Сейчас ваша корзина пуста!
Совершенствование технологии восстановления колесных пар повышенной твердости
Цикл статей:
Глава 1 — Совершенствование технологии восстановления колесных пар повышенной твердости
Глава 2 — Перспективы использования колес повышенной твердости
Глава 3 — Теоретическое исследование процесса восстановления профиля катания колесных пар повышенной твердости
Глава 4 — Экспериментальное исследование обрабатываемости бандажной стали повышенной твердости
Глава 5 — Оптимизация процесса восстановления колесных пар повышенной твердости
Глава 6 — Технико-экономическая оценка результатов исследования
Введение
Актуальность.
Взаимодействие колеса и рельса является физической основой движения подвижного состава по железным дорогам. От параметров этого взаимодействия во многом зависят безопасность движения и основные технико-экономические показатели хозяйств пути и подвижного состава. Так, в частности, потери энергии, обусловленные изнашиванием в системе колесо-рельс, составляют 10 — 30 % расходуемых топливно-энергетических ресурсов на тягу поездов. Кроме того, расходы на реновацию рельсов и колесных пар составляют немалую часть общих расходов дистанций пути, локомотивных и вагонных депо соответственно. Особенно большие издержки в связи с этими расходами терпят локомотивные депо, поскольку за последние полвека средний срок службы локомотивной колесной пары существенно сократился.
Среди причин, вызвавших в 70 — 90 гг. прошлого столетия значительное возрастание интенсивности изнашивания колесных пар, следует отметить замену буксовых подшипников скольжения подшипниками качения, увеличение длины и массы поездов, сужение колеи до 1520 мм, введение профиля рельсов, предусматривающего двухточечный контакт бандажа с головкой рельса и др. Все это в совокупности привело к существенному изменению нагруженности зоны контакта, температуры и условий смазывания в этой зоне, а также к изменению среднестатистической скорости скольжения колеса в поперечном относительно головки рельса направлении. Результатом этих изменений стало существенное возрастание интенсивности изнашивания колес подвижного состава, которое в свою очередь привело к катастрофическим результатам для локомотивного и вагонного хозяйств.
Для преодоления сложившейся ситуации МПС РФ принята «Программа реорганизации и развития отечественного локомотиво- и вагоностроения, организации ремонта и эксплуатации пассажирского и грузового подвижного состава на период 2001 — 2010 гг.». Одна из основных задач, выдвинутых этой программой, — повышение ресурса бандажей колесных пар локомотивов: на первом этапе — до 0,6 млн. км; на втором — до 1,2 млн. км. Таким образом, проблемы повышения износостойкости колесных пар, в частности, за счет повышения твердости обода и качества восстановления при ремонте этим документом обозначены как одни из наиболее приоритетных.
Объект исследования — колесная пара.
Предмет исследования — процесс восстановления бандажных колесных пар подвижного состава повышенной твердости.
Цель диссертационной работы.
Разработка рекомендаций по повышению эффективности процесса восстановления бандажных колесных пар повышенной твердости при ремонте.
Достижение поставленной цели предполагает решение следующих задач:
- оценка соотношения твердостей колеса и рельса (НВК / НВр) и его влияние на повышение ресурса;
- экспериментальное и теоретическое исследование процесса восстановления бандажной стали повышенной твердости;
- оптимизация режимов восстановления бандажей повышенной твердости и разработка рекомендаций по их практическому применению.
Методы исследования.
Исследования выполнялись на основе системного подхода к вопросам анализа функционирования и ремонта колесных пар, включая оценку напряженно- деформированного состояния (НДС) бандажного колеса повышенной твердости, его износа и особенностей его восстановления при ремонте. Теоретической базой проведения исследований послужили метод конечных элементов (МКЭ), метод подобия, программные комплексы А^УБ, Со5то5\\’гогк5, МАБТЯАМ, положения ряда разделов фундаментальных наук (механики, теплофизики и др.) и теории резания. Экспериментальные исследования (в том числе с использованием метода планирования эксперимента) проводились в лабораторных и производственных условиях.
Автор защищает.
- Результаты оценки соотношения механических свойств пары «колесо- рельс» и его влияние на срок службы колеса;
- Методику комплексного анализа процесса восстановления колес по профилю катания на основе термомеханического подхода;
- Систему управления процессом восстановления колесных пар по температуре формоустойчивости режущего инструмента.
Научная новизна.
- Предложена методика комплексного исследования процесса восстановления колесных пар по профилю катания при ремонте на основе термомеханического подхода;
- Создана виртуальная среда для исследований и анализа процессов восстановления колесных пар;
- Установлены области существования сочетаний параметров процессов восстановления колес с различной твердостью обода;
- Разработана система управления процессом восстановления колесных пар по температуре формоустойчивости режущего инструмента.
Практическая значимость.
- получены численные значения показателей НДС для колес различного диаметра и износа материала колес повышенной твердости;
- разработана программа, позволяющая анализировать показатели процесса восстановления колесных пар;
- предложены рациональные технологические режимы и геометрия режущего инструмента для восстановления колес повышенной твердости;
- разработаны технологические регламенты по практическому применению рациональных режимов восстановления колес различной твердости;
- результаты работы используются в учебном процессе.
Достоверность подтверждена сравнением согласованности теоретических и экспериментальных данных. Расхождение данных расчета силовых характеристик процесса резания и полученных при эксперименте составило 7-12%.
Основные результаты работы докладывались на научно-технических конференциях: «63 научно-техническая конференция студентов, аспирантов и молодых ученых» (г. Санкт-Петербург, 2003 г.), Международная конференция «Транспорт XXI века» (г. Варшава, Польша 2004 г.), Международная конференция «Развитие транспортного машиностроения в России. Желдормашиностроение-2004» (г. Щербинка, 2004), «64 научно-техническая конференция студентов, аспирантов и молодых ученых» (г. Санкт-Петербург, 2004), VI Международная конференция «Проблемы прочности материалов и сооружений на транспорте», (г. Санкт- Петербург, 2004), III Международная научно-техническая Интернет — конференция «Новые материалы и технологии в машиностроении» (г. Брянск, 2004), IV Международная научно-техническая конференция «Подвижной состав XXI века (идеи, требования, проекты)» (г. Санкт-Петербург, Россия 2005 г.), а также на заседаниях Силезской Школы транспортной механики (г. Катовице, Польша 2004).
По материалам исследований опубликовано 12 печатных работ, получено 1 авторское свидетельство на полезную модель.
Работа выполнялась на кафедре «Технология металлов» Петербургского Государственного Университета Путей Сообщения.
Экспериментальные исследования проводились в лабораториях кафедры «Технология металлов», в локомотивных депо (ТЧ19) Малая Вишера, ТЧ18 (Дно) и вагонном депо ВЧД20 (Кемь).
Диссертация состоит из 8-и разделов, включая введение, заключение, список используемых источников и приложения. Объем работы составляет 140 стр., в том числе 60 рисунков, 22 таблицы, 4 приложения.
По результатам работы сделаны основные выводы и даны рекомендации их практического использования.
Современное состояние проблемы. Цель и задачи исследования
Показатели работы железнодорожного транспорта и статистические данные по износу бандажей колесных пар локомотивов
В пятидесятые — восьмидесятые годы прошлого века на отечественных железных дорогах был проведен ряд широкомасштабных мероприятий по изменению конструкции подвижного состава и верхнего строения пути. Все они в той или иной степени повлияли на динамику и характер изнашивания элементов три- бологической пары «колесо — рельс» [1,2].
Переход с паровозной тяги на тепловозную и электрическую означал с одной стороны замену тягового подвижного состава (ТПС) с бестележечным экипажем на ТПС с экипажем тележечного типа, что обеспечило лучшую вписывае- мость ТПС в кривые участки пути и, как следствие, снижение износа внутренних граней головок рельсов и рабочих поверхностей гребней колес. Этому же способствовала замена двухосных вагонов четырехосными и более поздняя замена электровозов с трехосными тележками электровозами с двухосными тележками.
С другой стороны, замена группового привода колесных пар индивидуальным, означало ухудшение противобоксовочных качеств ТПС и, как следствие, повышение интенсивности вертикального изнашивания рельсов и изнашивания поверхностей катания бандажей ТПС.
В целом вышеуказанные изменения в конструкции подвижного состава привели к тому, что рабочие поверхности гребней стали изнашиваться медленнее, чем поверхности катания, что нельзя не признать положительным фактором в отношении изнашивания колеса в целом.
Новые серии подвижного состава, принимавшиеся в эксплуатацию в эти годы, отличались все увеличивающейся нагрузкой от колесной пары на рельсы, а для ТПС — также и максимально реализуемой силой тяги, что в значительной степени ужесточило условия работы колесных пар [3-6].
Большое влияние на условия работы колесных пар оказывают возрастающие скорости движения поездов. Допустимые скорости движения грузовых поездов установлены в пределах 90 — 100 км/ч, пассажирских: 120 — 160 км/ч (до 200 км/ч — высокоскоростные поезда) [7]. Увеличение скорости движения приводит к росту динамических нагрузок на колесные пары и появлению высокочастотных колебаний на участках с большой жесткостью пути.
Возрастание нагрузок от колесной пары (КП), максимально реализуемой силы тяги и скорости приводило к повышению напряженного состояния рельсов и колес [8, 9, 10, 11, 12], что еще более увеличило износ колес и рельсов.
Сужение рельсовой колеи, привело к уменьшению среднего зазора между рабочими гранями гребня колеса и головки рельса. Это с одной стороны повысило устойчивость подвижного состава в колее и позволило увеличить допускаемые скорости движения, с другой, — вызвало возрастание интенсивности износа гребней подвижного состава и вертикальных граней головок рельсов.
Результатом перечисленных выше изменений стало возрастание интенсивности изнашивания бандажей колесных пар.
Значительный вклад в исследование процессов взаимодействия колеса и рельса внесли отечественные ученые Алехин C.B., Бартенева Л.И., Богданов В.М., Вихрова A.M., Голубенко С.И., Горский A.B., Григоренко В.Г., Губенко С.И., Есаулов В.П., Захаров С.М., Ларин Т.В., Марков Д.П., Пашолок И.Л., Удальцов А.Б., Цюренко В.Н., Школьник Л.М., Шур Е.А. и др., а также зарубежные исследователи Джоули Р., Калкер Дж., Картер Ф., Ландгрен Д., Ситаж М., Турне X., Харрис У., Эберсон В. и др.
Совершенствованию технологических процессов ремонта колесных пар подвижного состава посвящены работы Алехина C.B., Богданова А.Ф., Будюкина A.M., Евсеева Д.Г., Иванова И.А., Киселева И.Г., Кушнера B.C., Маш- нева М.М., Омарбекова А.К., Раубы A.A., Тарапанова A.C., Урушева C.B. и др.
Этими учеными предложено немало технических решений, обеспечивающих в той или иной степени повышение производительности восстановления и снижение интенсивности изнашивания колесных пар. Значительная часть этих решений реализована на практике.
На рис. 1.1. изображено положение КП локомотива или вагона и рельса при ширине колеи 1524 и 1520 мм, а также характер износа и количество удаляемого металла с КП при обточке. |
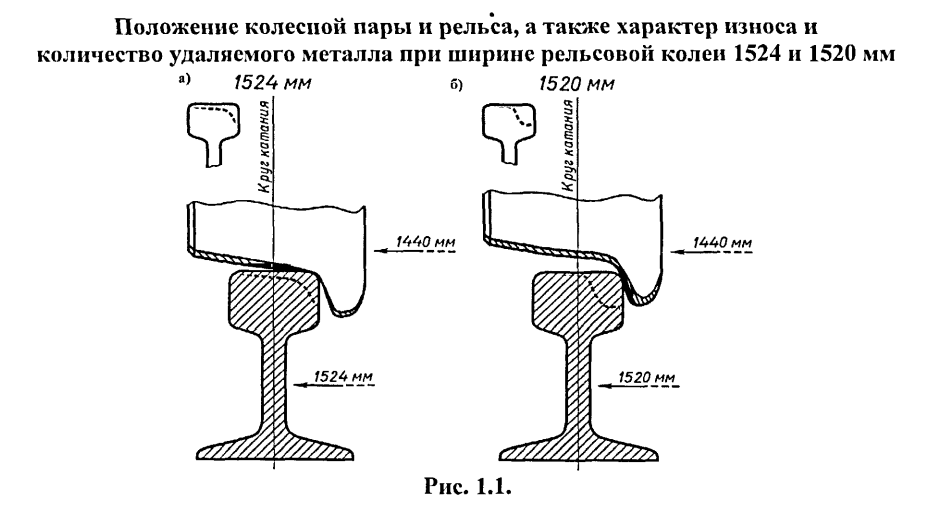
Как показывают авторы [13, 14], при ширине колеи 1524 мм в процессе эксплуатации КП сначала нарастал прокат по кругу катания без существенного уменьшения толщины гребня, и лишь при значениях проката, близких к предельно допустимому, отмечалось возрастание интенсивности изнашивания гребня. Таким образом, обточку колесных пар, назначали в связи с достижением предельного значения проката или в связи с обнаружением непрогнозируемого дефекта (выщербины, раковины и т. п.). После изменения колеи до 1520 мм износ гребня стал опережать нарастание проката. Изменился и характер износа: после сужения колеи он стал происходить как бы по касательной плоскости к внутренней (рабочей) поверхности гребня. Ресурс КП резко сократился. Как видно из рис. 1.1.,б гребень колеса «завис» на головке рельса. Положение «зависшего» гребня на головке рельса и вызываемое этим изменение взаимного давления металла рельса и колеса определило, что гребень с внутренней стороны стал вытягиваться тоже по касательной плоскости к вершине гребня, образуя «пленочный наклеп» и остроту в сторону вершины (рис. 1.2.). Это привело, кроме возрастания интенсивности износа гребня, к существенному учащению обнаружения остроконечного наката и к возникновению нового типа повреждений колес — опасной формы гребня.
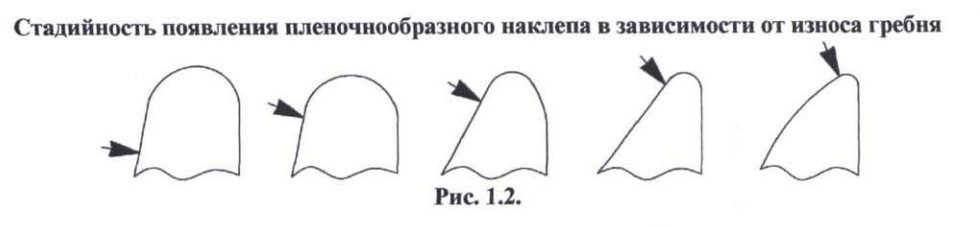
Совокупность «острого гребня» и ступенчатого бокового износа рельса, приводила к сходам с рельсов подвижного состава, особенно на станциях с «кривыми» маршрутами стрелочных улиц. В сложившейся ситуации было принято решение, не отличающееся системным подходом к проблеме, а именно была в одностороннем порядке повышена твердость рельсов, притом, что твердость рабочих поверхностей колес была оставлена прежней. С одной стороны применение рельсов тяжелых типов позволило значительно снизить эксплуатационные расходы железных дорог. Были пересмотрены в сторону увеличения с 350 до 650 млн. ткм брутто межремонтные сроки работы верхнего строения пути, а также нормы расхода ресурсов рельсов на его содержание. Изменение межремонтных сроков при существующей грузонапряженности позволило снизить потребности в капитальном ремонте пути на 4,4 тыс. км в год и сократить на 1,58 тыс. км/год объемы работ по смене рельсов в кривых. В ценах 2002 г. это дает снижение годовых расходов на 11,24 млрд. руб., из которых 5,62 млрд. руб. относится на увеличение погонного веса рельсов и 5,62 млрд. руб. на термоупрочнение рельсов [15].
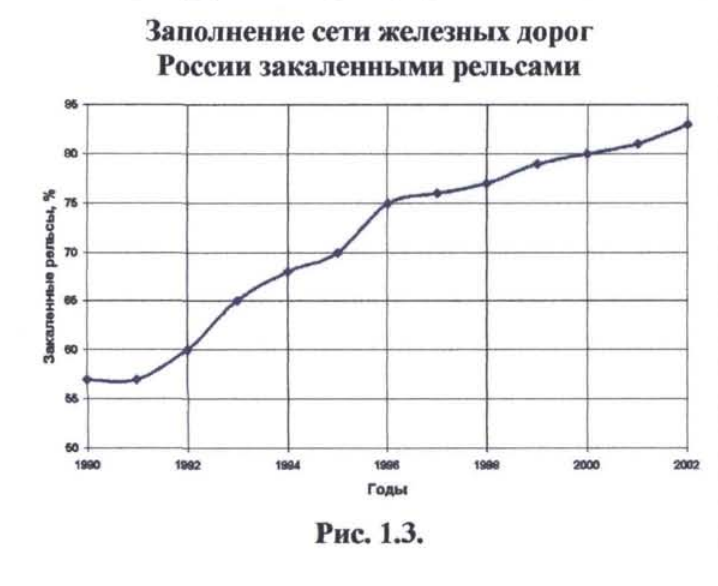
Но по мере укладки новых объем- нозакаленных рельсов еще более повышалась интенсивность изнашивания рабочих граней гребней колес. На рис. 1.3. и 1.4. представлен график заполнения сети железных дорог России закаленными рельсами [16] и диаграммы структуры обточек эксплуатационному парку локомотивов на сети железных дорог РФ за 1999 и 2002 гг. [17].
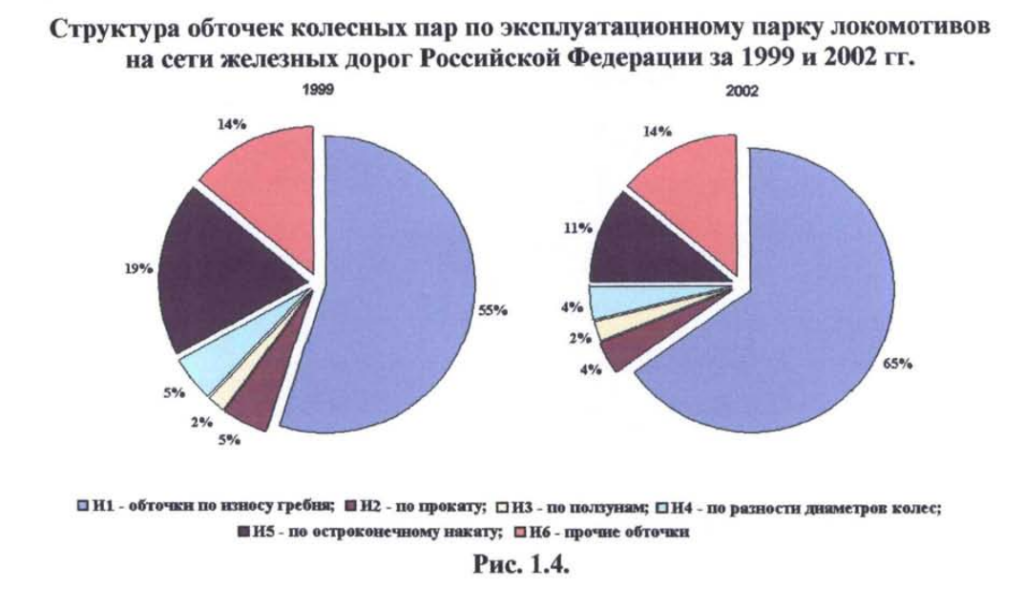
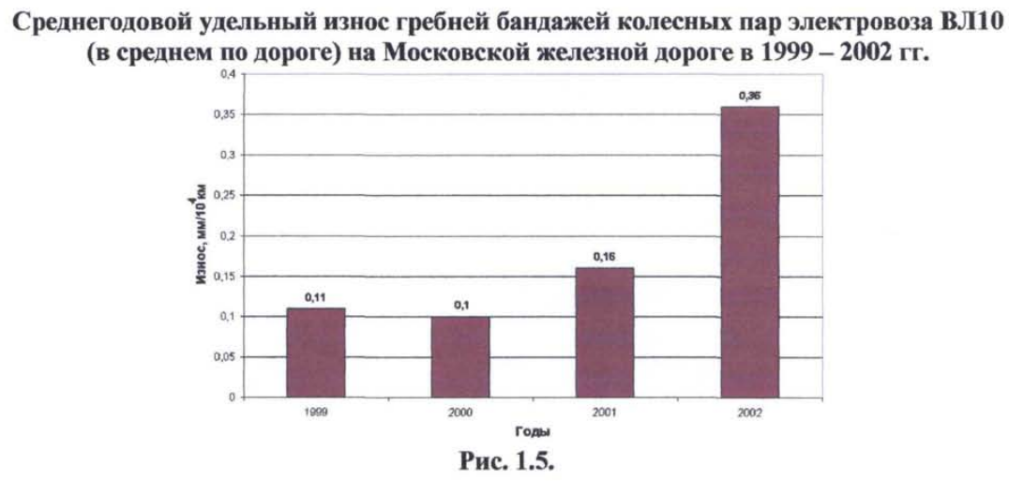
Из сравнительного анализа диаграмм 1.3 и 1.4., очевидно, что одновременно с ростом удельного веса объемно закаленных рельсов (1999 г.- да 78%, 2002 г. — «83%) возрастает и доля обточек по износу гребня. Среднегодовой удельный износ гребней бандажей колесных пар в ряде случаев вырос в « 3 раза. Такая интенсивность износа вызвала рост эксплуатационных расходов в локомотивном и вагонном хозяйствах, связанных с внеплановыми обточками колесных пар, дополнительным приобретением новых бандажей и колес. Убытки только локомотивного хозяйства оцениваются в 6,0 млрд. руб./год в ценах 2002 г [15].
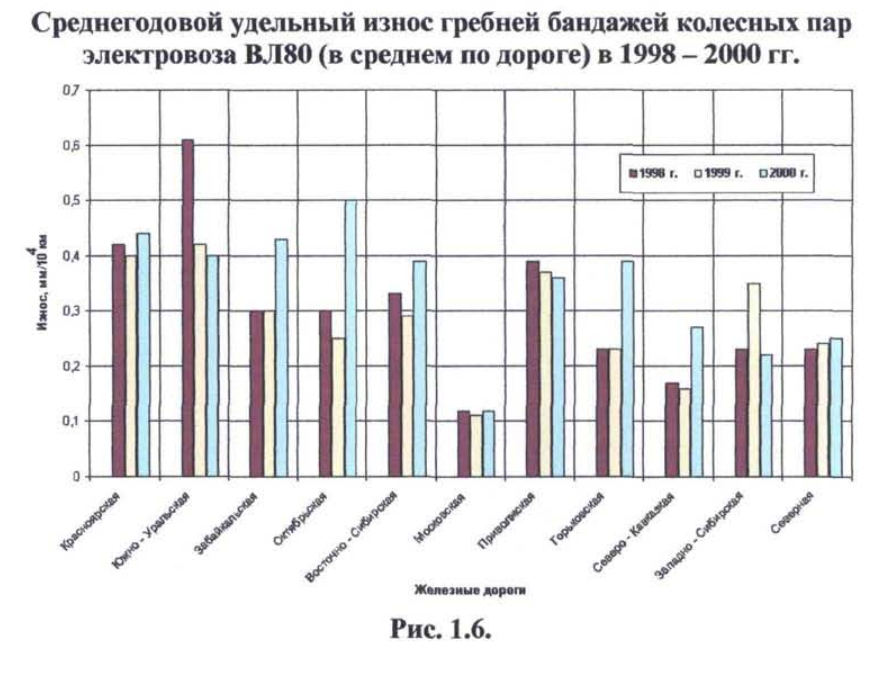
На диаграммах I.5., 1.6. представлено изменение среднегодового удельного износа гребней бандажей колесных пар локомотивов [17].
Ежегодно на железных дорогах России выполняют более 170 тыс. обточек бандажей колесных пар ТПС. В 2002 г. только на Дальневосточной железной дороге (ДВЖД) выполнено 8105 обточек колесных пар ТПС, что составляет всего 3% общего количества обточек по сети. На обточки по износу гребня (И1) приходится более 73%. Каждая колесная пара электровозов обтачивалась в среднем 2,7 раза, тепловозов — 2,1 раза. Среднее значение расходов на обточку (без учета затрат на лубрикацию) на ДВЖД составляет 10-15 тыс. руб.
Порчи и неисправности по видам оборудования распределились следующим образом [18]:
- 40,7% отказов (280 сл.) связанных с дизелем;
- 11,3% (78 сл.) связано с отказами вспомогательного оборудования;
- 31,5% (217 сл.) от общего числа обусловлены отказами электрооборудования;
- 7,6% (52 сл.) —колесные пары.
Увеличение неплановых ремонтов по колесным парам в сравнении с 2001 г. допустили [18]: Октябрьская с 0,62 до 0,65 сл. на измеритель, Юго-Восточная с 0,97 до 1,02 сл., Приволжская с 0,623 до 0,85 сл., Западно-Сибирская с 1,34 до 1,5 7сл.
Нетрудно представить затраты по всей сети Российских железных дорог, если в «копилку» обточек колесных пар внесли: Куйбышевская железная дорога — 12%, Красноярская — 10%, Восточно-Сибирская, Забайкальская, Свердловская — по 9%, Западно-Сибирская — 8% и т.д. [19].
Обтачивания по износу гребня при ремонте связаны с удалением большого объема работоспособного металла колеса, то есть с существенным технологическим изнашиванием. Так при равномерном износе на каждый миллиметр бокового износа гребня требуется снять металл по толщине бандажа на глубину около 1,75 мм [20]. Поэтому возрастание доли таких обточек всегда влечет за собой непропорционально сильное сокращение среднего срока службы колеса.
Очевидно, износ гребней колес ТПС происходит не только в кривых участках пути. Известно, что среднее значение доли кривых на железных дорогах России не превышает 30% от общей протяженности главных путей [19].
С целью снижения интенсивности изнашивания КП в последние годы проводится ряд мер технического и организационно-технологического характера [21, 22] (лубрикация, улучшение конструкции пути и подвижного состава, совершенствование геометрии профиля поверхности катания КП и рельсов, повышение качества их металла и т.д.). К сожалению ни одно из этих мероприятий в полном объеме проблемы не решило.
Кардинальное решение вопроса может быть найдено только на базе использования научных знаний в области взаимодействия пары колесо-рельс. Необходимо проведение научно обоснованной модернизации колесных пар с одновременной разработкой мероприятий, обеспечивающих эффективную эксплуатацию и ремонт модернизированных колесных пар.
Существенные изменения в причинах повреждений колес подвижного состава и рельсов, а также возникающие задачи поиска путей освоения возрастающего объема перевозок, делают необходимым развитие программы «колесо- рельс» с включением в нее всех аспектов взаимодействия в этой сложной трибо- динамической системе. Разработанный проект «Стратегической программы» предусматривает шесть связанных между собой направлений работы [15]:
- трибомеханика контакта колеса и рельса;
- конструкция экипажной части подвижного состава;
- конструкция пути;
- нормы содержания ходовых частей подвижного состава и пути;
- продольная динамика при движении поезда;
- мониторинг в системе колесо-рельс.
Стратегическая программа обеспечения устойчивого взаимодействия системе «колесо-рельс» представлена на рисунке 1.7.
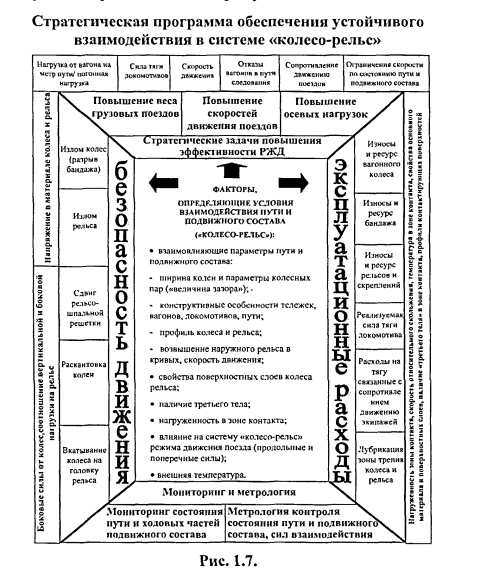
Анализ основных направлений работ по повышению ресурса колесных пар
Анализ «Стратегической программы обеспечения устойчивого взаимодействия в системе «колесо-рельс»» и публикаций [10-27 и др.], посвященных снижению и стабилизации износа бандажей колесных пар, позволяет наметить следующие основные технические и организационно-технологические направления решения проблемы:
- Автоматизация и компьютеризация анализа состояния КП;
- Совершенствование конструкции ходовых частей ТПС;
- Оптимизация профиля бандажа ТПС;
- Совершенствование технологии обмера КП;
- Лубрикация;
- Упрочнение бандажей колесных пар.
Таким образом, решение проблемы может быть только комплексным, то есть включающим в себя наиболее успешные решения во всех направлениях. В перспективе на основании этих решений должны быть разработаны обязательные к исполнению всеми локомотивными депо «Единые правила ремонта и содержания экипажной части локомотивов».
Рассмотрим подробнее существующие в настоящее время направления снижения интенсивности изнашивания колес тягового подвижного состава по каждому пункту предложенной классификации.
Автоматизация и компьютеризация анализа состояния КП
Опыт эксплуатации колесных пар свидетельствует, что правильная организация использования локомотивов при научно-обоснованной системе планово- предупредительных ремонтов высокого качества — гарантия устойчивой и надежной работы всего подвижного состава [24, 25].
Существующие методы организации ремонта локомотивного парка железных дорог нашей страны ориентированы на усредненные показатели использования локомотивов. Действующая в настоящее время структура ремонтных циклов практически одинакова для всех поездных локомотивов. Между тем условия эксплуатации колесных пар настолько отличаются в различных регионах нашей страны, что ресурс колесных пар может отличаться на порядок. В связи с этим всегда остро стоял вопрос рационального планирования производства обточек колесных пар. Эта задача сложна и объемна и не может быть качественно решена без автоматизации и компьютеризации.
Применение современных прикладных математических программ позволяет решать многие оптимизационные задачи, в том числе и оперативно рассчитывать оптимальные межремонтные пробеги.
Проблема состоит в отсутствии унифицированной базы данных по колесным парам. Подобная база может быть создана, например, на основе методики, разработанной проф. Омарбековым. Круг проблем, решаемых введением качественной компьютерной базы, заключается в следующем [27]:
- сокращение обслуживающего персонала, занятого обработкой документации по колесным парам;
- возможность рационального планирования межобточечных периодов;
- возможность рациональной организации переподкаток колесных пар с целью ликвидации разницы по толщине бандажей.
Совершенствование конструкции ходовых частей ТПС
Устойчивость движения ТПС
Устойчивость против виляния зависит от поворотной (изгибной) и сдвиговой жесткости между двумя колесными парами.
Исследования показывают [28], что для обеспечения необходимой сопротивляемости вилянию двух соседних колесных пар необходимо оптимальное сочетание жесткости на изгиб и сдвиг. Можно подобрать комбинацию этих параметров для оптимизации характеристик проектируемой тележки.
Влияние осевой нагрузки и массы поезда
Наблюдениями на Забайкальской дороге установлено, что одним из основных факторов влияния на износ рельсов является уровень загрузки вагонов. В идентичных условиях на четном (грузовом) ходу средняя интенсивность бокового износа составила 0,16, а максимальная — 0,30 мм/млн.т, а по нечетному (порожняковому) ходу — соответственно 0,07 и 0,10 мм/млн.т. Аналогичные зависимости по влиянию загрузки на интенсивность износа получались ранее многими авторами. Следует отметить, что в грузовом направлении постоянно возрастает уровень статических осевых нагрузок вследствие возрастания доли угольно-рудных грузов.
Контактные напряжения
Анализ полученных данных [29, 30, 31, 32] и др. показывает, что контактные напряжения существенно зависят от величины колесной нагрузки, радиуса головки рельса и профиля колеса. С увеличением нагрузки контактные напряжения увеличиваются, причем при контакте головки рельса радиусом 300 мм и бандажом прямолинейного профиля с увеличением нагрузки от 50 до 300 кН контактные напряжения возрастают на 480 МПа, тогда, как при контакте изношенного рельса с изношенным бандажом такое же увеличение нагрузки вызывает рост контактных напряжений лишь на 150 МПа. Для снижения износа колес при взаимодействии с изношенным рельсом необходимо совершенствование профиля поверхности катания обода и повышения прочностных характеристик колесной стали.
Влияние проскальзывания
Значительное влияние на износ пары «колесо-рельс» оказывает жесткая
связь между колесами и явление проскальзывания. Конусность поверхности катания, центрируя колесную пару, одновременно вызывает извилистое движение, что обусловливает износ поверхности катания. Кроме того, одно из колес может проходить большой путь, а другое — отставать.
Интенсивное извилистое движение, увеличивает рост поперечного проскальзывания и тем самым, изменяет форму износа профиля бандажа. На рис 1.8. приведены [22] характерные профили износа.
По данным [33] увеличение нагрузки на ось с 21,5 тс до 23,75 тс изменило характеристики проскальзывания и соответственно другие параметры контактного взаимодействия в паре «колесо-рельс».
Взаимодействие колеса и рельса описывают на основе явления крипа, исследованию которого посвящены многочисленные работы. Феноменологическое описание крипа связывают с именем Картера [34, 35], хотя первые эксперименты были проведены еще Рейнольдсом [36]. Наиболее значительные исследования были выполнены Калкером [37, 38, 39, 40] и др.
Уточнения результатов этих исследований применительно к задачам устойчивости движения рельсовых экипажей и к задачам создания оптимальных тяговых усилий показали, что достаточную достоверность результатов можно получить, пользуясь линейной теорией Калкера с учетом поправочных коэффициентов 1о1у Я. [41], А.Л. Голубенко [42] и др.
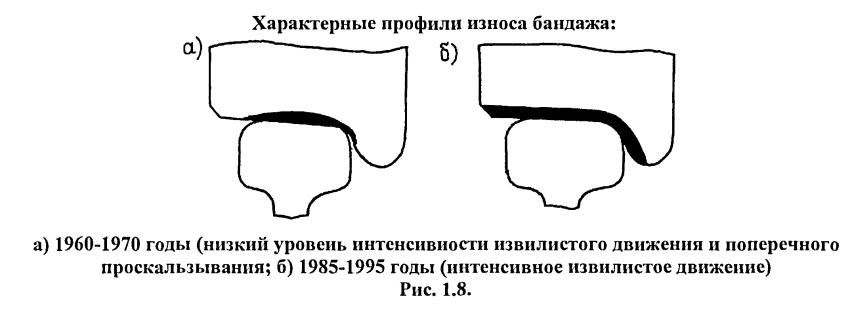
Основные усилия исследователей и разработчиков подвижного состава направлены на изменение конструкции тележек и колесных пар. Одной из причин усложнения конструкции тележки является стремление улучшить вписывание экипажа в кривые на основе применения специальных конструктивных решений для управления колесными парами [43].
Внимание к подвижному составу с независимо (свободно) вращающимися колесами (НВК) в теоретическом и экспериментальном аспектах возникло сравнительно недавно: в 1942 г. появились первые теоретические публикации немецких авторов. Это было обусловлено высоким уровнем развития сети скоростных железных дорог в Германии и наиболее острым проявлением проблемы боковых колебаний подвижного состава.
Вагонная тележка с НВК вследствие исключения продольного проскальзывания колес обеспечивает уменьшение износа поверхностей катания колеса и рельса. Одновременно исчезает тенденция к вилянию. Таким образом, уменьшается износ в системе колесо-рельс, снижаются сопротивление движению, энергозатраты и шум. Конструкция с НВК реализована в поезде Talgo [44].
Однако необходимо отметить, что все предлагаемые решения будут способствовать снижению износа гребня, но не окажут определяющего влияния на повышение его износостойкости.
Оптимизация профиля бандажа ТПС
В Государственной металлургической академии Украины [44] уже на протяжении нескольких десятилетий проводятся исследования, направленные на совершенствование контактного взаимодействия в паре колесо — рельс. Результатом этих многолетних исследований стало утверждение МПС в 1995 году «Инструкции по формированию, ремонту и содержанию колесных пар тягового подвижного состава железных дорог колеи 1520 мм». Эта инструкция предусматривает использование наряду с существовавшим и единственным на то время профилем рабочей поверхности колеса по ГОСТ 11018-87 ремонтного профиля ДМеТИ ЛБ. На рис. (1.9., а) и таблице 1.1. представлен профиль ГОСТ и геометрические параметры характерных точек.
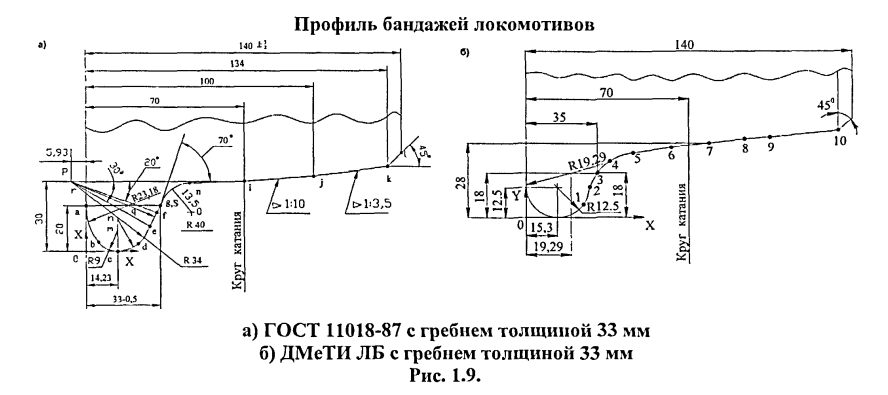
Модификация профиля рабочей поверхности колеса преследовало две цели:
- снижение интенсивности изнашивания рабочей поверхности колеса;
- уменьшение количества металла снимаемого при восстановлении исходной формы рабочей поверхности колеса.
Снижение интенсивности достигается изменением параметров взаимодействия колеса и рельса, а именно подбором геометрических характеристик рабочей поверхности колеса, обеспечивающих минимизацию контактных напряжений на рабочей поверхности гребня (особенно в кривых участках пути)
Уменьшение количества удаляемого металла при обточке требует такого изменения формы поверхности, чтобы на 1 мм восстановления толщины гребня с поверхности катания удалялся слой металла меньшей толщины, что может быть достигнуто только изменением угла наклона рабочей поверхности гребня к внутренней поверхности бандажа.
При разработке профиля рабочей поверхности колеса ДМеТИ были учтены все эти требования: в отличие от профиля ГОСТ, он представляет собой комплексно криволинейную кривую, задаваемую координатами десяти контрольных точек. Поверхность катания имеет форму дуги (у профиля ГОСТ — прямая), угол наклона рабочей поверхности гребня к внутренней грани бандажа увеличен до 34° (у профиля ГОСТ — 27°), изменена конфигурация галтели, сопрягающей гребень и поверхность катания (у профиля ДМеТИ она более пологая).

Профиль ДМеТИ разработан как ремонтный. Этот профиль придается колесам при обточке — изготавливаются колеса до сих пор с профилем ГОСТ, то есть в настоящее время одновременно эксплуатируются колеса обоих профилей (ГОСТ — у колес, не подвергавшихся обточке и ДМеТИ — после обточки): тотальное внедрение профиля ДМеТИ потребовало бы серьезной модернизации всего оборудования для производства колес. На рис. (1.9.,б) и таблице 1.2. представлен профиль ДМеТИ и геометрические параметры характерных точек.
В настоящее время профиль ДМеТИ используется во всех локомотивных депо, производящих обточку. В целом для колес с этим профилем характерна более низкая интенсивность изнашивания. Но внедрение этого профиля кардинальным образом не решает проблему.
Лубрикация
Лубрикация, то есть подача смазки в зону контакта гребня колеса с рельсом нашла широкое применение как в России, так и за рубежом. Этот метод снижения интенсивности изнашивания относительно прост и дешев [28]. Устройства для подачи смазки — лубрикаторы могут устанавливаться как на локомотивах, так и на путевых устройствах; в соответствии с этим их классифицируют на путевые и локомотивные.
По мере увеличения осевых нагрузок и массы поездов значение лубрика- ции возрастает, поскольку повышение грузонапряженности железнодорожных линий влечет за собой существенный рост интенсивности изнашивания рельсов и колес.
Износ колеса и рельса зависит от свойств третьего тела в зоне контакта, подача смазки существенно изменяет значения коэффициента трения, контактных напряжений, относительных проскальзываний контактирующих тел, в свою очередь зависящих от угла набегания, профилей колеса и рельса, характеристик вписывания тележек и эксплуатационных условий. Все эти элементы образуют сложную трибосистему. Очень трудно, если вообще возможно, вернуть систему в условия нормального функционирования, т. е. в условия работы при нормальном режиме изнашивания, без применения лубрикации [17]. Выгоды от введения луб- рикации включают [46]:
- снижение интенсивности изнашивания боковой поверхности головки рельсов и гребней колес, что приводит к уменьшению интенсивности замены колес и рельсов;
- сокращение расхода топлива или электроэнергии, обусловленное улучшением взаимодействия колеса и рельса;
- уменьшение выделения шума, связанного с взаимодействием колеса и рельса.
Оптимальной считается такая система лубрикации, которая обеспечивает уменьшение расхода энергии, интенсивности изнашивания и сменяемости колес и рельсов без создания отрицательных эффектов воздействия на тяговые характеристики поезда и движение экипажей в кривых [47].
В России большее распространение получили путевые лубрикаторы — опыты по применению локомотивных гребнесмазывателей нельзя признать вполне удачными из-за несовершенства их конструкции, а именно из-за попадания смазки на поверхность катания, что вызывает резкое снижение силы сцепления.
В целом следует признать, что введение лубрикации хотя и снижает интенсивность изнашивания гребней, не решает проблему кардинально: даже при применении лубрикаторов интенсивность изнашивания колесных пар существенно выше, чем она была в 50-е годы прошлого века.
Упрочнение бандажей колесных пар
В исследованиях ВНИИЖТа [50, 51] 1960 — 1990х годов отмечалось, что для равной износостойкости отношение твердости колесного образца к твердости рельсового образца должно быть порядка «1,2 при проскальзывании до 1%, а при проскальзывании до 10% — «1,0 — 1,1.
В настоящее время необходимость повышения твердости рабочих поверхностей колес практически ни у кого не вызывает сомнений. Этой проблеме посвящено немало публикаций [16, 46, 52].Основные доводы в пользу повышения твердости можно классифицировать следующим образом:
- данные сравнительного анализа состояния колесного парка в настоящее время и до укладки объемнозакаленных рельсов;
- результаты обоснования необходимости повышения твердости рабочей поверхности колес с использованием математических моделей взаимодействия колеса с рельсом и анализа данных натурных экспериментов.
Ресурс бандажа и эффективность его реализации
В настоящее время твердость металла обода эксплуатирующихся колес у поверхности достигает 320…330 НВ, снижаясь по направлению к оси колеса по сечению обода до 255-280 НВ на глубине 50 мм. То есть срезаемый слой металла обода при обточках не только уменьшает диаметр колеса, но и определяет снижение его износостойкости.
Представим назначенный ресурс колеса в виде площади ОНВС (рис. 1.10.), ограниченной осями координат и линией ВС — функцией износостойкости металла обода [52]. Металл на поверхности обода будет иметь наибольшую износостойкость — ОВ. На глубине 50 мм — меньшую — НС. Обозначим назначенный ресурс через Т = ОНВС.
Рассмотрим использование назначенного ресурса колеса в процессе эксплуатации на примере браковки его по ползуну и подрезу гребня. На рис. 1.11. слой металла обода, обозначенный через 1, износился в процессе эксплуатации, но не до пре дельной величины. Появление подреза гребня вызывает необходимость смены колесной пары и последующей ее обточки. При обточке колесной пары с подрезом гребня с поверхности срезается не минимально необходимый, а больший слой металла обода то есть с обода срезается полезный (работоспособный) слой металла. На рис. 1.11. он обозначен цифрой 2 и заштрихован.
По данным [54] за одну обточку колесных пар с подрезом гребня, ползунами и т.п. в стружку снимается до 3-4 мм и более полезного (работоспособного) слоя металла.
Назначенный ресурс Т представим в виде суммы двух слагаемых:
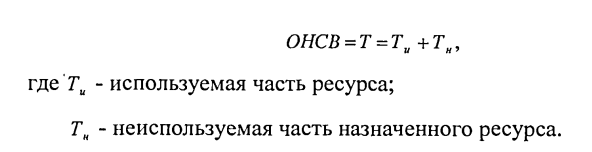
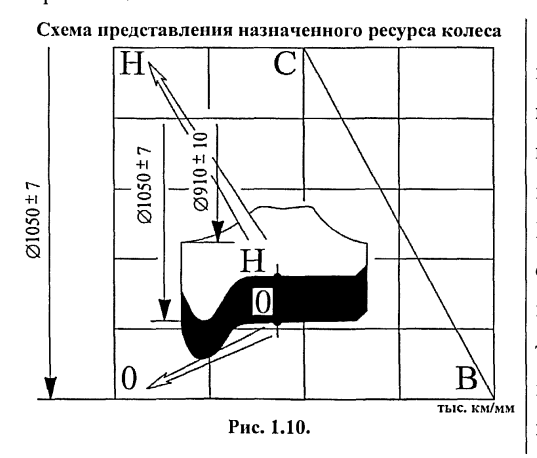
Заштрихованные площади, обозначенные на рис. 1.11. через 2, 4, 6, … , характеризуют неиспользуемую часть назначенного ресурса, определяемую механической обработкой на глубину большую, чем это необходимо для восстановления геометрических параметров профиля обода колеса. Т.е. в процессе ремонта удаляется работоспособный слой металла бандажа. В соответствии с рис. 1.11. ресурс, неиспользуемый на стадии эксплуатации из-за применяемой неэкономичной технологии восстановления профиля, определится суммой площадей:

Используемый в настоящее время ресурс восстанавливаемых колес с подрезом гребня определяется следующей суммой площадей (рис. 1.11):
Ти =1 + 3 + 5 + … и составляет примерно 60% назначенного ресурса (Ти = 0,6Г).
Т = Ти+Ти =0,6Г + 0,4Г Аналогичные рассуждения по рис. 1.11 действительны и для колеса с ползуном. При обточке колесной пары с ползуном с поверхности катания срезается значительный слой работоспособного металла обода 2 + 4 + …, резко сокращая используемую часть назначенного ресурса.
Анализируя рис. 1.11., можно отметить, что существует два основных пути повышения ресурса колес:
- за счет экономии металла обода, нерационально срезаемого при ремонте, т.е. снижения величины Тн (неиспользуемой части назначенного ресурса) при восстановлении геометрии профиля колеса с использованием ресурсосберегающих технологий;
- за счет увеличения износостойкости металла обода, повышения величины Ти (используемой части назначенного ресурса) [55, 56]. Повышение износостойкости может быть достигнуто повышением твердости, совершенствованием конструкции ходовых частей ТПС и др.
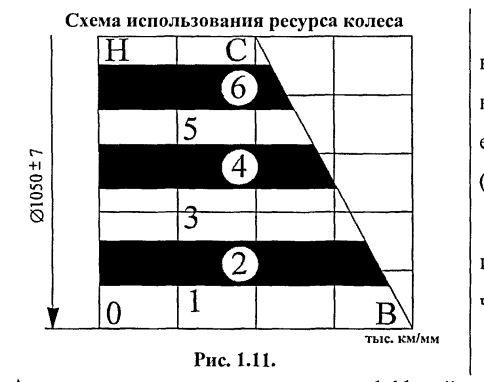
Особенности процесса механической обработки колесных пар
Основным технологическим оборудованием при восстановлении и создании профиля поверхности катания колесных пар являются колесотокарные станки. В нашей стране и за рубежом разработано и используется большое количество станков подобного типа [58 — 64].
При текущем ремонте локомотивов и электросекций так же используется способ восстановления профиля поверхностей катания колесных пар без выкатки их из-под подвижного состава. Такая технология обработки колесных пар значительно эффективнее, чем традиционная [62].
При обработке колесных пар без выкатки не требуется выполнения трудоемких вспомогательных работ, таких как отсоединение концов ТЭД, подъем кузова и др.
В мировой практике на выпускаемых станках используется такие методы обработки резанием, как фрезерование, точение и шлифование.
Методы восстановления колесных пар
Анализ методов восстановления профиля обода колесных пар [63 — 66] показал, что в ближайшем будущем приоритет сохранится за лезвийной обработкой — точение на колесотокарных станках по копиру или программе, фрезерование на станках типа КЖ 20 сборными фрезами и др.
Перспективным методом обработки [70] поверхности обода с термомеханическими повреждениями является врезное профильное высокоскоростное шлифование (ВПВШ), обеспечивающее снижение технологического износа за счет минимизации припуска. Этот метод целесообразно применять для колесных цехов при обработке не менее 13 тыс. колесных пар в год. Оснащение станков ЧПУ, как показал опыт Красноярского вагонного депо [72], обеспечивает высокое качество и производительность только при чистовой обточке колесных пар. Необходима предварительная черновая обработка на другом станке (особенно это касается колес с термомеханическими повреждениями — ТМП), кроме того, такое оборудование требует высокой культуры обслуживания.
Жесткость технологической системы
Жесткость системы СПИД при обработке колес — это один из наименее определенных факторов. В результате наличия зазоров в механизме подачи суппорта и в копировальном устройстве станка при врезании резца происходит его отжатое (отжим). Отжим тем больше, чем больше радиус округления, размеры и угол наклона фаски режущей части инструмента. Следовательно, уменьшение этих параметров уменьшит величину отжима и облегчит врезание.
Статические и динамические характеристики станков даже одной модели изменяются в широких пределах. С увеличением срока и интенсивности эксплуатации наряду со снижением жесткости, увеличивается и диапазон ее изменения. Так для новых станков модели 1К62 жесткость лежит в пределах (5,6- 2,67) -107, а после пяти лет эксплуатации — (5,6-1,27)-107 Н/м [70]. Жесткость эксплуатирующихся колесотокарных станков по данным [66] составляет (0,5-1,б)-107 Н/м. Это служит одной из причин возникающих вибраций, снижающих стойкость инструмента.
Инструментальные материалы
Анализ литературы [72 — 80] показал, что исследованию свойств твердых сплавов посвящено много работ, но при высоких температурах эти свойства, особенно пластические, исследованы не достаточно, чтобы обосновано определить оптимальный температурный интервал их эксплуатации.
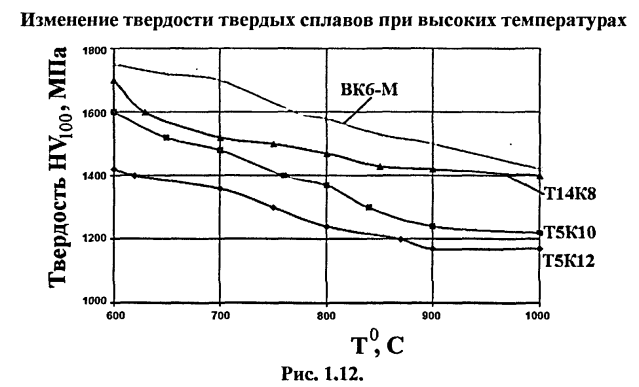
Изменение твердости твердых сплавов при высоких температурах представлено на рисунке 1.12 [67].
Таким образом, существенным резервом повышения эффективности механической обработки при ремонте колесных пар является рациональный выбор твердого сплава и разработка методов повышения его физико-механических свойств.
Конструкция режущего инструмента
Конструкция инструмента должна обеспечить достаточно высокие эксплуатационные свойства и экономичность процесса обточки колесных пар, т. е. соответствовать параметрам, обоснованным наукой и практикой. Наиболее слабым звеном анализируемой системы является режущая часть сборного инструмента — СМП, так как его корпус или державка, как правило, изготавливается с достаточным запасом прочности и жесткости [69].
Изнашиванию и разрушению в основном подвержены лезвия и режущие кромки этих пластин. Геометрическая форма режущей части должна обеспечивать высокую стойкость, хорошее стружколомание и другие специфические требования, характерные для конкретных условий восстановления профиля колеса обточкой. Это требует особого подхода к разработке геометрической формы режущей части, связанного с исследованием изменений ее исходной геометрии в процессе обточки колеса и глубокого анализа геометрии с позиций современных достижений теории резания.
На рисунках 1.13. — 1.14. представлены конструкции и геометрия резцов применяющихся для восстановления колесных пар. Научные основы проектирования и технологии изготовления режущих инструментов разработаны отечественными учеными: Гречишниковым В.А., Кирсановым Г.Н., Лаптевым С.И., Рауба A.A., Султановым Т.А., Хаетом Г.Л., Цвисом Ю.В., и др. Решению различных задач повышению эффективности работы режущей части инструментов посвящены фундаментальные исследования отечественных и зарубежных ученых Бетанели А.И., Верещаки A.C., Евсеева Д.Г., B.C., Лоладзе Т.Н., Можаева С.С., Остафь- Ф., Старкова В.К., Талантова Н.В. и др.
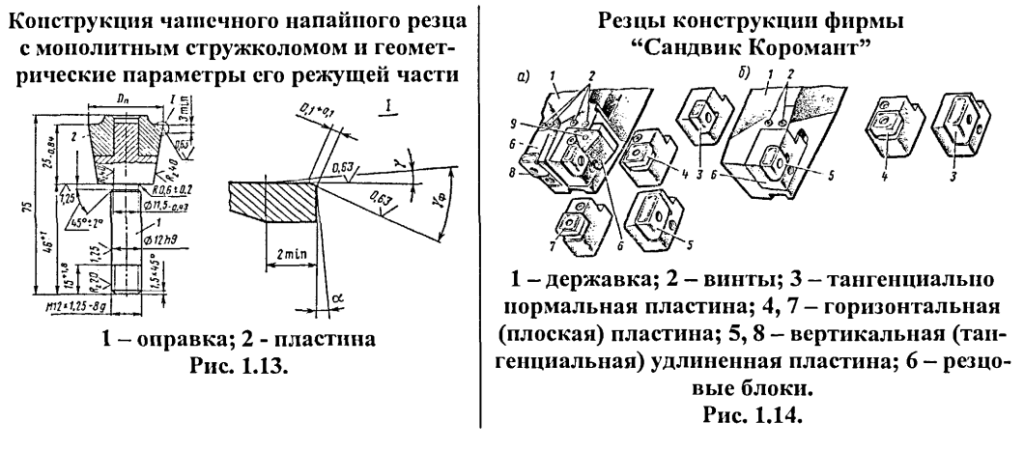
Правильный и обоснованный выбор геометрии режущей части инструмента позволяет существенно увеличить его ресурс. Режущую часть многогранных пластин характеризуют следующие параметры: передний угол, задний угол, форма передней поверхности, величина радиуса при вершине, состояние режущей кромки. Определение оптимальных, для конкретных условий обработки колес, геометрических параметров режущей части многогранных пластин возможно на основе исследований производственного опыта, данных, приведенных в технической литературе и дополнительных исследований закономерностей деформаций и напряженного состояния в зоне стружкообразования. Последнее необходимо потому, что в литературе отсутствуют ответы на очень многие вопросы, возникающие при выборе геометрии для конкретных условий обработки колесных пар. Исследования по оптимизации геометрии многогранных твердосплавных пластин в литературе носят, в основном, описательный характер.
Учитывая вышесказанное, разработать универсальные геометрию и технологию восстановления, удовлетворяющие разнообразным условиям обработки колес, не представляется возможным. Поэтому необходимо разработать подходы к оптимизации конструктивных параметров лезвия и технологию восстановления с учетом основных факторов, влияющих на процесс удаления припуска при вое-
становлении профиля поверхности катания. К этим факторам следует отнести — режимы резания физико-механические свойства материала колес и свойства поверхностного слоя (НВ,ств,3); количество, размеры и вид дефектов восстанавливаемой поверхности; жесткость системы СПИД; количество врезаний за период стойкости и др. [68].
Режим резания
В практике машиностроения режимы резания для конкретных условий обработки деталей назначают либо по рекомендациям нормативных справочников, созданных на основе производственного опыта (табличный метод), либо определяют расчетным путем по алгоритмам созданным на основе эмпирических зависимостей [77].
Назначение режимов резания тесно связано с процедурой оптимизации основных параметров процесса: скорости главного движения, величины подач и глубины резания (У, 5, (), т.е. определяются такие параметры из множества возможных значений, которые при установленных ограничениях обеспечивают заданные качество и производительность при минимальных затратах.
Для процесса обточки колес характерно колебание в широком диапазоне припуска на обработку, твердости обрабатываемой поверхности, степени изношенности станка и инструмента и др. В зависимости от вида дефекта (например, подрез гребня) повреждения глубина резания может достигать 14-16 мм, а твердость обрабатываемой поверхности (например, наличие ползуна) — до 900 НУ и более. Кроме того, колесо имеет сложный фасонный профиль, что приводит в процессе обработки к изменению угла контакта чашечного режущего инструмента с деталью от 0 до 105°, т.е. ширина среза может в определенный момент достигать 27,5 мм [81].
Математический аппарат оптимизации режимов резания достаточно хорошо отработан, на его основе созданы программные комплексы, которые при высоком качестве исходных данный позволяют достаточно точно определить оптимальные значения параметров [82 — 97].
В табл. 1.3. приведены результаты оптимизации режимов токарной обработки колес по профилю обода [53], которые разработаны применительно к физико-механическим свойствам колесной стали по ГОСТ 10791-89*.
Для требуемого на первом этапе повышения ресурса бандажей до 0,6 млн. км, качества их восстановления необходимо повышение твердости металла обода, исследование процесса обработки и восстановления бандажей повышенной твердости и разработка рекомендаций ремонтным предприятиям РЖД по особенностям технологии восстановления с использованием существующего инструмента и оборудования.
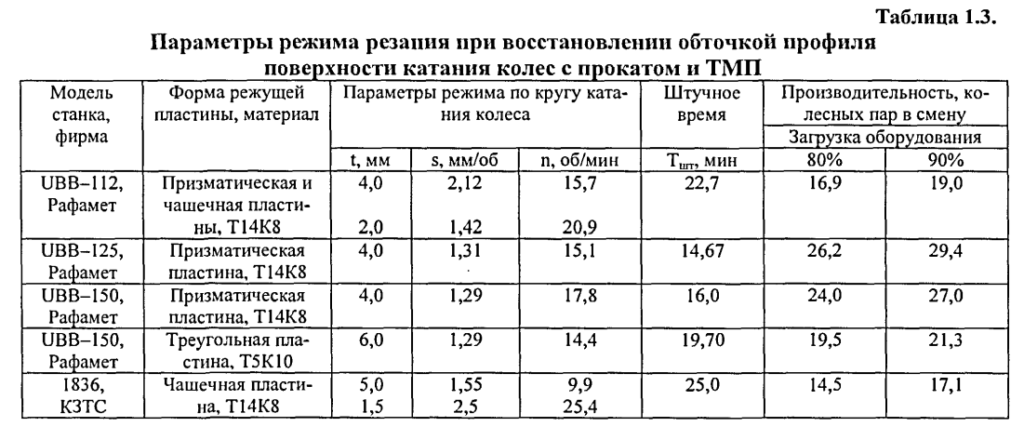
Выводы по главе 1. Цель и задачи исследования
- Статистические данные по износу бандажей колесных пар локомотивов показывают необходимость увеличения их ресурса, т.к. количество внеплановых ремонтов, связанных с обточкой бандажей, увеличилось и значительно снизило их ресурс.
- Анализ «Стратегической программы обеспечения устойчивого взаимодействия в системе «колесо-рельс»» показал, что для снижения интенсивности изнашивания бандажей колесных пар предполагается решение следующих технических и технологических мероприятий: автоматизация и компьютеризация анализа состояния КП; совершенствование конструкции ходовых частей ТПС; оптимизация профиля бандажа ТПС; совершенствование технологии обмера КП; лубрикация; упрочнение бандажей колесных пар. Вопросы, связанные с обрабатываемостью бандажей повышенной твердости в «Стратегическую программу обеспечения устойчивого взаимодействия в системе «колесо-рельс»» не включены.
- Оценка ресурса бандажа и эффективности его реализации показали, что помимо организационных и технологических мероприятий, повышение ресурса бандажа можно обеспечить за счет совершенствования технологии восстановления и повышение износостойкости металла поверхностного слоя бандажа, за счет улучшения физико-механических свойств.
- Выполненный обзор литературных данных по особенностям процесса восстановления колесных пар ТПС показал нестабильность характеристик используемого оборудования, обрабатываемых колес (меняющийся припуск, твердость, дефекты и др.), инструмента, изменение их в процессе ремонта, а так же отсутствие рекомендаций по восстановлению колес повышенной твердости.
Изложенное выше позволяет сформулировать цель настоящей работы.
Целью данной работы является разработка рекомендаций по повышению эффективности процесса восстановления бандажных колесных пар повышенной твердости.
Достижение поставленной цели предполагает решение следующих задач:
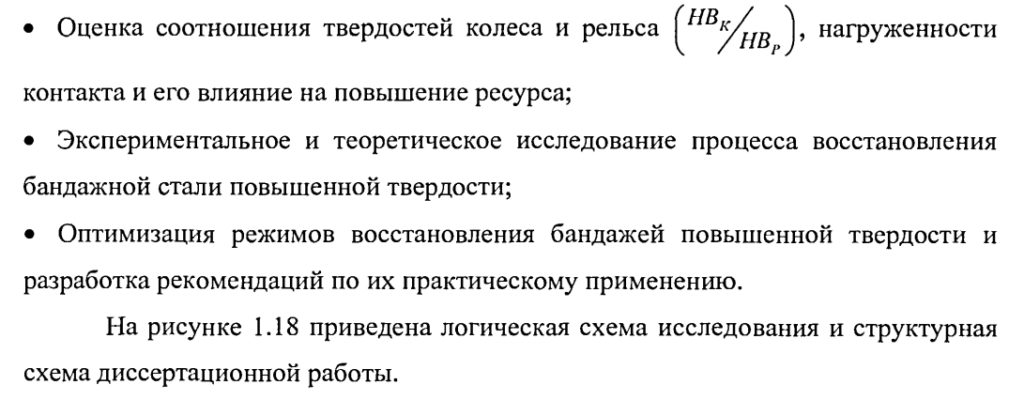
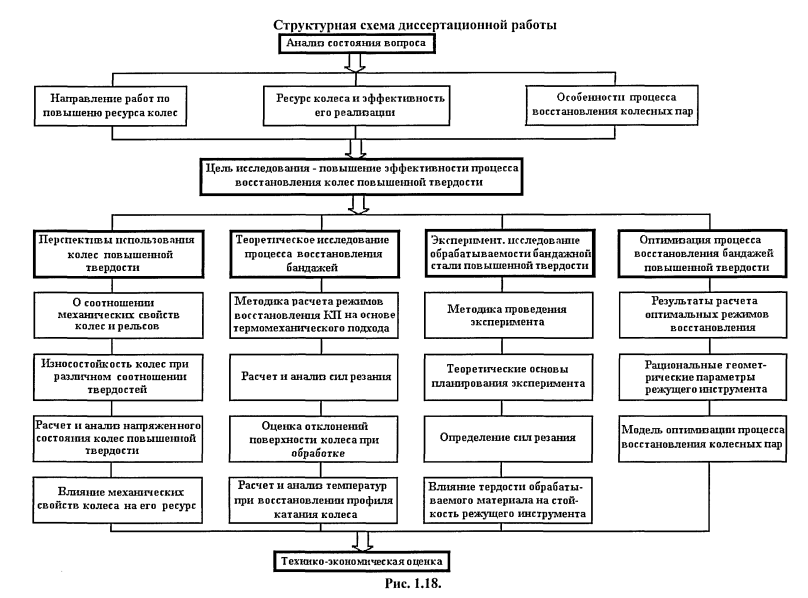
Список литературы
- Черкашин Ю. М. Использование результатов фундаментальных и приклад¬ных исследований проблем взаимодействия подвижного состава и пути при решении задачи предотвращения сходов колеса и рельса //Современные про¬блемы взаимодействия подвижного состава и пути: Материалы научно- практической конференции/ ВНИИЖТ. — М., 2003. с. 21 — 29.
- Корольков Е. П., Бондаренко А. И. О путях уменьшения износа гребней колес железнодорожного подвижного состава //Современные проблемы взаимодейст¬вия подвижного состава и пути: Материалы научно-практической конферен¬ции/ ВНИИЖТ. — М., 2003. с. 110 — 112.
- Продление срока службы рельсов и колес. По материалам зарубежной печа¬ти// Вестник транспорта. 2002, №6, с.39 — 40.
- Исследование процесса восстановления профиля катания бандажных локомо-тивных и моторвагонных колесных пар с использованием отжига при нагреве ТВЧ: Отчет ЛИИЖТ. Руководитель темы Продан Н. С. №449. Инв.№02825036774. Л., 1981. 124 с.
- Школьник Л. М., Парышев Ю. М., Вихрова А. М. Эволюция технических ус¬ловий на вагонные колеса// Вестник ВНИИЖТ, 1986, №6, с. 34 — 39.
- Левинзон М. А., Лазаренко Ю. М., Крылов В. Л., Семерзанов В. В., Козлов М. В., Парсчевский А. Г. и Толмачев С. В. Возможность и условия обращения гру¬зовых вагонов с повышенными осевыми и погонными нагрузками (по данным диагностического поезда ВНИИЖТ)// Вестник ВНИИЖТ, 2002, №4, с. 37 — 39.
- Пехтерев Ф. С. Повышение скоростей движения. О ходе реализации про¬граммы развития скоростного и высокоскоростного движения на железных до¬рогах России// Железнодорожный транспорт, 2002, № 7, с. 10-15.
- Оптимизация взаимодействия колеса и рельса// Железные дороги мира, 2003, №1, с. 66-70.
- Яковлев В. Ф., Дудкин Е. П., Артамонова Н. Е., Параскевопуло Ю. Г. Рацио- -нальная-периодичность-обточки-колес-вагонов-промышленного-транспорта:
Интенсификация работы предприятий промышленного железнодорожного
транспорта. — Межвуз. сб. научн. трудов под ред. В. Ф. Яковлева. Л.: ЛИИЖТ, 1988, с. 55-61. - Вериго М. Ф., Коган А. Я. Взаимодействие пути и подвижного состава. М.: Транспорт, 1986, 559 с.
- Яковлев В. Ф. Исследование сил взаимодействия, деформаций и напряжений в зоне контакта железнодорожных колес и рельсов. Дисс. на соиск. уч. степ, докт. техн. наук. Л.: ЛИИЖТ, 1964, 377 с.
- Пахомов М. П. Взаимодействие подвижного состава и пути и динамика ваго¬нов. Метод, указания по курсу лекций. Омск, 1966, 139 с.
- Пашолок И. Л., Харитонов В. Б. О возможном повышении износостойкости железнодорожных колес// Вестник ВНИИЖТ. 1997, №1, с. 32 — 36.
- Филиппов О. К. Заметки инженера — практика// Локомотив. 1999, №2, с. 23 — 26.
- Богданов В. М. Стратегическая программа обеспечения устойчивого взаимо-действия в системе колесо-рельс //Современные проблемы взаимодействия подвижного состава и пути: Материалы научно-практической конференции/ ВНИИЖТ. — М., 2003. с. 14 — 20.
- Шур Е. А. К вопросу об оптимальном соотношении твердости рельсов и ко¬лес //Современные проблемы взаимодействия подвижного состава и пути: Ма¬териалы научно-практической конференции/ ВНИИЖТ. — М., 2003. с. 87-93.
- Бартенева Л. И. Технология лубрикации боковой поверхности рельсов пере-движными рельсосмазывателями — комплексное решение проблемы износа в контакте гребень колеса — рельс //Современные проблемы взаимодействия под-вижного состава и пути: Материалы научно-практической конференции/ ВНИ¬ИЖТ. — М., 2003. с. 114 — 122.
- Анализ состояния безопасности движения в локомотивном хозяйстве в 2002 году / Департамент локомотивного хозяйства МПС. — М., 2003, 76 с.
- Новачук Я. А., Тепляков А. Н., Григоренко В. Г. Стратегия повышения ре¬сурса бандажей колесных пар тягового подвижного состава //Современные проблемы взаимодействия подвижного состава и пути: Материалы научно- практической конференции/ ВНИИЖТ. — М., 2003. с. 164 — 167.
- Зальцман С. Г. Повышение износостойкости гребней железнодорожных ко¬лес в процессе ремонта. Дисс. на соиск. уч. степ. канд. техн. наук. СПб.: ПГУПС, 1999, 198 с.
- Шур Е.А., Бычкова Н.Я., Марков Д.П., Кузьмин H.H. Износостойкость рель-совых и колесных сталей // Трение и износ. Том 16. — 1995. №1. с. 80 — 91.
- Неглинский В.В. Обобщение результатов эксплуатационных наблюдений за изнашиванием реборд колесных пар локомотивов // Трение и износ. Том 16. — 1995. №1. с. 119-125.
- Анализ комплекса свойств, определяющих долговечность цельнокатаных ко¬лес вагонов в эксплуатации/ Ю. М. Парышев, А. М. Вихрова, JI. М. Школьник, Д. П. Марков (Сб. тр. ВНИИВ (Вагоностроение: вопросы надежности и прочно¬сти)). М.: Минтяжмаш, 1986, с. 5 — 9.
- Собенин Л.А., Бахолдин В.И., Зинченко О.В., Воробьев A.A. Устройство и ремонт тепловозов. — М.: Академия, 2004. — 416 с.
- Рахматулин М.Д. Ремонт тепловозов. М.: изд. «Транспорт». 1977. — 447 с.
- Снова об износе бандажей и рельсов/ Б.В. Захаров, E.H. Рогова, A.A. Сашко, В.А. Чашин// Локомотив. 1996, №9, с. 19 — 20.
- Омарбеков А. К. Управление техническим состоянием колесных пар тягового подвижного состава в эксплуатации. — М.: 2001. 183 с.
- Обобщение передового опыта тяжеловесного движения: вопросы взаимодей-ствия колеса и рельса / Перевод с англ. / У. Харрис, С. Захаров, Д. Ландгрен, X. Турне, В. Эберсон / М.: Интекст, 2002, 416 с.
- Беляев Н.М. К вопросу о местных напряжениях в связи с сопротивлением рельс смятию. Труды ЛИИЖТа. Л.: Путь. 1929. Вып. 99. с. 283 — 296.
- Параскевопуло Ю. Г. Пути повышения технического ресурса ходовых частей передвижных миксеров. Дисс. на соиск. уч. степ. канд. тех. наук. Л.: ЛИИЖТ. 1989.
- Яковлев В.Ф. Исследование динамических контактных деформаций в колесах и рельсах в эксплуатационных условиях. Труды ЛИИЖТа. Л.: 1963. Вып. 210. с. 76-Т23;
- Яковлев В.Ф. О применимости теории Герца — Беляева к расчету контактных напряжений в боковых выкружках головки рельса и гребня колеса. Исследова¬ние контактной прочности рельсов и колес подвижного состава. Труды ЛИИЖТа. Л.: 1963. Вып. 210. с. 21-75.
- Лазарян В. А. Динамика вагонов. М.: изд. «Транспорт». 1964. 256 с.
- Carter F. W. On the action of locomotive driving wheel//Proc. Roy. Soc. Ser. A., 1926. V112.-P.151- 157.
- Carter F. W. On the Stability of Running of locomotives//Proc. Roy. Soc. A., 1928. 121.
- Reynolds O. On Rolling friction / Philos. Trans, of the Royal soc/ London. 1876. v. 166. P. 155- 175.
- Kalker J.J. On the rolling contact of two elastic bodies in the presence of dry fric¬tion: Dost. Thes. / Delft University of Technology. Dtlft. 1967.
- Kalker J.J. A streep theory for rolling with and spin. Physical Sciences. 1967. v. 60. PP. 10-62.
- Kalker J.J. On the rolling contact of two elastic bodies in the presence of dry fric¬tion. Thesis. Delft. 1973. P. 155 (N2), TND, N52, August, 1973.
- Kalker J.J. A fast algoritm for the simplified theory of rolling contact// Vehicle sys-tem dynamics. — 11 (1982), PP. 1 — 13.
- Joly R. Stability transversale dove ferroviaire. Possibility du systeme guide «rail- roure». Rail international / Jailed, 1984. p. 14 — 36.
- Голубенко А. Л. Сцепление колес с рельсом: Монография. К.: Фирма «Ви- пол». 1993.
- Винник Л.В. Колесная пара дифференциального вращения для вагонов мет-рополитена. Дисс. на соиск. уч. степ. канд. тех. наук. СПб.: ПГУПС 1997.
- Frederich F. Expérimente zur Spurfurung. ZEV-Glasers Annalen, 111 (1987) N6. s. 171-179.
- Есаулов В.П. и др. Восстановление работоспособности железнодорожных ко¬лес в процессе эксплуатации Е. П. Есаулов, А. В. Складковский, Е.Н. Шевчен- ко/ЛКонструкционно-технологическое обеспечение надежности колес рельсо¬вых экипажей. Сб. н-х тр. СПб.: ПГУПС. 1997. с. 36 — 45.
- L.I. Barteneva, V. Tutin, V. Kartsev, D. Veniaminov, V. Nikitin. Lubrication of Rails and Wheels on Russian Railways. Proceedings of IHHA’99 STS-Conference on Wheel/Rail Inter face. Moscow, 1999, V. 1, p. 205.
- S. Marich, S^^/tecHe and R. Fogary. The Optimization of Rail/Wheel Lubrication Practice in the Hunter Valley. RTSA Technical Conference, Core 2000. Adelaide, May 2000, p. 41.
- Марков Д.П. Повышение твердости колес подвижного состава. // Вестник ВНИИЖТ. 1995. №3. с. 10 — 17.
- Ларин Т.В. Износ и пути продления службы бандажей железнодорожных ко¬лес/ М.: Трансжелдориздат. 1958. 168 с.
- Ларин Т. В. Об оптимальной твердости элементов пары трения «колесо — рельс» // Вестник ВНИИЖТ. 1965. — №3. с. 5-9.
- Вихрова A.M., Ларин Т.В, Парышев Ю.М., Хургин Л.С. О соотношении твердостей рельсовой и колесной стали// Вестник ВНИИЖТ. 1983. №6. с.34 — 38.
- Паристый И.Л., Троицкий А.А., Исакаев Э.Х., Филиппов Г.А., Яблонский А.Э. Плазменное упрочнение колесных пар// Локомотив. 1999, №3, с. 32-33.
- Повышение работоспособности колес рельсового транспорта при ремонте технологическими методами / И.А. Иванов, С.В. Урушев, М. Ситаж, A.M. Бу- дюкин; Под ред. д-ра техн. наук И.А. Иванова. — СПб: Петербургский Государ-ственный Университет Путей Сообщения, 1995. — 124 с.
- Богданов А.Ф., Чурсин В.Г. Эксплуатация и ремонт колесных пар вагонов. — М.: Транспорт, 1985. — 270 с.
- Иванов И.А., Урушев С.В. О повышении ресурса цельнокатаных колес // Же-лезнодорожный транспорт. 2000. — №6. — с. 25-26.
- Иванов И.А. Повышение ресурса колес рельсовых экипажей. Дисс. на соиск. уч. степ, доктора техн. наук. СПб.: ПГУПС, 1993, 257 с.
- Певзнер В.О. Проблемы износа колес и рельсов. Влияние ширины колеи //Железнодорожный транспорт.-1996.№12.с.36-39.
- Иванов И.А. Алехин C.B. Перспективы совершенствования методов формо-образования профиля катания колесных пар. — Труды ЛИИЖТ, вып. 395. — Л.: ЛИИЖТ, 1976.
- Колесотокарный высокопроизводительный станок мод. 102. Каталог фирмы В. Хегеншейдт (ФРГ)
- Руководство на колесотокарные станки модель 1836, 183 А, КЗТС. — г. Крама-торск, 1971.
- Станок для шлифования профиля поверхности катания колесных пар. — Па¬тент США №3455065, 1965 г.
- Тырлик Т., Ольброт Э., Мащнашек Т. Станки для железнодорожного под¬вижного состава фирмы РАФАМЕТ. — материалы семинара. — Кузня Рацибор- ска, Польша, 1976, 18 с.
- Восстановление профиля поверхности катания колесных пар / И.А. Иванов, М. Ситаж, А.Ф. Богданов; Под ред. д-ра техн. наук И.А. Иванова. — СПб: Пе-тербургский Государственный Университет Путей Сообщения, 2000. — 127.
- А. с. РФ № 44559 МПК 7 В 23 В 5/23. Станок для обточки колесных пар без демонтажа их с железнодорожного транспортного средства./ Иванов И.А., Со¬рокин П.Г., Воробьев A.A. Зарегистрирована 27.03.05.
- Алехин C.B., Иванов И.А. Выбор метода обработки профиля поверхности ка-тания колесных пар // Новые достижения науки и техники в технологии маши-ностроения. Орел: Орловское отделение Приокского книжного издательства, 1976. с.7-9.
- Иванов И.А. Алехин C.B. Перспективы совершенствования методов формо-образования профиля катания колесных пар. // Технология производства и по-вышение долговечности деталей подвижного состава/ Сборник научных трудов — Л.:ЛИИЖТ, 1971. Вып. 329. с. 3-11.
- Алехин C.B., Иванов И.А. Эффективность методов формообразования про¬филя катания колесных пар // Материалы XXI научно-технической конферен¬ции. Л.: ЛИИЖТ, 1970. с. 113-114.
- Урушев C.B. Разработка ресурсосберегающих технологий ремонта колес же-лезнодорожного подвижного состава. Дисс. на соиск. уч. степ, доктора техн. наук. СПб.: ПГУПС, 2000, 450 с.
- Рауба A.A. Разработка системы использования твердосплавного инструмента для механической обработки деталей типа изношенных колесных пар. Дисс. на соиск. уч. степ, доктора техн. наук. М.: 2002, 338 с.
- Иванов И.А. Перспективы использования шлифования при восстановлении профиля катания колесных пар // Вопросы оптимизации технологических про-цессов и оборудования ремонтного производства. Повышение долговечности подвижного состава / Сборник научных трудов. — Л.: ЛИИЖТ. 1976.
- Старков В.К. Обработка резанием. Управление стабильностью и качеством автоматизированном производстве. М.: Машиностроение, 1989. 296 с.
- Гельфанд А.Е., Новгородов A.C., Фотеев Н.К. Обработка твердых сплавов. М.: МАШГИЗ, 1963. 243 с.
- Креймер Г.С. Прочность твердых сплавов. М.: Металлургия, 1971, 248 с.
- Лоладзе Т.Н. Прочность и износостойкость режущего инструмента. М.: Ма-шиностроение, 1982. 320 с.
- Методы определения качества металлокерамических твердых сплавов. Под ред. К.П. Имшенника. М.: ВНИИТС, 1968. с. 70.
- Остафьев В.А. Расчет динамической прочности режущего инструмента. М.: Машиностроение, 1979. 168 с.
- Повышение прочности и износостойкости твердосплавного инструмента/ Л.Г. Куклин, В.И. Сагалов, В.Б. Серебровский, С.П. Шабашов. М: Машино¬строение, 1968, 140 с.
- Третьяков В.И. Основы металловедения и технологии производства спечен¬ных твердых сплавов. М.: Металлургия, 1976. 528 с.
- Хает Г.Л. Прочность режущего инструмента. М.: Машиностроение. 1975, 168 с.
- Сборный твердосплавный инструмент / Г.Л. Хает, В.Н. Гах, К.Г. Громаков и др. М.: Машиностроение, 1989, 256 с.
- Шубин А.А., Жуков Д.А. Восстановление геометрических параметров про¬филя катания колесных пар с учетом физико-механических свойств обрабаты¬ваемой поверхности // Конструкционно-технологическое обеспечение надежно¬сти подвижного состава. Сб. науч. тр. Л.: ЛИИЖТ, 1985. с. 54-56.
- Владимиров Е.В. Автоматизация с помощью ЭВМ расчета режимов резания и норм времени при одноинструментной обработке деталей на металлорежу¬щих станках. Минск.: ИТК АН БССР. 1975. 95 с.
- Горанский Г.К., Владимиров Е.В., Ламбин Л.Н. Автоматизация технологиче¬ского нормирования на металлорежущих станках с помощью ЭВМ. М.: Маши¬ностроение, 1970. 220 с.
- Рыжов Э.В., Аверченко В.И. Оптимизация технологических процессов меха-нической обработки. Киев: Наук, думка, 1989. 192 с.
- САПР. Типовые математические модели и алгоритмы расчета оптимальных режимов одноинструментальной обработки материалов резанием. Методиче¬ские рекомендации МР 119 — 85. М.: ВНИИНМАШ, 1985. 120 с.
- Тинн К.А., Тыугу Э.Х. Технологические расчеты на ЭЦВМ. М.: Машино-строение, 1968. 351 с.
- Экономическая оптимизация процесса восстановления профиля поверхно¬стей катания колесных пар обточкой после отжига при нагреве токами высокой частоты/ М.М. Машнев, В.В. Диденко, А.П. Шифман, И.А. Иванов, А.Д. Але¬шин.// Конструкционно-технологическое обеспечение надежности подвижного состава. Сб. научн. тр. Л.: ЛИИЖТ. 1985. с. 48-53.