Сейчас ваша корзина пуста!
Оборудование и методика экспериментальных исследований
Цикл статей:
Глава 1 — Разработка химического состава и технологии термической обработки железнодорожных рельсов из стали бейнитного класса
Глава 2 — Теоретические предпосылки разработки химического состава сталей бейнитного класса
Глава 3 — Оборудование и методика экспериментальных исследований
Глава 4 — Исследование влияния различных видов термической обработки на структуру и свойства сталей бейнитного класса
Глава 6 — Служба железнодорожных рельсов из сталей бейнитного класса
Материал, методика и оборудование для экспериментальных
исследований
В соответствии с поставленными задачами исследования и учетом теоретических предпосылок по разработке стали бейнитного класса в качестве объектов исследования были выбраны низко-и среднеуглеродистые стали, легированные марганцем, кремнием, хромом и молибденом. В качестве микролегирующих добавок использовали ванадий, вводимый совместно с азотом.
Исследование сталей с целью последовательного исключения бесперспективных составов проводили поэтапно.
На первом этапе исследовали влияние легирующих элементов на механические свойства. На основании полученных результатов осуществляли выборку составов по следующим механическим характеристикам, соответствующим требованиям категории рельсов Т1 по ГОСТ Р 51685-2000: временное сопротивление разрыву стали должно быть более 1200 Н/ мм , относительное удлинение — более 8 %, относительное сужение — более 25 %, ударная вязкость при плюс 20 С — более 25 Дж/ см.
На следующем этапе осуществляли уточнение и корректировку выбранных составов на серии лабораторных плавок.
На заключительном этапе работы проверку выбранного состава осуществляли на промышленных плавках с исследованием механических свойств и структурного состояния на полнопрофильных рельсах.
Согласно первому этапу работы исследование проводили на металле 40 плавок. Сталь выплавляли в лабораторной индукционной печи, разливали на слитки весом 2,5 кг, в которых варьировали содержание одного легирующего элемента при неизменной концентрации других элементов согласно схеме, приведенной в таблице 3.1.
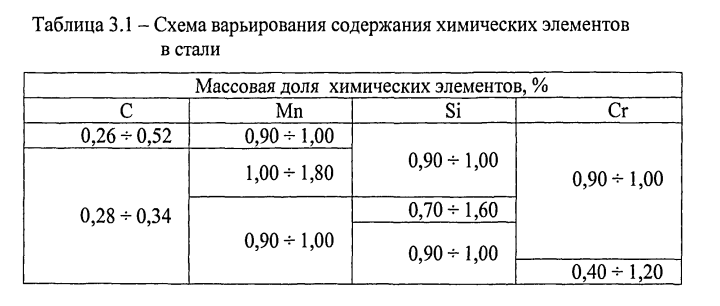
Слитки пластически деформировали в заготовки сечением 14x14x1000 мм, которые затем подвергали нагреву до температуры 880 — 890 °С и охлаждению на воздухе. Из термически обработанных заготовок изготовили разрывные и ударные образцы.
Из рассмотренных 40 плавок требуемый комплекс механических свойства обеспечивался при следующем содержании химических элементов, масс. %: 0,28-0,34 С; l,00-l,4Si; 1-1,8 Мп; 0,9 — 1,10 Cr.
Корректировку и уточнение выбранных составов проводили на металле 10 лабораторных плавок. При этом помимо заданных пределов ряд плавок провели с высоким содержанием углерода при разной концентрации легирующих элементов для изучения их совместного влияния на структу- рообразование стали. Химический состав полученных сталей приведен в таблице 3.2.
Лабораторные плавки проводили в 40 кг — индукционной печи и разливали на слитки размером 120×120 мм и весом 38 кг. Слитки пластически деформировали в заготовку размером 40x70x1000 мм. Поперечное сечение заготовки было максимально приближено к сечению головки рельса. Для устранения влияния ковки пластины подвергали нагреву до температуры 880 — 890 °С и последующему охлаждению на воздухе.
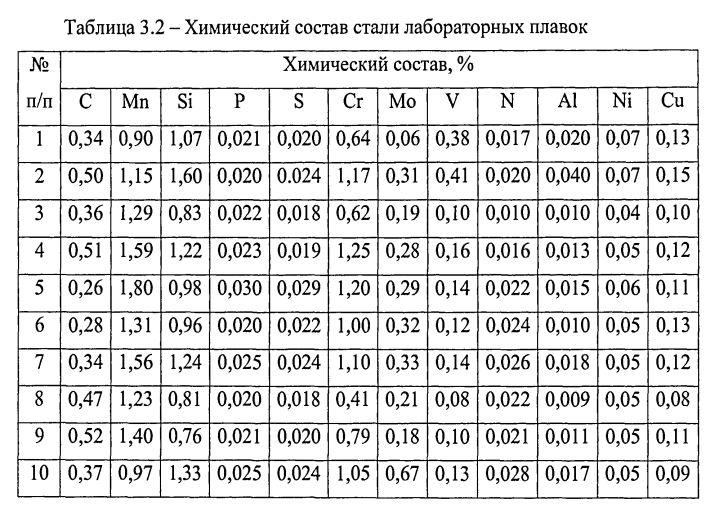
Для изучения влияния ускоренного охлаждения и отпуска на механические свойства стали лабораторных плавок подвергали закалке в масле и отпуску. Закалку проводили с температуры 860 °С, отпуск при температурах 300-550 °С.
Для проведения окончательной корректировки химического состава провели исследования на полнопрофильных рельсах двух промышленных плавок. Химический состав стали опытных плавок приведен в таблице 3.3.
В промышленных условиях выплавку стали осуществляли в 100 — тонной дуговой электропечи ДСП — 100И7 с обработкой на агрегате комплексной обработки стали (АКОС). Ферромолибден присаживали в завалку. Феррохром марки ФХ — 100 в количестве 1600 кг присаживали в печь. Остальные легирующие: ферросилиций марки ФС65, силикомарганец, а также феррованадий (280 кг, в том числе 80 кг азотированного) присаживали в ковш во время выпуска плавки из печи.
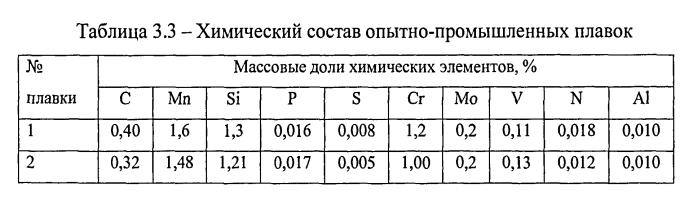
В процессе обработки на АКОС в ковш для корректировки химического состава металла присаживали силикомарганец, ферросилиций и феррохром. Доводку содержания углерода в металле производили путем вдувания коксовой пыли. Силикокальций для окончательного раскисления металла вводили в виде порошковой проволоки. Разливку производили по схеме одиночных плавок. Температура метала в печи перед раскислением и перед выпуском составила 1700 °С, перед установкой на ППС — 1565 °С, в промежуточном ковше -1511 + 1520 °С.
Разливку металла производили на 4-х ручьевых MHJI3 с сечением кристаллизатора 330×300 мм. После порезки на мерные длины HJT3 незамедлительно транспортировали в ямы замедленного охлаждения, где заготовки остывали под крышками в течение 72 часов, уложенные в 3 и 4 ряда между металлом рядовых плавок.
Нагрев HJT3 под прокатку осуществляли до температуры 1200 °С. Нагретые заготовки прокатывали на рельсовый профиль типа Р65. Температура рельсового раската на выходе из чистовой клети составляла 980 + 1050 °С. После порезки рельсового раската на длину ~ 25060 мм и отбора проб рельсы охлаждали на стеллаже в положении «лежа на боку», плотно придвинув друг к другу. Охлажденные рельсы подвергали правке на роли- коправильной машине. Правленые рельсы после отбора исследовательских проб порезали на конечную длину 24995 ± 5мм.
Принятые рельсы подвергали нормализации и отпуску либо отпуску. Температура нагрева под нормализацию составила 870 + 880 °С. Нагрев рельсов под нормализацию осуществляли в нагревательной печи РБЦ,
сформировав их в пакет по 5+9 шт. При нагреве рельсов температурный режим по зонам печи соответствовал требованиям ТИ РБ — 043 — 2004 и не отличался от технологии нагрева стандартных рельсов из стали Э76Ф под закалку. После выдачи из печи рельсы охлаждали пакетом на стеллаже выдачи до температуры цеха. Охлажденные до температуры цеха рельсы подвергли отпуску при температуре 350 °С в течение 2,5 часов.
После термической обработки рельсы подвергали правке на РПМ по обычному режиму, предусмотренному для объёмно-закалённых рельсов из стали Э76Ф. После правки от опытных рельсов производили отбор проб. На заключительной стадии опытные рельсы аттестовывали по качеству поверхности, геометрии и прямолинейности.
На полнопрофильных бейнитных рельсах исследовали неметаллические включения, макро- и микроструктуру, определяли механические свойства, твердость, копровую прочность и остаточные напряжения.
Механические свойства и твердость опытных рельсов сравнивали с механическими свойствами объёмно-закалённых рельсов из стали марки Э76Ф по ГОСТ Р 51685 — 2000, химический состав и механические свойства которых приведены соответственно в таблицах 3.4 и 3.5.
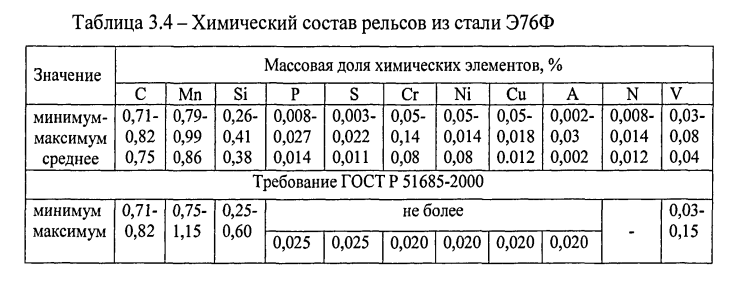
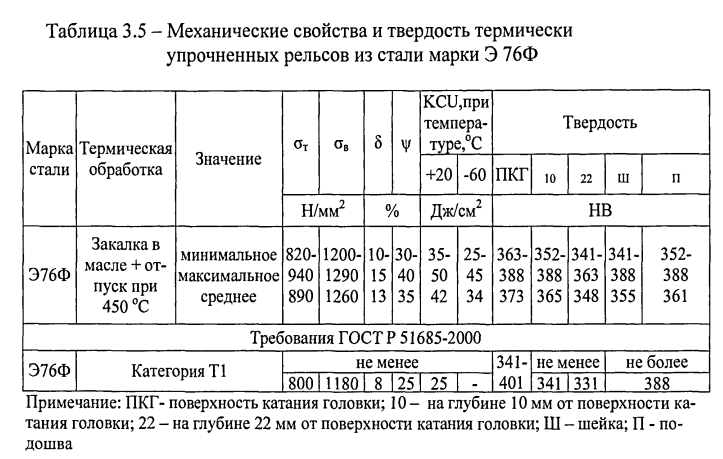
Методы исследований
Металлографический метод
Неметаллические включения, величину зерна и микроструктуру сталей бейнитного класса определяли с помощью оптического микроскопа NEOPHOT-21 при увеличении хЮО -И ООО. Для выявления микроструктуры применяли 4 % спиртовой раствор азотной кислоты.
Неметаллические включения стали определяли в соответствии с требованиями ГОСТ Р 51685 — 2000 и методом Ш по ГОСТ 1778 -70.
Шлифы для исследования готовили на образцах, вырезанных из верхней выкружки головки, из середины шейки и края пера подошвы. Процесс приготовления шлифов включал следующие операции: вырезку образцов на отрезном станке, шлифование на плоскошлифовальном станке, полирование на полировальном станке.
Электронно-микроскопическое исследование Электронно-микроскопическое исследование проводили на электронном микроскопе JEC-200CX, а также на растровом электронном микроскопе-микроанализаторе LEO EVO-40. Электронно-микроскопическое исследование, проводимое с помощью микроскопа ШС- 200СХ, осуществляли прямым методом на фольгах, вырезанных на глубине 8 — 10 мм от поверхности катания головки рельса.
Метод макроструктурного анализа
Макроструктуру стали и макродефекты выявляли методом глубокого травления поперечных и продольных темплетов в 50 % водном растворе соляной кислоты в соответствии ОСТ 14 -1 — 235 — 91 «Сталь. Метод контроля макроструктуры непрерывнолитой заготовки для производства сортового проката и трубных заготовок», РД 14 — 2Р — 5 — 2004 «Классификатор дефектов макроструктуры рельсов, прокатанных из непрерывнолитых заготовок электростали» и ГОСТ Р 51685 — 2000 «Рельсы железнодорожные. Общие технические условия».
Травление темплетов осуществляли в травильной ванне. Поверхность, подвергаемую глубокому травлению, предварительно строгали или шлифовали. Темплеты перед травлением нагревали в ванне подогрева до температуры 60 -5- 80 °С. Нагретые темплеты помещали в ванну с травильным раствором, нагретым до 60 — 80 °С. Длительность травления темплетов составляла 25 30 мин. После травления темплеты промывали горячей водой с последующей нейтрализацией горячим содовым раствором.
Методы испытаний
Механические испытания
Для определения механических свойств проводили испытания на растяжение и ударный изгиб. Испытания на растяжение осуществляли на разрывной машине 7-250 при комнатной температуре по ГОСТ 1497- 84 на цилиндрических образцах диаметром (1 = 6 мм с расчетной длиной 1 = 30 мм, которые вырезали вдоль направления прокатки из зоны выкружки головки рельсового профиля.
Испытания образцов на ударный изгиб при комнатной температуре (20 0 С ) и минус 60 °С проводили на копровой машине МК- 15 в соответствии с требованиями ГОСТ 9454 — 78. Образцы размером 10x10x55 мм с 11-образным надрезом (11= 1мм и глубина надреза 2 мм) для испытания вырезали вдоль направления прокатки из зоны выкружки головки рельсового профиля. Результаты механических испытаний сравнивали с требованиями ГОСТ Р 51685-2000.
Измерение твердости
Измерение твердости образцов из стали лабораторных плавок и рельсов опытно-промышленных плавок осуществляли по ГОСТ 9012 — 59 на твердомере Бринелля (ТБ) путём вдавливания стального шарика диаметром 10 мм при нагрузке 29430 Н.
Для измерения твердости металла лабораторных плавок и рельсов опытно-промышленных плавок соответственно подготовили образцы размером 40x70x30 мм и рельсовые поперечные темплеты.
Твердость рельсовых поперечных темплетов замеряли в соответствии с требованиями ГОСТ Р 51685 — 2000. Замеры твёрдости на поверхности головки поперечного темплета осуществляли после предварительной зачистки обезуглероженного слоя на глубину 0,6 + 0,8 мм. Твёрдость в поперечном сечении рельсовых темплетов определяли в пяти точках: в головке на расстоянии 10 и 22 мм от поверхности катания по вертикальной оси рельсового профиля, в середине шейки и на двух перьях подошвы на расстоянии 9 мм от их боковых граней.
Твердость по Роквеллу (ГОСТ 9013-59) определяли вдавливанием ин- дентора — алмазного конуса с углом при вершине 120° и радиусом закругления 1,2 мм на образцах с плоской поверхностью при стандартной нагрузке для шкалы «С» (Р0=ЮОН, Р1=1400 Н, Р= 1500Н). Измерение твердости осуществляли по точкам, указанным по сечению головки (рисунок 3.1).
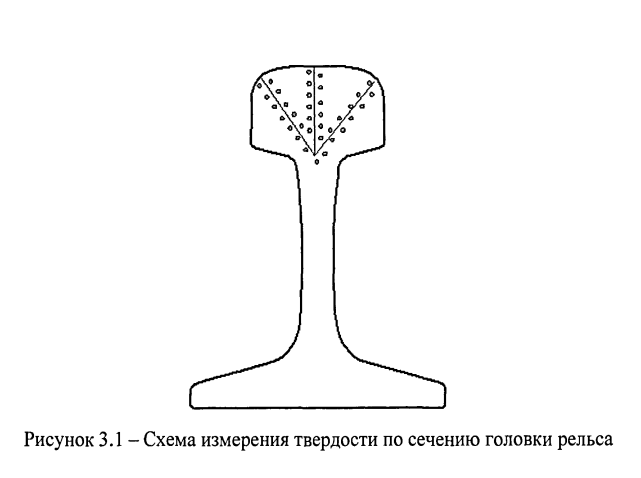
Копровые испытания
Копровые испытания проводили в соответствии с ГОСТ Р 51685 — 2000 на полнопрофильных пробах длиной 1300 ± 50 мм при температуре минус 60 °С и падении груза (1000 ± 3 кг) с высоты 9 м. Копровые испытания осуществляли на рельсоиспытательном копре.
После удара груза измеряли стрелу прогиба испытываемой пробы путем прикладывания линейки длиной 1 м ребром к поверхности катания головки рельса.
Измерение остаточных напряжений
Измерение остаточных напряжений осуществляли методом вырезки паза в соответствии с ГОСТ Р 51685 — 2000. По этому методу пробу длиной 600 ± 3 мм, отрезанную на расстоянии не менее 1500 мм от торца рельса, надрезали вдоль шейки по нейтральной оси рельса на длину 400 ± 3 мм. Ширина прорезаемого паза должна быть не менее 6 ± 1 мм. Уровень остаточных напряжений определяли по расхождению паза.
Список литературы
- Снижение загрязненности рельсов оксидными включениями при рас¬кислении стали FeSiCa+FeSiZr / А.А. Дерябин [и др.] // Металлург.- 1981.-№2,- С.30-32.
- Синельников В.А. Технологические аспекты повышения качества и уровня потребительских свойств железнодорожных рельсов / В.А. Си¬нельников, Г.А. Филиппов // Металлург.- 2001.- № 10.- С.50 -52.
- Панасюк В.В. Предельное равновесие хрупких тел с трещинами./В.В. Панасюк.- Киев: Наукова думка, 1968.- 246 с.
- Палатник JI.C. Структура и динамическая долговечность сталей в усло¬виях тяжелого нагружения./ JI.C. Палатник, Т.М. Равицкая, Е.П. Остров¬ская.- Челябинск: Металлургия, 1988.-160с.
- Воротилкин A.B. Основные причины износа в системе колесо-рельс // ТРИБОФАТИКА: сб.док.- Иркутск: ИрГУПС, 2005.- Том.1. — С. 415-417.
- Сравнение затрат жизненного цикла обычных и термоупрочненных рельсов // Железные дороги мира.- 2006.- № 3.- с.71-74.
- Хрупкий излом рельса //Путь и путевое хозяйство.- 1993.- № 8.- с. 9 -10.
- Сосновский J1.A. Теория накопления износоусталостных повреждений. / J1.A. Сосновский, A.B. Богданович.- Гомель,- 2000.- 60 с.
- Сосновский JI.A. Трибофатика: износоусталостные повреждения в про¬блемах ресурса и безопасности машин ./J1.А. Сосновский, H.A. Махутов. — М. — Гомель: ФЦНТП «Безопасность», НПО «ТРИБОФАТИКА».- 2000.- 304 с.
- Богданович П.Н. Трение и износ в машинах./ П.Н. Богданович, В.Я. Прушак. — Минск: Вышэйшая школа, 1999.- 376с.
- Сосновский JI.A. Проблема колесо/рельс с позиции трибофатики / J1.A. Сосновский, В.П. Сенько // Влияние свойств металлической матрицы на эксплуатационную стойкость рельсов: сб. науч. тр.- Екатеринбург: ГНЦ РФ ОАО «УИМ», 2006.- С. 215 — 228.
- Муравьев Е.А. Динамика образования внутренних напряжений и ис¬кривленности рельсов при объемной закалке их в масле /Е.А. Муравьев, М.С. Михалев // ЦНИИ МПС.- М., 1973.- Вып.491С.42-49.
- Технология термообработки рельсов для работы в особо тяжелых усло¬виях эксплуатации /Д.К. Нестеров [и др.] // Сталь.- 1989,- С.79-82.
- Золотарский А.Ф. Термически упрочненные рельсы / А.Ф.Золотарский, Я.Р. Раузин, Е.А. Шур. — М.: Транспорт. 1976,264с.
- Лемпицкий В.В. Производство и термическая обработка железнодорож¬ных рельсов / В.В. Лемпицкий, Д.С. Казарновский, C.B. Губерт. — М.: Металлургия, 1972. — 272 с.
- Недорезов И.В. Обзор промышленных процессов закалки рельсов и ос¬таточных напряжений в них // Производство проката.- 2001.- №6.- С. 13-18.