Сейчас ваша корзина пуста!
Перспективы использования колес повышенной твердости
Цикл статей:
Глава 1 — Совершенствование технологии восстановления колесных пар повышенной твердости
Глава 2 — Перспективы использования колес повышенной твердости
Глава 3 — Теоретическое исследование процесса восстановления профиля катания колесных пар повышенной твердости
Глава 4 — Экспериментальное исследование обрабатываемости бандажной стали повышенной твердости
Глава 5 — Оптимизация процесса восстановления колесных пар повышенной твердости
Глава 6 — Технико-экономическая оценка результатов исследования
В первой главе установлено, что одной из ряда причин повышения износа поверхности катания колесных пар локомотивов и снижение их срока службы является одностороннее увеличение твердости рельсов. В соответствии документом «Стратегическая программа обеспечения устойчивого взаимодействия в системе «колесо-рельс»» поставлена задача повышения ресурса колесных пар локомотивов на первом этапе до 0,6 млн. км. Одним из направлений в комплексе намеченных «Стратегической программой обеспечения устойчивого взаимодействия в системе «колесо-рельс»» мероприятий является повышение твердости бандажей колесных пар локомотивов.
Выполнение этой задачи потребовало оценки соотношения механических свойств колес и рельсов и анализа напряженно-деформированного состояния локомотивных колесных пар при действующих нагрузках на колесо в процессе работы.
О соотношении механических свойств колес и рельсов
Работы последних лет, посвященные проблеме износа гребней колес и боковых поверхностей рельсов в России, касались ряда факторов, предположительно оказывающих влияние на их износ [1] и др. Внедрение лубрикации снизило остроту проблемы, но не устранило причины повышения интенсивности изнашивания колес в последнее десятилетие.
Как известно [2, 3], на поведение экипажа значительное влияние оказывают характеристики сцепления колес с рельсами и упругого скольжения или крипа в зоне контакта колеса и рельса. Важная роль при этом принадлежит свойствам материалов, из которых изготовлены колеса и рельсы. И твердость металла является одним из существенных факторов влияния на износостойкость колес железнодорожного подвижного состава. В исследованиях ВНИИЖТа 1960-80х годов [4, 5] отмечалось, что для равной износостойкости отношение твердости колесного образца к твердости рельсового должно быть не менее 1,2 при проскальзывании до 1 %. Использование этих рекомендаций позволило снизить повреждаемость пары колесо-рельс, имевшую место в конце сороковых — пятидесятых годах (рис. 2.1.).
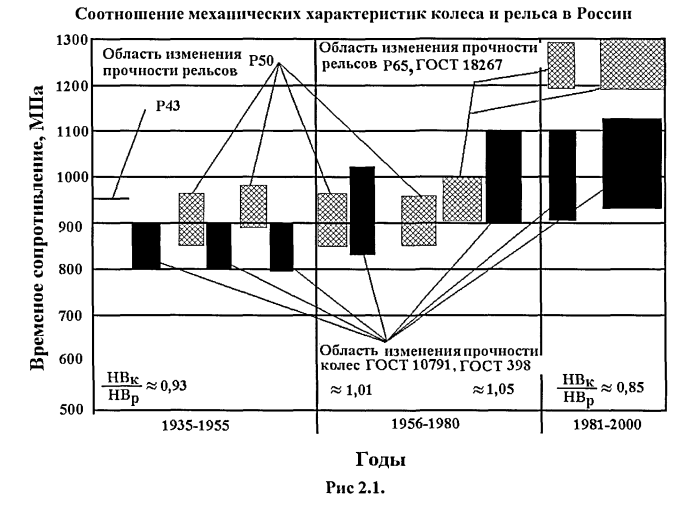
Как показывает современный международный опыт, соотношение механических характеристик колес грузовых вагонов 365-325 НВК и основного типа рельсов 300-330 НВр в США составляет [6, 7] в среднем 1,1. Соотношение предела прочности колес грузовых вагонов Международного союза железных дорог (UIC R7) — сгв =820 -940 МПа и основного типа рельсов (Grade 700) — <тв =680-820М7я составляет в среднем 1,15 (рис. 2.2.).
В настоящее время твердость рельсовой стали по ГОСТ 18267 в среднем составляет 365 единиц НВ, а обода эксплуатирующихся бандажных колес по ГОСТ 398-96 составляет 280 единиц НВ. Внедрение за последнее десятилетие термической обработки рельсов и придание им твердости 341-388 НВ сыграло важную роль для улучшения работы железных дорог. Однако аналогичных мер по колесам предпринято не было. В результате соотношение твердостей колеса и рельса на многих направлениях оказалось меньше единицы. К сожалению, как отмечал Машнев М.М. [8], такой технически революционный «переворот» не получил как должного анализа, так и глубокой технико-экономической оценки. Односторонний же шаг по увеличению твердости рельсов без учета «интереса» колес, действительные возможности материала которых до сих пор раскрыты не полностью, вряд ли можно признать нормальным.
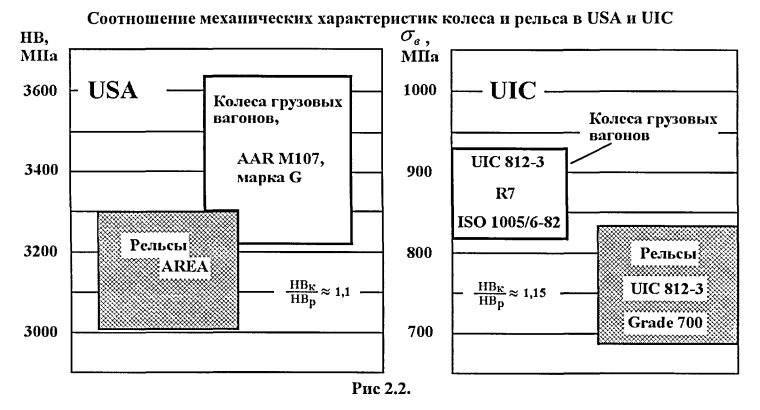
В последних работах ВНИИЖТа в данном направлении [9] исследовалась износостойкость колесных сталей в более широком диапазоне твердостей с различными по величине и направлению проскальзываниями в паре с рельсовыми сталями различной твердости. Отмечается, что с увеличением проскальзывания увеличивается разница в скоростях изнашивания твердых и мягких пар. Был сделан вывод о том, что упрочнение колес и рельсов должно быть дифференцированным: чем выше величина проскальзывания, а это характерно для поверхности гребня, тем большую твердость должна иметь эта поверхность. Повышение твердости поверхности гребня повысит его износостойкость.
Учитывая отсутствие свойства устойчивости невозмущенного движения вагона [10], рост величины поперечного проскальзывания [9, И, 12] пары «колесо-рельс», о чем свидетельствует изменение в последние годы формы износа поверхности обода (значительное снижение доли проката), и повышение интенсивности изнашивания боковых поверхностей рельса и гребня колеса, можно говорить и о несоответствии соотношения НВК / НВр — условиям эксплуатации. К такому же выводу приводят и исследования ВНИИЖТа [4, 9].
Требования определенного минимума твердости — важный критерий износостойкости стали. Однако при повышенной нагрузке на узел трения и необходимости увеличения ресурса пары трения этого недостаточно [13].
Возникает необходимость в дополнительном критерии, характеризующем деформируемость металла: одновременно с высокой твердостью нужен еще некоторый запас пластичности. Так как пластическая деформация при трении приводит к наклепу, то материал может работать в тяжелых условиях на трение, пока не исчерпывается его способность к пластической деформации, иначе говоря, пока сохраняется способность материала претерпевать деформационное упрочнение без разрушения. Таким образом, для оценки износостойкости материала следует принимать во внимание обе характеристики — твердость и запас пластичности. Чем дольше материал способен претерпевать пластическую деформацию без разрушения, тем выше долговечность узла трения. В этой связи следует рассматривать значение таких элементов структуры, как размеры и форма зерен, расположение по границам зерен избыточных фаз, общая однородность и измельченность микроструктуры, распределение фаз, особенно карбидов. Величина повышения твердости поверхностного слоя обода желательна только до НВК =360-^-390. Это связано с тем, что фазовый состав колесной стали представляет собой смесь почти кубической а-фазы с низким содержанием углерода (примерно до 0,1%) и тонкопластинчатых карбидов. Твердость до НВК =360-^390 у этой стали можно получить за счет увеличения дисперсности карбидной фазы, а а- фазу можно поддерживать кубическую. В таком виде а — фаза обладает большой способностью к демпфированию, что уменьшает вероятность образования трещин, отколов и т.д. Дальнейшее повышение твердости колесной стали НВК > 400 может быть осуществлено только за счет получения тетрагональной а-фазы, содержащей повышенное количество углерода (0,1-^0,3%). В таком состоянии а — фаза обладает значительно меньшей демпфирующей способностью. Следовательно, сталь в целом становится более склонной к развитию трещин, к развитию трещин, отколов и т.д. Рассмотрим износостойкость колес при различном соотношении твердости колеса и рельса.
Износостойкость колес при различном соотношении твердости колеса и рельса
Влияние твердости колеса на интенсивность изнашивания исследовалось ВНИИЖТом. Испытанию подвергались образцы диаметром 40 мм с проскальзыванием 10% [5]. В ходе эксперимента установлено, что увеличение твердости колесной стали с 310 до 360 НВ приводит к снижению износа с 0,8 до 0,3 г., т.е. увеличение твердости колесной стали на 1НВ снижает износ на 1%.
Практически аналогичные данные по материалам «Сумитомо металс» были получены при испытании образцов диаметром 30 мм из стали твердостью 310 -360 НВ (колеса НТ — для повышенных нагрузок) при испытаниях в условиях качения с проскальзыванием 10%; износ этих образцов меньше на 33% по сравнению с образцами из стали 8ТУ-80 твердостью 300 — 330 НВ (серийные колеса).
Таким образом, все исследователи отмечают одну и ту же закономерность: увеличение твердости колес на 1НВ в эксплуатационном интервале твердостей увеличивает износостойкость на 1% [14].
При этом, как отмечают выше указанные исследователи, увеличение твердости колес с 250 до 400 НВ практически не влияет на интенсивность изнашивания и контактную долговечность рельсов, а контактно-усталостная долговечность колес возрастает пропорционально квадрату приращения их твердости.
В связи со всем выше изложенным резонно поставить вопрос: Каково же должно быть соотношение между твердостями колеса и рельса (НВК и НВ,,), обеспечивающее минимизацию интенсивностей изнашивания колес и рельсов?
Т.В. Лариным были выполнены исследования [4] на машинах трения МИ — 1 и МИ — 3 с использованием образцов из рельсовой и колесной сталей (рис. 2.3).
По результатам этих исследований сделаны следующие выводы: 1. В условиях трения качения с проскальзыванием по принятой схеме интенсивность нарастания износа элементов пары трения неодинакова и обуславливается соотношением их твердости. С повышением твердости одного элемента износостойкость его повышается при условии понижения твердости другого элемента пары. Для равной износостойкости элементов отношение твердости колесного образца к твердости рельсового должно быть не менее 1,22. Величина проскальзывания зависит от твердости элементов пары: с повышением ее проскальзывание сначала повышается, а затем уменьшается. В парах с постоянной твердостью колесных образцов проскальзывание уменьшается с понижением твердости рельсовых образцов.
- Интенсивность нарастания износа элементов пары трения находится в прямой зависимости от величины проскальзывания до твердости колесных образцов 425 НВ.
- Наибольшая сопротивляемость истиранию наблюдается при повышении твердости образцов до 330-340 НВ. Далее спад кривой зависимости износа от твердости протекает менее активно и остается почти на одном уровне.
Дальнейшие исследования ВНИИЖТа в этом направлении [14] и др. привели к выделению одиннадцати основных (первичных) факторов, влияющих на скорость изнашивания колес
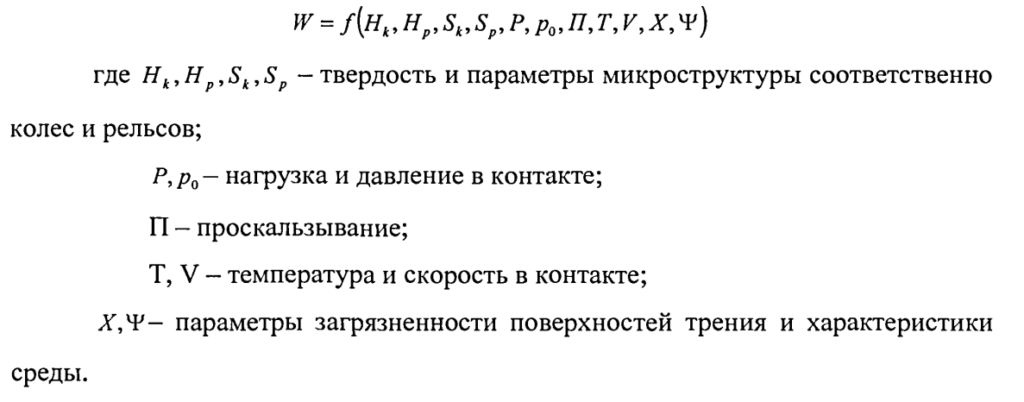
В работе [14] рассматривается влияние твердости колесной стали на износостойкость, но в более широком диапазоне твердостей. При этом отмечается, что данные, получаемые в эксплуатации, достоверны только при очень небольшом отклонении твердостей от среднесетевых. Между тем основные параметры этой системы — нагрузки, проскальзывания, свойства колесной и рельсовой стали, интенсивность движения, параметры окружающей среды колеблются в очень широких пределах. Локальное изменение любого из этих параметров выводит всю систему из равновесия и делает ее реакцию непредсказуемой. Закалка небольшой партии колес или рельсов равносильна закалке одного зуба у шестерни и может привести к результатам, обратным ожидаемым. Достоверные результаты можно получить только после полной замены колес на всей сети. Например, ранее предпринимались попытки поверхностной закалки небольших партий колес с применением плазменного нагрева и нагрева ТВЧ. Результаты эксплуатационных испытаний этих колес были отрицательными [15]. Как было показано далее, этого и следовало ожидать, поскольку необходимо изменять твердость не только колес, но и рельсов, причем дифференцированно по их ширине с учетом величин проскальзывания, давления и других условий эксплуатации. При этом значение комплексного лабораторного эксперимента, позволяющего учесть все эти условия, очень велико — он становится практически единственным инструментом исследования в этой области.
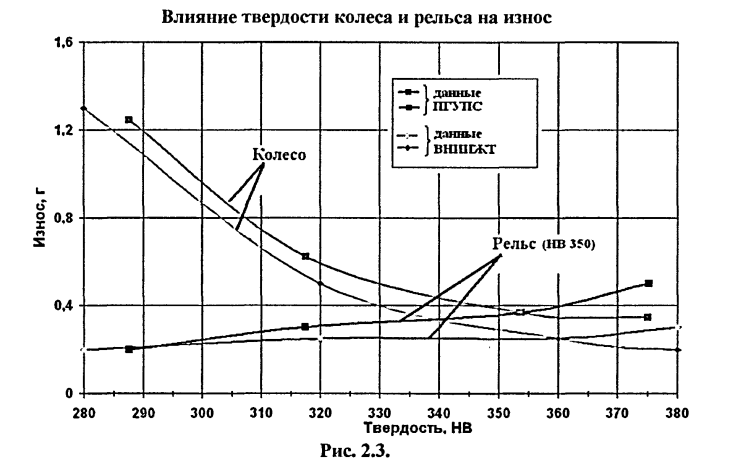
Эксперименты, кафедры «Технология металлов» ПГУПС (рис. 2.3), по оценке износостойкости этой пары материалов при проскальзывании 10% показа ли, что снижение суммарной скорости изнашивания достигалось при увеличении твердости образца из колесной стали до твердости рельсового (НВр = Збо) и выше
(НВК =380-390).
По данным [13] в табл. 2.1. и 2.2. приведены результаты влияния на износ разной степени проскальзывания и соотношение твердостей колес и рельсов.
Отечественный и мировой опыт говорит о том, что никакого волшебного соотношения между твердостью рельсов и колес не существует, а есть оптимальная твердость для рельсов и колес, определяемая рядом факторов. Оптимальной твердостью и для рельсов, и для колес, страдающих от процессов контактной усталости и износа, является 370-400 НВ. Формально соотношение значений их твердости близко к единице, но, если попытаться эксплуатировать колеса и рельсы с одинаковой твердостью порядка 200-250 НВ при существующих осевых нагрузках, ничего хорошего на получиться из-за явно недостаточного сопротивления смятию, контактной усталости и износу.
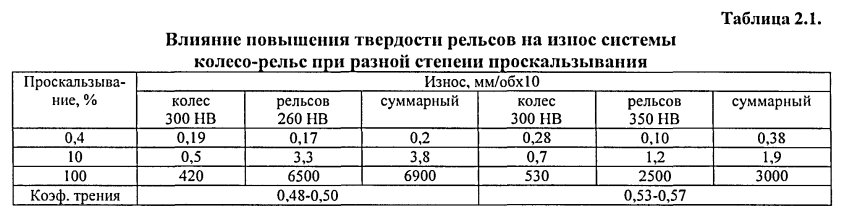
Таким образом в работе [13] также высказывается необходимость повышения твердости обода колеса до НВ 400. Вместе с другими мероприятиями по «Стратегической программе обеспечения устойчивого взаимодействия в системе «колесо-рельс»» повышение твердости бандажных колес позволит увеличить их ресурс до 0,6 млн. км на первом этапе. Подобные работы уже ведутся для вагонных колес из сталей ГОСТ 10791.
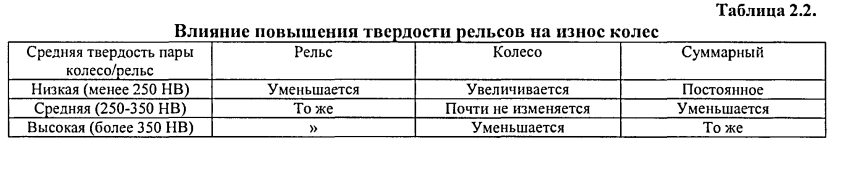
На рис. 2.3. представлены данные по соотношению твердости колес и рельсов при проскальзывании 10 % по данным ПГУПС и ВНИИЖТ. Из анализа рис. 2.3. видно, что твердость колесной стали должна составлять примерно 360-370 НВ.
Для определения общей картины взаимодействия колеса и рельса необходимо провести анализ напряженного состояния колес повышенной твердости.
Расчет и анализ напряженного состояния колес повышенной твердости
Для оценки общего напряженного состояния в паре колесо-рельс достаточно решить задачу Герца для одноточечного контакта профилей ДМеТИ и ГОСТ.
Построение математической модели процессов возникновения деформаций и напряжений в колесе при действии на него вертикальных и боковых нагрузок производилось на основе метода конечных элементов [16 — 23].
Основные положения для расчета напряжений в колесе методом конечных элементов [24]:
- сечение колеса разбивается на определенное количество элементов;
- элементы соединяются между собой в узлах. Перемещения узлов неизвестны;
- устанавливаются функции, однозначно определяющие перемещения точек внутри элементов в зависимости от перемещения узлов;
- функции перемещения точек элементов определяют однозначно деформации внутри элементов в зависимости от перемещения узлов. Деформации внутри элементов, с учетом соответствующих физических соотношений, определяют напряженное состояние в каждом элементе и на его границах. Ниже приведена краткая методика расчета.
Для разработки конечно-элементных моделей колеса и рельса в программных комплексах ANSYS и Cosmos Works использовались объемные 20-ти узловые параболические конечные элементы, которые подходят для моделирования нерегулярной сетки конечных элементов. Используемые для расчета конечные элементы имеют квадратичную функцию формы, что позволило с высокой точностью определить напряжения, возникающие в элементах колеса (особенно в зонах концентрации напряжений). Используемый конечный элемент имеет три степени свободы в каждом узле (перемещения вдоль осей х, у, т). Элемент поддерживает пластичность, гиперэластичность, ползучесть, большие деформации и др. Геометрия элемента показана на рис. 2.4.
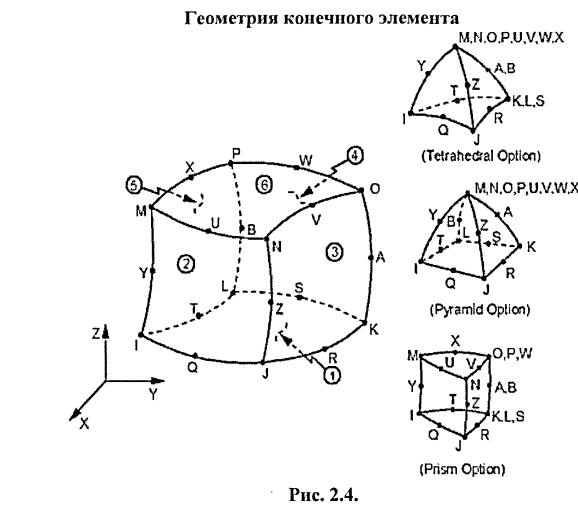
Для построения математической модели напряженно-деформированного состояния колеса воспользовались прямым методом жесткости. В глобальной декартовой системе координат производилось разбиение колесной пары на гексоэд- ральные конечные элементы. При этом колесная пара опирается на рельсы. В связи с чем решали контактную задачу теории упругости.
Решение данной задачи теории упругости производится с помощью минимизации интегральной величины, связанной с работой напряжений и внешней приложенной нагрузки. Так как данная задача решается в напряжениях с заданными на границе усилиями, то нужно минимизировать дополнительную работу системы. Формулировка метода конечных элементов предполагает отыскание поля перемещений и тем самым связана с минимизацией потенциальной энергии системы при отыскании узловых значений вектора перемещений. После того как перемещения будут определены, можно вычислить компоненты тензоров деформаций и напряжений.
Полная потенциальная энергия упругой системы может быть разделена на две части, одна из которых соответствует энергии деформаций в теле, а другая определяется потенциальной энергией массовых сил и приложенных поверхностных сил. В соответствии с этим запишем полную потенциальную энергию в виде:
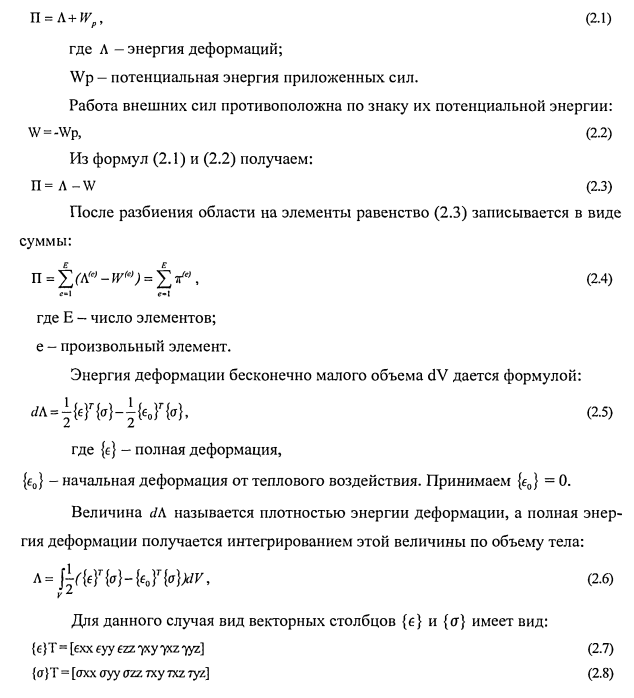
В основе курса теории упругости [24] лежат два соотношения: закон Гука, который связывает компоненты тензоров напряжений и деформаций, и соотношения связи между деформациями и перемещениями. Закон Гука в общей форме имеет вид:
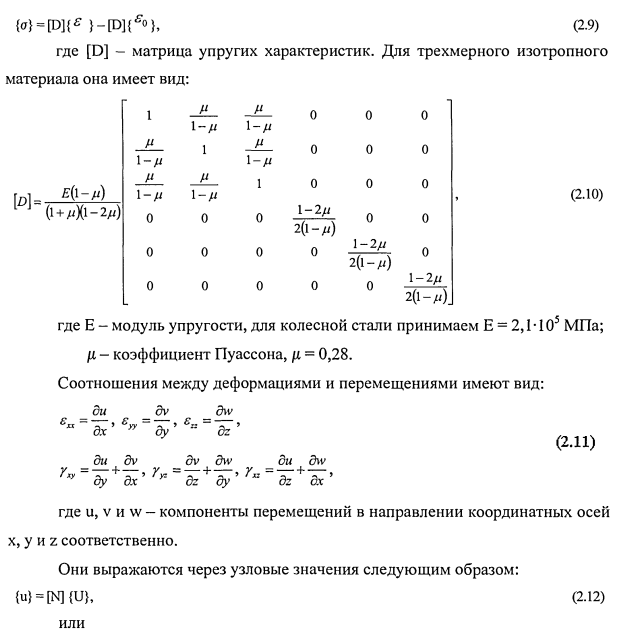
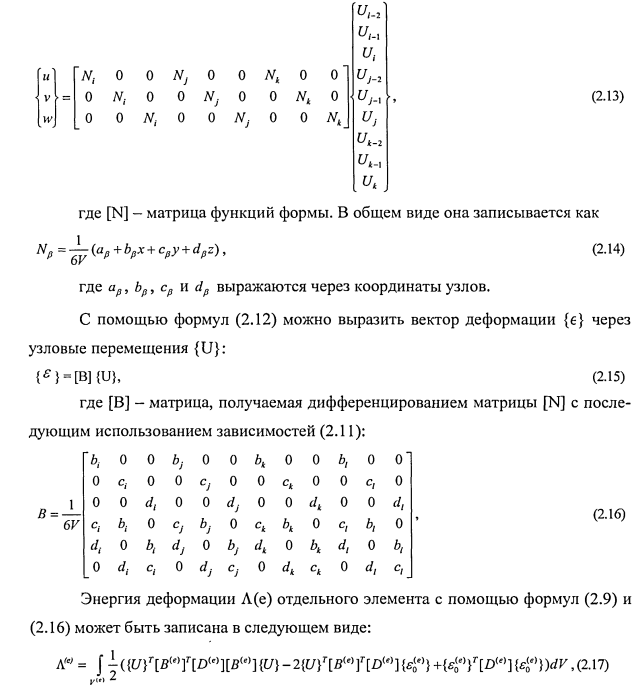
Последнее слагаемое в (2.17) не зависит от узловых значений {и}, поэтому оно не влияет на процесс минимизации и в дальнейшем не будет приниматься во внимание.
Работа, совершаемая внешними силами, может быть разделена на три различные части: работа \Ус, совершаемая сосредоточенными силами, работа \Ур,
которая получается в результате действия компонент напряжений на внешней стороне поверхности, работа совершаемая массовыми силами. Работу сосредоточенных сил легко определить, если в каждой точке приложения сосредоточенной силы поместить узел. Работа сосредоточенной силы равна произведению величины этой силы на длину пути, на котором эта сила действует. Таким образом, работа отдельной силы равна Р-и. Обозначая узловые силы через {Р}, а узловые перемещения через {и}, совершенную работу можно записать в виде произведения матриц:
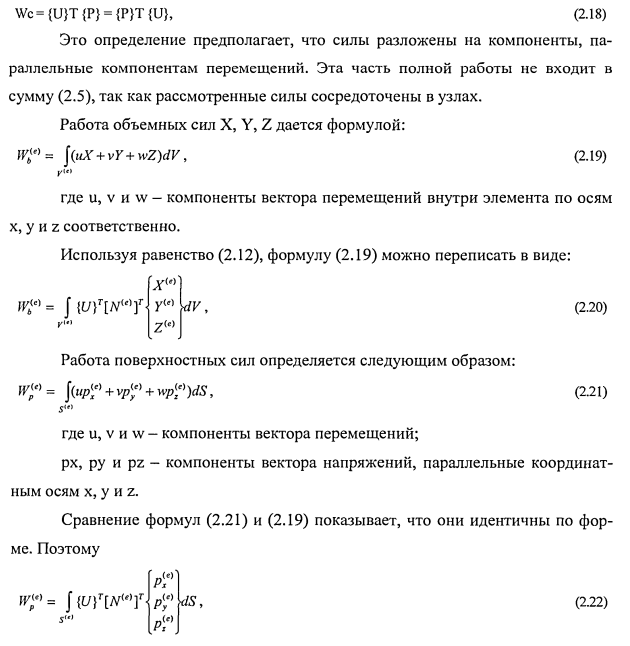
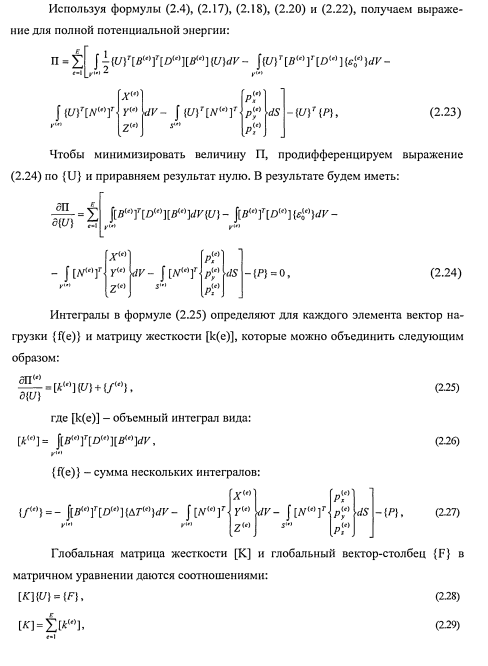
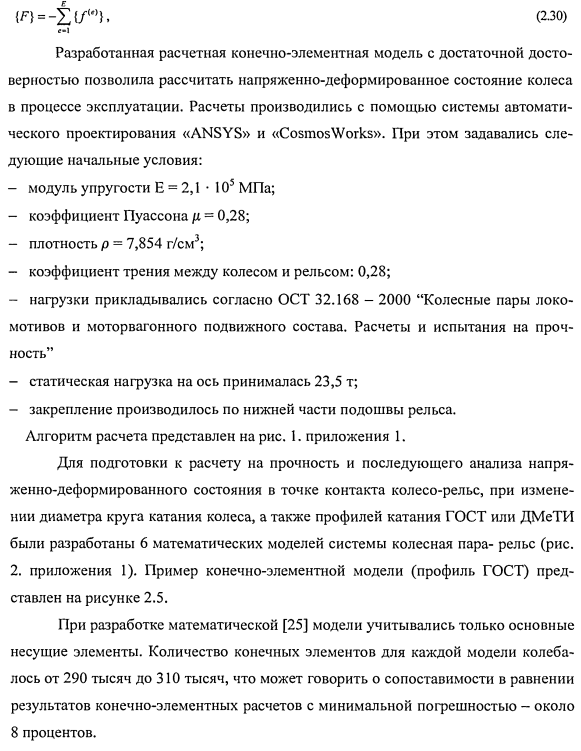
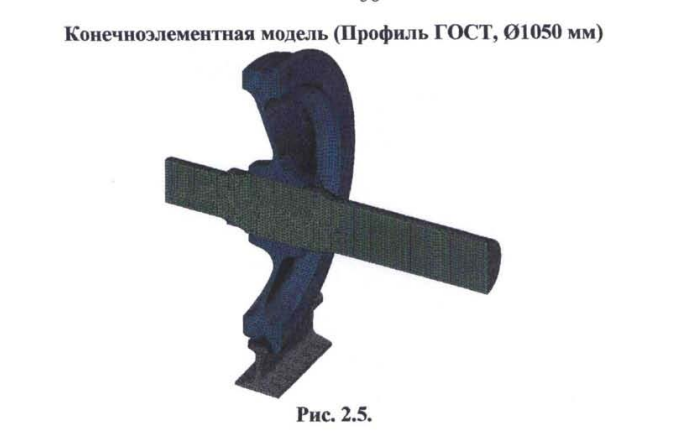
Результаты расчета моделей колесной пары представлены на рис. 3-5 приложения 1.
Из анализа результатов расчетов моделей колеса и рельса следует, что: 1. Наибольшие эквивалентные напряжения возникают в модели 1 (ГОСТ диаметр по кругу катания 950 мм) и составляют 720 МПа. Наименьшие эквивалентные напряжения возникают в модели 6 (ДМеТИ диаметр по кругу катания 1250 мм) и составляют 595 МПа. Максимальные эквивалентные напряжения, возникающие в модели, представлены на рис. 2.6.
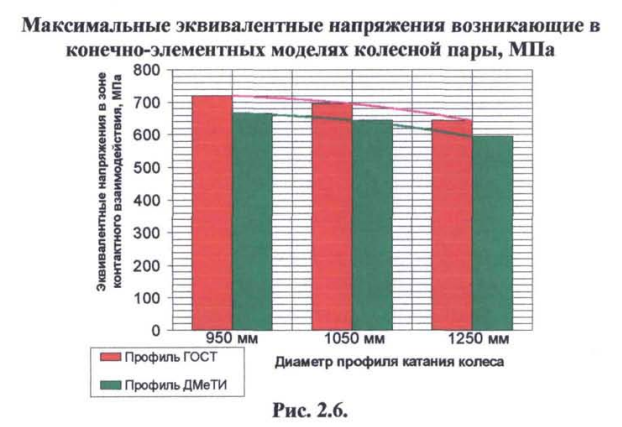
Разница, в процентах, между величинами эквивалентных напряжений колес с профилем ГОСТ и с профилем ДМеТИ представлены на рис. 2.7. и со-ставляет в среднем 7 процентов.
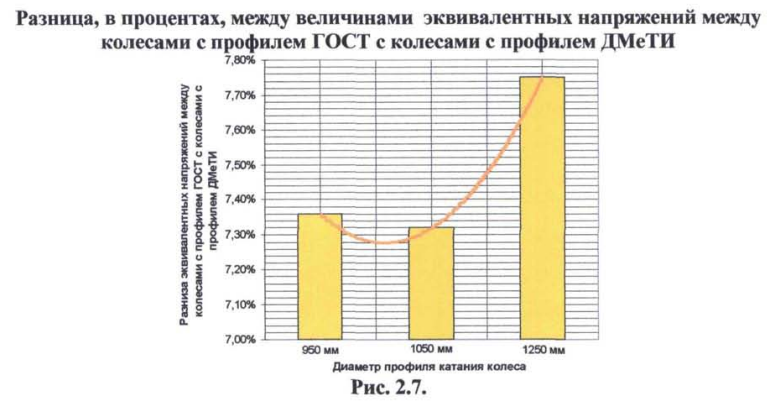
При увеличении диаметра круга катания колеса, величины эквивалентных напряжений возникающих в контакте снижаются на 5-12 процентов.
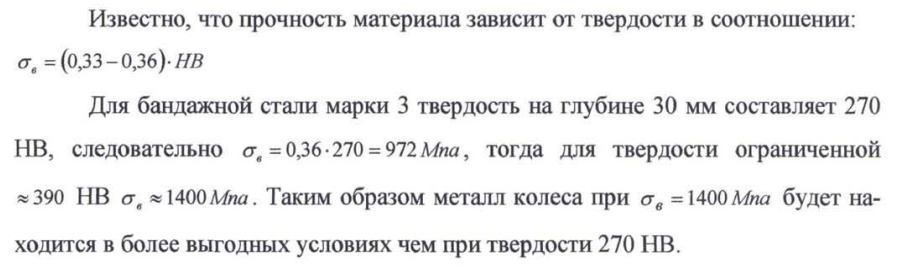
Влияние механических свойств колеса на его ресурс
Как показали экспериментальные исследования (рис.2.3.) и литературные данные [4, 5, 13] и др. при повышении твердости колесной (бандажной) стали по ГОСТ 398 — 96 (табл. 2.3.) возрастает ее износостойкость (п.2.2.), а также допускаемые напряжения (п.2.3.) в более прочном ободе.
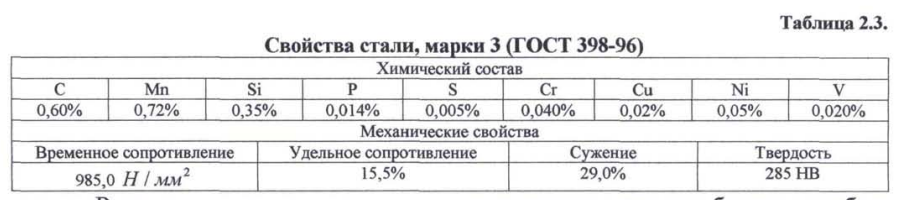
Рассмотрим качественную схему использования ресурса бандажа изображенную на рис. 1.11., которую с учетом полученных данных (рис.2.3.) и [25] можно представить в следующем виде (рис. 2.8.).
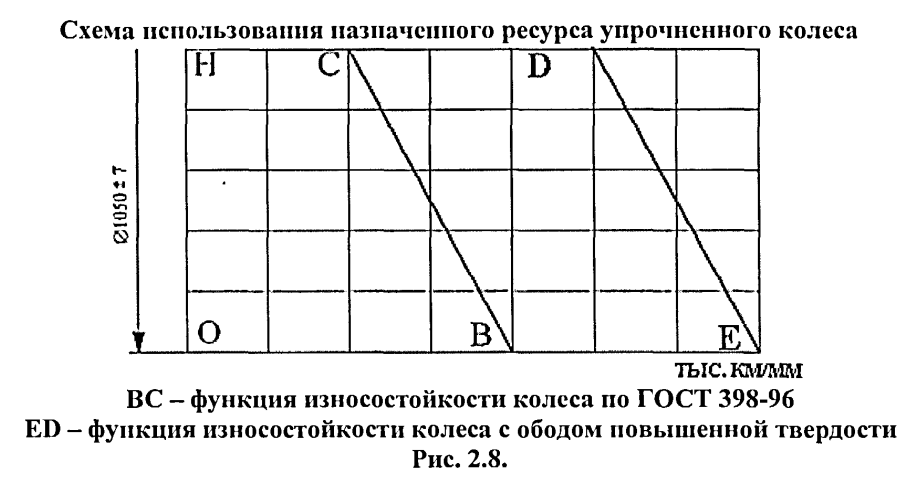
По первым результатам эксплуатации вагонных колес с ободом повышенной прочности [26], отмечается увеличение их износостойкости и меньшая повреждаемость дефектами. Сейчас находится в эксплуатации около 400 тыс. колес. Предположив повышение износостойкости упрочненных колес на 75% получим соответствующее повышение ресурса колеса. Кафедрой «Технология металлов» ПГУПС проводились эксперименты [25] по оценке износостойкости колесной стали повышенной твердости на магистральном, повышенном транспорте и в метрополитене. После термообработки ТВЧ поверхности катания колес до твердости 320-360 НВ износостойкость возросла на 30-г 50% по сравнению с твердостью 270-280 НВ. Учитывая предполагаемое повышение твердости до 360 НВ, можно предположить рост износостойкости более 75 %.
Выводы по главе 2
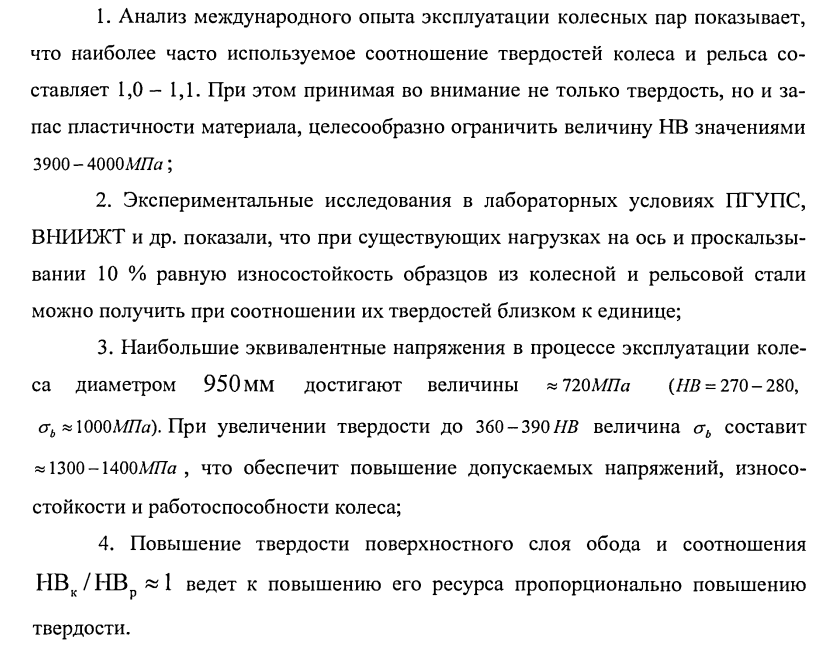
Список литературы
- Проблемы износа колес и рельсов. Возможные пути борьбы /В.М. Богданов, Ю.А. Евдокимов и др.// Железнодорожный транспорт. 1996. №12, с.30-31.
- Лазарян В.А. Динамика вагонов. М.: изд. Транспорт, 1964. 256 с.
- Гарг В.К., Дуккипати. Динамика подвижного состава: Пер. с англ./Под ред H.A. Панькина. — М.: Транспорт, 1988. — 391 с.
- Ларин Т.В. Об оптимальной твердости элементов пары трения «колесо — рельс» // Вестник ВНИИЖТ, 1965. №3. с.5-9.
- Вихрова A.M. и др. О соотношении твердости рельсовой и колесной стали/А.М. Вихрова, Т.В. Ларин, и др. // Вестник ВНИИЖТ, 1983, №6. — с. 34-38.
- Пашолок И.А., Цюренко В.Н., Самохин E.H. Повышение твердости колес // Железнодорожный транспорт. 1999. №7. с. 40-43.
- Воробьев А. А., Сорокин П. Г. О методике оценки соотношения твердости пары колесо-рельс // Совершенствование конструкции локомотивов и системы их об-служивания. Межвузовский сборник научных трудов., 2004 г. СПб. с. 171-176.
- Машнев М.М. Работоспособность и ресурс подвижного состава // Железнодо-рожный транспорт. — 1993. №1. с.43-46.
- Марков Д.П. Трибологические аспекты износостойкости и контактно- усталостной выносливости колес подвижного состава: Автореферат дис. на соиск. д.т.н.-М.: ВНИИЖТ. 1997. 51 с.
- Кошелев В. А., Челнокова Л.И. Устойчивость движения вагона и износ рабо¬чих поверхностей колес и рельсов // Конструкционно-технологическое обеспече¬ние надежности подвижного состава: Сб. науч. тр. — СПб.: ПТУ ПС, 1994 — с. 39-41.
И. Неглинский В.В. Обобщение результатов эксплуатационных наблюдений за изнашиванием реборд колесных пар локомотивов // Трение и износ. Том 16. 1995. № 1, с. 119-125. - Пашолок И.А., Харитонов В.Б. О возможном повышении износостойкости железнодорожных колес // Вестник ВНИЖТ. 1997. №1. — с. 32-36.
- Шур Е. А. К вопросу об оптимальном соотношении твердости рельсов и колес //Современные проблемы взаимодействия подвижного состава и пути: Материалы научно-практической конференции/ ВНИИЖТ. — М., 2003. с. 87-93.
- Марков Д.П. Повышение твердости колес подвижного состава. // Вестник ВНИИЖТ. 1995. №3. с. 10 — 17.
- Ларин Т.В. Износ и пути продления службы бандажей железнодорожных ко-лес/М.: Трансжелдориздат. 1958. 168 с.
- К. L. Johnson. Contact Mechanics. Cambridge University Press, 1985. P. 427.
- J. Kalousek, E. Magel, S. Grassie. Perspective on Metallurgy and Contact Mechan¬ics. Proceedings of IHHA’99 STS-Conference on Wheel/Rail Interface. Moscow, 1999, p. 175 — 186.
- S. Grassie, J. Kalousek. Rolling Contact Fatigue of Rails: Characteristics, Causes and Treatments. Proceedings of the 6th IHHA Conference. Capetown, 1997, p. 381 — 404.
- Сегерлинд JI. Применение метода конечных элементов. М.: Мир, 1979, 388 с.
- Ефимов Ю.Н., Сапожников Л.Б., Троицкий А.П. Реализация метода конечных элементов на ЭВМ для решения плоской задачи теории упругости // Известия ВНИИГ, 1970, т.93, с.17 — 46.
- Розин Л.А. Метод конечных элементов. Л.: Энергия, 1971, 214 с.
- Есаулов В. П., Сладковский A.B. Применение полуаналитического МКЭ к расчету тел вращения под действием несимметрической нагрузки. Деп. в Укр. ЦИНТИ 02.01.89-№14-4к89, 18с.
- Галлагер Р. Метод конечных элементов М.: Мир, 1984, 428 с.
- Тимошенко С. П., Гульдер Дж. Теория упругости. М.: Наука, 1975.
- Восстановление профиля поверхности катания колесных пар / И.А. Иванов, М. Ситаж, А.Ф. Богданов; Под ред. д-ра техн. наук И.А. Иванова. — СПб: Петербург¬ский Государственный Университет Путей Сообщения, 2000. — 127.
- Воробьев А. А., Сорокин П. Г Исследование напряженного состояния пятна контакта колеса и рельса // Новые материалы и технологии в машиностроении. Сборник научных трудов / Выпуск 3. — Брянск: БГИТА, 2004-с.8-18.
- Пашалок И.Л., Филиппов Г.А., Шишов A.A. Колеса с повышенной твердостью обода производства ОАО «ВМЗ» //Современные проблемы взаимодействия под-вижного состава и пути: Материалы научно-практической конференции/ ВНИ- ИЖТ.-М., 2003. с. 87-93.