Сейчас ваша корзина пуста!
Разработка, внедрение и освоение технологии термической обработки железнодорожных рельсов из стали бейнитного класса в условиях оао «нкмк»
Цикл статей:
Глава 1 — Разработка химического состава и технологии термической обработки железнодорожных рельсов из стали бейнитного класса
Глава 2 — Теоретические предпосылки разработки химического состава сталей бейнитного класса
Глава 3 — Оборудование и методика экспериментальных исследований
Глава 4 — Исследование влияния различных видов термической обработки на структуру и свойства сталей бейнитного класса
Глава 6 — Служба железнодорожных рельсов из сталей бейнитного класса
Химический состав стали (масс. %: 0,34 С; 1,56 Мп; 1,24 Si; 1,10 Сг; 0,33 Мо) бейнитного класса, полученный на лабораторных плавках, опробовали в промышленных условиях на полнопрофильных рельсах.
С этой целью на ОАО «НКМК» были выплавлены 2 опытно- промышленные плавки (таблица 3.3), из которых изготовили железнодорожные рельсы типа Р65 длиной 25 м. Качество опытных рельсов оценивали в горячекатаном и отпущенном состояниях, а также после нормализации и отпуска, и сравнивали с объёмно-закаленными рельсами из стали марки Э76Ф. Опытные рельсы подвергали испытаниям на определение копровой прочности, механических свойств, остаточных напряжений, загрязненности неметаллическими включениями, макро-и микроструктуры.
Разработка технологии термической обработки железнодорожных рельсов из сталей бейнитного класса
В предыдущих разделах диссертационной работы установлено, что упрочнение сталей бейнитного класса достигается при непрерывном охлаждении на воздухе с температуры перекристаллизации. Наилучшее сочетание прочности, пластичности и ударной вязкости достигается после проведения отпуска при 350 °С.
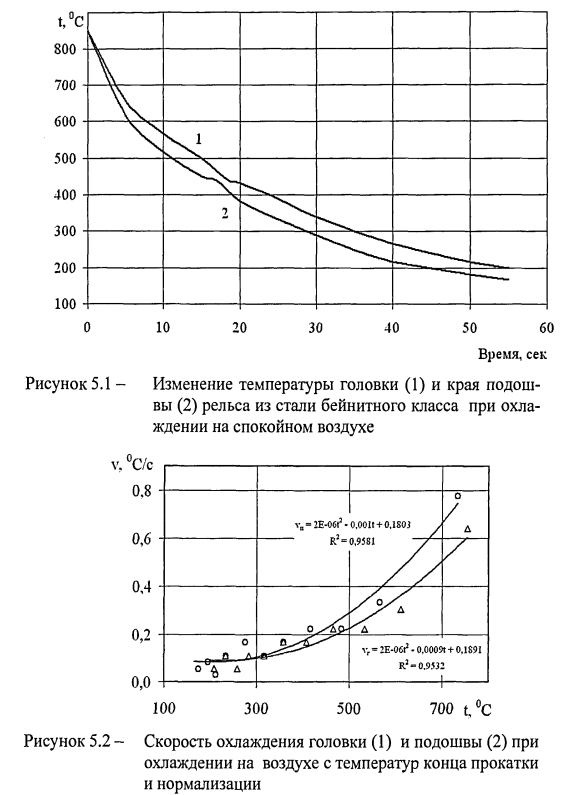
Коэффициенты корреляции между расчетными точками и аппроксимирующей зависимостью показали достоверность полученных результатов. Согласно полученным расчетам при охлаждении рельсов на спокойном воздухе от температур 860 °С в интервале бейнитного превращения реализуются практически одинаковые для различных участков профиля скорости охлаждения на уровне 0,2 °С/с. При этом существенной разницы межу скоростями охлаждения головки и подошвы не выявлено.
Упрочнение рельсов из сталей бейнитного класса достигается в равной степени с прокатного нагрева и температуры аустенитизации под нормализацию. Исходя из этого в промышленных условиях могут быть реализованы две технологии термической обработки, а именно: одинарной термической обработки — отпуск при 350 °С после охлаждения на воздухе с температуры прокатного нагрева (рисунок 5.3) и двойной термической обработки, включающей нормализацию и отпуск при 350°С (рисунок 5.4).
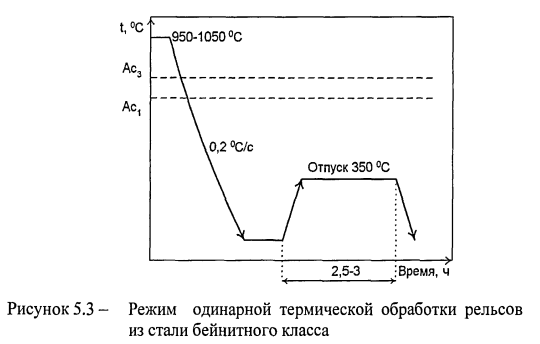
Согласно первой схемы термической обработки рельсы после прокатки охлаждают на стеллаже в положении «лежа на боку», плотно придвинув их друг к другу. Охлажденные рельсы подвергают правке на ролико- правильной машине. Затем рельсы, сформировав в пакеты по 15-17 штук, нагревают в роликовой печи до температуры 350 °С для отпуска. Общее время нагрева и выдержки рельсов в печи при отпуске составляет 2,5*3 часа. После отпуска рельсы не подвергают правки, в исключительных случаях допускается доправка на гибочных машинах.
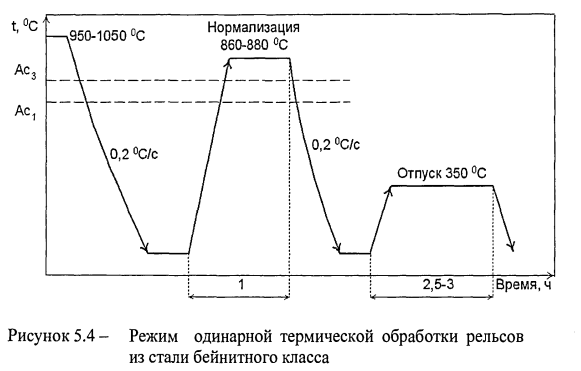
Согласно второй схеме термической обработки рельсы после охлаждения с прокатного нагрева подвергают последовательно правке в роликоправильной машине, нормализации и отпуску. Температура нагрева рельсов под нормализацию составляет 860 * 880 °С. Нагрев рельсов под нормализацию осуществляли в роликовой печи, сформировав их пакет по 5*9 шт. После выдачи из печи рельсы охлаждают на стеллаже до температуры цеха. Отпуск рельсов производится в роликовой печи при температуре 350 * 360 °С в течение 2,5 *3 часов. После отпуска рельсы подвергаются правке в роликоправльной машине.
Качество и свойства железнодорожных рельсов из сталей бейнитного класса
Разработанные технологии термической обработки применили при производстве железнодорожных рельсов из сталей бейнитного класса двух опытно-промышленных плавок. Качество термической обработки оценивали по результатам механических и копровых испытаний, анализа структурного состояния рельсов. Наряду с этим исследовали металлургическое качество рельсов. Металлургическое качество бейнитных рельсов оценивали по степени загрязненности металла неметаллическими включениями в соответствии с требованиями ГОСТ Р 51685 -2000.
Металлургическое качество рельсов, как известно, обеспечивается технологией раскисления стали. Введение в сталь легирующих элементов и микролегирующих добавок практически не сказалось на характере и морфологии неметаллических включений бейнитной стали двух опытных плавок. Металлографические исследования показали, что в металле двух плавок присутствует в основном характерные для углеродистых рельсов четыре типа неметаллических включений: сульфиды, оксисульфиды, пластичные силикаты и хрупкоразрушенные алюминаты кальция. Длина строчек пластичных силикатов стандартом не регламентирована, однако известно, что на рельсах этот вид неметаллических включений приводит к снижению ударной вязкости стали при температуре минус 60 °С [142]. Максимальная длина строчек пластичных силикатов в бейнитной стали опытных плавок № 1 и 2 в среднем составила соответственно 0,37 и 0,67 мм. Строчки хрупкоразрушенных алюминатов кальция имеют допустимую длину, которая для плавки № 1 в среднем составила 0,26 мм, для плавки № 2 — 0,86 мм. При этом повышенная загрязненность металла алюминатами кальция, как и пластичными силикатами отмечается на рельсах, прокатанных из хвостовой части непрерывнолитого слитка. Вместе с тем, в бейнитной стали опытных плавок полностью отсутствуют недопустимые строчки глинозёма и нитридов титана, а также глинозёма, сцементированного силикатами. В целом, по загрязненности бейнитная сталь опытных плавок практически не отличается от углеродистой стали стандартного состава.
Введение в сталь микродобавок ванадия, совместно с азотом, привело к образованию мелкодисперсных частиц карбонитридов ванадия, расположенных в объеме и по границам зерен (рисунок 5.5). Модифицирующее влияние микродобавок оказало тормозящее влияние на рост зерна аустенита.
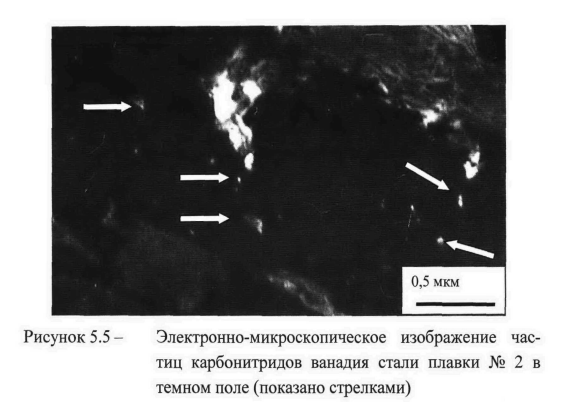
Измельчающее действие нитридообразующих элементов проявляется только после проведения термической обработки (нормализации или закалки) и выражается в повышении пластичности и ударной вязкости. В горячекатаном же состоянии влияние нитридообразующих элементов проявляется, как правило, только в некотором повышении прочности.
Удовлетворительное металлургическое качество рельсов из бейнитной стали определяется не только допустимой степенью загрязненности металла, но и отсутствием развития таких нормируемых для рельсовой стали макродефектов, как: осевая химическая неоднородность, точечная неоднородность и ликвационные полоски. Макроструктура металла опытных плавок удовлетворяет требованиям ГОСТ Р 51685-2000.
Бейнитная сталь относится к флокеночувствительным маркам стали, в этой связи задача предотвращения образования флокенов являлась одной из главных при освоении производства рельсов из бейнитной стали, особенно в условиях отсутствия на комбинате вакуумирования жидкой стали. Трудность решения задачи заключалась еще и в том, что существующая на комбинате технология противофлокенной обработки, включающая регламентированное замедленное охлаждение в коробах, также не могла быть использована из-за отсутствия магнитных свойств у бейнитной стали, в интервале температур 500 + 400 °С, при котором происходит наиболее эффективное удаление водорода.
Наиболее рациональным средством, позволившим предотвратить образование флокенов в бейнитных рельсах, явилось применение регламентированного охлаждения непрерывнолитых заготовок в термоямах. Выдержка непрерывнолитых заготовок в термоямах до температуры 300 + 100 °С использовалась, как правило, для снятия внутренних напряжений и в качестве противофлокенной обработки не применялась. Основываясь на теоретические расчеты, предусматривающие снижение водорода в заготовках от 4+6 до 1,5 ррш при температурах более 240 °С [143], время выдержки непрерывнолитых заготовок в термоямах увеличили до 72 часов, что обеспечило плавное снижение температуры заготовок от 500 до 100 °С. Регламентированный режим охлаждения заготовок в термоямах, а также медленное охлаждение рельсов на стеллажах после прокатки позволили предотвратить образование флокенов в бейнитных рельсах.
Исследования показали, что при охлаждении с температуры конца прокатки со скоростью 0,2 °С/с на рельсах двух опытно промышленных плавок достигается разный комплекс механических свойств.
По результатам механических испытаний установлено, что в наибольшей степени упрочняются рельсы плавки № 1, отличающиеся от рельсов плавки № 2, повышенным содержанием углерода, марганца, кремния и хрома. Попытка повысить твердость и прочностные характеристики за счет увеличения содержания углерода и основных легирующих элементов в стали привела к отрицательным результатам — твердость на подошве рельсов плавки № 1 достигла недопустимо высоких значений, которые составили 401 * 555 HB (таблица 5.1). При этом предел текучести головки этих рельсов составил — 1130 * 1170 Н/мм2, временное сопротивление разрыву — 1420 * 1490 Н/мм . Сравнительно высокое содержание углерода и легирующих элементов также отрицательно сказалось на пластических характеристиках рельса плавки №1. Рельсы указанной плавки показали низкие значения относительного удлинения (4 * 5 %) и относительного сужения (10 * 13 %). Вместе с этим, при испытании на ударный изгиб из рассматриваемых вариантов рельсовой стали на рельсах плавки №1 получены сопоставимые с объемно-закаленными рельсами значения ударной вязкости при плюс 20 °С и сравнительно низкие значения ударной вязкости при минус 60 °С.
Высокие твердость и прочностные характеристики в сочетании с низкими пластическими свойствами рельсов плавки №1 в горячекатаном состоянии обусловлены наличием смешанной структуры, состоящей из мартенсита, бейнита и остаточного аустенита (рисунок 5.6). Поскольку различить структуры нижнего и верхнего бейнита от мартенсита с помощью оптического микроскопа представляло большие трудности, их идентификацию проводили, основываясь на критерии, изложенные в работе [138]. Согласно данным работы, в микроструктуре рельсов исследуемой плавки можно отчетливо выделить нижний бейнит, наблюдаемый в виде двух модификаций: отдельных длинных грубых пластин, ориентированных под определенными углами друг к другу, и пластин более тонкого строения, плотно примыкающих друг другу, образующих пакет. Предполагается, что грубые пластинки бейнита образуются в первоначальный момент времени превращения аустенита, пластинки более тонкого строения и меньшего размера формируются несколько позже в стыках грубых пластин и по кристаллографическим плоскостям аустенита. Мартенсит в структуре исследуемых рельсов представлен преимущественно в виде реек, почти параллельно примыкающих друг к другу, образуя пакет.
Пакетный или реечный мартенсит отличается от пакетов бейнита меньшим размером. При этом отмечено, что структура горячекатаных рельсов имеет грубое игольчатое строение .Наилучшее сочетание механических свойств показали рельсы из бейнитной стали плавки №2. По результатам механических испытаний и измерения твердости видно (таблица 5.2), что рельсы из стали плавки № 2 в горячекатаном состоянии практически по всем механическим характеристикам превосходят объёмно- закалённые рельсы из стали марки Э76Ф.
Преимущество бейнитных рельсов плавки № 2 достигнуто по твердости (375 — 388 НВ), пределу текучести (880-890 Н/мм2), временному сопротивлению разрыву (1270-1290 Н/мм ), относительному удлинению (11-17 %) и ударной вязкости при температуре плюс 20 °С (32 — 37 Дж/см ). По относительному сужению (25 — 33 %) и ударной вязкости при температуре минус 60 °С (11 — 17 Дж/см2) горячекатаные рельсы плавки № 2 несколько уступают термически упрочненным рельсам из углеродистой стали. Указанный уровень механических свойств обусловлен образованием бейнитной структуры.
Согласно разработанной термокинетической диаграммы для стали (масс.: 0,30 % С; 1,56 % Мп; 1,4 % Бі; 1,3 % Сг) близкой по составу к стали плавки № 2, при скорости охлаждения 0,2 0 С/с должна формироваться структура состоящая из феррита, верхнего и нижнего бейнита (рисунок 5.7).
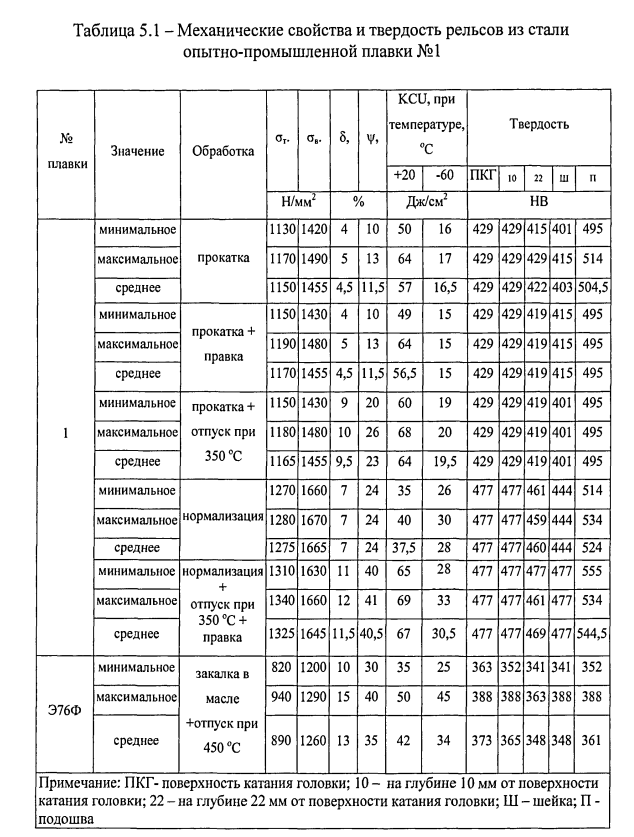
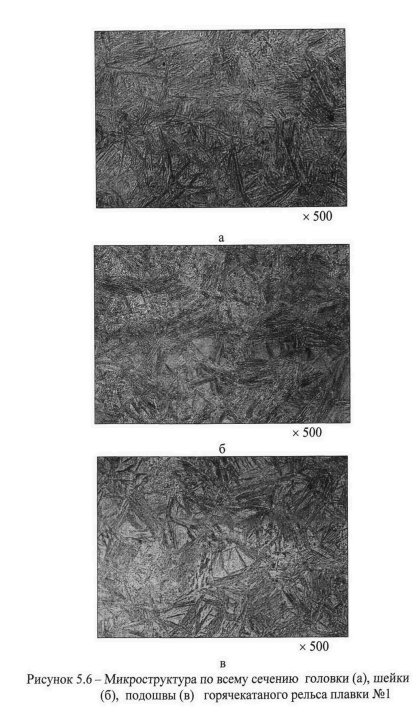
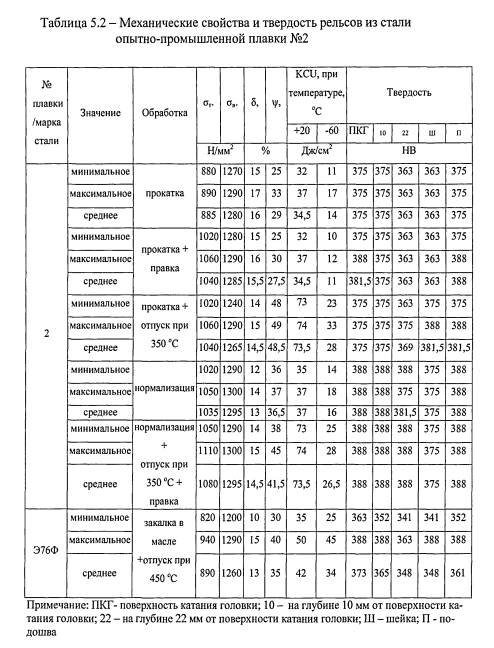
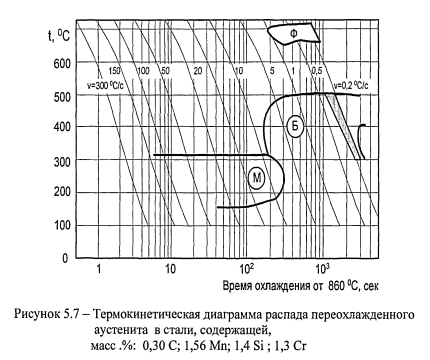
Поведенное металлографическое исследование горячекатаных рельсов плавки №2 выявило структуру бейнита (рисунок 5.8). При этом идентифицировать структуру на нижний и верхний бейнит не представилось возможным. В то же время результаты измерения твердости показали равномерное распределение твердости по глубине головки рельса опытной плавки № 2, что свидетельствует о достаточно однородной структуре этого рельса (рисунок 5.9). Сопоставление изменения твердости по глубине головки рельсов опытной плавки № 2 с объемно-закаленными рельсами из стали марки Э76Ф показало, что по мере удаления от поверхности снижение твердости в большей степени наблюдается на рельсах из стали марки Э76Ф, чем из стали опытной плавки № 2.
Видно, что характер изменения твердости головки опытных рельсов плавки №2 и объемно-закаленных рельсов из стали марки Э76Ф совпадает с поверхности и на глубине до 10 мм.
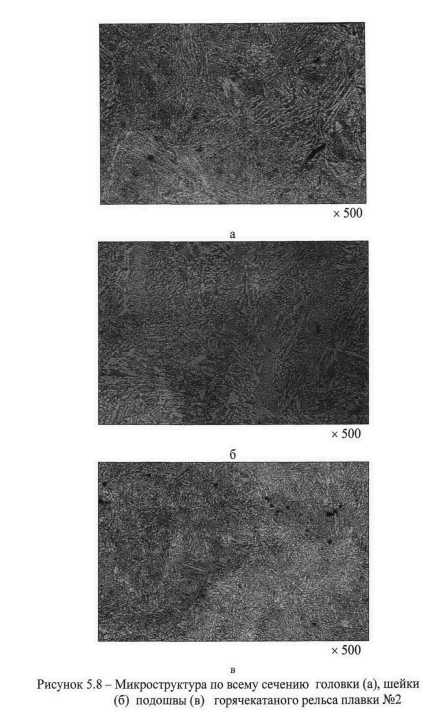
Далее твердость объемно-закаленных рельсов резко снижается до значения 36 НЯС. В то время, как на опытных рельсах отмечается некоторая стабилизация значений твердости на уровне 38 НІІС. Стабилизация значений твердости по глубине головки опытных рельсов указывает на однородность структурного состояния головки по всему сечению.
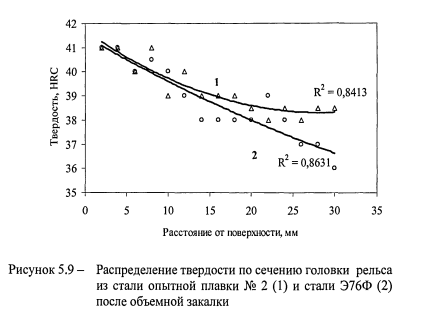
Механические свойства и структурное состояние повлияли на технологические свойства опытных рельсов. Рельсы плавки №1 правку не выдержали — разрушились в поперечном направлении, повышенная их хрупкость обусловлена присутствием в структуре стали мартенсита. В то же время рельсы плавки №2 удовлетворительно поддавались многократному упруго-пластическому изгибу. Попытка исправить кривизну рельсов плавки №1 при правке с меньшими усилиями оказалась безрезультатной — кривизна рельсов практически не исправлялась. Следует отметить, что правка в роликоправильной машине привела к повышению предела текучести и некоторому снижению ударной вязкости. Такое упрочнение стали, сопровождающее повышением предела текучести и снижением ударной вязкости, обусловлено деформационным упрочнением [139]. Это не просто упрочнение в результате наклепа (свойственное ферриту, и стабильному аустениту), в данном случае подобное изменение механических свойств связывают с превращением у-фазы в продукты бейнитного, возможно, и мартенситного превращений.
Рельсы двух плавок различаются не только по механическим и технологическим свойствам, но и имеют неодинаковый уровень копровой прочности. Бейнитные рельсы плавки № 2, в отличие от рельсов плавки № 1, показали высокую надежность против хрупких разрушений, о чем свидетельствует большая величина стрелы прогиба (20 мм) их копровой пробы, испытанной при цеховой температуре падающим грузом с высоты 7,3 м, тогда как стрела прогиба рельса плавки №1 составила всего 14 мм. Копровые испытания, проведенные при температуре минус 60 °С и падении груза с высоты 9 м, выдержали только рельсы плавки № 2, стрела их прогиба составила 24 мм. Копровые пробы от рельсов плавки №2 с первого удара разрушились на множество кусков, что свидетельствует о низкой сопротивляемости бейнитных рельсов №1 хрупким разрушениям.
Таким образом, исследования бейнитных рельсов двух опытных плавок, проведенные в горячекатаном состоянии, показали явное преимущество рельсов плавки № 2 по копровой прочности, механическим и технологическим свойствам.
Как было показано в предыдущих разделах, отпуск при 350 °С сталей бейнитного класса сопровождается повышением их пластичности и ударной вязкости. В свою очередь, холодная правка приводит к повышению предела текучести и снижению ударной вязкости при температуре минус 60 °С.
Ниже проанализировано суммарное влияние отпуска и холодной правки на механические свойства горячекатаных рельсов.
После отпуска при 350 °С и правки установлено заметное повышение предела текучести, которое на рельсах плавки №2 изменилось от 880 + 890 до 1020 — 1060 Н/мм2, на рельсах плавки № 1 — от 1130 — 1770 до 1150 + 1170 Н/мм2. Как видно, прирост предела текучести в большей степени наблюдается на рельсах плавки №2. При этом значения временного сопротивления возросли в меньшей степени. Если изменение предела текучести обусловлено влиянием правки, то повышение относительного сужения и ударной вязкости при плюс 20 °С достигнуто преимущественно за счет отпуска. В результате отпуска при 350 0 С относительное сужение рельсов плавки №1 повысилось от 10 — 13 до 20 — 26 % , рельсов плавки №2 — от 25 — 33 до 49 %. Ударная вязкость при плюс 20 °С отпущенных рельсов плавки №2 возросла практически в два раза по сравнению с исходным горяче-
л
катаным состоянием и составила 74 против 32-37 Дж/см . При этом микроструктура стали опытных плавок при отпуске практически не изменилась (рисунки 5.10). Отмечен лишь более отчетливый рисунок игольчатой структуры.
Благодаря существенному приросту относительного сужения и ударной вязкости при плюс 20 °С после отпуска, рельсы плавки №2 имеют заметное преимущество по сравнению с рельсами плавки №1, а также с объемно-закаленными рельсами из стали марки Э76Ф. Разное сопротивление рельсов опытных плавок хрупким разрушениям, выявленное при копровых испытаниях в горячекатаном состоянии, подтвердилось и в отпущенном состоянии. Испытания на копровую прочность при температуре минус 60 °С и падении груза с высоты 9 м рельсы плавки № 1 в отпущенном состоянии, также как и в горячекатаном состоянии, не выдержали — копровая проба разрушилась. Рельсы плавки № 2 в полной мере выдержали испытания, показав хорошую сопротивляемость стали хрупкому разрушению, стрела прогиба копровой пробы составила 25 мм, что находится на уровне объемно-закаленных рельсов из стали марки Э76Ф. Таким образом, благоприятное влияние отпуска при 350 °С, отмеченное на образцах лабораторных плавок, подтвердилась при испытании полнопрофильных рельсов опытно-промышленных плавок. К тому же проведение отпуска компенсировало отрицательное влияние холодной правки.
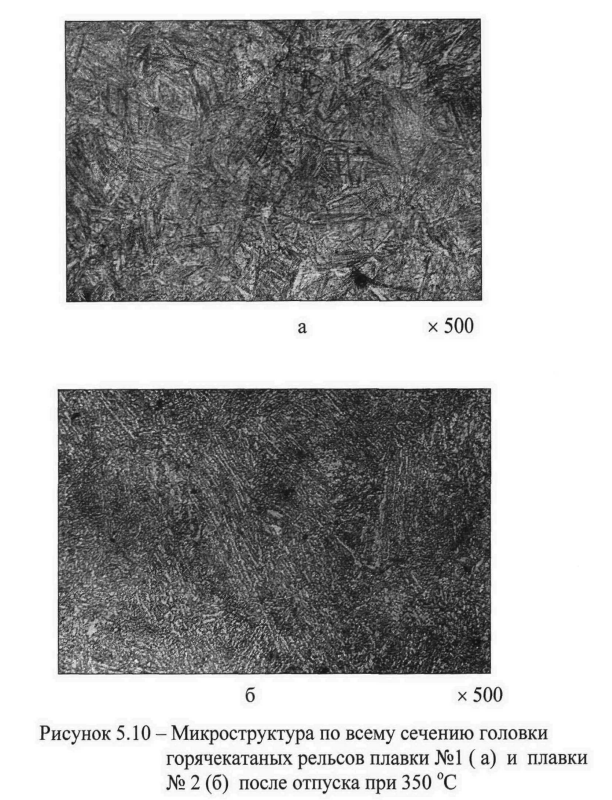
Проведение нормализации положительно сказалось на повышении механических свойств, особенно это заметно на свойствах рельсов плавки №1, чем рельсов плавки №2. Значения предела текучести и временного сопротивления разрыву рельсов плавки №1 после нормализации возросло соответственно до 1270 и 1600 Н/мм , тогда как в горячекатаном состоянии значение указанных характеристик находилось соответственно в пределах 1130 * 1170 и 1420 * 1470 Н/мм 2. Повышение прочностных свойств нормализованных рельсов плавки № 1 сопровождается снижением ударной
вязкости. Значения ударной вязкости рельсов плавки №1 значительно ниже в нормализованном, чем в горячекатаном состоянии и составили соответственно 35 — 40 и 50 — 64 Дж/см2. Подобное изменение свойств рельсов после нормализации, очевидно, связано с более полным у—превращением, а также измельчением зерна, что видно по более тонкому строению микроструктуры (рисунки 5.11 и 5.12). Бейнитная структура в рельсах плавки № 2 и бейнито-мартенситная структура в рельсах плавки №1 наблюдаются по всему сечению рельсов и характеризуется разной степенью дисперсности: наибольшую дисперсность имеет структура подошвы, а наименьшую — шейка. Промежуточное положение занимает головка рельса. Разная степень дисперсности по сечению рельса обусловлена неодинаковыми условиями охлаждения разных его элементов. Меньшая степень дисперсности структуры шейки, несмотря на ее малые геометрические размеры практически, соизмеримые с подошвой, объясняется, по- видимому, следующим: шейка, находясь между головкой и подошвой, охлаждается с меньшей скоростью из-за остаточного тепла, передаваемого в основном головкой и частично подошвой. Скорость же охлаждения головки и подошвы при прочих равных условиях определяется только их размерами.
Достигнутые после нормализации высокие прочностные и пластические характеристики, тем не менее, не обеспечили надежность рельсов плавки №1 против хрупких разрушений. Пробы нормализованных рельсов плавки № 1 не выдержали копровые испытания при температуре минус 60 °С и падении груза с высоты 9 мм. Тогда как рельсы плавки №2 в нормализованном состоянии, также как и в горячекатаном, выдержали копровые испытания, стрела их прогиба составила 25 мм, что свидетельствует о высокой надежности этих рельсов против хрупких разрушений.
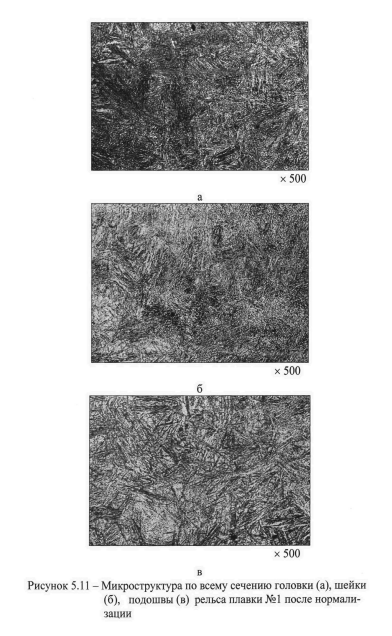
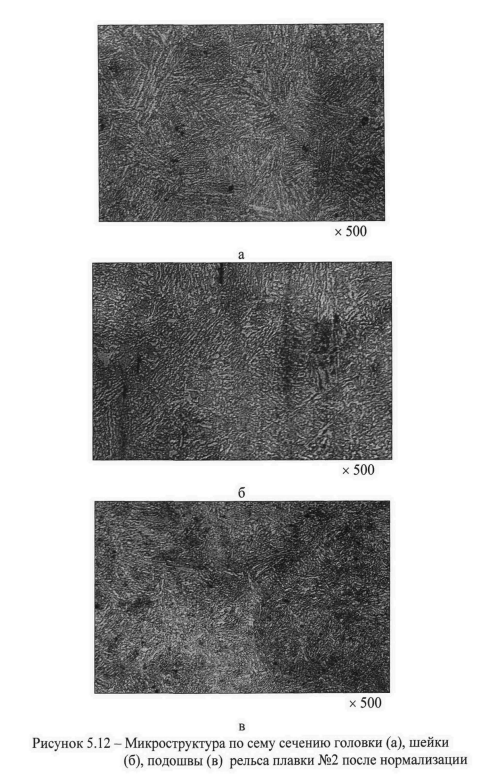
На горячекатаных рельсах однозначно установлено благоприятное влияние отпуска при 350 °С на пластические характеристики и ударную вязкость стали бейнитного класса. Помимо этого отмечено повышение предела текучести головки горячекатаных рельсов в результате холодной правки.
Для подтверждения установленных зависимостей исследовали влияние отпуска при 350 °С и последующей правки на механические свойства рельсов после нормализации.
Анализ полученных результатов показал, что нормализация с отпуском и правка обеспечили в рельсах опытных плавок повышение всего комплекса механических свойств. Сравнивая полученные результаты с результатами горячекатаных отпущенных рельсов, можно отметить, что нормализация с отпуском в совокупности с правкой приводят к большим значениям твердости, предела текучести и временного сопротивления разрыву. При этом прирост твердости и прочности заметен в большей степени на рельсах плавки № 1, чем рельсах плавки №2. Так, если максимальные значения предела текучести и временного сопротивления разрыву отпущенных горячекатаных рельсов плавки № 1 составили, соответственно,
л
1180 и 1480 Н/мм , то после нормализации и отпуска эти характеристики достигли, соответственно, следующих значений: 1340 и 1660 Н/мм . Для отпущенных горячекатаных рельсов стали плавки №2 максимальные значения предела текучести и временного сопротивления разрыву составили,
л
соответственно, 1060 и 1290 Н/мм . Практически такой же уровень указанных характеристик имели рельсы после нормализации и отпуска, который составил, соответственно, 1100 и 1300 Н/мм .
Положительное влияние нормализации с отпуском сказалось не только на повышении прочности и твердости, но и на достижении более высоких показателей пластичности и ударной вязкости. При этом в большей степени отмечено это влияние на изменении пластических характеристик рельсов плавки №1, чем рельсов плавки №2. По сравнению с горячекатаным состоянием относительное удлинение рельсов плавки №1 возросло в среднем от 9,5 до 11,5%, относительное сужение от 23 до 40, 5 % , ударная вязкость, испытанная при температуре минус 60°С, повысилась от 19, 5 до 30,5 Дж/ см . Тогда как показатели пластичности и ударной вязкости рельсов плавки № 2 после нормализации с отпуском находились на уровне горячекатаного состояния. При этом существенного изменения в микроструктуре сталей не выявлено. После нормализации и отпуска, также как и после прокатки и отпуска, отмечается отчетливый рисунок микроструктуры (рисунок 5.13).
Несмотря на повышение уровня пластичности и ударной вязкости рельсы плавки №1 низкотемпературные копровые испытания не выдержали. В отличие от рельсов плавки №1, рельсы плавки №2 выдержали копровые испытания, что свидетельствует о высокой надежности этих рельсов против хрупких разрушений. Наряду с этим рельсы плавки №2 после нормализации и отпуска показали и хорошие технологические свойства. В процессе правки на рельсах в 90 % случаях (рисунок 5.14) получена удовлетворительная прямолинейность, соответствующая требованиям высокоскоростного движения.. Тогда как на объемно-закаленных рельсах из стали марки Э76Ф количество таких случаев достигает всего лишь 70 %.
В отличие от рельсов плавки №2 рельсы плавки №1 плохо правились в роликоправильной машине или не выдерживали ее при приложении значительных нагрузок. Таким образом, из двух рассмотренных плавок наилучшим комплексом механических и технологических свойств обладает сталь, содержащая следующие основные химические элементы, масс. %: 0,32 С; 1,48 Мп; 1,21 81; 1,00 Сг.
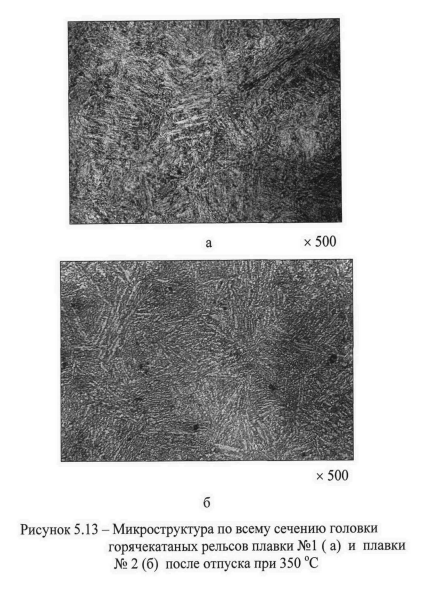
Для получения более полной информации по данной стали провели глубокий анализ ее структурного состояния методами просвечивающей электронной микроскопии тонких фольг.
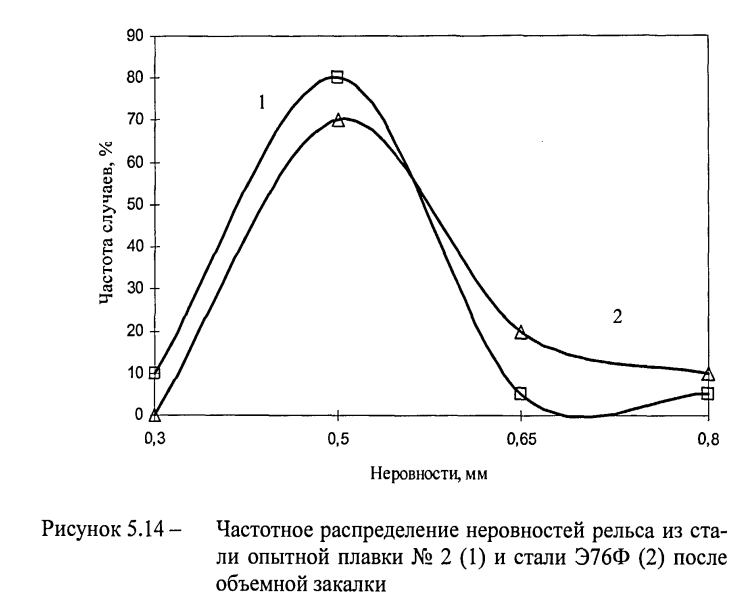
Электронно-микроскопическим исследованием установлено, что структура рельсов из стали указанного состава после нормализации и отпуска состоит из следующих структурных составляющих: реечного феррита, полиэдрических зерен феррита, остаточного аустенита и цементита (рисунок 5.15). По границам кристаллов реечного феррита расположены прослойки остаточного аустенита с наличием цементита. Остаточный ау- стенит распределен в структуре неравномерно. Количество его колеблется до 10 %.
Такую микроструктуру стали можно охарактеризовать, согласно классификации И. Охмори и другим работам [140,144-146], как структуру бескарбидного бейнита, состоящую из феррита и аустенита, сильно обогащенного углеродом.
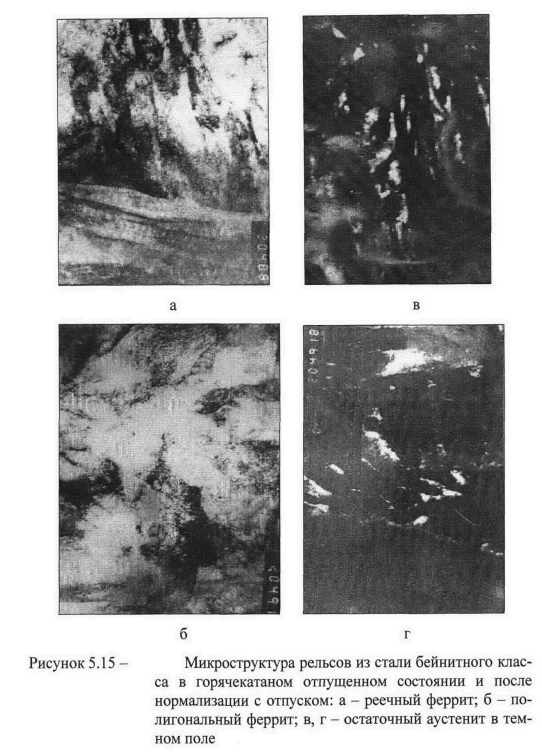
По данным работы [138] структура бескарбидного бейнита характеризуется значительной метастабильностью остаточного аустенита, поэтому для бескарбидного бейнита важными характеристиками являются не количество остаточного аустенита, сколько его стабильность. Стабильность остаточного аустенита оценивают по влиянию на его двух сильно действующих факторов: температуры и пластической деформации. В.Д. Счастливцев отмечает, что сталь со структурой бескарбидного бейнита обладает весьма высоким комплексом механических свойств и стабильность остаточного аустенита существенно влияет на свойства. В работе [137] отмечается, что появление под действием напряжений и пластической деформации хрупкой составляющей — мартенсита не обязательно ведет к развитию макроскопической хрупкости и преждевременному разрушению. В определенных условиях, напротив, вызванное деформацией превращение сопровождается микро ПНП-эффектом, т.е пластичностью, наведенной превращением, которая в безуглеродистых сталях улучшает комплекс свойств. Разработка этого направления принадлежит В.Ф. Заккею, Э.Р. Паркеру в США, И.Тамуре в Японии, а также отечественным исследователям: О.П.Максимовой, И.Я.Георгиевой, В.Н. Замбржицкому, И.Н. Богачу- ву, А.И. Уварову и др.
Дополнительное исследование микроструктуры, проведенное с помощью растрового микроскопа-микроанализатора LEO EVO-40, показало наличие ферритных пластин гребнеобразной и игольчатой формы (рисунки 5.16, 5.17). При этом в ферритных пластинах карбидов не выявлено. Пластины феррита имеет однородное строение (рисунок 5.18).
На основании полученных положительных результатов по исследованию опытных рельсов из стали бейнитного класса были разработаны технические условия ТУ 0921-167 оп- 01124323 -2003 «Рельсы железнодорожные типа Р 65 высокой прочности из бейнитной стали» (приложение А) для производства рельсов из стали бейнитного класса.
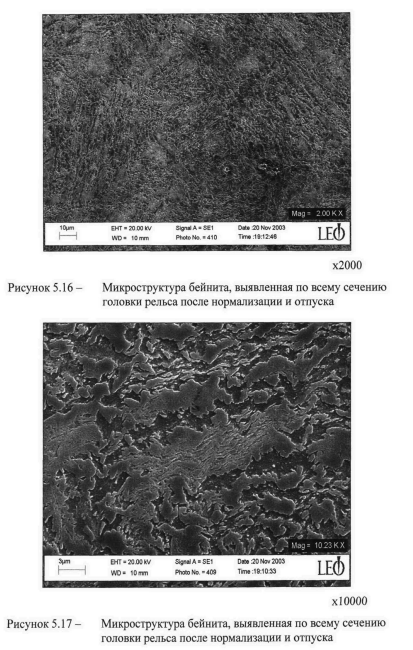
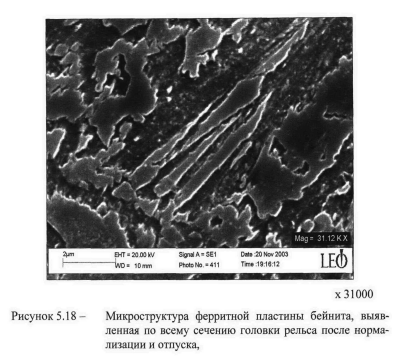
Оценка технико-экономического и энерго-экологического
эффекта при нроизводстве рельсов из сталей бейнитного класса
Наряду с достижением высоких показателей качества выпускаемой рельсовой продукции не менее важным является вопрос повышения экономической эффективности и экологической безопасности производства.
Разработка рельсовой стали бейнитного класса и внедрение новой технологии термической обработки позволила не только улучшить экологические условия работы, за счет исключения из технологического цикла пожароопасного индустриального масла, но и существенно снизить производственные затраты. При существующем на ОАО «НКМК» оборудовании возможна реализация четырех вариантов технологии термической обработки железнодорожных рельсов из сталей перлитного и бейнитного класса, которые представлены, соответственно, на рисунках 5.19 и 5.20. Оценку техникоэкономических и энерго-экологических аспектов действующей и разработанной технологии термической обработки проводили анализируя следующие факторы: удельные затраты тепла на осуществление термической обработки, комплекс механических свойств железнодорожных рельсов, возможность исключения из цикла термической обработки стадии закалки в масле. Анализ полученных результатов представлен в таблице 5.3. Как видно из таблицы 5.3 разработанные технологии термической обработки железнодорожных рельсов из стали бейнитного класса марки Э30ХГ2САФМ имеют ряд преимуществ по сравнению с действующими. В частности, удельные затраты тепла при термической обработке рельсов из сталей бейнитного класса по варианту II (рисунок 5.20) практически в 4 раза меньше по сравнению с вариантом II (рисунок 5.19) термической обработки рельсов из стали перлитного класса, при этом комплекс механических свойств более высокий, чем у объемнозакаленных рельсов. При отоплении заколочной и термической печи природным газом средний удельный расход условного топлива достигает 120 кг.у.т./ т стали, соответственно, столь значительное сокращение удельных затрат тепла приводит к ощутимой экономии природного газа. При термообработке бейнитных рельсов по варианту I (рисунок 5.20) затраты тепла несколько выше (в среднем на 3-6 %) по сравнению с технологий объемной закалки, что связано с повышенной температурой нагрева в закалочной печи и необходимости нагрева рельсов в отпускной печи от 60 до 350 °С (на 290 °С), а при отпуске объемнозакаленных рельсов от 200 до 450 °С (на 250 °С).
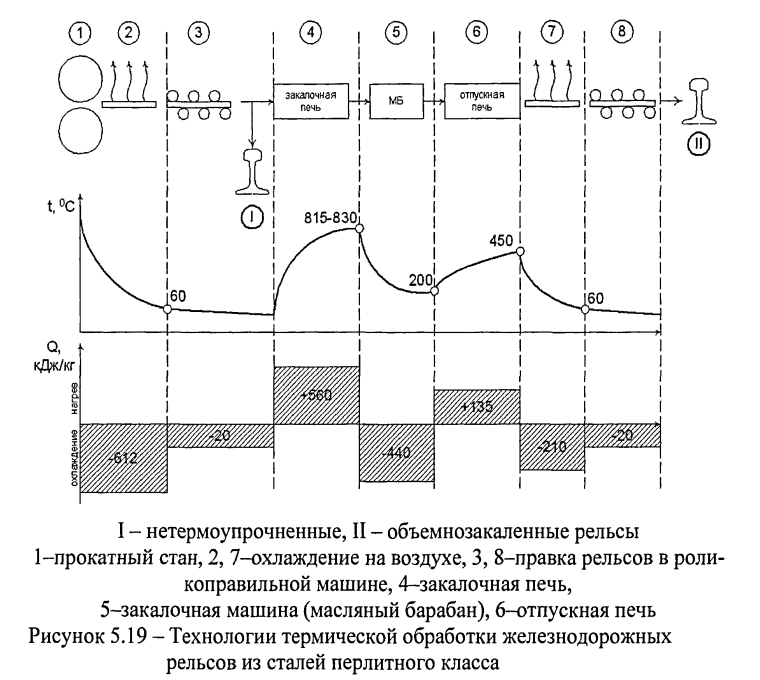
Как видно из таблицы 5.3, рисунка 5.20 и как неоднократно отмечалось выше, разработанные технологии термической обработки рельсов из сталей бейнитного класса позволяют исключить стадию закалки в масле, соответственно, вывести из эксплуатации закалочную машину, являющуюся одним из самых экологически неблагоприятных агрегатов в технологии производства рельсов. Наиболее экологически опасными являются выделяющиеся пары масла.
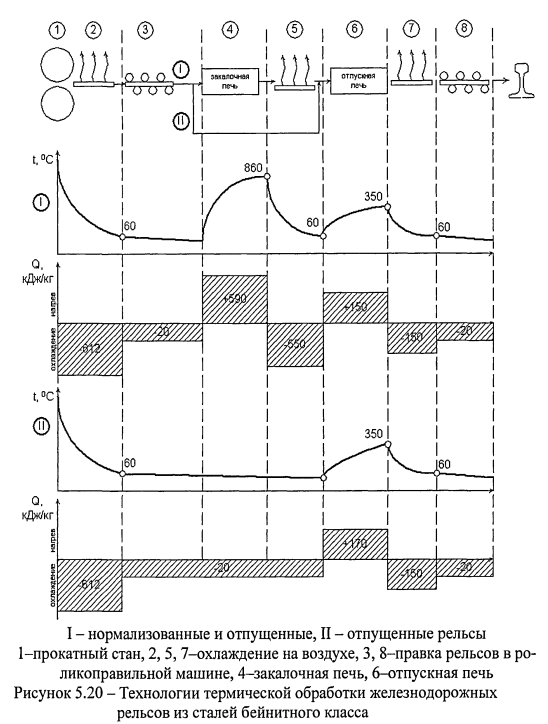
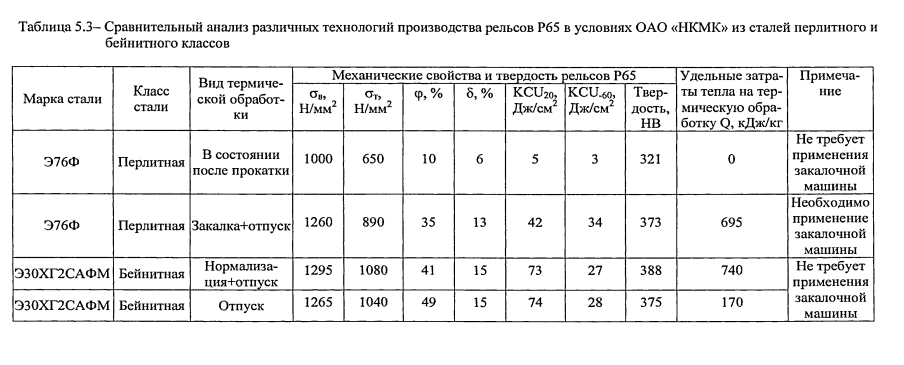
По данным различных источников при закалке металлоизделий в масляных ванная в отводящемся от ванн воздухе может содержаться до 1 % паров масла от массы теомообрабатываемых изделий. Исключение закалки в масле позволяет снизить общую себестоимость рельсов, исключить затраты на обслуживание закалочной машины, расходы на
индустриальное масло. Совокупный прогнозируемый экономический эффект от производства железнодорожных рельсов из стали бейнитного класса марки Э30ХГ2САФМ при минимальном объеме производства 50 тыс. тонн составил 3 600 тыс. руб. в год.
Выводы
- Для производства рельсов из сталей бейнитного класса разработаны,освоены и внедрены в производство две технологии термической обработки: с прокатного нагрева и перекристаллизационного нагрева под нормализацию с последующим отпуском при 350 °С.
- Железнодорожные рельсы, изготовленные из опытных сталей бейнитного класса, показали удовлетворительное металлургическое качество, сопоставимое с качеством рельсов из стали марки Э76Ф.
- Установлено, что при непрерывном охлаждении на воздухе как с прокатного нагрева, так и после нормализации, на рельсах из сталей опытных плавок обеспечиваются высокие прочностные свойства. При этом на рельсах из стали с содержанием углерода 0,40 % достигаются более высокие прочностные свойства, намного превосходящие свойства объемно-закаленных рельсов из стали марки Э76Ф. Более низкие прочностные характеристики, сопоставимые с объемно-закаленными рельсами, обеспечиваются на рельсах из стали с содержанием углерода 0,32 %. Высокие прочностные свойства бейнитных рельсов в горячекатаном и нормализованном состояниях сопровождаются пониженной пластичностью и ударной вязкостью. Более низкая пластичность отмечена на рельсах с содержанием углерода 0,40 %, низкая ударная вязкость — рельсах с содержанием углерода 0,32 %. Повышение пластических свойств и ударной вязкости без снижения прочностных характеристик обеспечивается на рельсах из бейнитной стали после отпуска при 350 °С. При этом наилучшее сочетание механических характеристик достигнуто на рельсах с содержанием углерода 0,32 %.
- Установлено, что после холодной правки у рельсов из стали бей- нитного класса достигается повышение предела текучести и снижение ударной вязкости при минус 60 °С. Пластическую деформацию, обусловленную правкой, можно рассматривать как дополнительное упрочнение стали и как явление, которое может возникнуть в результате контактного взаимодействия рельса с колесом при эксплуатации.
- Металлографическое исследование показало, что при содержании в стали углерода 0,32 % при непрерывном охлаждении на воздухе образуется однородная бейнитная структура по всему сечению рельса. В стали с содержанием углерода 0,40 % формируется в основном структура, состоящая из бейнита, мартенсита и остаточного аустенита.
- В процессе производства отмечена повышенная хрупкость рельсов из бейнитной стали с содержанием углерода 0,40 %. Рельсы из этой стали практически не поддаются правке при приложении небольшой нагрузки и хрупко разрушаются при увеличенном давлении. Удовлетворительные технологические свойства показали рельсы из бейнитной стали с содержанием углерода 0,32 %. В результате правки на этих рельсах получена прямолинейность, соответствующая требованиям скоростного движения.
- На основании проведенного анализа разработаны технические условия ТУ 0921-167 оп- 01124323 -2003 для производства рельсов из стали бей- нитного класса марки Э30ХГ2САФМ
- 8.Совокупный прогнозируемый экономический эффект от производства железнодорожных рельсов из стали бейнитного класса марки Э30ХГ2САФМ при минимальном объеме производства 50 тыс. тонн составил 3 600 тыс. руб. в год.
Список литературы
- Казарновский Д.С. Разработка, освоение и внедрение низколегирован¬ной стали для железнодорожных рельсов тяжелых типов / Д.С. Казар¬новский, М.А. Гершгорн, Ф.Ф. Свириденко // Сталь.- 1964.- № 4.- С.45 — 55.
- Изготовление и термическая обработка легированных мартеновских рельсов / Ю.В. Грдина [и др.] // Вопросы производства и исследования железнодорожных рельсов. — М.: Академия наук, i960.- С.79 — 93.
- Казарновский Д.С. Разработка оптимального состава и режим термиче¬ской обработки легированной стали для железнодорожных рельсов : Вопросы производства и исследования железнодорожных рельсов. — М.: Академия наук, 1960. — С.93 — 104.
- Дерябин A.A. Повышение качества рельсовой титаносодержащей стали / A.A. Дерябин, В.Е. Семенков, Б.И. Топычканов // Сталь.- 1987. -№ 12.- С. 17-19.
- Дерябин A.A. Улучшение качества рельсов из стали, раскисленной алюминием / A.A. Дерябин, В.В. Могильный, А.Б. Добужская // Сталь.- 1997.-№7,- С.50-55.
- Производство рельсов из дисперсионно — упрочненной стали / В.И. Ворожищев [и др.] // Изв. вузов. Черная металлургия.- 2004. — № 2.- С. 47 -52.
- Изучение свойств рельсовой стали Э 76Ф, микролегированной молиб¬деном / В.И. Ворожищев [и др.] // Материалы юбилейной рельсовой ко¬миссии: сборник докладов.- Новокузнецк,- 2002.- С. 294 — 300.
- EN 13674 — 1: 2003 «Железные дороги — Путь- Рельсы. Часть 1: Же¬лезнодорожные рельсы Виньоля 46кг/м и более».
- Освоение производства магистральных рельсов типа Р65 из низколеги¬рованных марок стали /О.В. Носоченко [ и др.] // Металлургическая и горнорудная промышленность.- 2003.- № 4.- С.66-69.
- Состояние и перспективы производства нетермоупрочненных рельсов из низколегированной стали на ОАО «НТМК» / В.И. Ильин [и др.] // Материалы юбилейной рельсовой комиссии. — Новокузнецк: Полиграф- комбинат, 2002.- С.290-294.
- Корнева J1.B. Качество рельсов для высокоскоростного движения / JI.B. Корнева, Т.Н. Осколкова // Вестник горно-металлургической секции Российской академии естественных наук: сб. науч. тр. СибГИУ. — Ново- узнецк, 2006.- Вып. 16.- С.97 — 101.
- Качество рельсов из низколегированной стали М70ХГСФ / Г.С. Гахе- ладзе // Сталь.- 2001.- № 4. — С. 65 — 66.
- Козлов А.В. Рельсовая сталь // Производство проката.- 2005.- №8- С. 41 -46.
- Kern A. The development of bainitic steels for special railwaysustem reguirements./A. Kern, H. Schmedders // Ibid.- P. 1015-1021.
- Yokoyama H. Wear and Rollinq Contact Fatique Behavior in Pearlitic and Bainitic Rail Steels. / H. Yokoyama, S. Mitao and S.Yamamoto. Proceedinqs 7th International Heavy Haul Conference.- Brisbane, Australia, — 2001,- p.551 -557.
- Yokoyama H., Yamamoto S., Fuyikake M. and Yoshida Y. Characterization of bainite rails and pearlite rails used in hiqh freiqht railroads in terms of wear resistance and damaqe resistance. 39th MWSP Conf. Proc., vol. 35, 1998.- p.1023- 1028.
- Steele R. Alloyinq Considerations for Heat Treatment of a Lower Bainite Microstructure. 39th MWSP Conf. Proc., vol. 35.- 1998, p.997 — 1006.
- Опыт производства рельсов из стали бейнитного класса на НТМК / А.В. Кушнарев [и др.] // Сталь.- 2005.- № 6.- С.131 — 133.
- Стали для рельсов высокоскоростных линий // Железные дороги мира. -2000.-№8.- С.67-70.
- Рельсы высокой прочности с бейнитной структурой, полученной с про¬катного нагрева / Де Боер X. [и др.] // Черные металлы.- 1995.- С. 29 — 36.