Сейчас ваша корзина пуста!
Исследование влияния различных видов термической обработки на структуру и свойства сталей бейнитного класса
Цикл статей:
Глава 1 — Разработка химического состава и технологии термической обработки железнодорожных рельсов из стали бейнитного класса
Глава 2 — Теоретические предпосылки разработки химического состава сталей бейнитного класса
Глава 3 — Оборудование и методика экспериментальных исследований
Глава 4 — Исследование влияния различных видов термической обработки на структуру и свойства сталей бейнитного класса
Глава 6 — Служба железнодорожных рельсов из сталей бейнитного класса
Особенности влияния химических элементов на механические свойства сталей бейнитного класса
Выбор химического состава стали для производства рельсов должен основываться на экономической целесообразности и необходимости получения сбалансированного комплекса механических свойств. Для рационального научно-обоснованного выбора необходимо установить закономерности влияния каждого легирующего элемента на механические характеристики стали.
В данном разделе представлены результаты исследования влияния содержания углерода, марганца, кремния и хрома на механические свойства стали. На основании экспериментальных данных установлено, что с повышением содержания углерода от 0,26 до 0,51% прочностные свойства стали повышаются, а именно, предел текучести возрастает в среднем от 850 до 1490 Н/мм2, временное сопротивление разрыву от 1200 до 1700 Н/мм (рисунок 4.1). Повышение прочностных свойств отрицательно сказывается на уровне пластических характеристик и ударной вязкости стали. При увеличении содержания углерода от 0,26 до 0,51% относительное удлинение снижается от 15 до 4 %, относительное сужение — от 27 до 2% (рисунок 4.2). Ударная вязкость как при комнатной температуре, так и при минус 60 °С уменьшается почти в 1,5 раза (рисунок 4.3). На основании полученных результатов установлено, что максимально допустимое содержание углерода в стали, легированной комплексом Мп — 81 — Сг, не должно превышать 0,40 %. Наиболее оптимальное сочетание прочности, пластичности и ударной вязкости наблюдается у стали при содержании углерода 0,28 — 0,34 %. При таком содержании углерода механические свойства наиболее близки к свойствам объёмно-закаленных рельсов из стали марки Э76Ф.
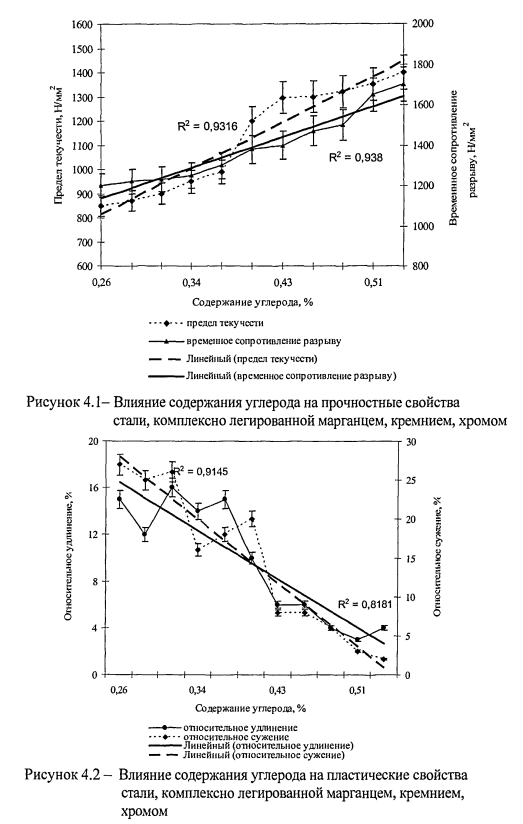
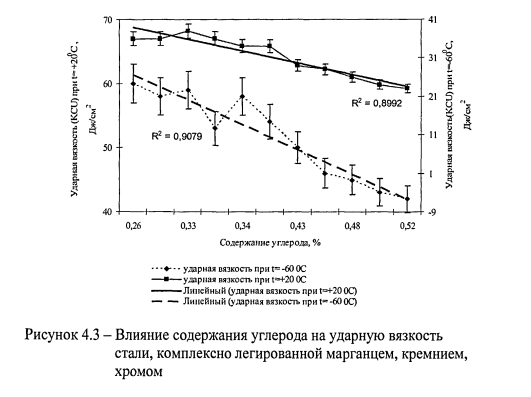
При установленном содержании углерода (0,28 0,34 %) увеличение содержания марганца от 1,0 до 1,8 % приводит к практически линейному повышению прочностных характеристик. Предел текучести возрастает от 870 до 980 Н/мм2, временное сопротивление разрыву — от 1200 до 1380 Н/мм2 (рисунок 4.4). При этом пластические свойства с увеличением содержания марганца существенно снижаются, но интенсивность снижения в диапазоне содержаний марганца 1,2 + 1,8 % заметно падает и по относительному удлинению остается на уровне 13 15 %, относительному сужению — на уровне 20 + 23 % (рисунок 4.5). Ударная вязкость с увеличением содержания марганца снижается. При содержании марганца 1,8 % значения ударной вязкости при плюс 20 °С и минус 60 °С достигают соответственно 30 и 12 Дж/см2 (рисунок 4.6).
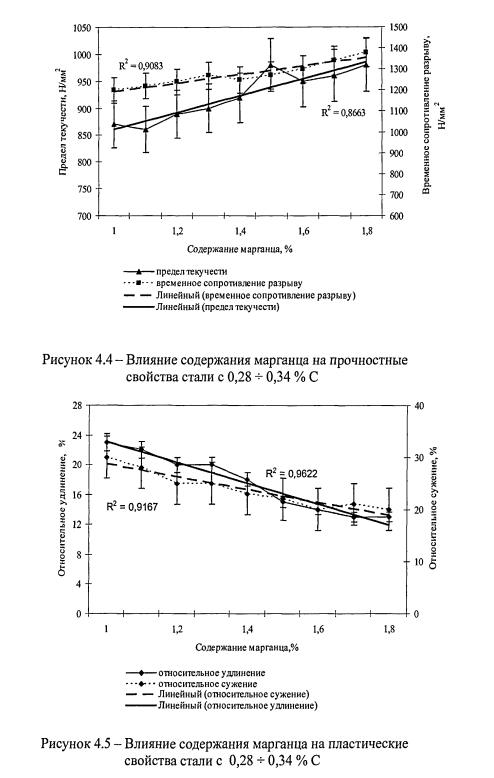
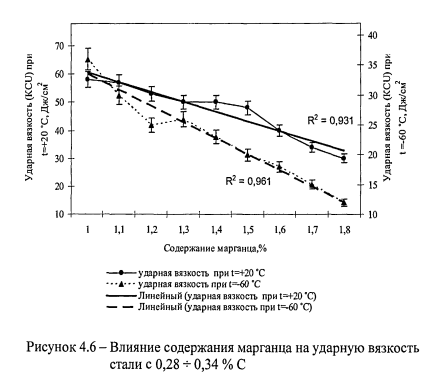
При изучении влияния кремния на механические свойства установлено, что кремний аналогично марганцу монотонно повышает прочностные свойства. Увеличение концентрации кремния от 0,76 до 1,8 % обеспечило повышение предела текучести от 800 до 1090 Н/мм2, а временного сопротивления разрыву — от 1080 до 1400 Н/мм2. (рисунок 4.7). Показатели пластичности с увеличением содержания кремния от 0,76 до 1,0 % несколько снижаются, и при дальнейшем увеличении содержания кремния до 1,80 % наблюдается стабилизация значений, которые для относительного удлинения составили 20 — 24 % и сужения — 30 — 34 % (рисунок 4.8). Характер изменения ударной вязкости от содержания кремния не установлен (рисунок 4.9). | Достоверность аппроксимации полиномиальной функции, описываемой изменение ударной вязкости при плюс 20 °С и минус 60 °С, очень низкая (0,3614 и 0,3878) и, по-видимому, связано с большой погрешностью результатов, полученных на заготовках размером 14×14 мм.
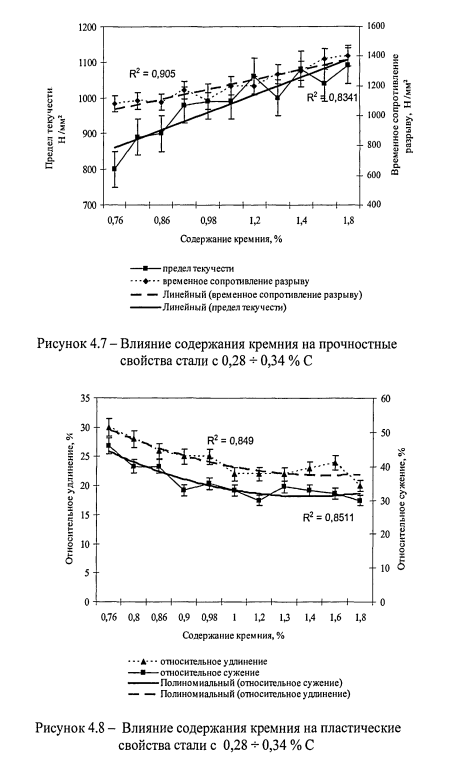
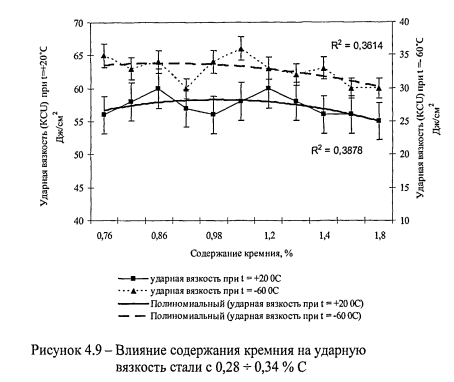
Увеличение содержания хрома во всем исследованном диапазоне концентраций от 0,41 до 1,2 % привело к практически линейному повышению предела текучести и временного сопротивления разрыву, соответственно, до 990 и 1400 Н/мм2 (рисунок 4.10). По пластическим характеристикам определенной зависимости не установлено. Достоверность аппроксимации полиномиальной зависимости относительного сужения и относительного удлинения от содержания хрома составила соответственно — 0,6292 и 0,7083 (рисунок 4.11). Ударная вязкость с повышением содержания хрома возрастает и в интервале концентраций от 1 до 1,2 % принимает стабильные значения, которые при температурах плюс 20 °С и минус 60 °С составили, соответственно, 58 60 и 33 + 36 Дж/см (рисунок 4.12). Как следует из данных, повышение содержания углерода, марганца, кремния и хрома сопровождается монотонным повышением прочностных характеристик и снижением свойств пластичности и вязкости.
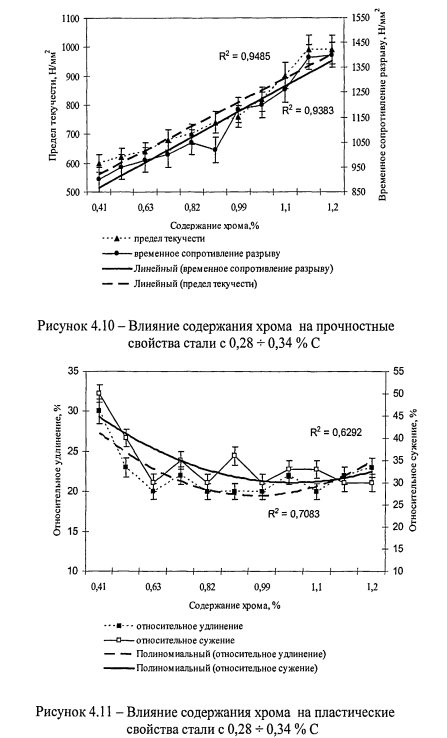
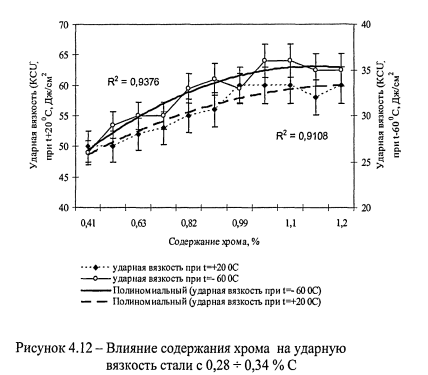
Статистическая обработка с помощью пакета программ 81а11511са 6.0. массива экспериментальных данных механических свойств сталей бейнитного класса с содержанием легирующих элементов (массовые доли, %): 0,26-0,52 С, 0,9-1,8 Мп, 0,76-1,40 81, 0,41-1,20 Сг позволила установить надежные зависимости, которые аппроксимированы следующими уравнениями:
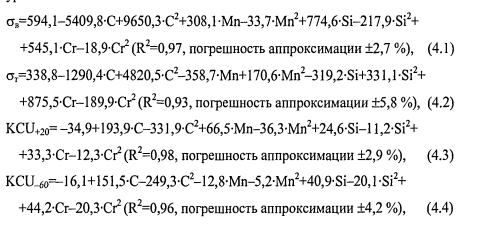
Установлено, что из рассмотренных составов сталей требуемый комплекс механических свойств, соответствующий рельсам категории Т1 (таблица 3.5), обеспечивается у стали бейнитного класса при следующем содержании химических элементов масс. %: 0,28-0,34 С; 1,00-1,4 Si; 1-1,8 Мп; 0,9 — 1,1 Cr.
Исследование влияния отпуска на структуру и свойства сталей
бейнитного класса
Проверку и корректировку концентрационных пределов углерода и легирующих элементов, выбранных в предыдущем разделе, проводили на образцах, приближенных по размеру к головке рельса. При этом помимо выбранных пределов исследовали влияние углерода в сочетании с различным содержанием легирующих элементов( таблица 3.2).
Исследования показали, что у сталей с содержанием углерода от 26 до 52 % путем комплексного легирования при непрерывном охлаждении на воздухе от температуры нагрева (860 — 880 °С) достигается разный уровень прочности, пластичности, ударной вязкости и твердости (рисунки 4.13 — 4.16).
Высокая прочность с низкой пластичностью и ударной вязкостью достигаются у стали с высоким содержание углерода (0,47 — 0,51 %) и легирующих элементов: марганца (1,15 — 1,59 %), кремния (1,22 — 1,60 %), хрома (1,17-1,25%). Хорошее сочетание твердости, прочности, пластичности и ударной вязкости обеспечивают стали при содержании углерода от 0,26 до 0,37 %, марганца от 0,97 до 1,80 %, кремния от 0,96 до 1,33 %, хрома от 1,00 до 1,20 % и молибдена от 0,20 до 0,67 %. При этом, чем ниже содержание углерода, тем выше должно быть содержание марганца или кремния при оптимальной концентрации хрома (~1 %). Таким образом, на ряде сталей (плавки № 5, 6, 7, 9, 10) показана возможность получения хорошего сочетания прочности, вязкости и пластичности.
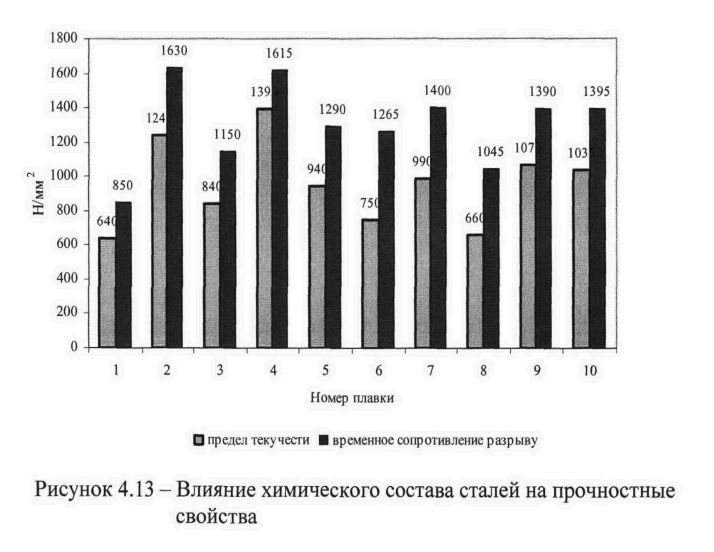
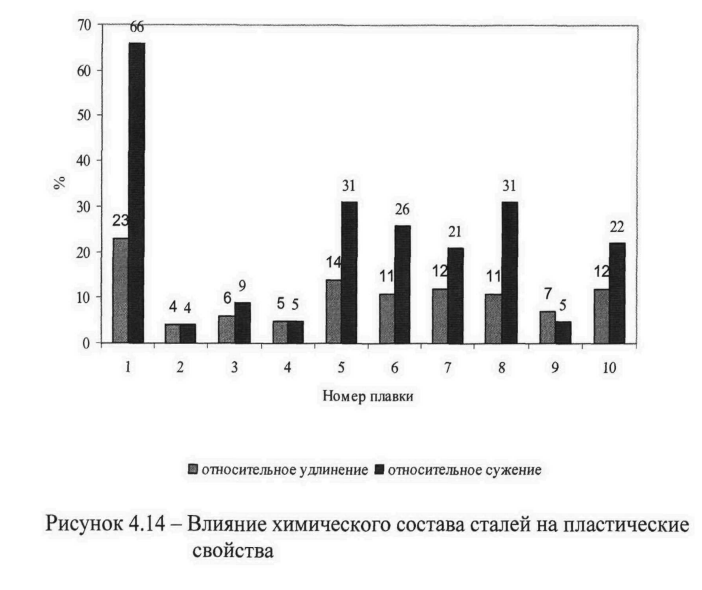
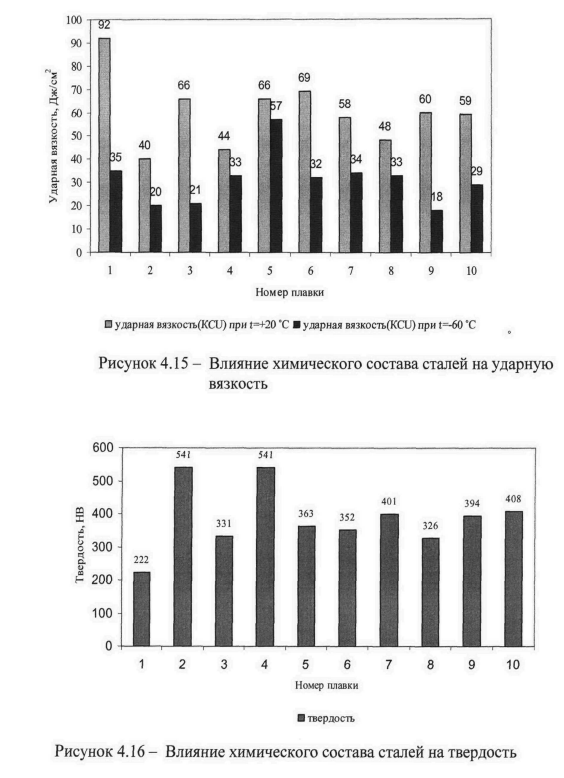
Различный уровень механических свойств исследуемых сталей обусловлен их структурой. Металлографическое исследование показало, что структура образцов плавок № 2 и 4, характеризующихся повышенным содержанием углерода и легирующих элементов, и отличающихся высокой прочностью, но низкой пластичностью и ударной вязкостью, состоит из мартенсита и бейнита. При этом в структуре стали плавки № 2 преобладает бейнит (рисунок 4.17), в стали плавки № 4 — мартенсит (рисунок 4.18).
Бейнит обнаруживается в виде более длинных монолитных пластин пакетного строения. Значительный размер пластин бейнита объясняется [138] за счет добавления микрофрагментов к острию иглы и возникновения новых цепочек в поперечном направлении. Мартенсит представлен в виде коротких разориентированных мелких игл.
В отличие от плавок № 2 и 4 микроструктура образцов плавок № 5, 6, 7, 8, 9 и 10, отличающихся наиболее сбалансированным комплексом механических свойств, состоит преимущественно из бейнита, а в отдельных случаях из бейнита и локальных участков, состоящих из продуктов перлитного превращения. Особенностями строения бейнита, а также долей присутствия продуктов перлитного превращения, обусловлены разные механические свойства исследуемых сталей. Наиболее близкие по свойствам стали плавки № 5 и 6 (рисунки 4.19,4.20) имеют практически одинаковую структуру, состоящую из бейнита преимущественно гребнеобразного строения и локальных участков, состоящих из продуктов перлитного превращения. Структура стали плавки № 8 (рисунок 4.21) состоит преимущественно из троостита, полигонального феррита и участков верхнего бейнита, чем и обусловлены сравнительно невысокие прочностные свойства (от=660 Н/мм ; с„=1045 Н/мм ) и твердость (326 НВ) указанной плавки.
Стали плавки № 7, 9 и 10, характеризующиеся близкими механическими свойствами и твердостью, равной соответственно 401, 394 и 408 НВ, отличаются характером микроструктуры. Структура плавки № 7 состоит из бейнита (рисунок 4.22). В отличие от плавки № 7 в структуре плавки № 9, отличающейся повышенным содержанием углерода и сравнительно низким содержанием кремния и хрома, выявлен троостит, распределенный в виде более массивных участков и бейнит (рисунок 4.23), чем и обусловлены полученные достаточно высокие прочностные свойства (ат-1070 Н/мм2; ов=1390 Н/мм2).
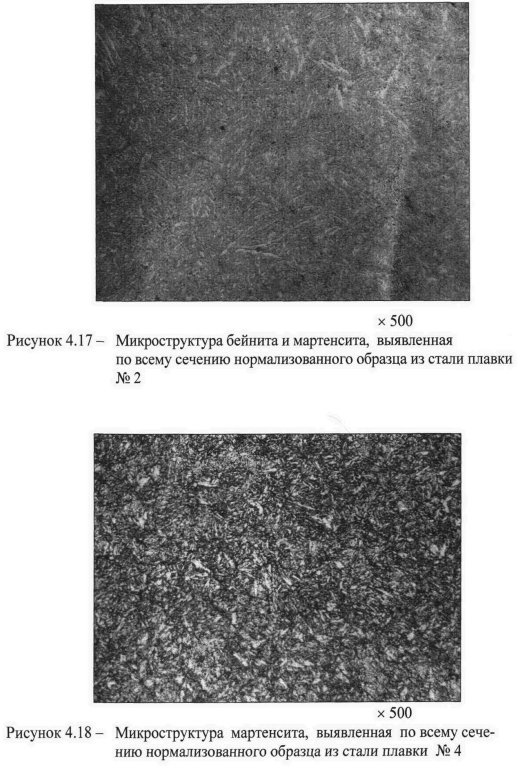
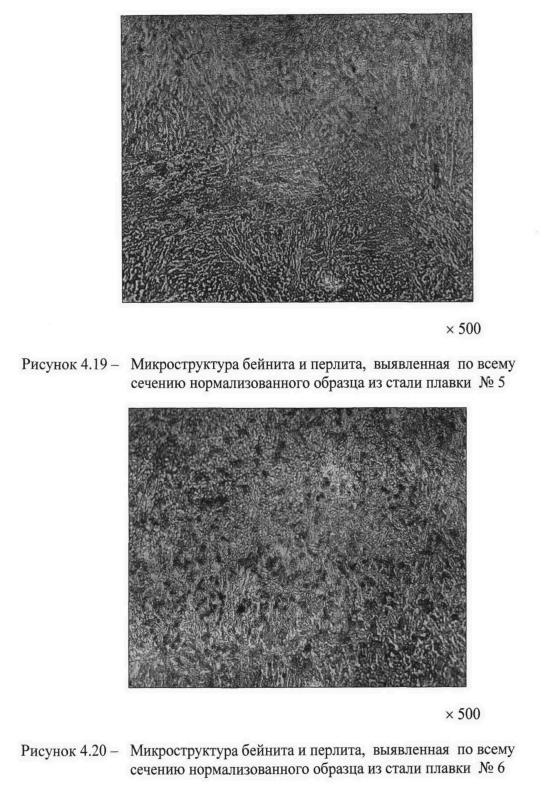
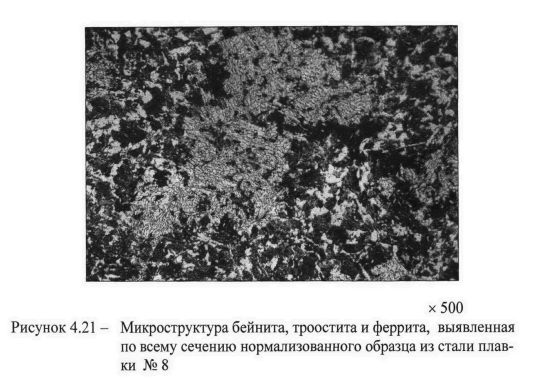
Наиболее тонкопластинчатая структура бейнита выявлена у стали плавки № 10 и представлена только в виде тонких длинных монолитных параллельных пластин, характерных для нижнего бейнита (рисунок 4.24).
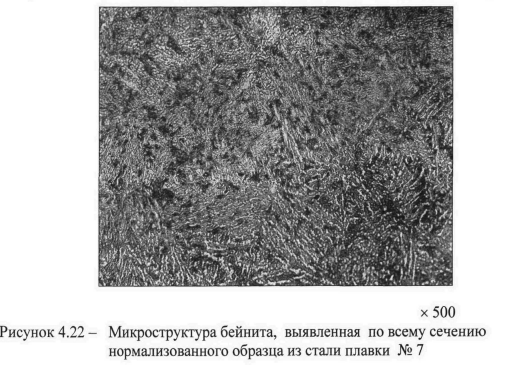
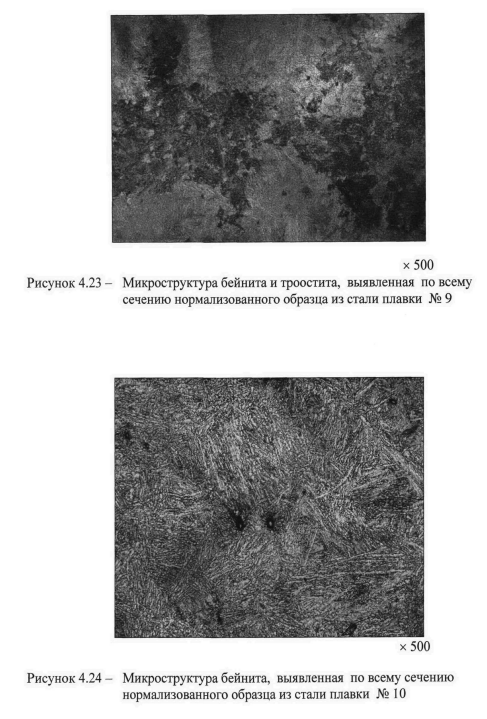
Наиболее грубые продукты бейнитного превращения, типичные для верхнего бейнита, выявлены в стали № 3 и представлены на рисунке 4.25. В структуре этой стали, наряду с верхним бейнитом, наблюдаются также продукты перлитного превращения и полигональный феррит. Перистым строением бейнита и наличием перлитных участков в структуре образца обусловлены сравнительно низкие механические свойства и твердость стали (от=840 Н/мм2; ов=1150 Н/мм2, 331 НВ).
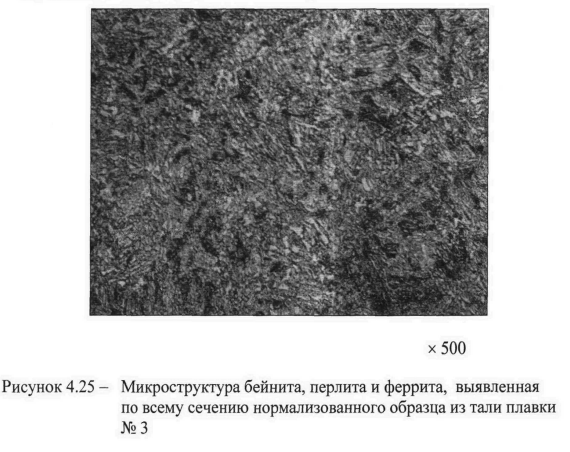
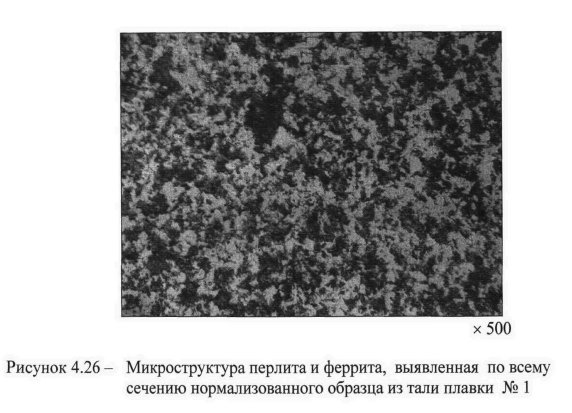
В работе [139] установлено, что количество остаточного аустенита при мартенситном превращении достигает 5 %, при бейнитном превращении — 20 %.
Результаты металлографического исследования показали, что структурное состояние исследуемых сталей при непрерывном охлаждении на воздухе с перекристаллизационного нагрева определяется суммарным действием углерода и легирующих элементов. Это влияние довольно сложное и не может быть сведено к простой схеме. В зависимости от концентрационных интервалов легирующих элементов превращение аустенита можно рассматривать как комбинацию нескольких одновременно или последовательно развивающихся процессов, которые протекают в близких температурных интервалах, но совершаются по своим кинетическим законам.
На основании проведенных исследований установлено, что наилучшее сочетание механических свойств и однородная бейнитная структура достигается у стали следующего состава, масс. %: 0,34 С; 1,56 Мп; 1,24 Бц 1,10 Сг; 0,33 Мо; 0,14 V; 0,026 N.
Как было показано выше, исследуемые стали упрочняются при охлаждении на воздухе с образованием различного структурного состояния, состоящего из различных структурных составляющих: мартенсита, бейни- та, остаточного аустенита и троосто-перлита. Полученные структуры в той или иной степени находятся в неравновесном состоянии. Для придания равновесного состояния исследуемые стали подвергали отпуску при температурах от 300 до 550 °С .
На рисунках 4.27 — 4.34 представлены результаты изменения механических свойств бейнитных сталей в зависимости от температуры отпуска. Анализ экспериментальных данных показал, что с повышением температуры отпуска выше 450 °С происходит разупрочнение исследуемых сталей (рисунки 4.27 и 4.28). При этом отмечено, что в большей степени разу- прочняются стали с мартенситно-бейнитной структурой (плавки № 2 и 4), в меньшей степени стали с наличием продуктов перлитного и бейнитного превращений (плавки № 5 + 10).
На фоне снижения прочностных характеристик практически у всех исследуемых сталей с повышением температуры отпуска отмечается плавное повышение относительного удлинения и сужения (рисунки 4.29 и 4.30). При этом у стали плавок № 5 и 8 отмечены максимальные значения, плавок № 2 и 4 — минимальные значения указанных характеристик. Несколько иначе изменяется при отпуске ударная вязкость исследуемых сталей. Установлено, что отпуск 350 °С по сравнению с нормализацией приводит у подавляющего большинства сталей к повышению ударной вязкости при комнатной и отрицательной температурах (рисунки 4.31 и 4.32). Особенно сильно возрастает ударная вязкость при комнатной температуре у сталей плавок № 3 и 8, уровень ее составил соответственно 90 и 80 Дж/см . Аналогичным образом, но в меньшей степени изменяется ударная вязкость у сталей при температуре минус 60 °С . При этом максимальное значение по этой характеристике достигнуто у стали плавки № 8.
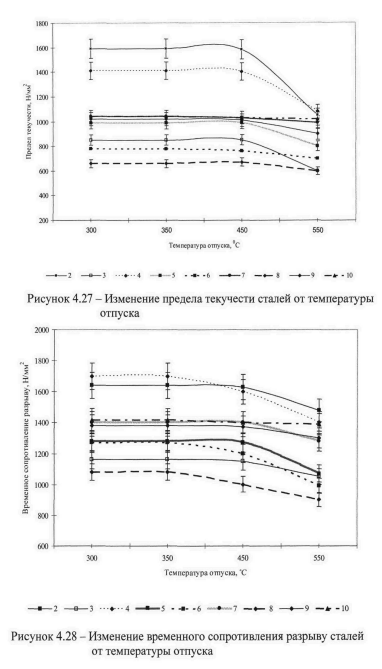
Охрупчивающее действие отпуска при 350 °С проявилось только на стали плавки № 4, имеющей преимущественно мартенситную структуру.
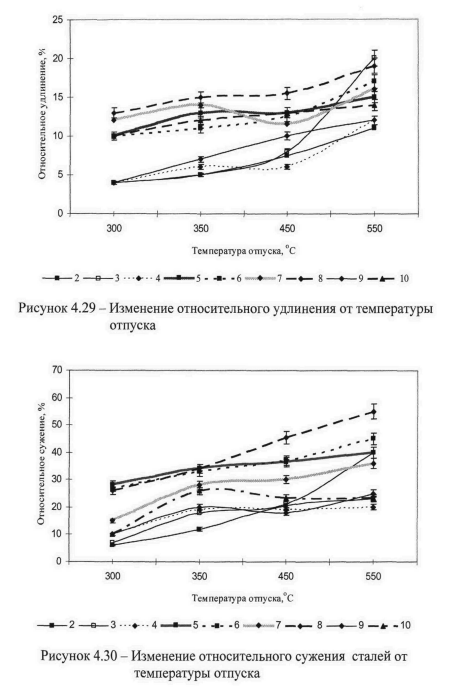
При достижении температуры отпуска 450 °С отмечено резкое снижение ударной вязкости при комнатной и отрицательной температурах (рисунок 4.33 и 4.34). Стабилизация значений ударной вязкости наблюдается при температуре отпуска 550 °С.
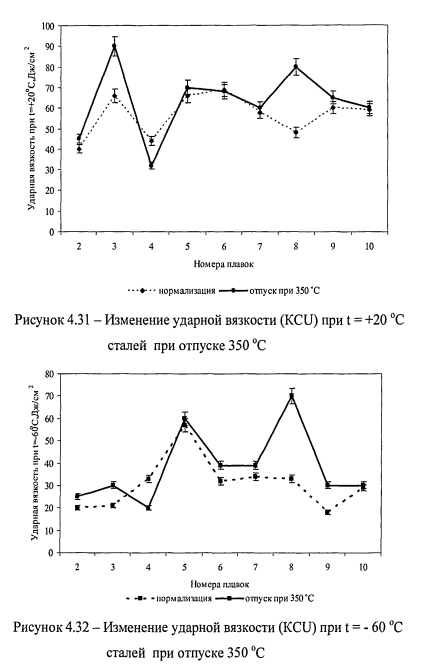
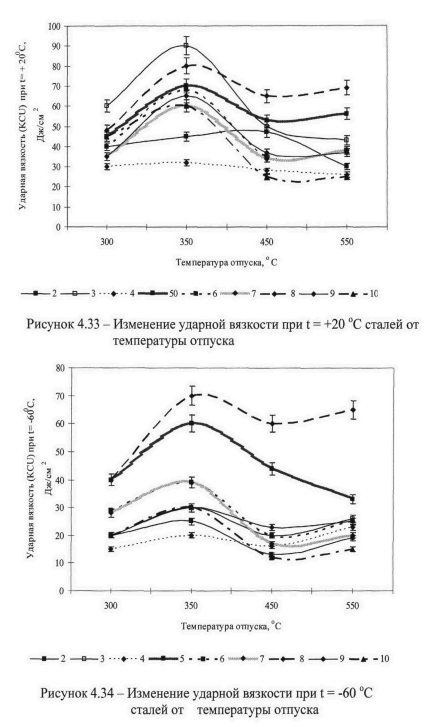
Сложный характер изменения ударной вязкости сталей с бейнитной структурой при отпуске объясняется, согласно работам [139, 140], особенностями поведения остаточного аустенита при отпуске. Поскольку остаточный аустенит является метастабильной фазой, его количеством и стабильностью определяются в конечном итоге свойства стали. Наблюдаемое у сталей сильное снижение ударной вязкости при отпуске в интервале 400 500 °С обусловлено, согласно установленной В.М. Счастливцевым терминологии, бейнитной хрупкостью. В отличие от обратимой отпускной хрупкости сталей, закаленных на мартенсит, бейнитное охрупчивание связывают с изменением внутризеренной структуры, а именно: с превращением остаточного аустенита в мартенсит или перлит и не связаны с процессами, происходящими на границе зерна. Повышение ударной вязкости и пластичности бейнитных сталей при низком отпуске обеспечивается за счет обогащения остаточного аустенита углеродом и повышения его стабильности.
Микроструктурный анализ, проведенный с помощью оптического микроскопа, позволил оценить влияние отпуска в диапазоне температур от 300 до 550 °С на изменение микроструктуры исследуемых сталей. Исследование показало, что отпуск при температурах от 300 до 350 °С не приводит к видимым изменениям микроструктуры исследуемых сталей. При дальнейшем увеличении температуры отпуска от 450 до 550 °С отмечается заметное изменение характера структуры только у сталей плавок № 2 и 4 (рисунок 4.35 и 4.36). Структура этих сталей состоит из феррито- карбидной смеси, сохраняющей форму пластин мартенсита. В то же время в сталях плавок № 5 + 10 с исходной, преимущественно бейнитной структурой, при отпуске 450 + 550 °С видимых изменений в микроструктуре не обнаружено. Структура исследуемых сталей имеет заметно более отчетливый рисунок по сравнению с их нормализованным состоянием и представлена на рисунках 4.37 4.42. Образование отчетливой, более травимой структуры при низком отпуске связывают, как правило, с выделением углерода из твердого раствора.
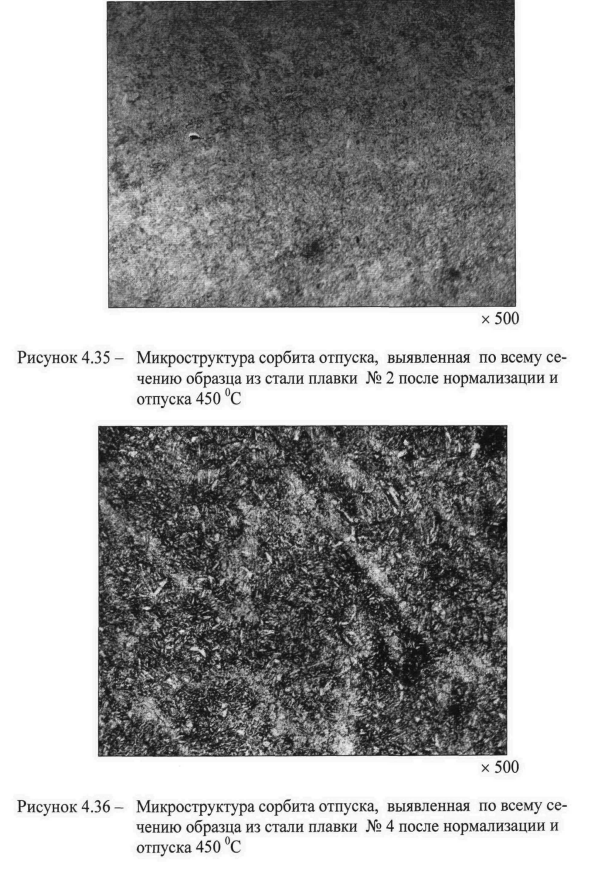
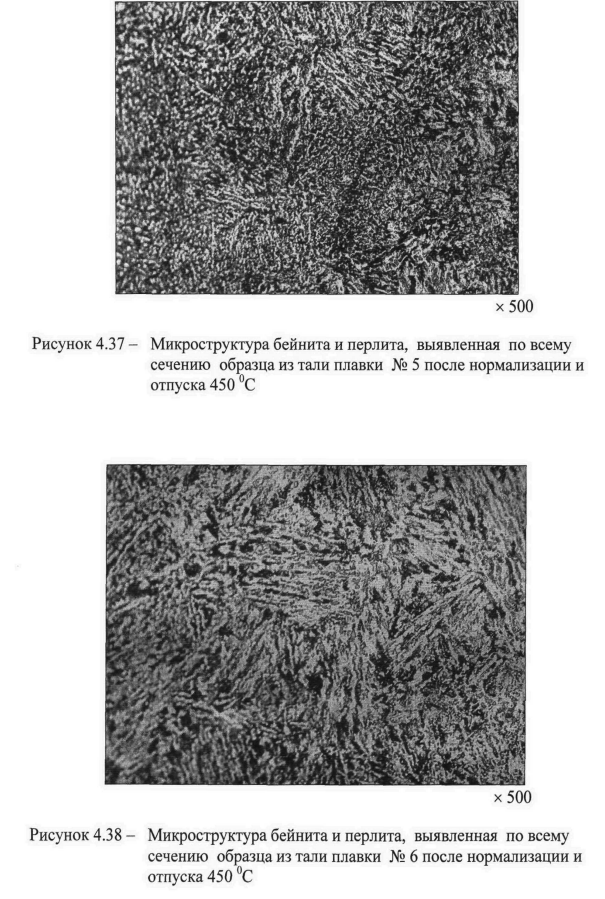
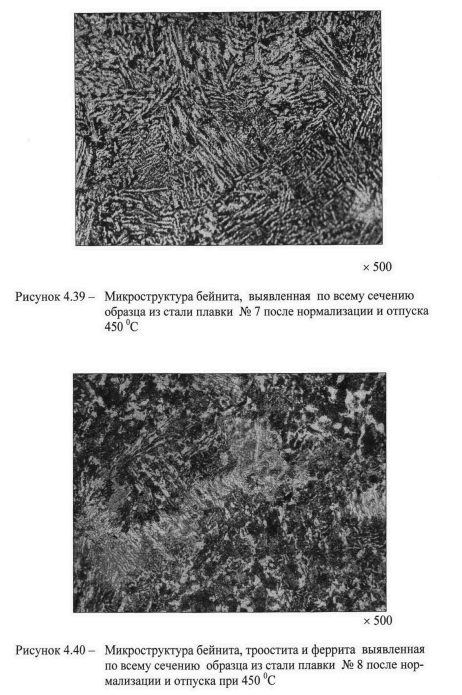
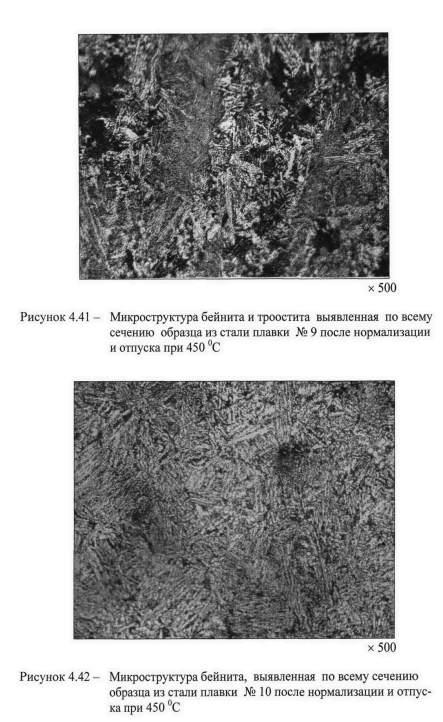
Таким образом, при исследовании установлено, что сбалансированный комплекс механических свойств по прочности, пластичности и ударной вязкости обеспечивается у нормализованных бейнитных сталей преимущественно при отпуске 350 °С. Из рассмотренных выше составов сталей наиболее рациональный в отношении получения высокого комплекса механических свойств показали плавки № 7 и 10.
Исследование влияния закалки с отпуском на свойства и
структурообразование сталей бейнитного класса
В предыдущем разделе показано, что отпуск при 350 °С приводит к существенному повышению пластических свойств и ударной вязкости бейнитных сталей за счет остаточного аустенита. Исходя из этого можно предположить, что изменяя количество остаточного аустенита в стали можно воздействовать на ее свойства. Для проверки этого утверждения воспользовались одним из возможных способов уменьшения количества остаточного аустенита, применив закалку в масле, обеспечив, тем самым, более высокую скорость охлаждения по сравнению с охлаждением на воздухе. Для сопоставимости результатов после закалки образцы исследуемых сталей отпускали при температуре 350 °С. Следует отметить, что проверка имеет относительный характер, поскольку рассматриваемые стали значительно различаются по составу. Полученные результаты механических испытаний показали, что закалка в масле с отпуском при 350 °С по сравнению с нормализацией (закалка на воздухе) и аналогичным отпуском приводит к повышению прочностных характеристик всех без исключения сталей (рисунки 4.43 и 4.44). Наиболее существенно закалка повысила предел текучести и временное сопротивление разрыву сталей плавок № 3, 5, 7, 8, 9 и 10. В меньшей степени влияние закалки сказалась на повышении прочностных характеристик сталей плавок № 2 и 4. Повышение прочности сопровождается снижением пластичности подавляющего большинства исследуемых сталей (рисунки 4.45 и 4.46). Исключение составили плавки № 2, 3 и 9, которые показали после закалки с отпуском более высокие значения пластических характеристик по сравнению с их исходным состоянием, полученным после нормализации и отпуска.
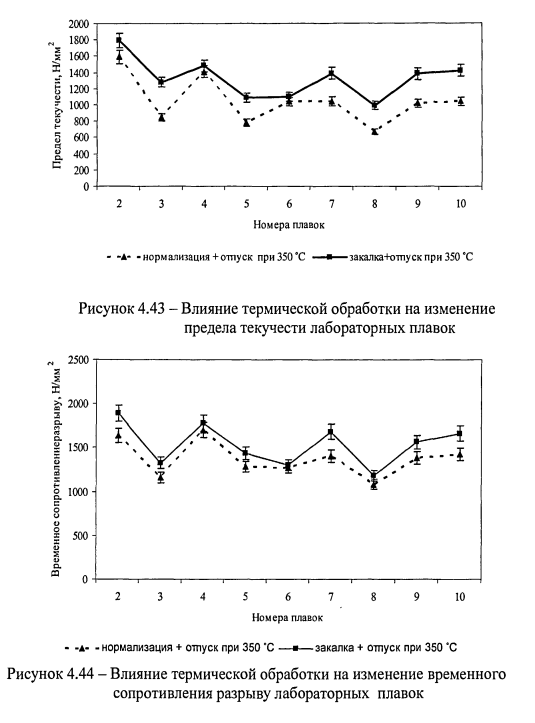
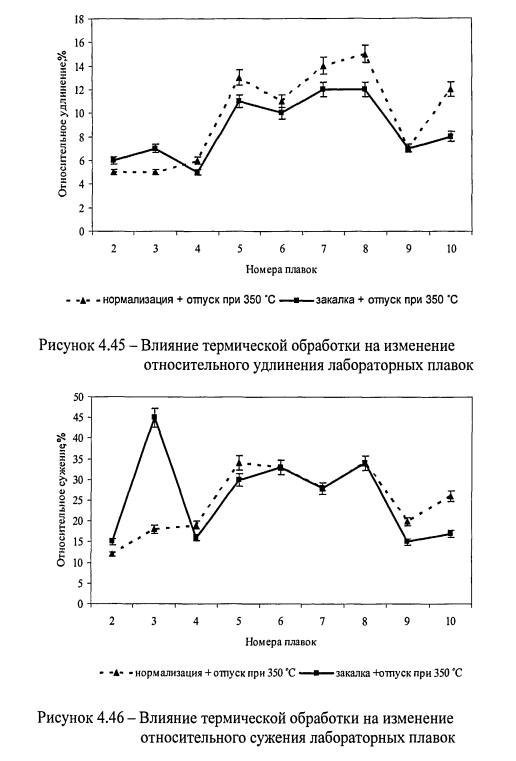
Особенно отрицательно сказалось влияние закалки на ударную вязкость. Закалка с отпуском при 350 °С по сравнению с нормализованно- отпущенным состоянием приводит к резкому снижению ударной вязкости, как при комнатной, так и отрицательной температурах (рисунки 4.7 и 4.48).
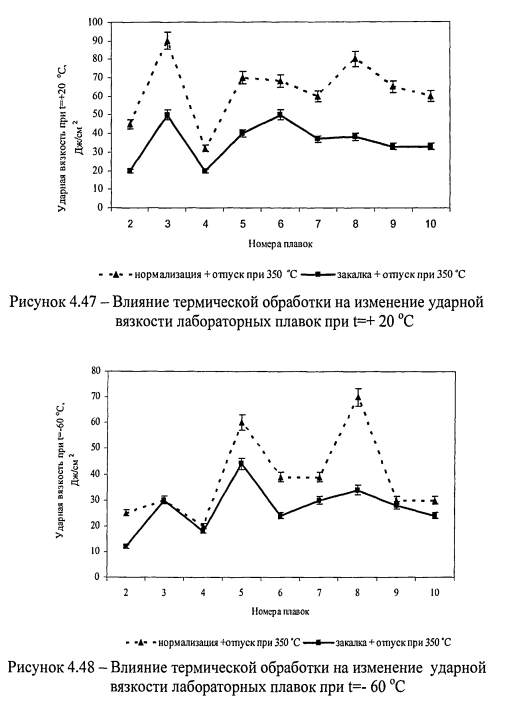
Полученные результаты механических испытаний согласуются с ре-зультатами металлографического исследования. После закалки образцы плавок № 2 и 4 имеют мартенситную структуру, показавшую при испытаниях высокую прочность и низкую пластичность. При этом структура плавки № 2, в отличие от плавки № 4, характеризуется выраженным игольчатым строением (рисунки 4.49 и 4.50). Сравнительно высокие прочностные свойства и пониженные пластические свойства плавок № 7, 9 и 10 обусловлены смешанной структурой, состоящей из бейнита и мартенсита, полученной после закалки на образцах плавок 7, 9 и 10 (рисунки 4.51 — 4.53). При этом плавка № 7 отличается как высоким уровнем прочности , так и пластичности, что обусловлено преобладанием в структуре бейнит- ной составляющей. Сбалансированный комплекс механических свойств плавок № 5, 6 и 8 обусловлен наличием однородной бейнитной структуры (рисунки 4.54 — 4.56). Из этих сталей наибольший интерес представляет плавка № 6, поскольку независимо от скорости охлаждения, химический состав указанной стали обеспечивает одинаковые свойства и структуру.
Самые низкий комплекс механических свойств плавки № 3 обусловлен наличием смешанной структуры, состоящей из перлита и бейнита (рисунок 4. 57).
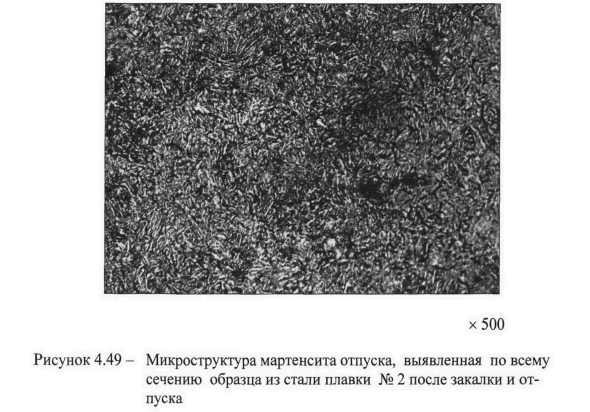
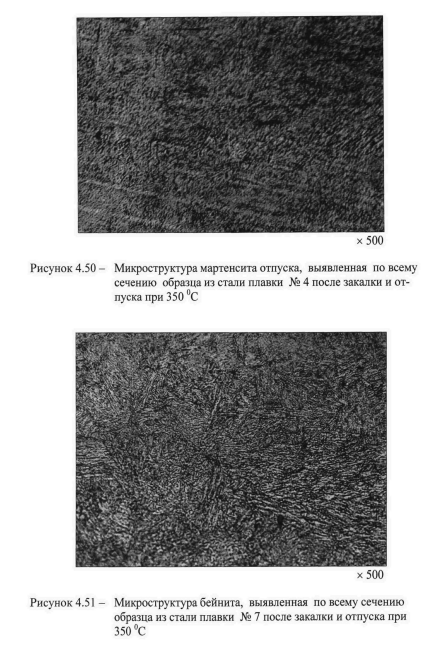
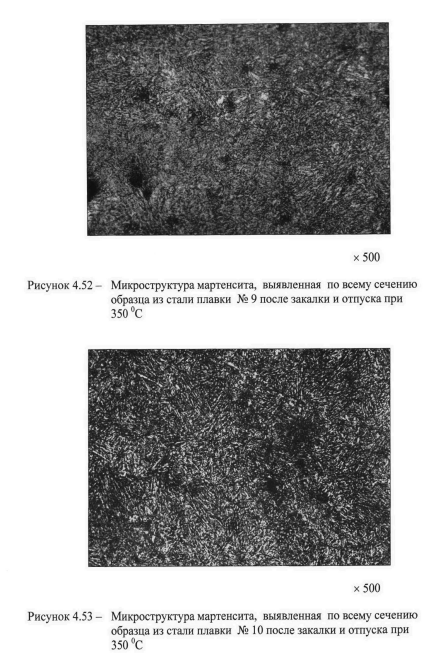
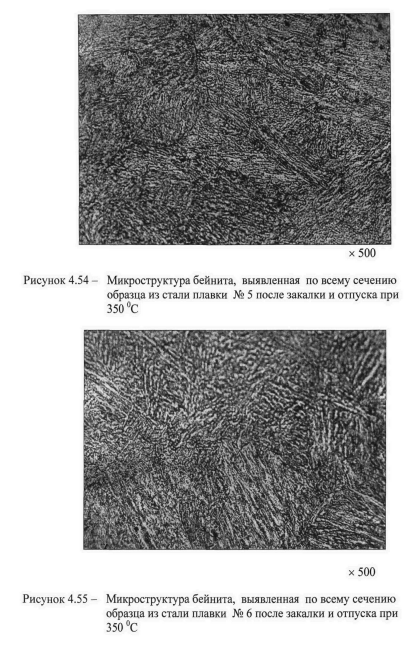
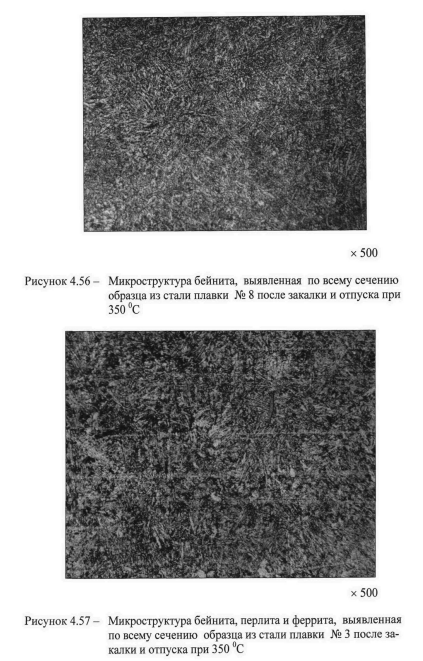
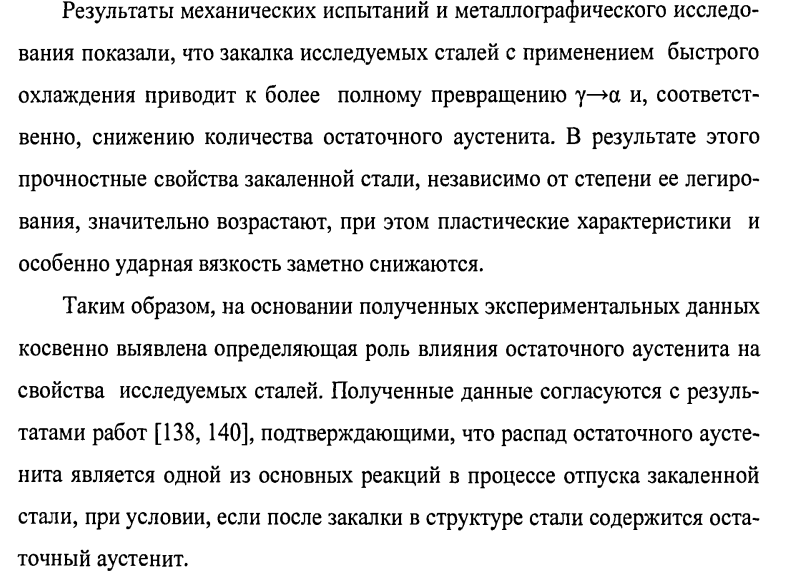
Выводы
- Исследовано влияние концентрационных пределов углерода и каж¬дого легирующего элемента системы Мп — Бі — Сг на механические свойст¬ва сталей бейнитного класса. Установлено, что повышение содержания уг¬лерода, марганца, кремния и хрома обеспечивает повышение прочностных характеристик и снижение свойств пластичности и вязкости. Для осущест-вления прогнозных расчетов механических и пластических свойств уста-новленные зависимости аппроксимированы регрессионными уравнениями.
- Установлено, что из рассмотренных 40 различных химических со-ставов сталей требуемый комплекс механических свойств, соответствую¬щий рельсам категории Т1, обеспечивает сталь бейнитного класса с содер¬жанием химических элементов, масс. %: 0,28-Ю,34 С; 1,00-И,4 8і; 1-4,8 Мп; 0,9-1,1 Сг.
- В результате исследований сталей с содержанием элементов, масс. %: 0,28-0,34 С; 1,00-1,4 Si; 1-1,8 Мп; 0,9 — 1,1 Сг установлено, что наи лучшее сочетание механических свойств и однородная бейнитная структура достигается у стали следующего состава, масс. %: 0,34 С; 1,56 Мп; 1,24 Si; 1,10 Сг; 0,33 Mo; 0,14 V; 0,026 N.
- При металлографическом исследовании установлено, что структурное состояние сталей определяется суммарным действием углерода и легирующих элементов. В зависимости от концентрационных пределов углерода и легирующих элементов при непрерывном охлаждении на воздухе в стали, наряду с продуктами бейнитного превращения, формируются структуры перлитной и мартенситной области фазовых превращений. 5.1 Разработка технологии термической обработки железнодорожных рельсов из сталей бейнитного класса.
- В результате исследований влияния отпуска в интервале температур 300 — 550 °С на механические свойства сталей бейнитного класса установлено, что при достижении температуры отпуска 450 °С на фоне некоторого разупрочнения стали происходит снижение пластических свойств при резком падении ударной вязкости при температурах плюс 20 °С и минус 60 «С. Резкое снижение ударной вязкости обусловлено проявлением бейнитной хрупкости, вызванной распадом остаточного аустенита. Определена оптимальная температура отпуска (350 °С), обеспечивающая у сталей бейнитного класса максимально высокий уровень ударной вязкости и пластических свойств без снижения прочностных характеристик. В предыдущих разделах диссертационной работы установлено, что упрочнение сталей бейнитного класса достигается при непрерывном охла¬ждении на воздухе с температуры перекристаллизации. Наилучшее сочетание прочности, пластичности и ударной вязкости достигается после проведения отпуска при 350 °С.
- Исследование влияния закалки на изменение механических свойств бейнитных сталей показало их взаимосвязь с остаточным аустенитом. Установлено, что с увеличением скорости охлаждения прочностные характеристики бейнитных сталей .повыщаются, а пластические свойства и ударная вязкость снижаются за счет проведения полного превращения у—»а.
Список литературы
- Изготовление рельсов с закаленной головкой с использованием прокат¬ного нагрева. Herstellung fon kopfgeharteten Schienen aus der Walzhitze /Moser A.,Pointner Р., Prskawetz G.// Berg — und Huttenmann. Monatsh.- 1988.- 133, №7.-C. 321-326.
- Свойства рельсов закаленных с индукционного нагрева /С.И. Рудюк [и др.] // Повышение качества ж.д. рельсов и колес: отрасл. сб. науч. тр. — Харьков: УкрНИИМет, 1987. — С.22-24.
- Полухин П.И. Прокатка и термическая обработка рельсов / П.И. Полу- хин, Ю.В.Грдина, Е.Я. Зарвин. — М.: ГНТИЛ по черной и цветной ме¬таллургии. 1962.-508с.
- Шур Е.А. Новый метод термической обработки рельсов с использовани¬ем двухстороннего охлаждения / Е.А. Шур, В.М. Федин, И.Г. Жигалкин // Материалы юбилейной рельсовой комиссии: сборник докладов. — Но¬вокузнецк, 2002. С. 149 — 155.
- Федин В.М. Объемно-поверхностная закалка деталей подвижного со¬става и верхнего строения пути./В.М. Федин — М.: Интекст, 2002.-208с.
- Меньшиков А.Г.Термическая обработка рельсов с использованием ско¬ростного струйного охлаждения // Сталь.- 1995. — №6.- С. 59 — 61.
- Галицын Г.А. Технология термообработки железнодорожных рельсов и накладок при охлаждении в воде / Г.А. Галицын, А.Б. Добужская, Е.А. Муравьев // Материалы юбилейной рельсовой комиссии: сборник док-ладов. — Новокузнецк, 2002.- С. 156 — 167.
- Исследование возможности закалки рельсов в водополимерных средах /В.И. Ворожищев [и др.] // Сталь. — 2005. — № 11. -С. 126 — 131.
- Свойства рельсов из низколегированной стали после термомеханиче¬ской обработки / В.И. Ворожищев [и др.] // Сталь.-1981. -№9. — С. 74 -76
- Упрочнение рельсов водовоздушной смесью в модуле с инжекционны- ми форсунками / В.Н. Цви1ун [и др.] // Изв. вузов.Чер. металлургия.- 1988.-№10.- С.74-76.
- Дифференцированная закалка и свойства рельсов из стали Э76 / А.В. Иванов [и др.] // Изв .вузов.Чер. металлургия,- 1998.- №2.- С.39 -42.
- Методы повышения эксплуатационных свойств рельсовой стали /В.А. Бердышев [и др.] // Изв. вузов. Черная металлургия.- 1997.- № 7. — С. 34¬38.
- Грачев В.В. Технология повышения эксплуатационных характеристик рельсовой стали дифференцированной закалкой / В.В. Грачев, В.Е. Гро¬мов, В.И. Петров // Материалы всероссийской научно-практической конференции «Металлургия на пороге XXI века: достижения и прогно¬зы». — Новокузнецк, 1999.- С.36 — 42.
- Heller W. Рельсы для современных условий эксплуатации / W. Heller, R. Schweitzer // ETR — Eisenbahntechnische Rundschau, — 34.1985.- № 10.- P. 733-736.
- Yokoma H. Development ofhigh strength pealitic steel rail(SP Rail) with ex¬cellent wear and damage résistance / H. Yokoma, S. Mitao, M. Takemasa // NKK Technical Review.- 2002.- N 86.- P.l- 17.
- Roney M.D. Опыт работы железных дорог США и Канады с осевыми на¬грузками до 30 т // Railway Gazette International.- 1988.- № 6.- P. 385-378.
- Шур E.A. Влияние структуры и структурных неоднородностей на свой¬ства термически обработанной рельсовой стали. / Е.А. Шур, Я.Р. Раузин // Рельсы повышенной эксплуатационной стойкости: сб. нуч. тр. М.: Трансжелдориздат, 1966.- С. 115 — 137.
- Шур Е.А. Выбор оптимальной структуры закаленных рельсов./ Е.А. Шур, Я.Р. Раузин // Производство, качество и стойкость железнодорож¬ных рельсов: сб. науч. тр. М.: Металлургия, 1966.- С. 201- 207.
- Шур Е.А. Причины образования структурных неоднородностей при по¬верхностной закалке высокоуглеродистой конструкционной стали. / Е.А.
- Шур, Я.Р. Раузин // Металловедение и термическая обработка метал¬лов.- 1967. — №1.. С. 53 — 56.
- Шур ЕЛ. Структурные основы термической обработки рельсов // Тер¬мическая обработка металлов: Сб. докладов. М., Металлургия, 1974. № 3. С. 36-38.
- Шур Е.А. Влияние структуры на эксплуатационную стойкость рель¬сов// Влияние свойств металлической матрицы на эксплуатационную стойкость рельсов: сб. науч. тр.- Екатеринбург: ГНЦ РФ ОАО «УИМ», 2006.- С. 37-61.
- Добужская А.Б. Исследование структуры рельсов с разной стойкостью против образования контактно-усталостных дефектов / А.Б. Добужская, Г.А. Галицын, В.И. Сырейщикова // Влияние свойств металлической матрицы на эксплуатационную стойкость рельсов: сб. науч. тр. — Екатеринбург: ГНЦ РФ ОАО «УИМ», 2006. — С. 64 — 80.
- Определение характеристик микроразрушения рельсовой стали на ос¬нове испытаний на растяжение т оценка их связи с работоспособностью рельсов /Г.А. Галицын [и др.] // Влияние свойств металлической матри¬цы на эксплуатационную стойкость рельсов: сб. науч. тр.- Екатеринбург: ГНЦ РФ ОАО «УИМ», 2006.- С. 81 — 96.
- Галицын Г.А. Моделирование эволюции дислокационной структуры стали в процессе нагружения рельсов. / Г.А. Галицын, А.Б. Добужская, В.В. Могильный // Влияние свойств металлической матрицы на экс¬плуатационную стойкость рельсов: сб. науч. тр.- Екатеринбург: ГНЦ РФ ОАО «УИМ», 2006.- С. 97 — 103.
- Сравнительный анализ структуры рельсовой стали отечественных и импортных производителей / К.В. Григорович [и др.] // Влияние свойств металлической матрицы на эксплуатационную стойкость рельсов: сб. науч. тр.- Екатеринбург: ГНЦ РФ ОАО «УИМ», 2006.- С. 128 — 141.
- Добужская А.Б. О повышении эксплуатационной стойкости рельсов за счет оптимального соотношения пластических свойств и однородности микроструктуры / А.Б. Добужская, Г.А. Галицын // Повышение качества и эксплуатационной стойкости рельсовой продукции: сб. докладов. -М.: Интекст, 2005.- С. 46 — 58.
- Казарновский Д.С. Связь между тонкой структурой и усталостной прочностью высокоуглеродистой стали / Д.С. Казарновский, Е.И. Чер¬нов, В.И. Газов // Металлы. — 1984.- №3.- С. 153 — 158.
- Счастливцев В.М. Износостойкоть рельсовой стали / В.М. Счастлив¬цев, A.B. Макаров, Т.И. Табатчикова // Влияние свойств металлической матрицы на эксплуатационную стойкость рельсов: сб.науч.тр.- Екате-ринбург: ГНЦ РФ ОАО «УИМ», 2006.- С. 142- 156.