на структу- рообразование и механические свойства; выборе химического состава бей- нитной стали, обеспечивающего сбалансированный комплекс механических свойств; определении параметров технологии термической обработки рельсов из стали бейнитного класса; промышленном внедрении и освоении технологии производства железнодорожных рельсов из стали бейнитного класса; обработке, анализе, обобщении и научном обосновании полученных результатов, формулировке выводов.
Основные положения, выносимые на защиту:
- Результаты экспериментальных исследований влияния состава сталей бейнитного класса на структурообразование и механические свойства.
- Результаты экспериментальных исследований влияния видов термической обработки на структурообразование и механические свойства стали бейнитного класса.
- Результаты разработки химического состава стали бейнитного класса для производства железнодорожных рельсов.
- Технология термической обработки железнодорожных рельсов из стали бейнитного класса марки Э30ХГ2САФМ.
- Результаты экспериментальных исследований влияния видов термической обработки на структурообразование и механические свойства стали бейнитного класса.
Достоверность полученных результатов подтверждается хорошей сходимостью результатов теоретических исследований, лабораторных и промышленных экспериментов, полигонными испытаниями рельсов на Экспериментальном кольце ВНИИЖТ.
Апробация работы. Основные положения диссертационной работы докладывались и обсуждались на следующих конференциях: Всероссийской научно-практической конференции (Новокузнецк, сентябрь 2002 г.); V Международном симпозиуме по трибофатике (Иркутск, октябрь 2005 г.); II Международной научно-технической конференции «Исследование, разработка и применение высоких технологий в промышленности» (Санк- Петербург, март 2006 г.); II Всероссийском научно-техническом семинаре «Влияние свойств металлической матрицы на эксплуатационную стойкость рельсов» (Екатеринбург, июль 2006 г.); 121 Рельсовой комиссии (Новосибирск, декабрь 2006 г.); VI Международной рельсовой комиссии по качеству рельсовой продукции метрополитенов (Киев, март 2007г.).
Публикации. Результаты диссертационной работы опубликованы в 1 справочнике, 17 статьях, из них 8 статей в изданиях, рекомендованных ВАК для опубликования результатов кандидатских и докторских диссертаций, защищены 8 патентами.
Структура и объём диссертации. Диссертационная работа состоит из введения, 6 разделов, основных выводов, списка литературы из 146 наименований, содержит 151 страницу, включая 14 таблиц и 80 рисунков.
Современное состояние научной проблемы и постановка задачи исследования
Современные требования к свойствам рельсов и рельсовой стали
К свойствам современных рельсов и рельсовой стали предъявляют следующие требования:
- сопротивление износу;
- сопротивление смятию;
- высокая усталостная прочность;
- прочность на растяжение;
- достаточная твердость;
- стойкость к охрупчиванию;
- высокая ударная вязкость (особенно актуальна для рельсов, используемых при отрицательных температурах);
- стойкость к растрескиванию (трещинообразованию);
- живучесть — способность сохранять необходимые рабочие качества при наличии повреждений в виде усталостных трещин;
- хорошая свариваемость (особенно актуальна для бесстыкового
пути);
- высокое качество поверхности;
- точность геометрических размеров, прямолинейность.
В настоящее время определены основные научно-технические направления решения проблем, связанных с повышением эксплуатационной стойкости рельсов. В частности, изучено влияние химических элементов на морфологию, состав и распределение неметаллических включений в рельсах. Проанализированы и уточнены представления о процессах модифицирования и микролегирования стали, а также конкретизированы принципы модифицирования и микролегирования рельсовой стали [1 — 15]. Изучены причины образования внутренних дефектов, приводящих к контактно-усталостным разрушениям рельсов при эксплуатации [16 — 23]. Исследовано влияние карбидо- и нитридообразующих элементов на свойства рельсовой стали [24 — 27].
Наряду с научными изысканиями проведены технические мероприятия по совершенствованию технологии отечественного рельсового производства. В этой связи были обнаружены новые пути и возможности повышения эксплуатационной надежности рельсов.
В частности, осуществлен переход технологии производства стали от мартеновского способа к кислородно-конвертерному и электросталеплавильному; внедрено вакуумирование [28 — 31]; освоено производство рельсов из непрерывнолитой заготовки [32 — 37]; усовершенствована технология правки рельсов и внедрены современные способы контроля прямолинейности рельсов по всей длине в технологическом потоке производства [38 — 42]. В результате проведенных мероприятий значительно улучшилось металлургическое качество рельсовой стали (чистота стали по сере, фосфору, газам, неметаллическим включениям, снижение пораженности металла макродефектами и поверхностными дефектами).
Повышение эксплуатационных свойств рельсов обусловлено не только улучшением их металлургического качества, но и также проведением оптимизации химического состава рельсовой стали. В этом направлении выполнен большой объём научно-исследовательских работ и промышленных экспериментов, а именно: освоено производство рельсов повышенной износостойкости из стали с увеличенным содержанием углерода до 0,88 % и микролегирующими добавками ванадия (0,07 + 0,08 %) и азота (0,012 -5- 0,017 %) [43, 44]. Эксплуатационные наблюдения, проведенные на перевальном участке Иркутск — Слюдянка Восточно-Сибирской железной дороги, отличающейся большим количеством кривых малого радиуса, показали высокую износостойкость рельсов из стали заэвтектоидного состава. Удельный их боковой износ составил 0,078 + 0,074 мм на 1 млн.тонн.брутто. В то же время для стандартных рельсов этот показатель значительно выше и составляет 0,124 мм на 1 млн.тонн брутто. Дальнейшее повышение содержания углерода выше заэвтектоидного лимитировано образованием структурно-свободного цементита. Как известно, образование по границам зерен перлитных колоний сетки структурно-свободного цементита приводит к резкому снижению ударной вязкости стали и динамической прочности рельсов [17].
Благодаря оптимизации химического состава углеродистой рельсовой электростали и применению технологии карбонитридного упрочнения достигнуто существенное повышение эксплуатационной стойкости до уровня мировых стандартов, обеспечившее наработку рельсов более 1 млрд. тонн брутто. [45].
Другим достижением является создание рельсов низкотемпературной надежности [46], обеспечившее безопасность движения при температурах минус 40° С и ниже. Этот параметр достигают посредством целенаправленного формирования в металле карбонитридов ванадия, для образования которых в стали должно содержаться достаточное количество ванадия и азота [47]. В работе [26] установлено, что гарантированное получение необходимой ударной вязкости рельсов низкотемпературной надежности обеспечивается следующим химическим составом стали (массовая доля, %): 0,75 С; 0,85 — 1,05 Мп; 0,30 — 0,45 81; 0,010 — 0,020Ы; 0,005 — 0,010 А1; 0,07-0,08 V.
Увеличение скоростей движения потребовало проведения ряда разработок, направленных на повышение геометрического качества рельсов. Технические мероприятия по улучшению режима правки, применение гибочных машин и подстуживания подошвы по всей длине рельсов перед закалкой, а также оптимизация режимов закалки и отпуска, позволили наладить производство рельсов для скоростного совмещенного движения [40].
Однако, несмотря на достигнутые результаты в повышении качества рельсов, в рамках существующей технологии отечественного производства затруднено изготовление рельсов, отличающихся повышенной надежностью и увеличенным ресурсом.
На основе многочисленных теоретических и экспериментальных исследований установлено, что сопротивление рельсов образованию дефектов термомеханического происхождения повышается с уменьшением содержания углерода в стали, а износостойкость и контактно-усталостная прочность рельсов значительно возрастают с увеличением дисперсности перлитной структуры. В настоящее время в структуре сорбита закалки стандартных рельсов межпластиночное расстояние приближается к своему предельному значению (0,1 мкм) [45]. В связи с этим пути дальнейшего повышения эксплуатационной стойкости рельсов предполагают переход к структуре бейнита, отличающегося более дисперсным строением и высоким комплексом механических свойств.
Как показывает практика, современным железным дорогам требуются рельсы повышенной точности геометрии при достаточной прочности и твердости стали, способной выдерживать высокие контактные нагрузки [49 — 52]. Согласно ГОСТ Р 51685 — 2000 для рельсов высшей категории В отклонение от прямолинейности в вертикальной плоскости не должно превышать ± 0,3 мм на длине 1,5 м, а концевая искривленность — 0,5 мм в вертикальной и горизонтальной плоскостях.
Жесткие допуски на геометрические характеристики рельсов необходимы не только для реализации высоких скоростей движения поездов (до 330 км/ч), от уровня их прямолинейности зависит также развитие повреждаемости рельсов дефектами контактно-усталостного происхождения и волнообразным износом [53, 54]. Проскальзывание колеса при движении повышает износ поверхности рельсов. Поэтому при создании рельсовой стали нового поколения требования к износостойкости и контактно- усталостной прочности являются основными.
Как показано в работе [55], основным видом, служащим причиной изъятия рельсов с пути, являются контактно-усталостные дефекты. Наибольшее число единичных отказов приходится на дефект по коду 21 (поперечная трещина в головке) [56]. Увеличение скоростей поездов неизбежно ведет к возникновению больших напряжений в месте контакта колеса и рельса, в связи с этим возрастает вероятность образования поперечных трещин в головке рельса [57]. Такие трещины, достигнув критического размера, могут привести к хрупкому разрушению рельса под поездом. В этом случае рассматривают две стадии работы рельса: первая — бездефектная, которая заканчивается зарождением контактно-усталостной трещины, вторая — развитие последней до критического размера, определяющая живучесть или трещиностойкость рельса. Соответственно надежность рельсов в конкретных условиях эксплуатации определяется продолжительностью второй стадии, которая, в свою очередь, зависит от критического размера трещины и скорости ее развития.
В работе [58] показано, что обязательным условием образования контактно-усталостных дефектов является наличие касательных напряжений. Их возникновение связано с проскальзыванием колеса относительно рельса из-за конического профиля колеса, а также при изменении режима движения подвижного состава (ускорение и торможение). При этом возникающие нормальные напряжения имеют максимальные значения на поверхности головки рельса, в то время как касательные напряжения максимальны, по данным работ [59, 60], на определенной глубине (4-^-8 мм) от ее поверхности. При этом очагом зарождения контактно-усталостных трещин, как показывают исследования ВНИИЖТ [61], являются скопления сложных оксидных включений. Однако, повышение чистоты стали по неметаллическим включениям в результате перехода к раскислению рельсовой стали комплексными сплавами [62 — 64] взамен алюминия, не привело к уменьшению количества одиночных изъятий рельсов по контактно- усталостным дефектам [65]. В работе [66] высказано предположение, что процесс зарождения микроразрушений определяется соотношением прочности и пластичности стали, прочности и деформируемости неметаллических включений, а также прочностью их сцепления с матрицей.
Другим наиболее частым дефектом контактно-усталостного происхождения являются вмятины и пятна, образующиеся в результате вдавливания колесом случайно попавших на рельс твердых тел, т. е. являются результатом механически обусловленной пластической деформации. Наряду с указанными дефектами также часто при эксплуатации рельсов возникают термомеханические повреждения, вызванные структурными превращениями в стали. Вследствие проскальзывания колеса на поверхности катания головки рельса в зоне контакта протекают мгновенные структурные и фазовые превращения, приводящие к образованию вторичной структуры (нетравящейся белой зоны), отличающейся высокой твердостью и хрупкостью. По результатам рентгеноструктурного анализа [67] белая зона характеризуется наличием линий аустенита и сильным уширением линий а — фазы, чего не наблюдалось вне белой зоны. При электронно- микроскопическом исследовании в зоне вторичных структур обнаружены также локальные изменения структуры исходного тонкопластинчатого перлита, выражающиеся в неоднородной плотности цементитных пластин и многократном их изгибе путем двойникования, дробления карбидов и появления участков промежуточного превращения с частичным растворением цементитных пластин и незавершенным формированием вторичной структуры. Локальные образования вторичной структуры, твердость которых иногда втрое превышает твердость основного металла, в дальнейшем приводят к зарождению микротрещин.
Моделирование процесса ударных нагрузок на образцах из стали с разным содержанием углерода и легирующих элементов показало, что образование вторичных структур очень сильно зависит от содержания углерода и легирующих элементов. Чем меньше содержание углерода, тем меньше вероятность образования белой зоны. В отношении легирующих элементов отмечено, что такие элементы, как N1, Сг, \У, Мп, Со, V в убывающем порядке влияют на чувствительность стали к образованию вторичных структур. По мнению Л.С. Палатника, Т.В. Равицкой и Е.Л.Островской высокая чувствительность к образованию вторичных структур стали, легированной никелем, объясняется, во-первых, его свойством расширять у — область и снижать критическую скорость закалки, а во-вторых, действием его как некарбидообразующего элемента, ускоряющего диффузию углерода и способствующего гомогенизации аустенита.
Не менее важной характеристикой рельсов является их износостойкость. Большинство исследователей считают, что интенсивность износа определяется в основном свойствами колесной и рельсовой стали. По мнению автора работы [68] в зависимости от соотношения твердостей сталей в месте контакта реализуется два варианта взаимодействия: в случае преобладания твердости колесной стали микронеровности поверхности колеса внедряются в относительно мягкую поверхность рельса. При таком взаимодействии склонность к проскальзыванию уменьшается, что соответствует уменьшению износа; в случае более высокой твердости рельса проникновение неровностей идет в сторону колеса и сопротивление проскальзыванию происходит только за счет взаимодействия микронеоднородностей на плоских поверхностях колеса и рельса. Отечественный и мировой опыт эксплуатации железных дорог показал, что превышение твердости рельса над колесом на 10 + 30 % приводит к катастрофическому износу колес. Вместе с этим, почти во всех странах с развитой железнодорожной сетью наблюдается тенденция к упрочнению рельсов и, соответственно, повышению твердости. Так, например, испытания, выполненные Федеральными железными дорогами Германии (DBAG) и компанией VoestAlpine Schienen (Австрия) показали, что углеродистые рельсы с термоупрочненной головкой имеют более высокую сопротивляемость изнашиванию, чем нетермо- упрочненные рельсы. Установлено, что после пропуска 100 млн. тонн, брутто поездной нагрузки износ рельса типа R 350 НТ в два раза меньше, чем рельса типа R260 и составил соответственно 0,25 и 0,50 мм [69]. Однако, достижение высокой твердости находится в противоречии с важным требованием по обеспечению свариваемости стали. Поэтому главной целью исследовательских разработок является достижение твердости без увеличения содержания углерода.
Появление усталостных трещин и в дальнейшем развитие хрупких разрушений зависят не только от качества рельсовой стали, уровня сил взаимодействия пути и подвижного состава, напряжений в элементах пути, а также от температуры окружающей среды. По данным служб пути на дорогах, расположенных в районах с суровыми климатическими условиями, зимой одиночные изъятия по дефектам в 2,0 2,5 раза больше, чем летом. Снижение температуры особенно заметно сказывается на развитии усталостных трещин в головке рельсов бесстыкового пути. В работе [70] также отмечается, что при низких температурах наблюдается снижение пластичности и вязкости, в результате этого возможно хрупкое разрушение рельса. Очевидно, что приоритетным направлением является повышение низкотемпературной надежности рельсового металла.
При традиционной оценке работоспособности пары «колесо — рельс» принимается во внимание либо износостойкость, либо механика усталостного разрушения.
При рассмотрении системы «колесо — рельс» с позиции трибофатики процессы контактно-усталостного разрушения и износа изучаются во взаимосвязи, выделяя новое представление о «комплексном износоустало- стном повреждении и разрушении силовых систем». Вопросы износоуста- лостного повреждения подробно изучены в работах J1.A. Сосновского, A.B. Богдановича, H.A. Махутова [71-73]. С точки зрения трибофатики «колесо — рельс» рассматривается как система комплексного повреждения: трения качения + механическая усталость одновременно (контактная усталость) и / или трение скольжения + механическая усталость одновременно (фрикционно-механическая усталость). Это означает, что между элементами системы имеет место силовое взаимодействие, обусловленное одновременным и совместным действием как контактного давления, так и циклических напряжений. В таком случае сопротивление системы комплексному износоусталостному повреждению и разрушению характеризуется следующими параметрами: долговечностью системы при одновременном действии контактного давления и циклических напряжений, обусловленной долговечностью либо колеса, либо рельса, либо обоих элементов одновременно; интенсивностью изнашивания системы с учетом действия циклических напряжений; пределом выносливости рельса с учетом влияния контактного давления; предельным контактным давлением с учетом влияния циклических напряжений. Из изложенного следует, что показатели работоспособности системы «колесо — рельс», определяемые методами трибофатики, достаточно полно отражают реальные условия их работы, тогда как аналогичные показатели, определяемые методами трения или механики усталостного разрушения, описывают поведение изучаемой системы в идеализированных условиях.
Оптимальная долговечность с позиции трибофатики как системы, так и ее элементов в целом, может быть достигнута путем управления процессами комплексного износоусталостного повреждения с учетом реального взаимодействия необратимых повреждений, обусловленных двумя источниками — контактным взаимодействием колеса и рельса и объемным повторно-переменным деформированием одного из них [74].
С точки зрения традиционных представлений для повышения тре- щиностойкости и износостойкости стали в рамках действующей на российских предприятиях технологии объёмной закалки в масле можно получить необходимые прочность и твердость стали, однако, при этом практически невозможно достигнуть требуемого уровня прямолинейности рельсов. Термические напряжения, формирующиеся по сечению рельса при объёмной закалке, существенно нарушают геометрическое качество рельсов [75]. Последующая правка не позволяет получить рельсы с удовлетворительной прямолинейностью и низкими остаточными напряжениями.
Наилучшим техническим решением, обеспечивающим получение прямолинейных рельсов, является применение способа легирования стали, приводящего к упрочнению стали без закалочного охлаждения.
Не менее важным требованием является удовлетворительная свариваемость рельсов. От качества сварного шва во многом определяется эксплуатационная стойкость бесстыковых плетей. При сварке углеродистых рельсов возникают значительные трудности, поскольку при высоком углероде возрастает вероятность хрупких разрушений, особенно при отрицательных температурах. Повышение прочности и долговечности сварных рельсов достигается не только соблюдением технологии сварки, но и улучшением свойств металла. Требования к качеству сварных рельсов особенно возрастают с ростом скоростей движения. Для повышения надежности сварных стыков рельсов авторы работы [41] отмечает важность обеспечения высокой степени прямолинейности рельсов, особенно концевой кривизны. Весьма важно, чтобы металл сварного шва обладал высокими пластическими свойствами и живучестью.
Обобщение сведений по вопросу эксплуатационной стойкости рельсов отечественного и зарубежного производства, а также анализ причин повреждения рельсов в условиях эксплуатации на отечественных железных дорогах позволили выделить наиболее значимые требования к рельсам, предназначенным для работы в современных условиях: точность геометрии, высокая сопротивляемость хрупким разрушениям, высокая чистота стали, высокая усталостная прочность, удовлетворительная свариваемость, низкие остаточные напряжения.
Проблема повышения прочности рельсовой стали
Вопросам повышения прочности и твердости рельсов посвящено много российских и зарубежных работ, однако, до настоящего времени данная проблема не утратила своей актуальности.
Термическое упрочнение является одним из наиболее эффективных способов повышения эксплуатационной стойкости рельсов [61]. Упрочнение привело к повышению твердости головки углеродистых рельсов с перлитной структурой до 340 -ь 370 НВ, обеспечению прочности на уровне 1200 -г- 1300 Н/мм и относительного удлинения до 12 % [77, 78]. Это позволило повысить износостойкость и контактно-усталостную прочность рельсов.
Обобщение работ [79 — 82] по вопросу промышленных процессов закалки позволяет выделить три типа процесса закалки рельсов: объемная закалка, поверхностная закалка с повторного нагрева, поверхностная закалка с прокатного нагрева. Третий тип закалки является наиболее энергосберегающим и в последнее время становится наиболее конкурентоспособным. Наиболее устаревшим и имеющим ряд недостатков является первый тип термического упрочнения — объемная закалка в масле. Эта технология применяется в настоящее время на отечественных металлургических предприятиях — ОАО «НКМК» и ОАО «НТМК».
Оценивая уровень качества термически упрочненных рельсов отечественного производства, следует отметить, что по уровню твердости и прочности отечественные термоупрочненные рельсы из углеродистой стали практически находятся на одном уровне с зарубежными, а по ударной вязкости даже превосходят их. Отечественные рельсы уступают зарубежным только по прямолинейности и остаточным напряжениям. Указанные недостатки обусловлены способом выполнения термической обработки рельсов на отечественных предприятиях — объемным погружением несимметричного профиля рельса в охлаждающую среду — масло. С целью уменьшения коробления и обеспечения требуемых механических характеристик постоянно проводится работа по совершенствованию существующей технологии и ведется поиск новых способов термического упрочнения. Специалистами научно-исследовательских и учебных институтов (ФГУП «ВНИИЖТ»; ГНЦ РФ «ОАО» УИМ; ГОУ ВПО «СибГИУ»), а также производителями отечественного рельсового проката (ОАО «НКМК» ОАО « НТМК») проведены многочисленные работы и исследования по экспериментальному опробованию термической обработки с применением двухстороннего охлаждения рельсов в сжатом воздухе и потоке воды [83 — 85], горячей воде [86], водополимерной среде [87]. Кроме этого опробована технология термомеханического упрочнения с применением последующего водо-воздушного охлаждения [88] и дифференцированного охлаждения, включающего регулируемое охлаждение водо-воздушными смесями [89 — 92]. По мнению Е.А. Шура внедрение в промышленное производство новой технологии упрочнения возможно только при условии выполнения гарантированных свойств и соблюдения экологичности и безопасности процесса. В силу тех или иных причин не один из опробованных способов термического упрочнения в настоящее время не внедрен в отечественное производство.
Рельсовая сталь в основном содержит 0,7 0,9 % углерода и имеет структуру перлита с разной степенью дисперсности.
Оценивая структурное состояние рельсовой стали, автор работы [93] обращает внимание на то, что микроструктура рельсов, уложенных в 1857 г., и современных рельсов практически идентичны. В обоих случаях межпластиночное расстояние перлита составляет не более 0,3 мкм.
Благодаря внедрению термической обработки в промышленное производство стало возможно достижение высокой степени дисперсности перлита порядка 0,1 мкм. Авторы работы [94] считают, что при создании технологии термической обработки необходимо учитывать критерии перлитной структуры : размер колоний перлита (Б), межпластиночное расстояние (X) и объемную долю цементита (Уо). Натурные испытания и исследования подтвердили зависимость сопротивляемости износу и контактно-усталостным трещинам рельсовой стали от параметров микроструктуры. Установлено, что сопротивляемость износу стали слабо улучшается с увеличением доли цементита, умеренно возрастает при уменьшении размера колонии и значительно возрастает с уменьшением межпластиночного расстояния. Приблизительно такие же результаты получены при определении сопротивляемости стали усталостным разрушениям. С учетом критериев структурного состояния фирмой №£К созданы рельсовые стали типа СР («суперперлит»). Наиболее прочной из перлитных сталей этого класса, по данным японских исследований [95], считается сталь ТНН 370, имеющая прочность 1300 МПа, которая достигается в результате сложной термической обработки стали с содержанием углерода 0,82 %, обеспечивающей межпластиночное расстояние менее 0,2 мкм. Разработчики японской рельсовой стали считают, что полученный результат близок к теоретическому пределу прочности перлитной рельсовой стали.
Результаты зарубежных исследователей согласуются с выводами отечественных исследователей [96 — 107]. По мнению Е.А.Шура повышение эксплуатационной стойкости рельсов возможно только при получении однотипной структуры с минимальным межпластиночным расстоянием.
Зарубежные и отечественные исследователи считают, что достигнутый на рельсовой стали перлитного класса результат близок к своему теоретическому пределу и что на этом практически завершаются работы по дальнейшему повышению прочности рельсовой стали перлитного класса.
Дальнейшее увеличение прочности рельсовой стали связывают с ее легированием, а также сочетанием легирования и термической обработки.
Разработка низколегированных марок сталей для производства рельсов является весьма перспективным направлением повышения прочности. Накоплен большой материал по исследованию широкого спектра химических составов рельсовых сталей, легированных кремнием, марганцем, хромом, ванадием, никелем, молибденом, алюминием и другими элементами [108 — 114]. Однако, первоначально в отечественном производстве разработки не нашли внедрения в производство из-за высокой стоимости ферросплавов. Для повышения прочности в массовом производстве отечественных рельсов широкое распространение получила термическая обработка, благодаря более низкой цене энергоносителей, в то время как за рубежом исследования по разработке низколегированных рельсовых марок сталей продолжали проводиться. Успешность и перспективность этого направления в настоящее время подтверждается созданием ряда марок стали 900А, ТШП, N11812 [115].
В последнее время в России интерес к разработке низколегированных марок сталей — как одной из возможностей получения механических свойств, соизмеримых со свойствами объёмно-закалённых рельсов, и обеспечения прямолинейности, удовлетворяющей требованиям высокоскоростного движения, возрос многократно.
Ранние исследования рельсов типа Р65 из низколегированной стали марок М70ХГСФ, М70ХГСБ и М70ХГСМ в горячекатаном состоянии показали повышенные характеристики механических свойств и твердости, соизмеримые со свойствами термически упрочненных рельсов [116].
В период 1996-2001 гг. на ОАО «НТМК» изготовлены опытные партии рельсов из стали марок 76ХГВ, 76ХГСАФ, 72Х2ГСАФ. Исследования показали, что прочностные свойства рельсов из стали марок 76ХГВ, 76ХГСАФ приближаются к свойствам термоупрочненных рельсов из углеродистых сталей, а прочностные свойства и твердость рельсов из стали марки 72Х2ГСАФ с большим содержанием марганца, кремния, хрома и ванадия практически находятся на уровне термоупрочненных рельсов стандартного производства, за исключением ударной вязкости [117]. По результатам металлографических исследований структура рельсов из низколегированных сталей представляет собой пластинчатый перлит с выделениями карбонитридов ванадия и карбидов хрома в ферритных пластинках. Требуемая прямолинейность нетермоупрочненных рельсов из стали марки 72Х2ГСАФ достигалась путем применения дополнительного отпуска и последующей правки в роликоправильной машине.
Промышленное освоение рельсов из низколегированной стали марки Э76ХГФ (таблица 1.1) на ОАО «НКМК» показало не только возможность достижения удовлетворительных механических свойств (таблица 1.2), но и позволило обеспечить на рельсах требуемые прямолинейность и низкие остаточные напряжения без применения дополнительного отпуска [118].
Удовлетворительное качество и свойства также показали рельсы из низколегированной стали марки М 70ХГСФ (таблица 1.1), изготовленные на ОАО «МК Азовсталь» [119]. Механические свойства опытных рельсов в горячекатаном состоянии близки к свойствам термически упрочненных рельсов из углеродистой стали (таблица 1.2) по ГОСТ 24182.
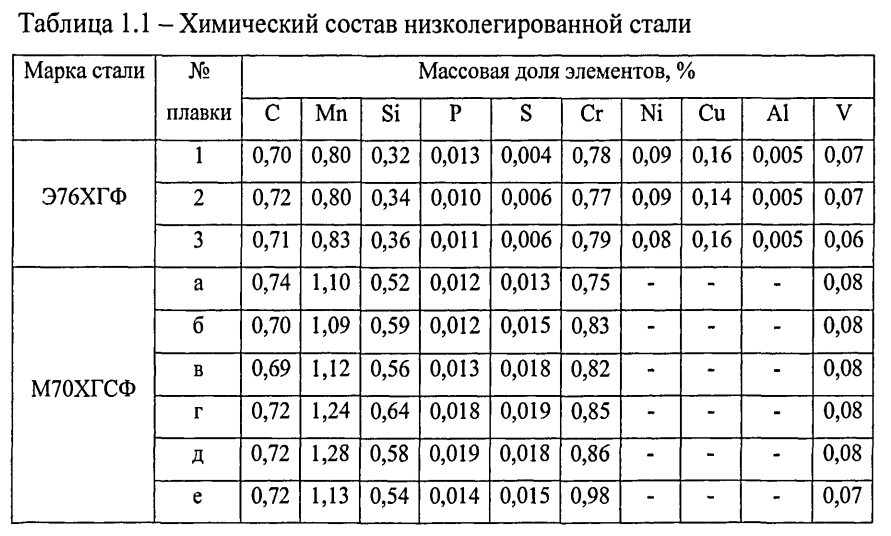
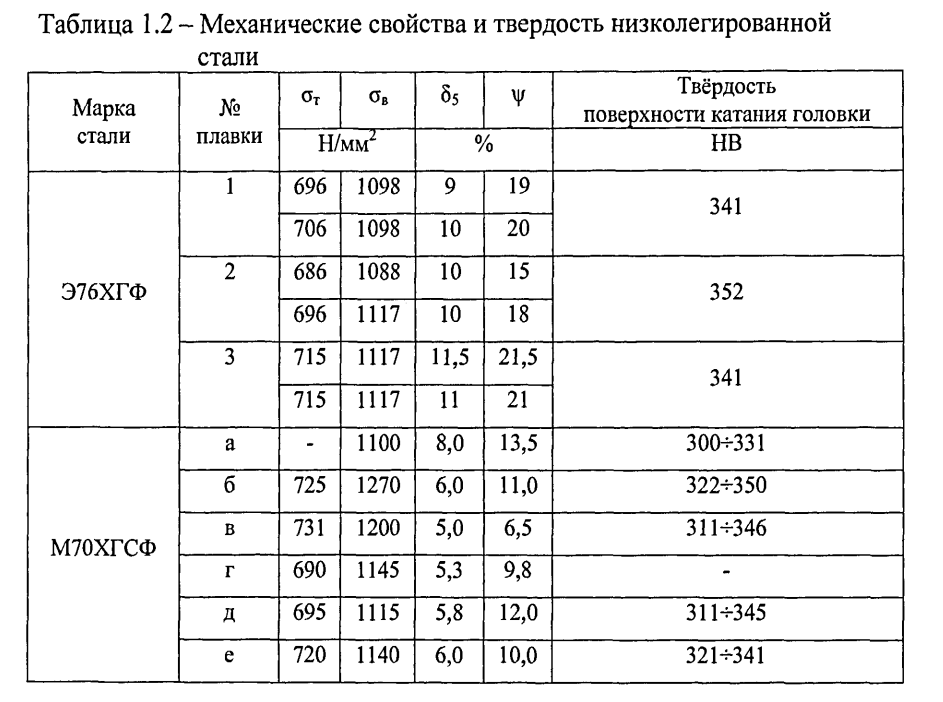
Производство рельсов из низколегированных рельсовых сталей является эффективным не только за счет повышения механических свойств, но и благодаря хорошим экономическим показателям. Затраты на производство низколегированных нетермоупрочненных рельсов примерно на 20 30 % ниже, чем углеродистых объёмно-закалённых рельсов.
Дальнейшее развитие низколегированных рельсовых сталей на основе перлитной структуры также практически исчерпало свои возможности. Как показывают исследования, возможности повышения механических свойств низколегированных углеродистых сталей ограничены предельными значениями твердости (352 НВ). Для достижения более высоких показателей требуется дополнительное легирование, либо термическая обработка для перехода на другую структуру. Как указывается в работе [120], новое поколение рельсовых сталей, по мнению японских исследователей, предпочтительно создавать на основе бейнитной структуры. Автор монографии [121] на основании обширных исследований сделал вывод, что наиболее перспективной является рельсовая сталь с пониженным содержанием углерода с минимальным межпластиночным расстоянием, а в предельном случае — со структурой бескарбидного бейнита.
Разработками бейнитных рельсовых сталей зарубежные исследователи занимаются достаточно давно, начиная с 90 г. XX века [122 -124], тогда как в России подобные работы находятся только на начальной стадии развития. Интерес к бейнитным сталям обусловлен их оптимальным сочетанием прочности, твердости и пластичности.
В обзорной работе [48] приведены химические составы рельсовых сталей с разным содержанием углерода и легирующих элементов. Выборочно химический состав бейнитных сталей приведен в таблице 1.3, их механические свойства — в таблице 1.4.
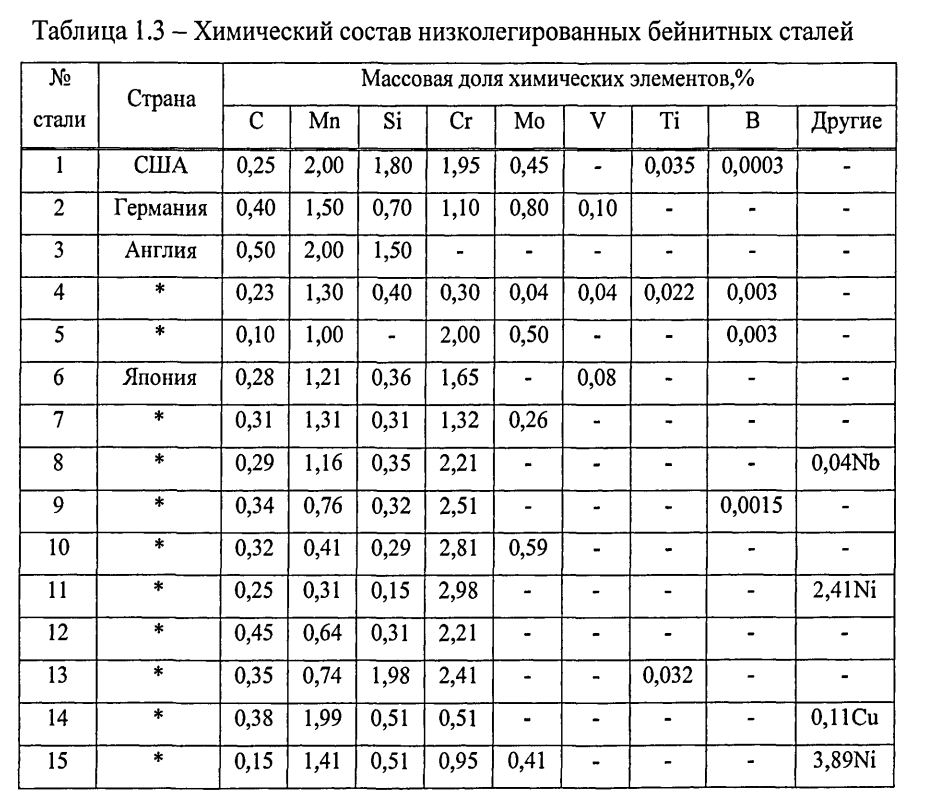
Представленные стали обеспечивают широкий спектр микроструктур в зависимости от химического состава и условий охлаждения, а именно: сталь № 1 в состоянии после прокатки имеет структуру реечного феррита с остаточным аустенитом по границам реек. Присутствует также высокодисперсный реечный мартенсит. В состоянии после закалки в воду структура состоит из реечного феррита без остаточного аустенита, с небольшим количеством игольчатого мартенсита.
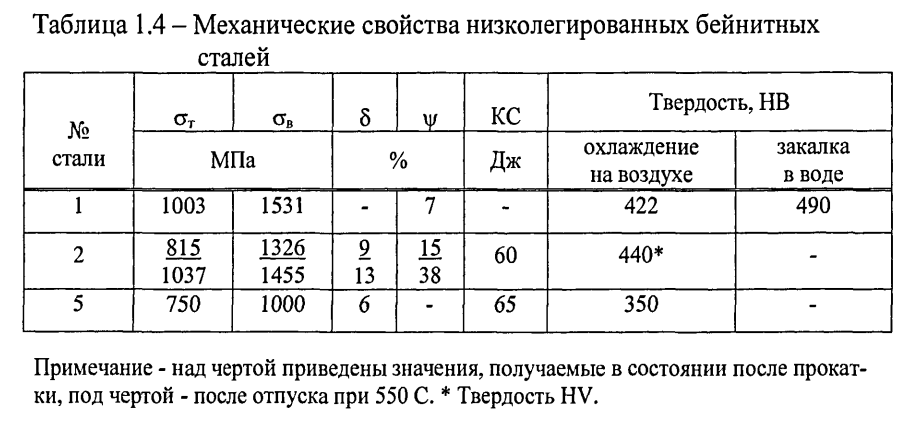
Сталь № 2 обеспечивает при охлаждении на воздухе с прокатного нагрева образование мелкоигольчатого бейнита, причем твердость стали составляет около 400 НУ. Указанная структура образуется по всему сечению рельса.
Сталь № 3 имеет бейнитную структуру реечного феррита с остаточным аустенитом по границе реек. Несмотря на относительно высокое содержание углерода, сталь не имеет в структуре карбидов из-за повышенного содержания кремния, который предотвращает их выпадение.
Сталь № 4 с прокатного нагрева охлаждается в потоке водяными струями с последующим самоотпуском. После такой термической обработки сталь имеет структуру отпущенного реечного мартенсита.
Сталь № 5 обеспечивает стабильность бейнитной структуры в широком диапазоне скоростей охлаждения, что необходимо при термической обработке сложного профиля рельса.
Стали № 6 -М5 обеспечивают получение бейнитной структуры при охлаждении в струе воздуха с прокатного нагрева. Твердость их колеблется в пределах НВ = 331-5- 425.
Структура бейнита и отпущенного мартенсита получена в отечественных рельсах из среднеуглеродистых сталей марок 40ХГСМ и 40ХГСН [125]. Рельсы из этих сталей после прокатки отличались высокой прочностью и ударной вязкостью при удовлетворительной пластичности (таблица 1.5).
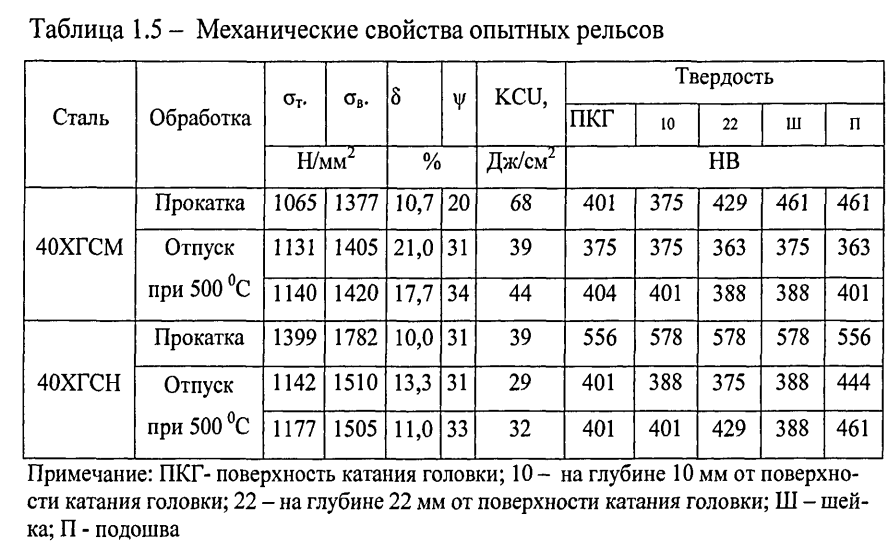
Отпуск при 500 °С несколько улучшил пластические характеристики, но ухудшил вязкость. Полученный первый опыт, однако, оказался неудачным, из-за высокой прочности рельсы в горячекатаном состоянии на существующем оборудовании практически не поддавались правке.
Из двух рассматриваемых в работе [100] вариантов структурного состояния (мартенсит или бейнит) в отношении рельсов предпочтение отдается бейнитной структуре. Меньшая износостойкость бейнитной структуры позволит, по мнению Е.А. Шура, реализовать большую контактно- усталостную долговечность рельсов за счет приближения к оптимальному соотношению между удалением (износом) поверхностных слоев металла и реализованной контактно-усталостной прочностью. Кроме этого указывается, что бейнитные структуры за счет пониженного содержания углерода могут противостоять термомеханическим повреждениям.
По данным работы [125], для рельсов из сталей бейнитного класса наиболее благоприятной в отношении вязкости разрушения считается смешанная структура, состоящая из нижнего бейнита и реечного мартенсита. В другой обзорной работе [48] отмечается, что высокую вязкость разрушения имеет структура верхнего бейнита, содержащая островки высокоуглеродистого мартенсита.
Несмотря на противоречивость взглядов, обобщение литературных данных по этому вопросу показало, что стали бейнитного класса, благодаря хорошему сочетанию прочности и вязкости, могут конкурировать со сталями перлитного класса. Бейнитные рельсовые стали перекрывают весь диапазон прочности современных углеродистых перлитных рельсовых сталей. Вязкость у бейнитных сталей выше, чем у перлитных. Это свидетельствует о том, что, например, при прочности 950 МПа в бейнитных сталях допустимая глубина трещины перед возникновением опасности хрупкого излома на 40 % больше, чем в перлитных [126].
При оценке бейнитных рельсов с позиции эксплуатационной стойкости также имеются противоречивые мнения. Одни исследователи [127] утверждают, что скорость износа рельсовых сталей, имеющих структуру бейнита, при контактном напряжении возрастает медленнее, чем скорость износа перлитных сталей.
Эксплуатационные испытания бейнитных рельсов, проведенные на Офотской железной дороге в Норвегии, являющейся самым грузонапря- женным участком (22 млн.тонн), показали высокую износостойкость бейнитных рельсов. По сравнению с рельсами из стали 900, срок службы бей- нитных рельсов повысился в восемь раз. Вместе с тем, конкретной оценки их по контактной усталостной прочности пока не получено. Характеризуя бейнитные рельсы как высокоизносостойкие, их рекомендуют использовать при перевозке тяжелых грузов с высокими нагрузками на ось.
По мнению других исследователей [128] бейнитные рельсы не выдерживают конкуренции с перлитными рельсами по износу и лучше всего проявили себя при эксплуатации на контактную усталость. Исследования показали, что при эксплуатации вагонов на типовых тележках износостойкость углеродистых рельсов возрастает с увеличением твердости. На этом же участке испытывали рельсы из бейнитной стали с твердостью 420 НВ. Результаты испытаний показали, что при обращении вагонов на типовых тележках рельсы из бейнитной стали изнашиваются быстрее на 50%, чем из углеродистой стали повышенного качества. При этом дефектов по контактной усталости на бейнитных рельсах не выявлено. В то же время существует еще одно мнение, что бейнитные рельсы имеют не только износостойкость, но высокое сопротивление усталостному разрушению [129].
Несомненно, что эти факты имеют важное значение для проведения дальнейшей поисковой работы по определению оптимального состава и структуры для обеспечения требуемых эксплуатационных свойств рельсов.
Создание нового поколения бейнитных рельсов требует исследований по установлению и определению параметров структуры, непосредственно влияющих на эксплуатационные характеристики рельсов.
Согласно фундаментальной теории, бейнит представляет собой смесь а — фазы (феррита) и карбида [130]. В отличие от перлита, в котором кристаллы обеих фаз, образующих эвтектоид, имеют пластинчатую форму, в бейните карбиды выделяются в другой форме, которая сильно зависит от температур. Поэтому в соответствии с кинетикой процесса бейнит подразделяют на верхний и нижний. В обзорной работе [48] бейнит подразделяют по морфологическим признакам как сферический, столбчатый, верхний, нижний, обратный. Согласно работе [131], структуру бейнита предлагают различать по трем типам: В1 — реечный (игольчатый) феррит с карбидами внутри реек; В2 — реечный (игольчатый) феррит с карбидами или остаточным аустенитом по границам реек; ВЗ — реечный (игольчатый) феррит с дискретными островками остаточного аустенита и /или мартенсита (никаких карбидов) по границам реек. По этой классификации нижний бейнит соответствует типу В1, верхний — типу В2, а гранулярный бейнит — типу ВЗ. Бейнитным комитетом Японского института стали предложены следующие модификации бейнита: полигональный, квази-полигональный, видманштеттовый, зернистый, бейнитный феррит и кубический мартенсит.
Сложный механизм бейнитного превращения соответственно затрудняет классификацию бейнитной структуры. Бейнит в общем случае состоит из различных структурных составляющих: а — фазы, карбидов, остаточного аустенита, имеющих разный химический состав, морфологию и дисперсность. Поэтому описание бейнита представляет собой наиболее сложную задачу.
Вопрос о влиянии легирующих элементов на структуру и механические свойства стали бейнитного класса в горячекатаном состоянии применительно к рельсам практически не изучен. В работе [127] указывается, что на структуру, образующуюся при бейнитном превращении без применения упрочняющей термической обработки, существенно влияет содержание углерода в стали. Стали, легированные хромом, никелем, молибденом, с содержанием углерода ниже ОД 0 % склонны к образованию гранулярного бейнита. Однако, эти стали могут иметь игольчатую структуру с мелкодисперсными выделениями карбидов, если основным легирующим элементом является марганец. Стали с содержанием углерода выше 0,25 % могут иметь игольчатую структуру нижнего или верхнего бейнита с выделением карбидов, иногда в них встречается перлит.
Как известно, структурным состоянием стали определяются ее механические свойства. Прочность бейнитной стали зависит от ширины фер- ритных реек и объемной доли цементита, а также участков остаточного ау- стенита и /или мартенсита. В обоих случаях, чем ниже температура превращения, тем тоньше структура и тем выше прочность стали.
Для большинства низколегированных сталей температуру начала бейнитного превращения определяют по эмпирической формуле:

Из формулы (1.1) следует, что наиболее сильное влияние на температуру бейнитного превращения оказывает углерод. Затем следует марганец, молибден, хром, никель.
В работе [132] указывается, что марганец, в первую очередь, задерживает перлитное превращение и снижает кривую бейнитного превращения. Молибден повышает бейнитную прокаливаемость. Хром более эффективен в повышении бейнитной прокаливаемости и при содержании его около 2 % обеспечивается бейнитная структура при наименьшей скорости охлаждения. Наилучшее сочетание свойств можно достичь при легировании стали одновременно хромом, марганцем и кремнием (в пределах 1 1,5 %). Углерод также эффективен в понижении температуры превращения и увеличении бейнитной прокаливаемости. Для понижения температуры превращения и получения структуры, обеспечивающей удовлетворительное сопротивление хрупкому разрушению, содержание легирующих элементов должно составлять около 3,5 %. При этом для повышения ударной вязкости и хладостойкое™ предпочтение отдается хрому по сравнению с марганцем и никелем. Для более точного регулирования температуры превращения целесообразнее легировать хромом и марганцем. Такое легирование стали особенно при низком содержании углерода обеспечивает хорошие вязкость и пластичность, малую склонность к отпускной хрупкости и хрупкому разрушению.
При изучении низкоуглеродистых сталей немаловажная роль отводится микролегирующим добавкам ванадия, ниобия, алюминия, обеспечивающим получение мелкозернистой стали и повышения ее хладостойко- сти. При комплексном легировании стали, особенно при сочетании карби- дообразующих и некарбидообразующих элементов, достигается весьма высокие прочность и вязкость бейнитной стали.
В настоящее время вся рельсовая сталь, производимая на отечественных металлургических предприятиях, подвергается микролегированию ванадием (0,04 0,08%). Наряду с исследованием влияния ванадия, проводились работы по изучению влияния азота на свойства рельсовой стали. Показано, что введение в сталь азота (до 0,014 %) способствует выделению более дисперсных карбонитридов ванадия, измельчению аустенитного зерна [113].
В обзорной работе [133] особенно указывается на положительное влияние ванадия как элемента, реализующего два механизма: измельчения зерна и дисперсионное упрочнение. Значение этого элемента особенно возрастает при применении электродугового способа выплавки, при котором в стали отмечается повышенное содержание азота, приводящего во многих случаях к старению и охрупчиванию стали. При введении ванадия в сталь нейтрализуется вредное влияние азота, делая сталь не подверженной старению и используя азот в качестве экономически эффективного легирующего элемента для оптимизации выделения дисперсных фаз.
В зависимости от химического состава и температуры превращения бейнитные стали могут иметь прочность в широком диапазоне значений. Ирвин и Пиккеринг, исследовавшие низкоуглеродистые бейнитные стали, установили, что механические свойства сталей бейнитного класса определяются дисперсностью пластинок феррита и карбидов. Многочисленные исследования показывают, что наилучшее сочетание свойств — прочности, пластичности и вязкости имеет структура нижнего бейнита. Для получения нижнего бейнита необходимо существенно задержать процесс образования полигонального феррита, сдвинув начало превращения вправо, и расширить область бейнитного превращения. Но как показывает практика, при непрерывном охлаждении получить структуру нижнего бейнита достаточно сложно.
Как видно, применение стали бейнитного класса для производства рельсов необходимо рассматривать как наиболее перспективный и эффективный способ повышения механических свойств, но требующий дополнительных исследований для достижения оптимальной структуры и механических свойств с целью обеспечения требуемых эксплуатационных свойств рельсов.
Для создания рельсов из стали бейнитного класса необходим системный подход и комплексные металлофизические исследования. Системный подход заключается в упорядочении состава стали по прочностным и пластическим свойствам. На основе металлофизических исследований требуется установить параметры структуры с целью доведения ее эксплуатационных свойств до требований потребителя. При таком подходе задачу достижения сбалансированного комплекса механических характеристик бейнитных рельсов можно решить без ухудшения других очень важных характеристик таких, как свариваемость и прямолинейность.
Анализом литературных данных установлено, что несмотря на достигнутое повышение качества железнодорожных рельсов, оно является недостаточным для обеспечения высокого жизненного цикла рельсов в современных условиях увеличения скоростей и нагрузок. Для обеспечения безопасности и высокой надежности движения поездов необходимо, чтобы рельсы имели высокий уровень прямолинейности; повышенное сопротивление хрупким разрушениям, высокую усталостную прочность, удовлетворительную свариваемость и низкие остаточные напряжения.
Существующая на отечественных металлургических комбинатах объёмная закалка в масле не обеспечивает требуемое качество рельсов в полном объеме. Замена устаревшей технологии термической обработки на легирование стали позволяет исключить коробление, возникающее при закалке под влиянием остаточных термических и структурных напряжений, и обеспечить на рельсах требуемые механические свойства и прямолинейность.
Низколегированные стали перлитного класса марок 76ХГВ, 76ХГСАФ, 72Х2ГСАФ, 76ХГФ, не подвергаемые термическому упрочнению, показали ограниченные возможности в достижении требуемых для рельсов прочности, твердости и относительного удлинения. Другой отрицательной стороной рельсов из низколегированной перлитной стали является их низкая хладостойкость.
Применение сталей бейнитного класса является одним из перспективных направлений в достижении высоких показателей прочности, твердости, пластичности и ударной вязкости рельсов. В то же время имеется противоречивость в результатах исследования эксплуатационных свойств бейнитных рельсов, в связи с этим четко не определена область их применения. Также отсутствует единая точка зрения о необходимом комплексе механических свойств бейнитных рельсов и допустимом структурном состоянии рельсов из стали бейнитного класса, что затрудняет выбор их оптимальных составов.
Таким образом, для определения химического состава рельсовой стали бейнитного класса, позволяющего заменить упрочняющую термическую обработку и получить на рельсах сбалансированный комплекс механических свойств, необходимо проведение комплексного исследования, направленного на выявление взаимосвязи структурного состояния металла с его механическими свойствами.
Выводы и постановка задач исследования
Рельсы являются главным элементом железнодорожного полотна от содержания, качества, стойкости которого в значительной степени зависит безопасность движения поездов, сохранность людей и грузов.
В настоящее время в России и за рубежом достигнуты значительные успехи в области повышения металлургического качества и эксплуатаци-онных свойств рельсов из сталей перлитного класса. При этом одним из наиболее перспективных направлений развития рельсовых сталей является разработка сталей бейнитного класса. Проблема создания сталей бейнит- ного класса для производства рельсов является малоизученной и бурно развивающейся областью научных исследований как в России, так и за ру-бежом. Переход от традиционных технологий производства рельсов из вы-сокоуглеродистых сталей перлитного класса на низколегированные из ста-лей бейнитного класса является весьма заманчивым и перспективным как для производителей, так и для потребителей рельсового металла. Рельсы из сталей бейнитного класса обладают повышенным комплексом механиче¬ских и эксплуатационных свойств, более технологичны, при экономном легировании охарактеризованы пониженной себестоимостью, позволяют отказаться от экологически вредных технологий объемной закалки в масле.
В рамках настоящего диссертационного исследования выделены сле-дующие задачи исследования:
- Исследовать особенности влияния легирующих элементов: угле¬рода, марганца, кремния и хрома на механические свойства и структурооб- разование сталей бейнитного класса.
- Исследовать влияние различных видов термической обработки на свойства и структуру сталей бейнитного класса.
- Разработать химический состав и технологию термической обра-ботки железнодорожных рельсов из стали бейнитного класса.
- Внедрить и освоить технологию производства железнодорожных рельсов из сталей бейнитного класса в условиях ОАО «НКМК».
- Провести полигонные испытания и установить особенности эво-люции структуры и механических свойств стали марки Э30ХГ2САФМ при эксплуатации рельсов в пути.
Список литературы
- Раскисление и модифицирование рельсовой стали /В.А. Поляничка [и др.] //Металлург. — 1990. — № 1. — С.28.
- Рельсы из микролегированной азотом стали /Г.Я. Левченко [и др.] //Сталь.- 1994.- № 1.- С. 26 — 28.
- Поляничка В.А. Ресурсосберегающая технология легирования рельсо¬вой стали ванадием /В.А. Поляничка, A.B. Пан, Д.К. Нестеров //Сталь. — 1993.-№5.- С. 26-28.
- Дерябин A.A. Совершенствование технологии раскисления рельсовой стали цирконийсодержащими сплавами /A.A. Дерябин, В.Е. Семенков, Б.И. Топычканов //Сталь.-1990.- №5.- С. 18 — 22.
- Шур Е.А. Влияние неметалличеких включений на разрушение рельсов и рельсовой стали /Е.А. Шур, С.М. Трушевский //Неметаллические вклю¬чения в рельсовой стали : сб. науч. тр.- Екатеринбург: ГНЦ РФ ОАО «УИМ», 2005.- С. 87-94.
- Улучшение качества рельсов из стали, раскисленной алюминием / A.A. Дерябин [и др.] // Сталь.-1997.- № 7.- С. 50 — 55.
- Влияние технологии выплавки и температуры на микростроение и структурно — чувствительные свойства жидкой рельсовой стали /A.A. Дерябин [и др.] // Сталь.-2004.- № 3.- С. 20 — 22.
- Разработка технологии производства рельсовой стали на установке печь — ковш / В.В. Павлов [и др.] // Сталь.-2004.- № 5.- С. 50 — 52.
- Могильный В.В. Качество рельсовой электростали повышенной чисто¬ты / В.В. Могильный, H.A. Козырев, A.JI. Никулина // Сталь,-1999. -№ 3.- С. 53-56.
- Дерябин A.A. Влияние модифицирования рельсовой стали барием и кальцием на свойства рельсов /A.A. Дерябин [и др.] // Влияние свойств металлической матрицы на эксплуатационную стойкость рельсов: сб. науч. тр. Екатеринбург: ГНЦ РФ ОАО «УИМ», 2006.- 235с.
- Дерябин A.A. Исследование эффективности процессов раскисления, мо¬дифицирования и микролегирования рельсовой стали / A.A. Дерябин, А.Б. // Сталь.- 2000.- №11.- С. 38-43.
- Повышение качества рельсов раскислением комплексными сплавами, содержащими кальций и титан /A.A. Дерябин [и др.] // Сталь. -1983.- № 12.- С.59-63.
- Снижение загрязненности рельсов оксидными включениями при рас¬кислении стали FeSiCa+FeSiZr /A.A. Дерябин [и др.] // Металлург.- 1981.-№ 2,- С.30-32.
- Г.А. Галицын, В.И. Сырейщикова // Влияние свойств металличе¬ской матрицы на эксплуатационную стойкость рельсов: сб.науч. тр. — Екатеринбург: ГНЦ РФ ОАО «УИМ», 2006.- С. 64 — 80.
- Новые технологические процессы производства для Сибири и Севера /
- П. Дементьев [и др.] // Современные проблемы совершенствования работы железнодорожного транспорта: межвузовский сб. нучн. тр.- М.: РГОТУПС, 1999.-С 156-157.
- Снитко Ю.П. Расчет растворимости карбонитридов в рельсовой стали. / Ю.П. Снитко, A.B. Введенский, Н.В. Королев //Материалы юбилейной рельсовой комиссии: сборник докладов. — Новокузнецк, 2002.- С. 97 — 105.
- Медовар Л.Б. Бейнитные стали для рельсов // Проблемы СЭМ.- 1998.- №3.- С. 16-20.
- Пути повышения надежности рельсов // Железные дороги мира. — 1999.- №8.- С.64-68.
- Стали для рельсов высокоскоростных линий // Железные дороги мира. — 2000. — № 8. — С.67-70.