Сейчас ваша корзина пуста!
Теоретическое исследование процесса восстановления профиля катания колесных пар повышенной твердости
Цикл статей:
Глава 1 — Совершенствование технологии восстановления колесных пар повышенной твердости
Глава 2 — Перспективы использования колес повышенной твердости
Глава 3 — Теоретическое исследование процесса восстановления профиля катания колесных пар повышенной твердости
Глава 4 — Экспериментальное исследование обрабатываемости бандажной стали повышенной твердости
Глава 5 — Оптимизация процесса восстановления колесных пар повышенной твердости
Глава 6 — Технико-экономическая оценка результатов исследования
Методика расчета режимов резания колесных пар на основе термомеханического подхода
Существующие рекомендации по режимам резания при восстановлении профиля катания колесных пар [1, 2, 3 4] на основе эмпирического подхода [5], лишь в первом приближении характеризуют рациональную область допускаемых режимов резания. При этом учет изменяющихся условий резания, например, твердости обрабатываемой стали, геометрических параметров режущих пластин, критериев затупления и др., требует дополнительных экспериментов. Увеличение числа учитываемых факторов делает проблему эмпирического исследования и оптимизации обработки профиля колес трудноразрешимой.
Расчет сил резания
Методика, использовавшаяся ранее для расчета сил резания, содержала целый ряд допущений, существенно снижавших точность расчета [5]. Основные из этих допущений относятся к определению максимального значения касательных напряжений в зоне стружкообразования, на передней и задней поверхностях инструмента, к использованию коэффициента трения для расчета сил на передней поверхности и к предположению о равенстве коэффициентов трения на передней и задней поверхностях инструмента, к учету влияния формы режущей кромки в плане на направление и величину сил резания [5 — 7]. Не учитывалось влияние температуры на касательные напряжения и силы резания. Относительно невысокие требования к точности расчета сил не оправдывают принимаемых грубых допущений. Большая часть их не соответствует действительным физическим процессам. Особенно недопустимо применять некорректные методики расчета сил в тех случаях, когда силы резания используются для определения мощностей источников тепла (плотностей тепловых потоков). В связи с этим методика расчета сил должна быть усовершенствована и приведена в соответствие с современными представлениями о процессе резания, основанными на термомеханическом подходе [8].
Расчет температур
При восстановлении обточкой обода колеса, возникающие на поверхностях инструмента температуры, определяют работоспособность инструмента и ограничивают производительность обработки [8]. Необходимым и достаточным условием оптимальности протекания процесса обточки колесных пар, по мнению ряда авторов [4, 10], является реализация в зоне резания оптимальной температуры, которая составляет «870°С. Работа колесотокарных станков в производственных условиях с использованием оптимальной температуры резания или температуры формоустойчивости [8] является наиболее целесообразной.
К расчету температур в режущем инструменте предъявляются особо высокие требования. Это связано с тем, что небольшие ошибки, допущенные при расчете температуры, могут привести к весьма существенным погрешностям определения соответствующей этой температуре скорости резания. В использовавшихся ранее методиках [9, 10, 11] при расчете температуры деформации не учитывалось влияние скорости деформации, деформации и температуры на касательные напряжения (предел текучести), не учитывается сама величина конечных деформаций (конечный истинный сдвиг), равная относительному сдвигу. Температура передней поверхности считается пропорциональной корню квадратному из критерия Ре. В действительности это не так. В частности, экспериментальными данными исследователей [12, 13] доказано, что в области высоких температур рост температуры с увеличением критерия Ре замедляется, причем тем в большей степени, чем выше температура. Это свидетельствует об уменьшении предела текучести на передней поверхности с ростом температуры, то есть о разупрочнении обрабатываемого материала. Учет разупрочнения материала при повышении температуры является обязательным условием для повышения точности расчета температуры.
При расчете температуры задней поверхности не учитывался источник тепла на участке застойной зоны. Учет застойной зоны существенно влияет на распределение температуры на фаске износа задней поверхности. Не учитывается и возможное разупрочнение материала на задней поверхности, которое может иметь место при высоких скоростях резания и большой ширине фаски износа.
В связи с этим значительный практический и теоретический интерес представляет создание программ, позволяющих выполнить анализ токарной обработки железнодорожных колесных пар теоретически, с помощью расчетов на ЭВМ. Решение этой задачи потребовало разработки методики расчета температур и напряжений на поверхностях режущего инструмента, обоснования выбора теоретически определяемых факторов, тесно связанных с изнашиванием и деформацией режущих лезвий, разработки методики расчета сил резания и отклонений обработанной поверхности. При расчете сил, температуры и напряжений на поверхностях режущего лезвия использовался термомеханический подход.
Расчет и анализ сил резания при прямоугольном точении чашечным резцом и резцом с прямолинейной режущей кромкой с закругленной вершиной
Рассмотрим точение чашечным резцом или криволинейной частью резца с закругленной радиусом г вершиной и геометрией в плоскости стружкообразования по рис.3.1.
Для расчета сил при прямоугольном точении инструментом с криволинейной режущей кромкой, рассмотрим малый отрезок режущей кромки Д/ (рис. 3.1), считая его прямолинейным и наклоненным к направлению подачи под углом в плане срх. Приращение силы на передней поверхности в горизонтальной плоскости и приращение нормальной силы на задней поверхности направлены перпендикулярно отрезку режущей кромки Д/. Эти силы могут быть вычислены по методике, описанной в [8, 14]:
На рис. 3.14. показаны проекции приращений этих сил на оси у и х.

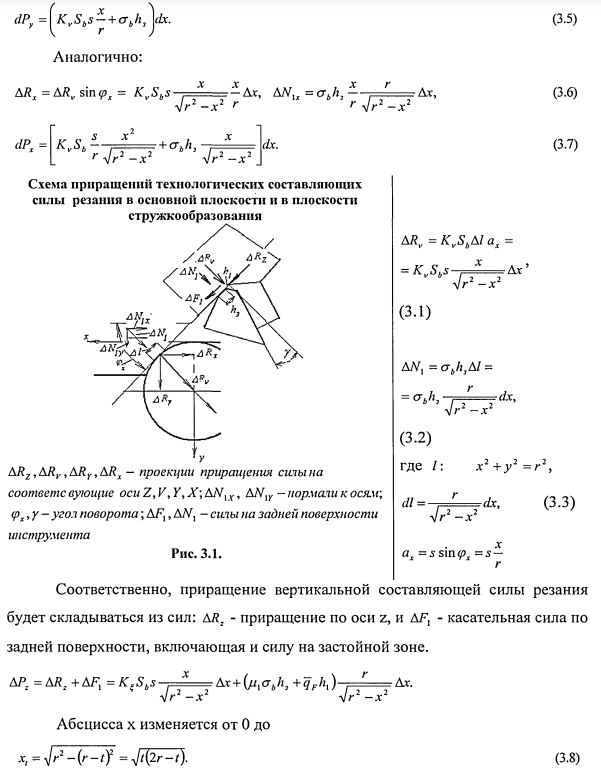
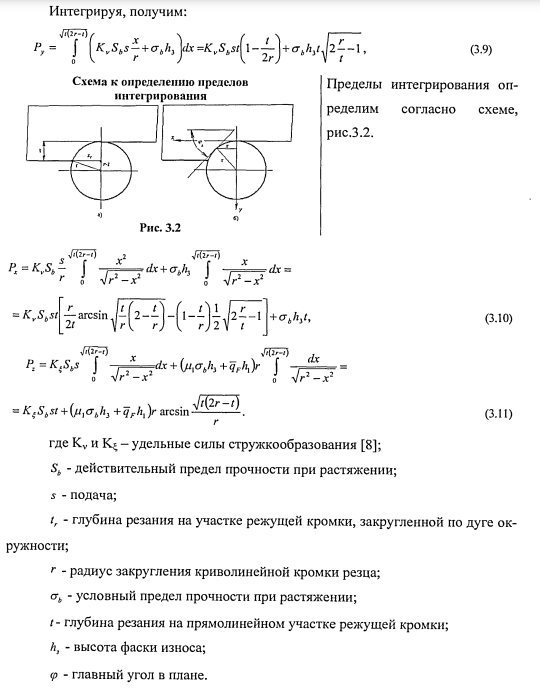
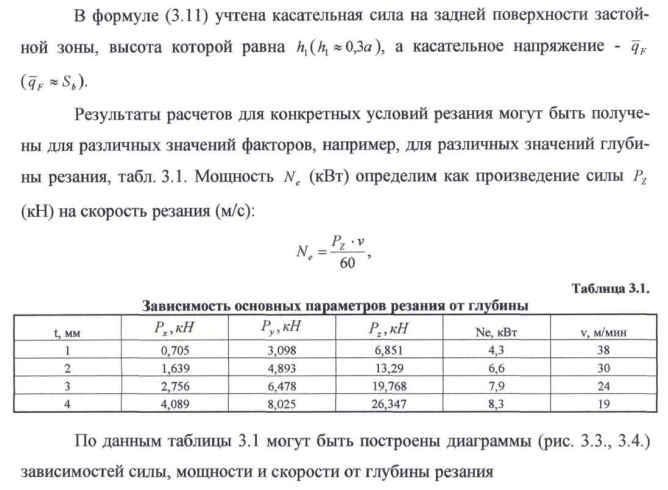
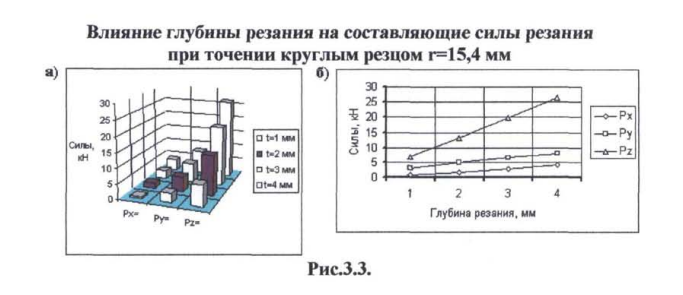
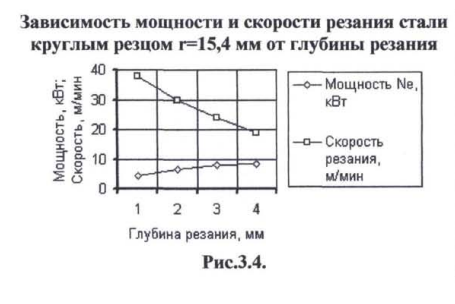
С увеличением глубины резания при точении чашечным резцом возрастает максимальная толщина срезаемого слоя, происходит возрастание силы резания (рис.3.3) и, следовательно, увеличиваются температуры передней,
задней поверхностей и температура резания. Для постоянства оптимальной температуры (температуры формоустойчивости) увеличение толщины срезаемого слоя необходимо компенсировать соответствующим снижением скорости резания (рис.3.4), что свидетельствует о целесообразности использования чашечного резца для чистового прохода.
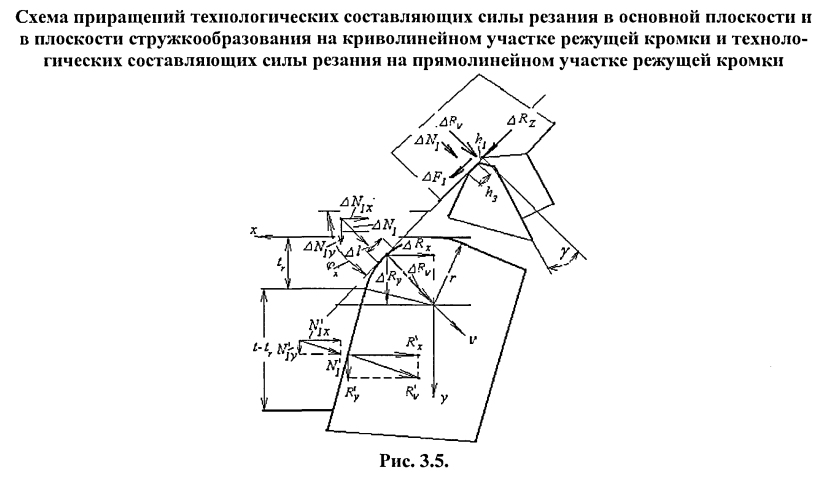
Проводя аналогичные рассуждения для «призматического» резца (рис. З.5.), имеющего участок криволинейной кромки — закругления вершины резца в плане, и участок прямолинейной кромки, расположенной под углом в плане ср, силы резания могут быть вычислены суммированием сил, вычисленных для каждого из названных участков:
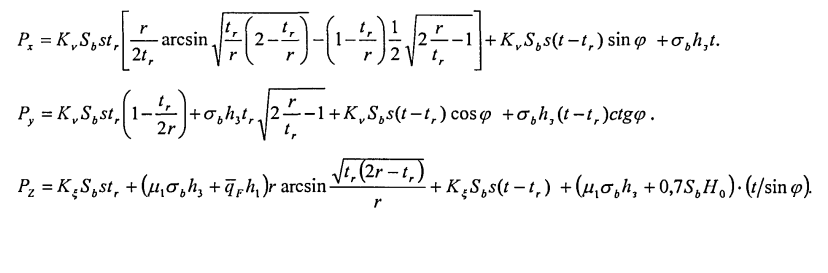
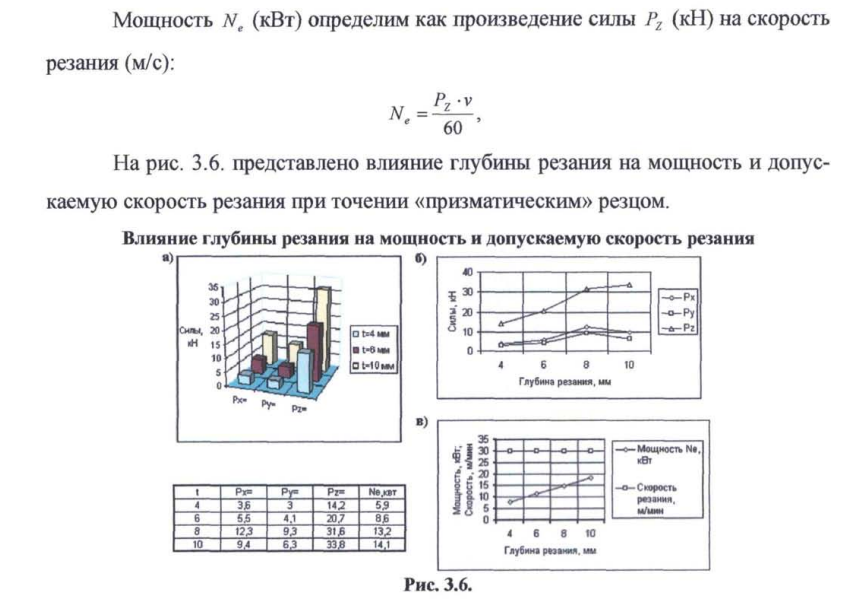
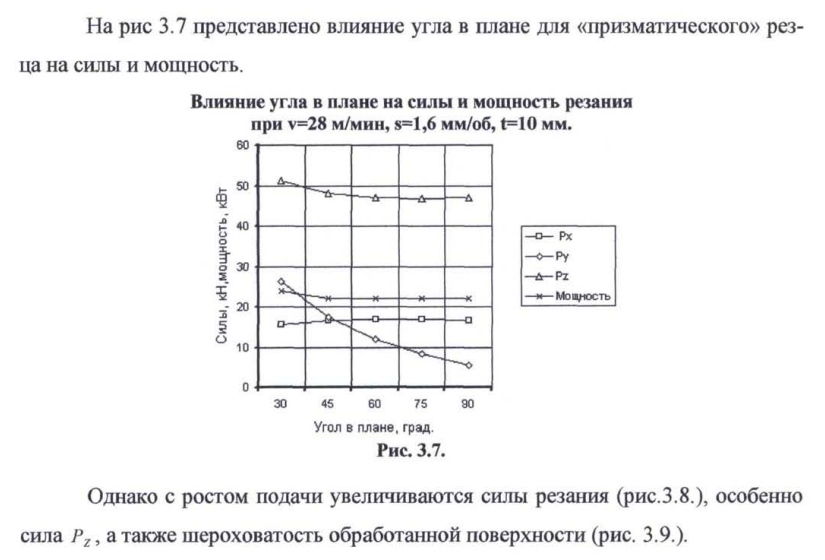
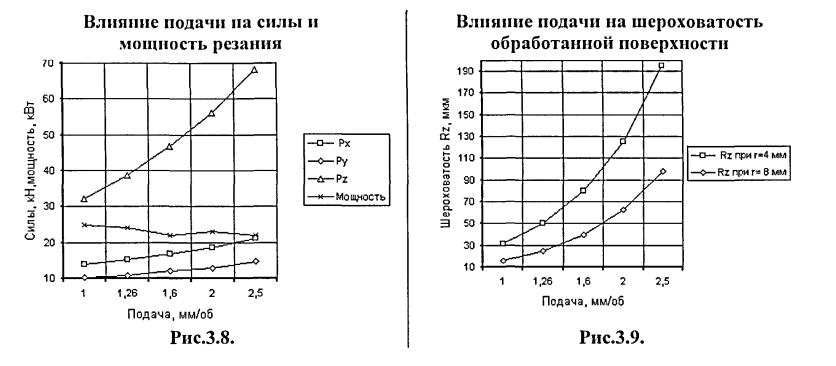
Расчет отклонений поверхности колеса из-за сил резания и износа резца
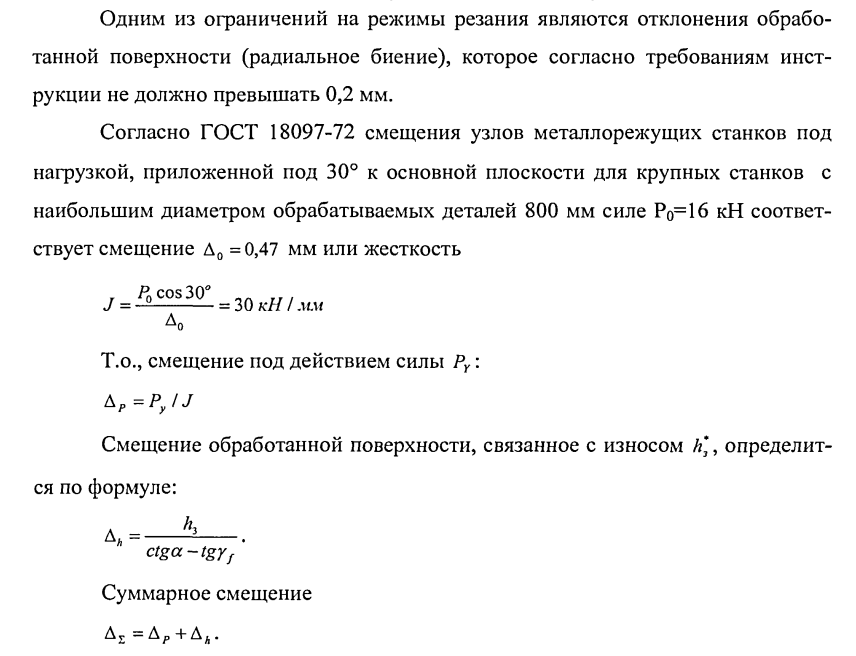
При точении чашечным резцом, чтобы отклонение обработанной поверхности было в пределах нормы (до 0,2 мм) глубина резания при чистовом проходе не должна превышать 2 мм (рис.3.10).
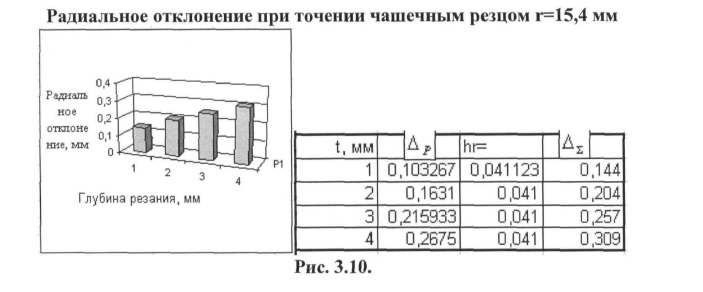
Расчет и анализ температур передней и задней поверхностей резца при восстановлении профиля катания колесной пары
Рассмотрение закономерностей распределения теплоты имеет большое значение для понимания физической сущности для понимания физической сущности и для разработки универсальных и точных методов расчета характеристик процесса резания. Значительный вклад в исследовании оценки температур в режущем инструменте при обработке колес как численными методами так и экспериментально внес д.т.н. профессор кафедры «Теплотехника и теплосиловые установки » ПГУПС И.Г. Киселев.
В работах проф. Киселева И.Г. предложен общий подход к рассмотрению и решению задач теплофизики, возникающих при ремонте колесных пар [15, 16, 17]. Теоретически краевые задачи теплопроводности сформулированы для любых объектов с различными условиями теплообмена на границах. При решении линейных и нелинейных краевых задач теплопроводности применительно к составным телам сложной формы (бандажное колесо, сборный режущий инструмент и др.) предпочтение было отдано методу последовательного энергетического баланса.
При анализе температурных полей резца отмечается, что преобладающим является тепловой поток, поступающий с передней поверхности инструмента. Часть этого потока попав в резец, отводится через заднюю поверхность инструмента в колесо и окружающую среду. Это приводит к перемене знака радиального градиента температуры, близко расположенной к этой поверхности резца.
В настоящей работе для получения более точных данных о распределении температур на рабочих поверхностях инструмента при восстановлении профиля колеса использован термомеханический подход, учитывающий изменение свойств обрабатываемого материала при высоком уровне скорости деформации, изменяющихся деформациях и температурах, характерных для процесса восстановления.
Тепловые потоки и температура контактных слоев передней и задней поверхностей режущего инструмента оказывают значительное влияние на его состояние. Резкое изменение этих параметров в начале процесса резания, их высокий уровень и различные скорости прогрева инструмента приводят к возникновению дополнительных термических напряжений. Частые повторные действия термических напряжений ведут к термоусталостному разрушению резцов. В основу расчета температуры на поверхностях инструмента положен термомеханический подход, описанный в [8] с использованием методов подобия для резания материалов, разработанными С.С. Силиным [10]. На основе анализа уравнения баланса механической и тепловой энергии при резании металлов С.С. Силин использует в расчетах безразмерные комплексы (критерии подобия)
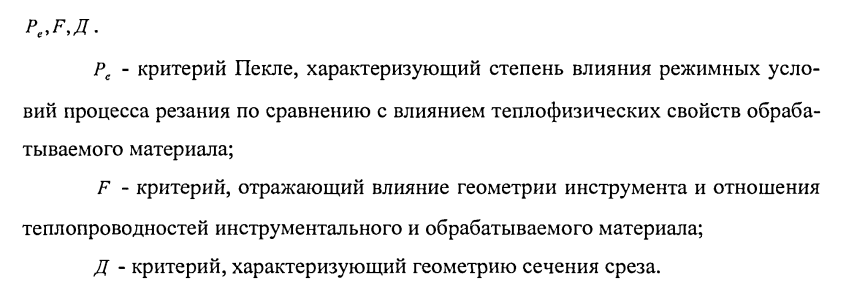
При расчете температур на рабочих поверхностях режущего инструмента решалась задача теплопроводности, описываемая уравнением Фурье (3.12) с граничными условиями всех четырех видов. При этом определяющими являются
граничные условия со стороны передней и задней поверхностей резца, контактирующих с деталью и стружкой.
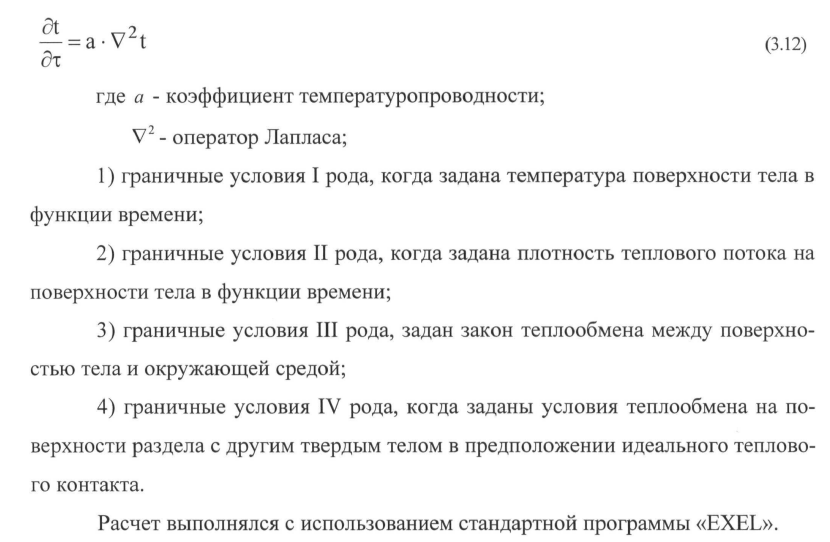
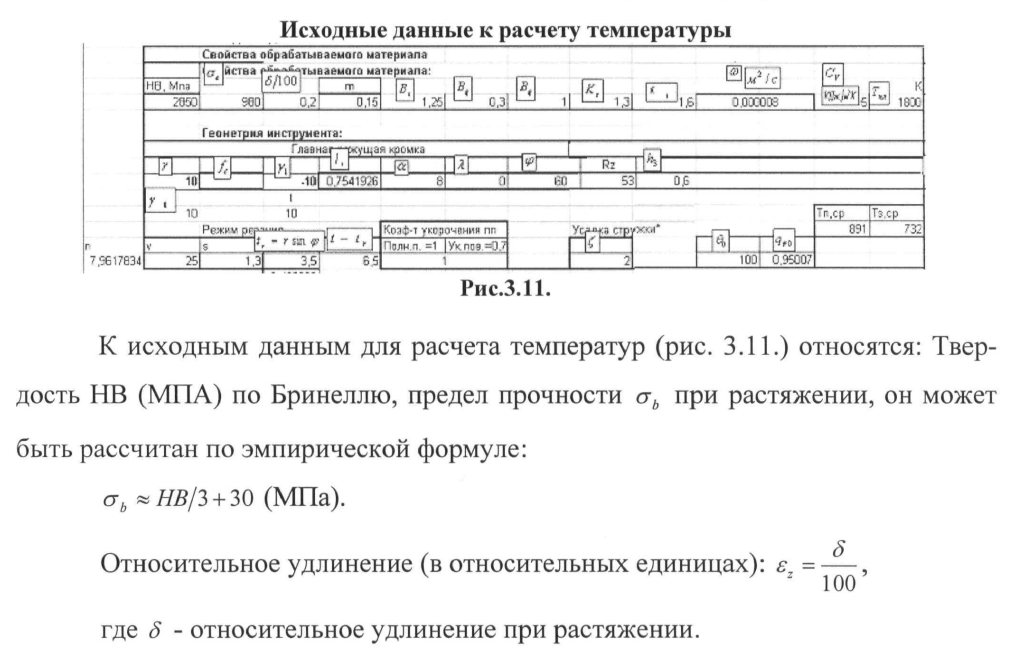
Определяющие уравнения для идеально пластического и упрочняемого материалов могут рассматриваться как упрощенные частные случаи более общего определяющего уравнения [8], отражающего влияние на предел текучести и деформации, и скорости деформации, и температуры. Примером такого обобщенного определяющего уравнения служит функция вида
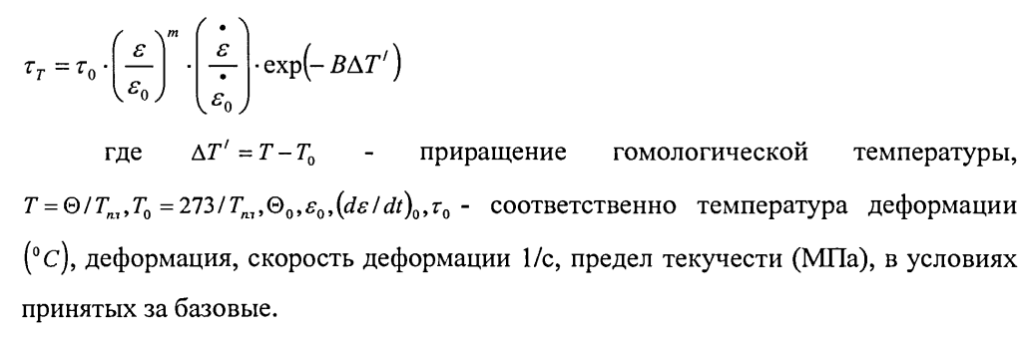
Для условий резания металлов представляет особый интерес учет изменений температуры, вызванных деформацией. Наиболее просто приращение температуры связано с деформацией в адиабатических условиях, т.е. в таких условиях, когда вся теплота остается в том объеме материала, в котором оно выделилось при деформации.
Поскольку в большинстве случаев перетоками теплоты в широкой области деформаций и оттоками теплоты из этой области в деталь можно пренебречь, то условия деформации материала в этой области могут быть охарактеризованы как адиабатические, т.е. без теплообмена деформируемой частицы с окружающим ее металлом. В этом случае с ростом текущего значения деформации соответственно увеличивается и температура. При допущении о постоянстве скорости деформации два последних сомножителя определяющего уравнения линейно зависимы и уравнение может быть представлено в виде [8].
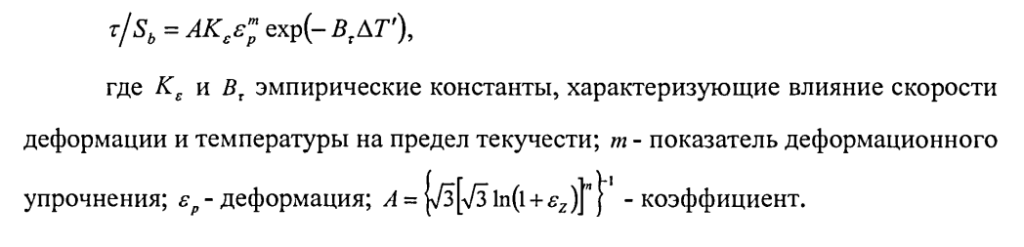
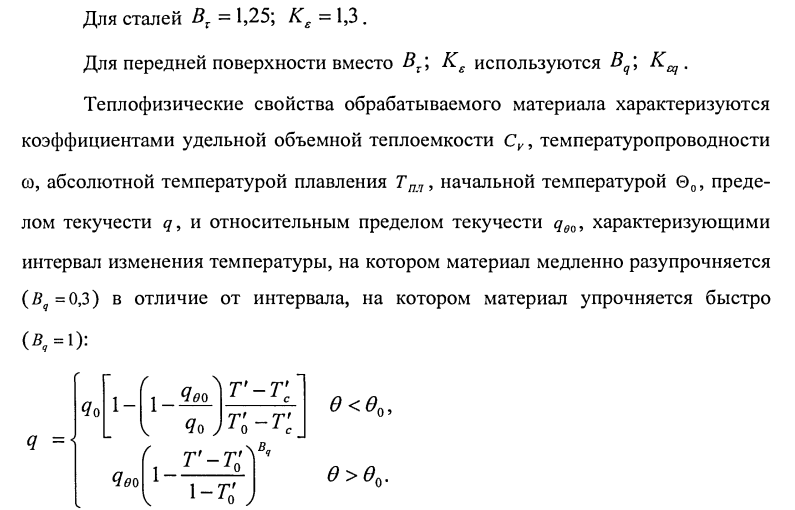
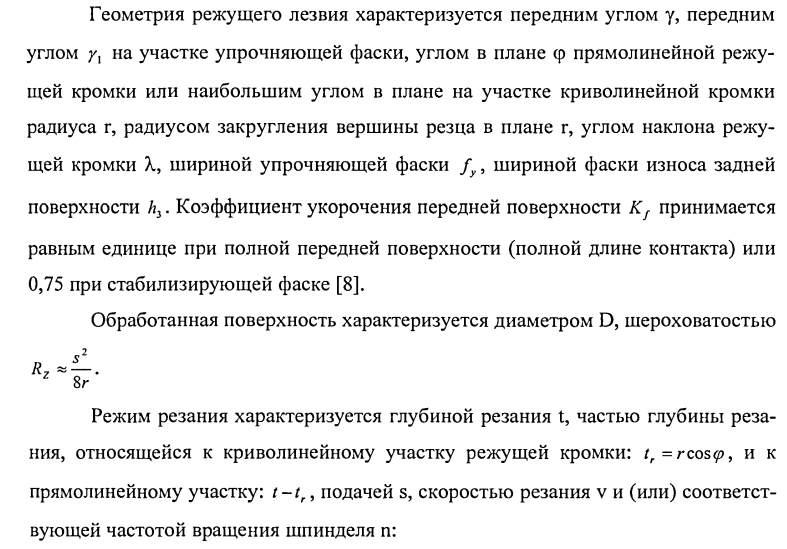
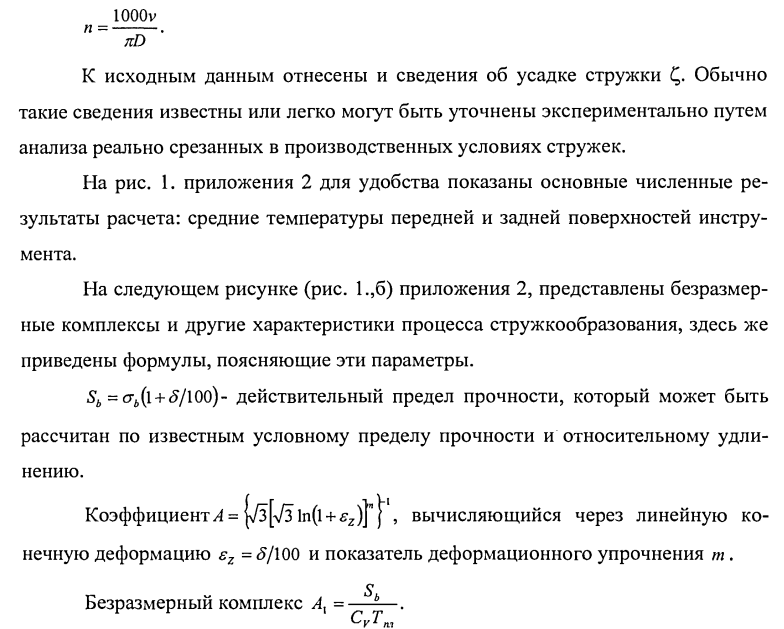
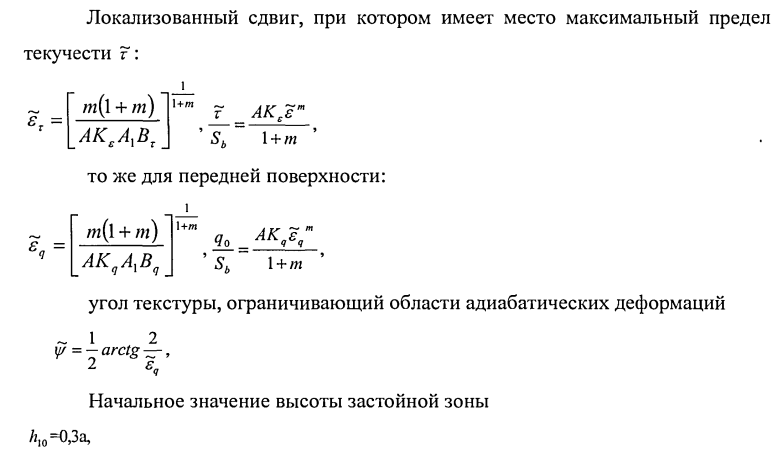
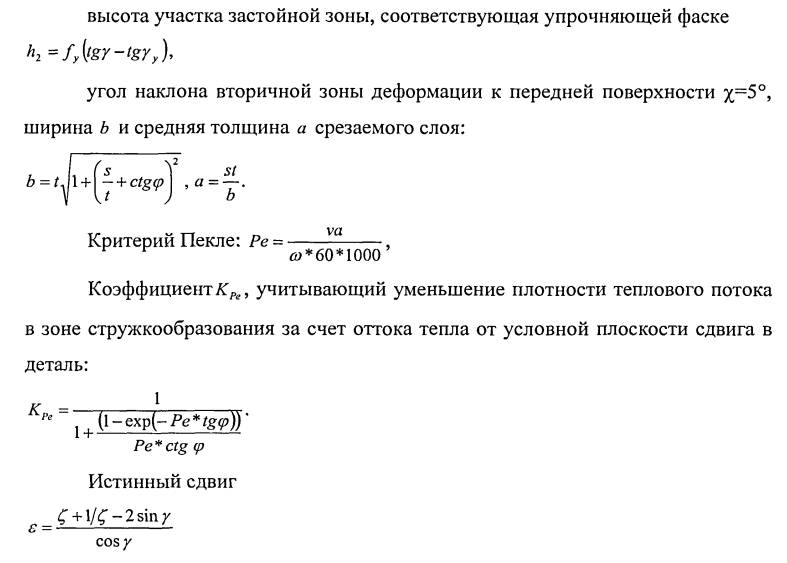
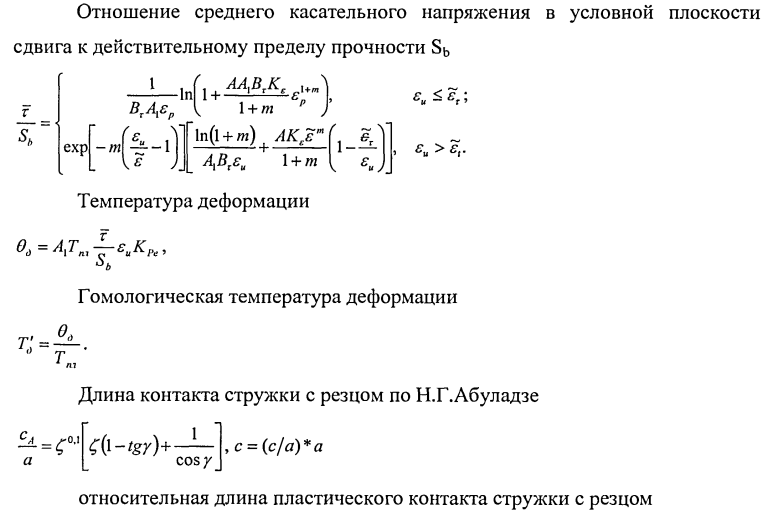
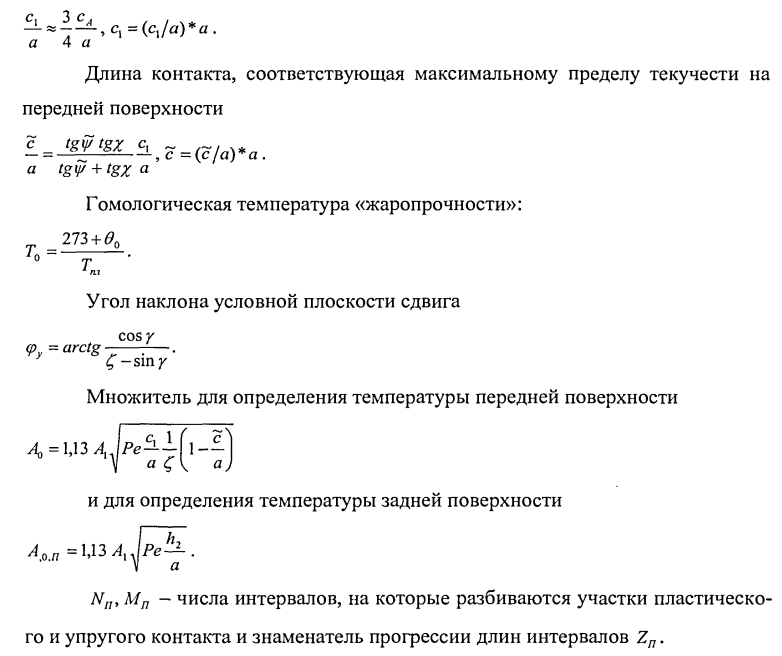

Строки первой матрицы представляют значения источника тепла и стоков, учитывающих разупрочнение материала под действием температуры.
В первом столбце матрицы указаны значения источника тепла, плотность теплового потока которого соответствует максимальному значению предела текучести на передней поверхности. Столбцы второй матрицы содержат значения длин соответствующих интервалов. Произведение матриц дает распределение температуры по длине контакта стружки с передней поверхностью резца.
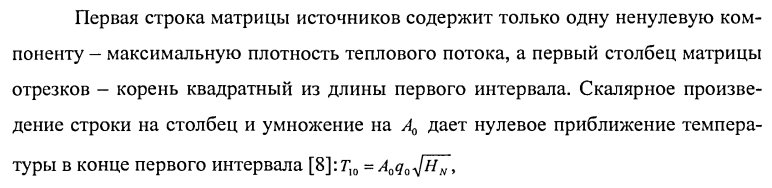
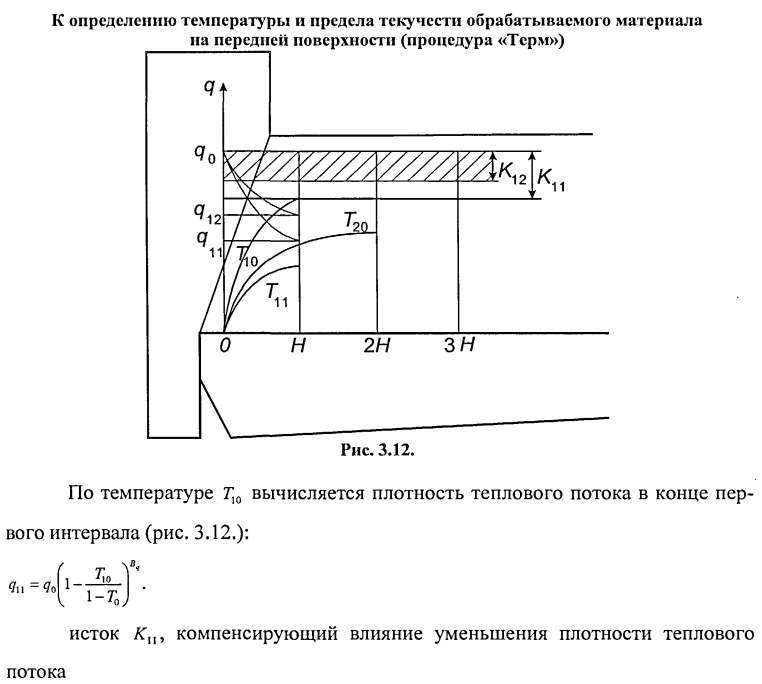
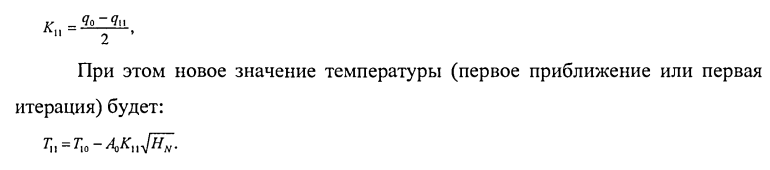
Итерации повторяются до получения устойчивого результата. Как правило, для этого достаточно 3-4 итераций. Кроме того, сходимость и устойчивость решения зависит от длины интервала. Первые интервалы должны быть достаточно малыми, так как температура на этом интервале возрастает быстро. Благодаря такому подходу, учитывающему зависимость плотности теплового потока от температуры, нелинейное дифференциальное уравнение теплопроводности сводится к линейному на каждом из интервалов и на каждой итерации.
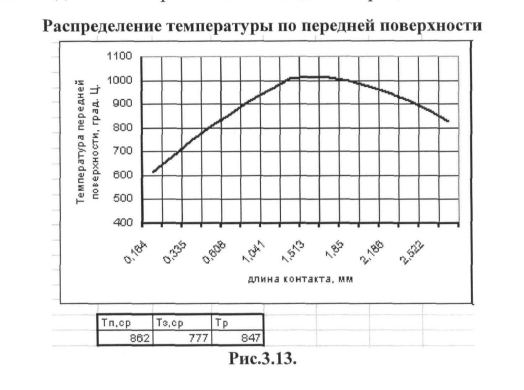
На следующем интервале добавляется еще один сток и т.д.
Зависимость температуры от координаты передней поверхности представляется в виде графика (рис. 3.13.).
Аналогично рассчитывается и температура задней поверхности. Здесь итерации предусмотрены только для участка задней поверхности застойной зоны, для которого выделены 8 интервалов представленных на рисунках 3 и 4 приложения 2.
Зависимость температуры задней поверхности от координаты задней поверхности представлена в виде графика (рис.3.14).
Температура более 700° С на режущей кромке достигается под воздействием источника тепла, расположенного на участке застойной зоны. Поскольку плотность теплового потока на участке застойной зоны значительно выше, чем на фаске износа, температура на фаске износа на некотором участке не только не возрастает, но напротив даже несколько уменьшается, достигая минимума, и только затем увеличивается. Благодаря этому заточка на задней поверхности фаски первоначального притупления величиной около 0,2 — 0,3 мм практически не вызывает повышения температуры или вызывает несущественное повышение температуры. Однако это наблюдается при относительно невысокой скорости резания. Такое первоначальное притупление благоприятно с точки зрения повышения пластической прочности режущего лезвия.
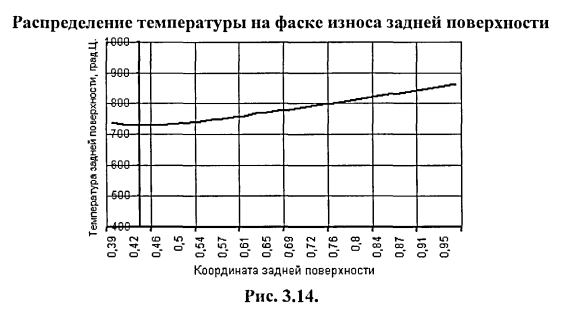
Проанализируем влияние отдельных факторов на расчетные температуры. При постоянных подаче 5 и угле в плане ф и постоянной ширине фаски износа, примерно равной критерию затупления h3 = 1 мм с ростом скорости резания температуры на передней и задней поверхностях инструмента растут, рис. 3.15.
При этом температура задней поверхности растет быстрее, чем температура передней поверхности. Медленный рост температуры передней поверхности связан с разупрочнением обрабатываемого материала с повышением температуры. Если бы теплостойкость инструментального материала и его прочность при высоких температурах были бы выше, чем у реальных сплавов типа Т14К8 или Т5К10, то повышение скорости резания, соответствующее повышению производительности обработки было бы целесообразным. Однако как раз в области повышения температуры от 800°С прочностные характеристики режущего лезвия резко снижаются, а вероятность деформаций и последующего катастрофического износа или разрушения (поломки) режущей пластины возрастает.
На прочность и формоустойчивость режущего лезвия оказывают влияние обе температуры: и на передней и на задней поверхностях инструмента. Но в каком соотношении они влияют на работоспособность инструмента? В том соотношении, в каком они влияют на температуру резания, или в другом? В работе [8] используется понятие температуры формоустойчивости режущего лезвия, которая кажется более подходящей для характеристики износостойкости и работоспособности режущего лезвия.
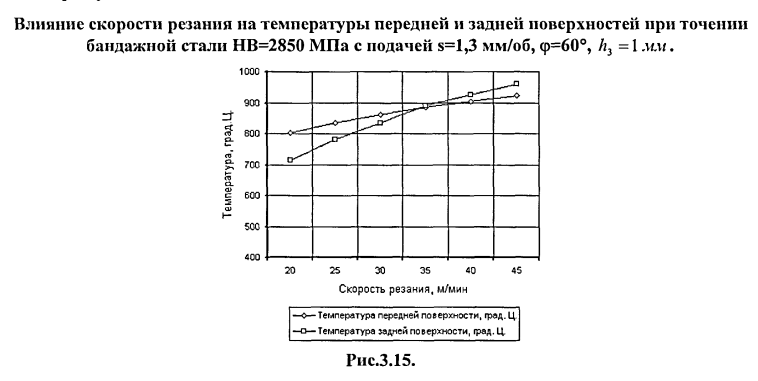
Температура формоустойчивости характеризует в среднем температуру внутри режущего лезвия, оказывающую сильное влияние на пределы прочности инструментального материала. Режущее лезвие (клин) прогревается равномерно по сечению в том случае, когда температуры передней и задней поверхностей равны друг другу. В случае неравенства этих температур точки, соответствующие возникновению катастрофического износа (или точки, соответствующие постоянной интенсивности изнашивания инструмента) располагаются на кривой, близкой к окружности (рис. 3.16).

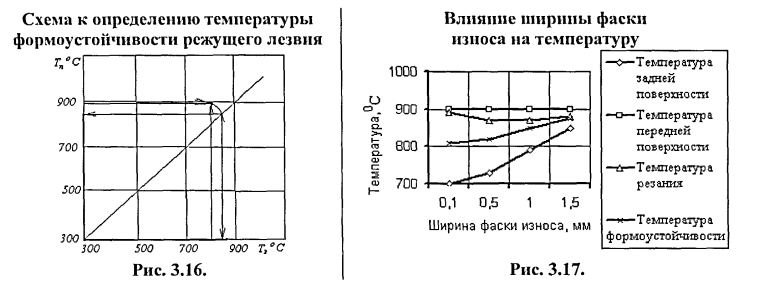
При износе инструмента температура передней поверхности практически постоянна (если существенно не изменяется передний угол в случае образования лунки), а температура задней поверхности, начиная с некоторых небольших значений ширины фаски износа, растет (рис.3.17). Вместе с ней увеличивается и температура внутри режущего клина. Эта тенденция хорошо улавливается температурой формоустойчивости, в то время как температура резания сначала уменьшается, а затем практически мало меняется. Следовательно в качестве температурного фактора, влияющего на формоустойчивость и износостойкость инструмента следует использовать температуру формоустойчивости, а не температуру резания.
Однако, учитывая, что в работах [18, 19-21] часто используется именно температура резания, приведем данные и об ее изменении.
Основной задачей исследования и оптимизации является повышение производительности [22 — 24] (или достижение наибольшего возможного уровня производительности) при сохранении рационального уровня температуры. Поэтому необходимо выяснить какие факторы способны снизить температуру при постоянной производительности.
Еще одной задачей является обоснование и выбор температурного фактора, наиболее тесно связанного с допускаемыми (рациональными) режимами резания и износостойкостью режущего инструмента. Традиционно в качестве основного температурного фактора использовалась температура резания, определявшаяся либо экспериментально — методом ее тественной термопары, либо расчетным путем как средняя между температурами передней и задней поверхностей инструмента.
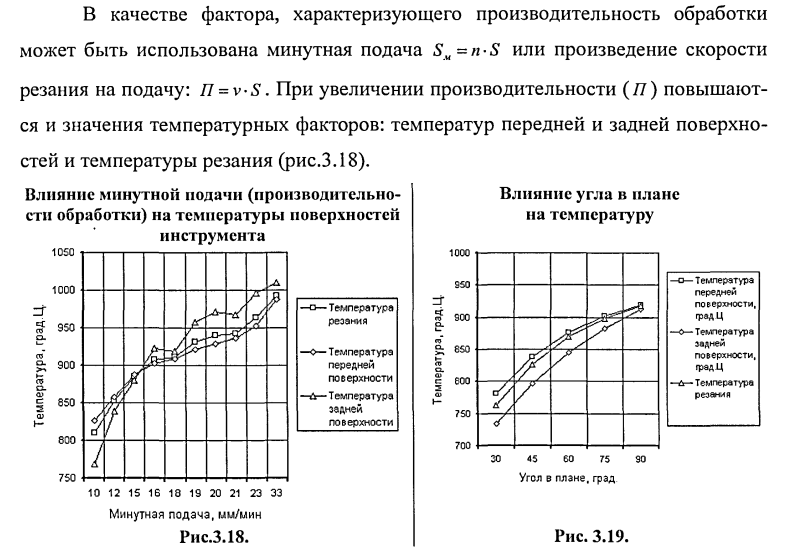
Довольно существенное влияние на температуру оказывает изменение угла в плане (рис.3.19).
Увеличение подачи на оборот при постоянной минутной подаче приводит к снижению температуры. Особенно существенно снижается температура задней поверхности.
Как следует из рис. 3.23, при достаточно больших значениях толщины срезаемого слоя, характерных для обтачивания железнодорожных колес, температуры передней поверхности и резания близки друг к другу. Особенно они близки при точении резцом с небольшой шириной фаски износа. Поэтому в первом приближении в качестве характеристики температуры могут использоваться как температура передней поверхности, так и температура резания.
Большое значение имеет переход от температуры, рациональные значения которой, как правило, известны и находятся в достаточно узком диапазоне, к соответствующей (рациональной) скорости резания, значения которой могут изменяться в более широком диапазоне в зависимости от твердости обрабатываемого материала, подачи, угла в плане, переднего угла, ширины фаски износа и других факторов (рис.3.21.).
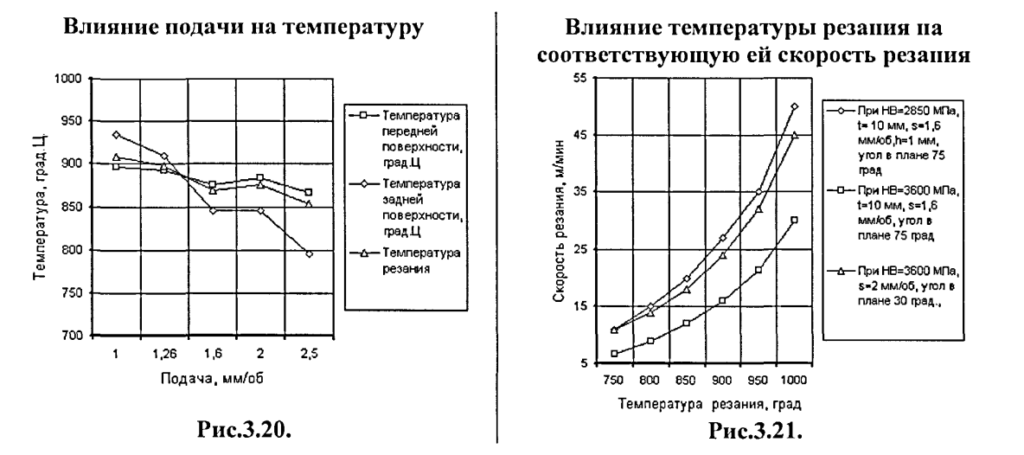
Такой переход может быть выполнен только с помощью достаточно точных расчетов, основанных на термомеханическом подходе.
Зависимости допускаемой скорости от температуры описываются вогнутыми кривыми (рис. 3.21.). При интенсивных режимах резания, соответствующих повышенным температурам увеличение скорости резания вследствие разупрочнения материала все слабее влияет на температуру. При этом создается обманчивое впечатление, заключающееся в том, что поскольку скорость резания слабо влияет на температуру, ее можно повышать. Однако в действительности максимальные и средние температуры передней и задней поверхностей и, следовательно, и температура резания должны быть ограничены рациональными значениями, в качестве которых в первом приближении может быть принята «оптимальная температура», рекомендуемая С.С.Силиным — 870 °С, а также полученная в работах кафедры «Технология металлов».
Меньшие углы в плане (например, 30°) могут быть применены при небольших глубинах резания (рис.3.22).
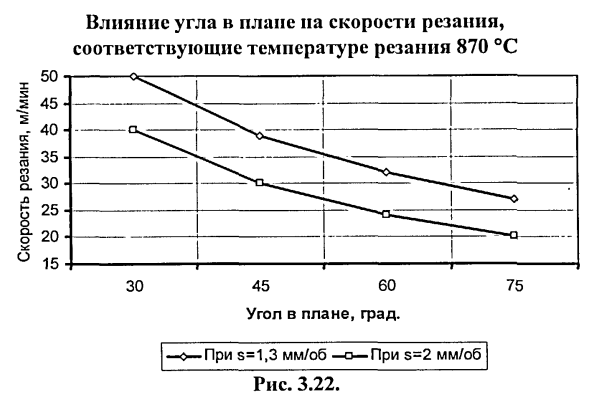
Уменьшение угла в плане существенно снижает температуру (рис. 3.24) при этом скорость резания может быть увеличена (рис З.7.), но увеличивает силу Ру [25, 26].
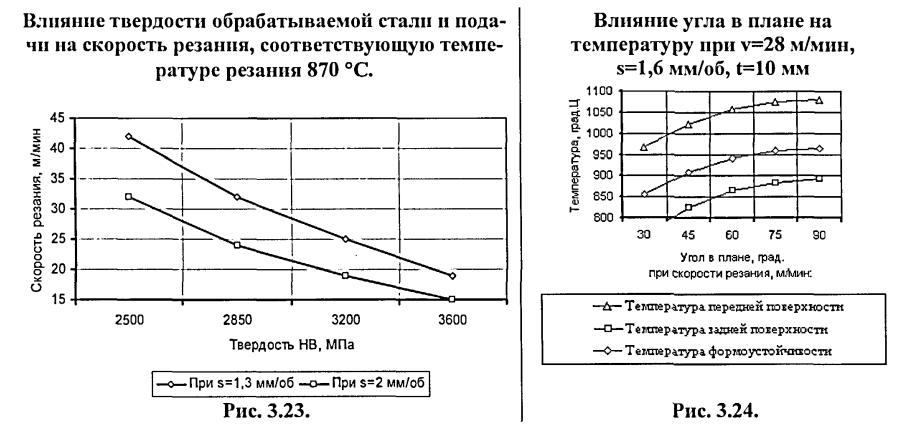
Характеристики процесса резания при различном износе инструмента
В связи с отсутствием надежных экспериментальных данных и производственных наблюдений об изнашивании режущих пластин при обработке железнодорожных колес из колесной стали, близкой по составу к углеродистой стали 60, воспользуемся данными «Сандвик Коромант» (см. табл. 3.2) [27]. Значение стойкости для скорости 20 м/мин получено экстраполяцией.
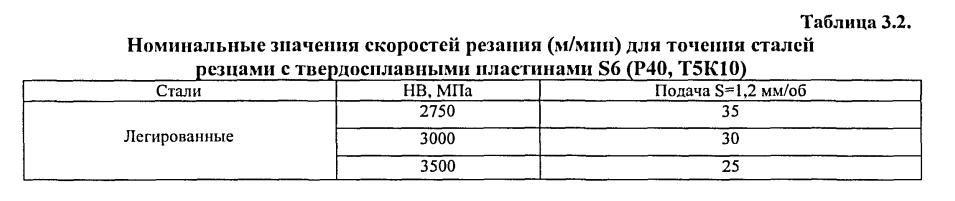
В качестве критерия затупления по задней поверхности принята ширина фаски износа 1 мм (см. табл. 3.3). Средние значения интенсивности изнашивания в первом приближении рассчитывались как отношение ширины фаски износа к пути резания.
Значения интенсивностей изнашивания при точении с толстыми срезами (о,25 — 2,5)-106 на порядок больше, чем при точении с тонкими и средними срезами [20]. Это свидетельствует о большой роли пластических деформаций в формоизменении и изнашивании режущего лезвия. В связи с этим в качестве температурного фактора целесообразно использовать температуру формоустойчивости режущего лезвия.
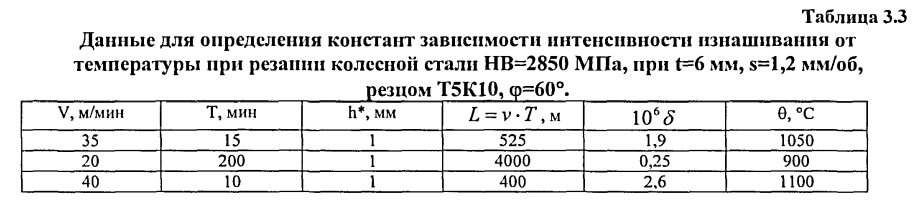
Пластические деформации режущего клина происходят с тем большей скоростью, чем выше отношение эквивалентных напряжений к допускаемому эквивалентному напряжению. Предполагается, что допускаемое эквивалентное напряжение зависит от температуры внутри режущего лезвия. В качестве характеристики этой температуры нами используется температура формоустойчивости:
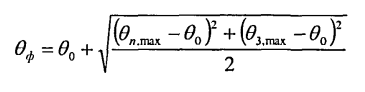
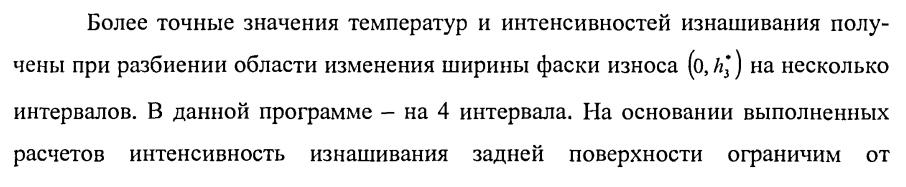
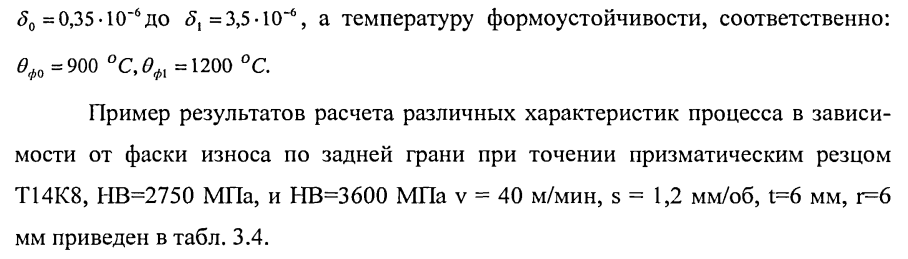
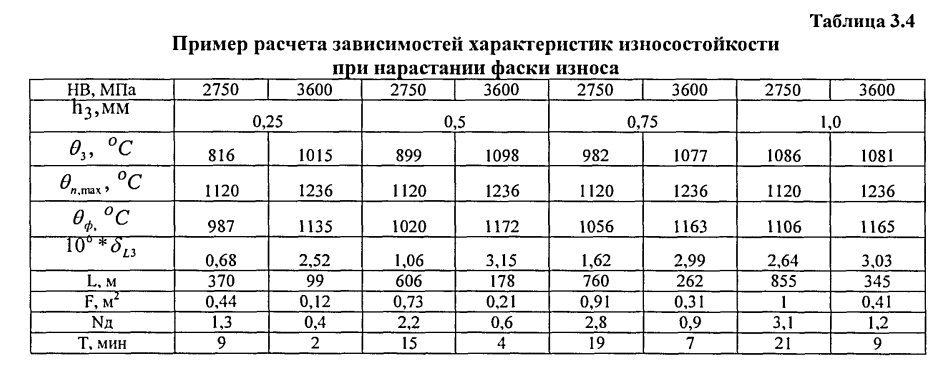
Эти результаты могут быть представлены в табличной форме или в виде графиков.
Кроме указанных данных представлены ранее вычисленные результаты по силам резания, мощности, отклонениям обработанной поверхности и шероховатости поверхности. Условия резания для рис. 5-14, приложения 2. те же, что и для табл. 3.3.
Выводы по главе 3
- Предложена методика оценки процесса восстановления колесных пар на
основе термомеханического подхода; - Получены аналитические зависимости, разработана прикладная про-грамма и создана виртуальная среда для анализа показателей процесса восстанов-ления колесных пар;
- Выполнен расчет и анализ сил и температур, возникающих в процессе восстановления, для колес с обычной и повышенной твердостью. В качестве ог-раничения для режущего инструмента принята температура формоустойчивости режущего лезвия ~ 870° С;
- Получены значения температур, сил резания, стойкости инструмента и др. параметров режима резания в зависимости от величины фаски износа.
Список использованной литературы
- Восстановление профиля поверхности катания колесных пар / И.А. Иванов, М. Ситаж, А.Ф. Богданов; Под ред. д-ра техн. наук И.А. Иванова. — СПб: Петербург¬ский Государственный Университет Путей Сообщения, 2000. — 127 с.
- Богданов А.Ф., Чурсин В.Г. Эксплуатация и ремонт колесных пар вагонов. — М.: Транспорт, 1985. — 270 с.
- Иванов И.А. Повышение ресурса колес рельсовых экипажей. Дисс. на соиск. уч. степ, доктора техн. наук. СПб.: ПГУПС, 1993, 257 с.
- Макаров А. Д. Оптимизация процессов резания. — М.: Машиностроение, 1976, 276 с.
- Бобров В.Ф., Грановский Г.И., Зорев H.H. и др. Развитие науки о резании ме-таллов. — М.: Машиностроение, 1967, с. 416.
- Зорев H.H. Расчет проекций сил резания. — М.: Машгиз, 1958, 56 с.
- Клушин М.И. Резание металлов. — М.: МАШГИЗ, 1958.
- С.А.Васин, А.С.Верещака, В.С.Кушнер. Резание материалов: Термомеханиче¬ский подход к системе взаимосвязей при резании: Учеб. для техн. вузов.-М.: Изд- во МГТУ им. Н.Э.Баумана, 2001.- 448 с.
- Силин С.С. Метод подобия при резании материалов. — М.: Машиностроение, 1979, 152 с.
- Шубин А. А. Оптимизация процесса восстановления профиля поверхности ка-тания вагонных колесных пар. Дисс. на соиск. уч. степ. канд. тех. наук. Л.: ЛИ- ИЖТ. 1986.
- Резников А.Н., Резников Л.А. Тепловые процессы в технологических систе¬мах: Учебник для вузов по специальности «Технология машиностроения и «Ме-таллорежущие станки и инструменты». М.: Машиностроение, 1990. — 288 е.: с ил.
- Силин С. С., Верещака А. С., Рыкунов А. И. К вопросу о применении износо-стойких покрытий при точении жаропрочных материалов // Резание и инструмент. — Харьков: Вища школа, 1985. — №33. — с. 81-86.
- Талантов Н. В. Физические основы процесса резания, изнашивания и разру¬шения инструмента. — М.: Машиностроение, 1992.
- A.A. Воробьев, П.Г. Сорокин Силы резания при восстановлении профиля обо¬да бандажа чашечными резцами. // Межвузовская научно — техническая конфе¬ренция студентов и молодых ученых: Шаг в будущее (неделя науки — 2004). — СПб. : ПГУПС, 2004. — с. 17.
- Киселев И.Г. Теплообменные процессы при ремонте колесных пар подвижно¬го состава железных дорог. — Zeszyty naukove Politechniki Slaskiej, №1048, Seria Transport. Z.14. Gliwice: 1989, Str. 131-142.
- Иванов И.А., Киселев И.Г. и др. Анализ тепловых процессов в технологиче¬ских системах обработки железнодорожных колес. Конструкционно- технологическое обеспечение надежности подвижного состава: Сб. статей. — СПб.: ПГУПС, 1997.-с. 100-111.
- Бобров В.Ф. Основы теории резания металлов. — М.: Машиностроение, 1975. с. 344.
- Силин С.С. Применение метода подобия для определения обрабатываемости современных материалов. — Труды Рыбинского авиационно-технологиченского ин-та, №3 -Ярославль, 1975. с. 5-33.
19 Силин С.С. К вопросу теоретического обоснования автоматизации процессов механической обработки по температуре резания — Труды Ярославльского поли-технического института. — Ярославль, 1976, с. 5-11. - Лоладзе Т.Н. Прочность и износостойкость режущего инструмента. -М.: Ма-шиностроение, 1982, 320 с.
- Иванов И.А. К вопросу оптимизации обработки цельнокатаных колес путем стабилизации температуры резания.- В кн. «Совершенствование технологическо¬го процесса ремонта и формирования колесных пар подвижного состава. — Л.: 1979. с. 97-102.
- Рекомендации по использованию и назначению параметров режима механиче¬ской обработки при восстановлении профиля поверхности катания вагонных ко¬лес. — М.: ЦВ МПС, 1994, 26 с.
- Иванов И.А., Урушев C.B., Алешин А.Д. Оптимизация параметров режимов резания цельнокатаных колес./ Zeszyty naukove Politechniki Slaskiej, №1094, Seria Transport. Z.15. Gliwice: 1990, Str. 79-92.
- И. А. Иванов, А. А. Воробьев, В. С. Кушнер, А. С. Безнин Влияние твердости поверхности катания железнодорожных колес на параметры режима обработки // Новые материалы и технологии в машиностроении. Сборник научных трудов / Под ред. Е.А. Памфилова. — Выпуск 3. — Брянск: БГИТА, 2004. — с. 37 — 41.
- А. А. Воробьев. О причинах повышенного износа колесных пар подвижного состава и оценка обрабатываемости колес повышенной твердости // Международ¬ная конференция: Транспорт 21 века — Варшава, Польша, 2004. — с. 389 — 397.
- БапсМк Соготап!;. Токарные инструменты. Каталог С-1000: 2-КШ, 1986.