Сейчас ваша корзина пуста!
Теоретические предпосылки разработки химического состава сталей бейнитного класса
Цикл статей:
Глава 1 — Разработка химического состава и технологии термической обработки железнодорожных рельсов из стали бейнитного класса
Глава 2 — Теоретические предпосылки разработки химического состава сталей бейнитного класса
Глава 3 — Оборудование и методика экспериментальных исследований
Глава 4 — Исследование влияния различных видов термической обработки на структуру и свойства сталей бейнитного класса
Глава 6 — Служба железнодорожных рельсов из сталей бейнитного класса
Концепция разработки химического состава сталей бейнитного класса для производства железнодорожных рельсов
В основу разработки химического состава сталей бейнитного класса для производства железнодорожных рельсов легли следующие основные положения: необходимость обеспечения однородной бейнитной структуры по всему сечению рельса без использования закалочного охлаждения; использование экономнолегирующих химических элементов; обеспечение высокого уровня механических и технологических свойств железнодорожных рельсов; повышение эффективности производства; улучшение экологических условий труда.
Обеспечение однородной бейнитной структуры применительно к рельсам достигается рациональными концентрационными пределами легирующих элементов. К числу элементов, расширяющих область бейнитного превращения, относят углерод, марганец, кремний, хром, никель, молибден и т.д. Легирование стали тем или иным элементом для достижения требуемого структурного состояния и механических свойств при прочих равных условиях определяется, в конечном счете, экономической эффективностью. В данном случае из представленного ряда легирующих элементов наиболее недефицитными и недорогими являются марганец, кремний и хром.
При разработке химического состава рельсовой стали бейнитного класса основным критерием требуемого уровня механических свойств является достижение наиболее высоких характеристик прочности, пластичности, ударной вязкости и хладостойкости. К требуемым технологическим характеристикам следует отнести способность бейнитной стали к горячему и холодному деформированию, механической обрабатываемости и свариваемости. При этом последняя характеристика является наиболее важной в условиях развития бесстыкового железнодорожного пути.
Применение сталей бейнитного класса для производства рельсов позволит исключить из технологического цикла производства рельсов применение индустриального масла, обеспечив, тем самым, повышение как эффективности производства, так и экологической безопасности. При этом исключение из технологического цикла закалочного охлаждения благоприятно сказывается на уменьшении кривизны рельсов в процессе производства, что позволяет свести до минимума холодную правку и соответственно снизить остаточные напряжения в рельсе.
Влияние легирующих элементов на формирование бейнитной структуры стали
Особенности кинетики превращения аустенита в промежуточной области определяются легированием стали. Многие легирующие элементы увеличивают продолжительность инкубационного периода, понижают верхнюю границу (Бн), температуру максимума скорости превращения и скорость промежуточного превращения [132]. По интенсивности воздействия (в убывающем порядке) легирующие элементы располагаются следующим образом: марганец, хром, никель, кремний. Легирование молибденом и вольфрамом оказывает сравнительно слабое влияние на кинетику превращения. На структуру, формирующуюся при бейнитном превращении, и ее свойства существенно влияет содержание углерода. Малоуглеродистые стали (не более 0,10 %), легированные хромом, никелем и молибденом, имеют структуру без карбидов, состоящую из зернистого бейнита. Стали с более высоким содержанием углерода (не менее 0,25 %) имеют игольчатую структуру из верхнего- и нижнего бейнита с выделением карбидов [127].
Влияние легирующих элементов на скорость роста кристаллов а- фазы бейнита связывают со смещением температурного интервала превращения к более низким температурам, изменением подвижности атомов углерода и градиентов концентрации у границы аустенит — феррит. Повышение отношения концентраций хрома и углерода, например в аустените, может обусловить полное подавление бейнитного превращения; при этом резко понижается подвижность углерода.
В углеродистых и легированных сталях при температурах образования верхнего бейнита возникает цементит (БезС). Содержание легирующих элементов в цементите бейнита приблизительно равно средней концентрации их в стали. Независимо от путей образования цементита (из аустенита или а- фазы) это указывает на практическое отсутствие диффузионного перераспределения легирующих элементов при промежуточном превращении. Некоторое обогащение цементита легирующими карбидообразующими элементами наблюдается иногда при наиболее высоких температурах промежуточной области и может рассматриваться как вторичный процесс (перераспределение легирующих элементов между а-фазой и цементитом). В некоторых сталях, легированных, например, кремнием, карбидные фазы при определенных температурах промежуточного превращения вовсе не возникают.
Определение концентрации углерода в а-фазе, образующейся при промежуточном превращении, — является трудной задачей, так как вслед за образованием этой фазы может немедленно происходить ее распад или дальнейший переход атомов углерода из а-фазы в аустенит.
Отпуск после промежуточного превращения приводит к образованию тем большего числа карбидных частиц внутри кристаллов а-фазы, чем ниже температура превращения. Это свидетельствует о том, что концентрация углерода в а-фазе тем выше, чем ниже температура превращения, тогда как, при одинаковой степени превращения содержание углерода в аустените тем больше, чем выше температура превращения.
В работе [134] отмечается, что чем выше температура аустенитизации и чем, соответственно, выше исходное содержание углерода в аустените, тем он стабильнее, тем легче получать в металле «бескарбидный» бейнит, называемый аусферритом. Именно последний и обладает наилучшим комплексом механических свойств и устойчивостью даже при низких температурах. А.А. Жуков отмечает, что развитие теории и практики получения аусферритных сплавов системы Бе-С является наиболее важным вопросом в связи с тем, что бескарбидные сплавы обладают очень высокими механическими свойствами и стабильностью.
Основные факторы, определяющие прочность бейнита — величина кристаллов а-фазы, дислокационная субструктура, содержание углерода в а-фазе, форма и распределение карбидных частиц. С понижением температуры превращения величина кристаллов а-фазы уменьшается, плотность дислокаций возрастает, содержание углерода в а-фазе повышается, карбидные частицы распределяются преимущественно внутри кристаллов а- фазы, что характерно для нижнего бейнита. Это приводит к росту предела текучести. Превращение аустенита, приводящего к образованию в структуре стали верхнего бейнита, вызывает резкое снижение механических свойств и особенно сопротивление хрупкому разрушению после отпуска в широком диапазоне температур [135]. В формировании той или иной структуры решающая роль отводится легированию стали. Легирующие элементы могут заметно смещать температурную область промежуточного превращения к более низким температурам, понижать диффузионную подвижность углерода в аустените, изменять градиенты концентрации углерода на межфазных границах аустенит — феррит и феррит — карбид.
Анализ условий стабильного получения бейнитной структуры
стали в условиях спокойного охлаждения на воздухе
Выбор основных легирующих элементов определялся необходимостью получения бейнитной структуры по всему сечению рельса при непрерывном охлаждении на воздухе от температуры аустенитизации. Для получения бейнитного превращения в широком диапазоне скоростей охлаждения необходимо расширить область бейнитного превращения, что достигается степенью легирования стали. Характер влияния легирующих элементов на бейнитное превращение зависит и от интенсивности охлаждения. В данном случае это влияние рассмотрено применительно к охлаждению стали на спокойном воздухе при нормализации[*].
В связи с этим научной основой для выбора требуемого состава послужил атлас диаграмм Аткинса [136], позволяющий прогнозировать структуру изделия в зависимости от его размера и скорости охлаждении. Для получения прогнозируемой бейнитной структуры профиль рельса условно разбили на простые геометрические формы (пластины) размером 40×70 мм (головка) и 20×20 мм (подошва и шейка).
Допустив, что размер пластин соизмерим с диаметрами (50 и 20 мм) цилиндрических образцов, по диаграммам Аткинса определили, что бей- нитная структура в заданных сечениях обеспечивается при охлаждении на спокойном воздухе при следующих концентрационных пределах химических элементов, масс. %: 0,20 — 0,50 С; 0,18 — 0,34 81; 0,50 — 1,55 Мп; 0,45 — 3,10 Сг; 0,28 — 0,55 Мо; 0,19 — 0,85 № (таблица 2.1).
Из рассмотренного ряда легирующих элементов наиболее сильное влияние на формирование бейнитной структуры оказывает углерод, марганец, хром, молибден и никель. При выборе системы легирования стали исходили из необходимости получения стабильной бейнитной структуры с учетом достижения экономической эффективности производства стали. Из экономических соображений никель в качестве легирующего элемента не рассматривали. По этой же причине ограничили содержание хрома и молибдена, соответственно, в пределах 0,40 + 1,20 % и 0,20 0,30 %. Для эффективности бейнитного превращения содержание марганца и кремния установили, соответственно, в пределах 0,90 1,80 и 0,70 1,60 %. Концентрационные пределы микролегирующих добавок ванадия и азота установили, исходя из данных работ [113].
Согласно работе [137] для бейнитных сталей предусматривается проведение нормализации, заключающейся в нагреве до температуры Ас3 + 30 «С и охлаждении на воздухе. В дальнейшем под нормализацией следует понимать охлаждение стали на спокойном воздухе от температуры аустенитизации.
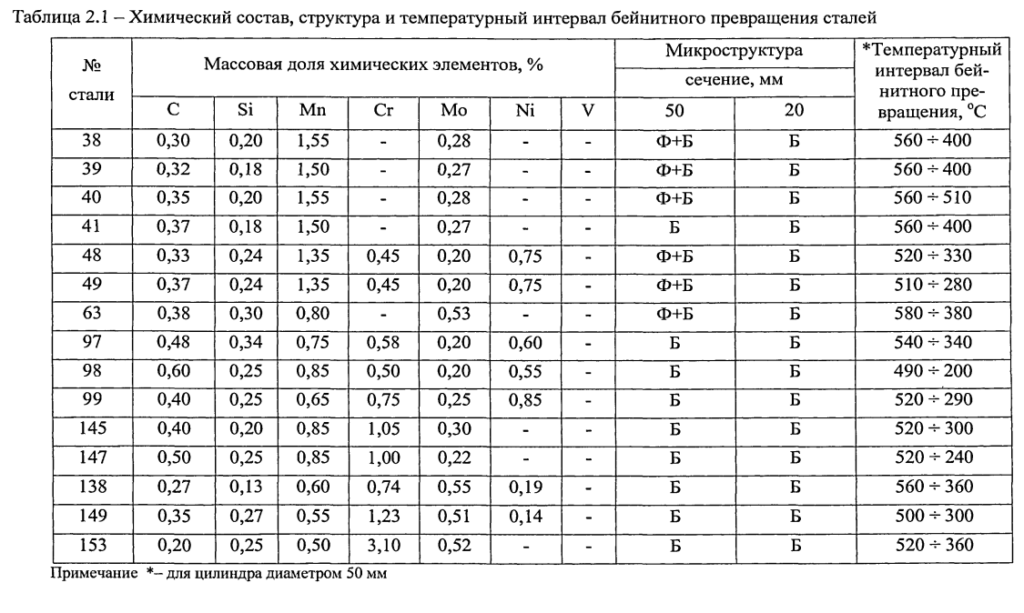
Список литературы
- Рельсы — основа железных дорог // Вестник деловой и коммерческой информации. — 2000.- № 2.- С. 2-3.
- Концепция нового национального стандарта на железнодорожные рель¬сы / A.A. Дерябин [и др.] // Сталь.- 2005.- №6.- С. 139 — 141.
- Козырев А.И. Истинные причины волнообразных неровностей (Дефект поверхности катания головки) // Путь и путевое хозяйство. 2003.- №9.-26-27.
- Рейхард В.А. Прямые рельсы / В.А. Рейхард, Е.А. Шур // Путь и путевое хозяйство. — 2002.- №12.- С.7-8.
- Абдурашитов А.Ю. Закономерности образования контактно — усталост¬ных дефектов // Путь и путевое хозяйство. — 2002.- №11.- С. 16-20.
- Решение и рекомендации Российской межведомственной Рельсовой ко¬миссии по улучшению качества и эксплуатации железнодорожных рель¬сов и рельсовых скреплений // Материалы Рельсовой комиссии: сб. док. ОАО «НТМК», 2000.- С.181-188.
- Изломы рельсов на дорогах Великобритании // Путь и путевое хозяйст¬во. — 2000.-№ 3.- С.39-40.
- Георгиев М.Н. Трещиностойкость железнодорожных рельсов./М.Н. Ге¬оргиев.- Кемерово, 2006.- 212с.
- Davies K.V. Analytical and experimental study of resid stress in rail / K.V. Davies, T.G. Johns // Transp.Rec.-1987.- № 794. — P.19 -24.
- Steel R.K. Fatigue crack growth and fracture mechanic considérations for flaw inspection of railroad rail // Material Evaluations. — 1980.- № 10.- P.33-38.
- Поляков B.B. Основы технологии производства железнодорожных рель¬сов./ В.В. Поляков, А.В. Великанов. — М.: Металлургия, 1990.- 416с.
- Повышение качества рельсов раскислением комплексными сплавами, содержащими кальций и титан / А.А. Дерябин [и др.] // Сталь.- 1983.- № 12.- С.59-63.
- Снижение загрязненности рельсов строчечными оксидными включе¬ниями при раскислении стали FeSiCaVAl сплавами / А.А. Дерябин [и др.] // Металлург.-1980.- № 12.- С.20 -23.
- Снижение загрязненности рельсов оксидными включениями при рас¬кислении стали FeSiCa+FeSiZr / А.А. Дерябин [и др.] // Металлург.- 1981.-№2,- С.30-32.