Сейчас ваша корзина пуста!
Оптимизация процесса восстановления колесных пар повышенной твердости
Цикл статей:
Глава 1 — Совершенствование технологии восстановления колесных пар повышенной твердости
Глава 2 — Перспективы использования колес повышенной твердости
Глава 3 — Теоретическое исследование процесса восстановления профиля катания колесных пар повышенной твердости
Глава 4 — Экспериментальное исследование обрабатываемости бандажной стали повышенной твердости
Глава 5 — Оптимизация процесса восстановления колесных пар повышенной твердости
Глава 6 — Технико-экономическая оценка результатов исследования
Результаты расчета оптимальных режимов восстановления колесных пар при различной производительности
Анализ режимов резания при обточке колесных пар в конкретных производственных условиях [1] позволил установить, что действительные режимы в большинстве случаев отличаются от тех, которые рекомендуются различными справочными данными [2, 3]. В связи с предполагаемым повышением твердости бандажей возникала необходимость в разработке методики расчета режимов и параметров процесса обработки колесных пар и определения их оптимальных значений.
Используя программу, которая позволяет рассчитать оптимальные режимы резания в соответствии с зависимостями, представленными в гл. 3., были произведены расчеты, результаты которых представлены на рис. 5.1. — 5.5. и на рис. 1 — 3 приложения 3.
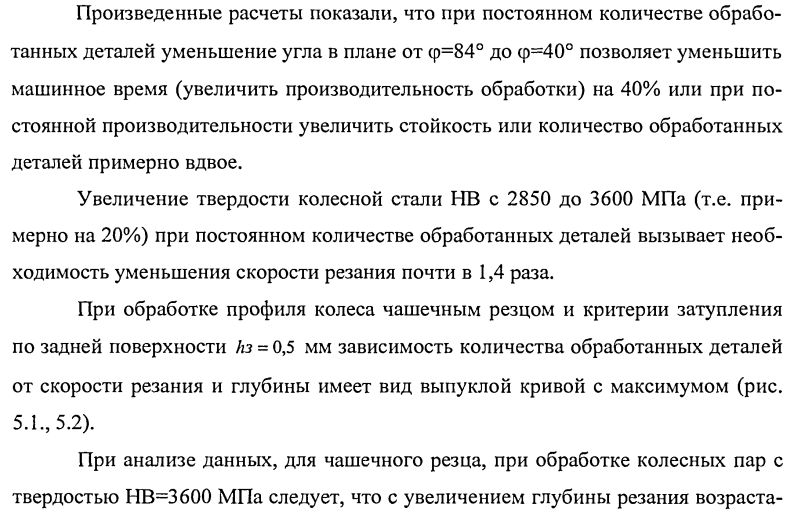
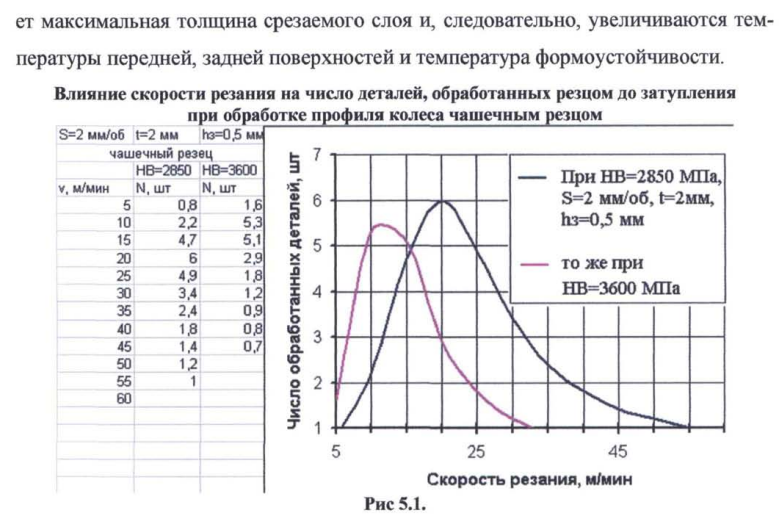
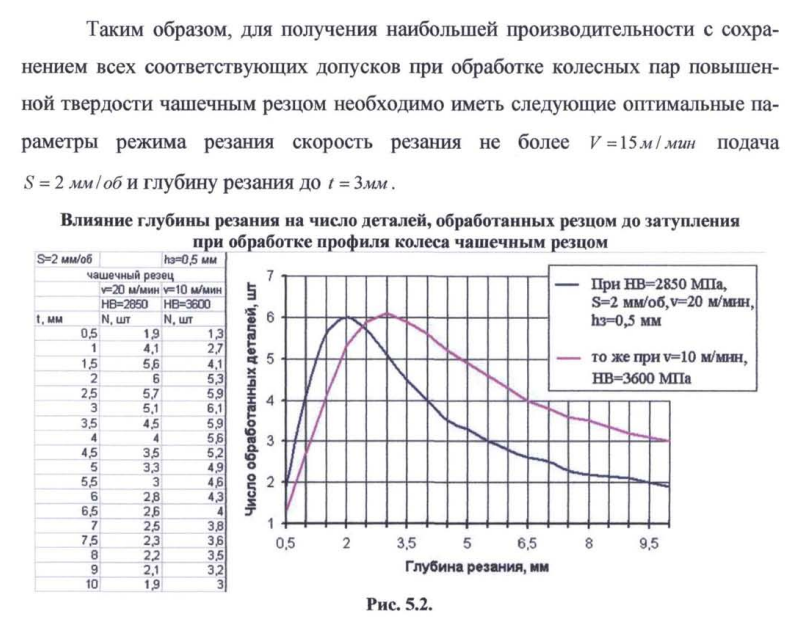
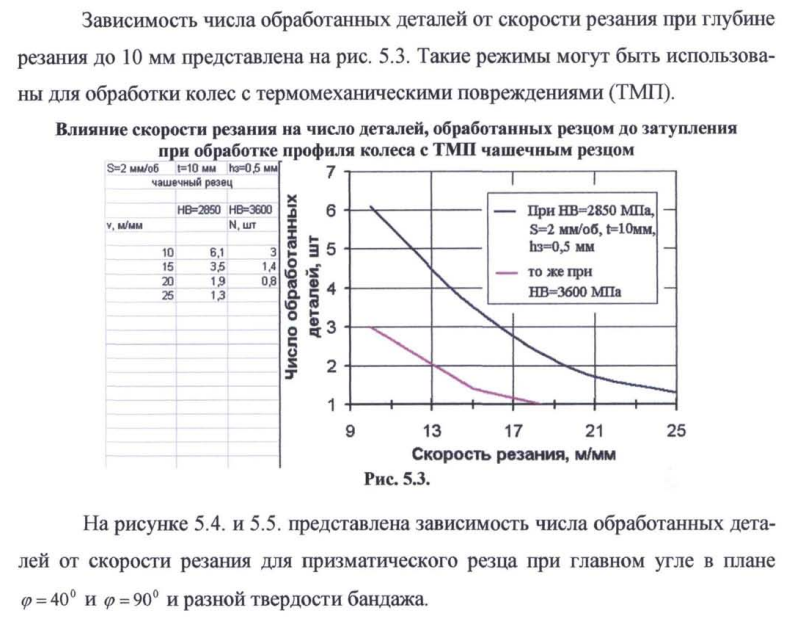
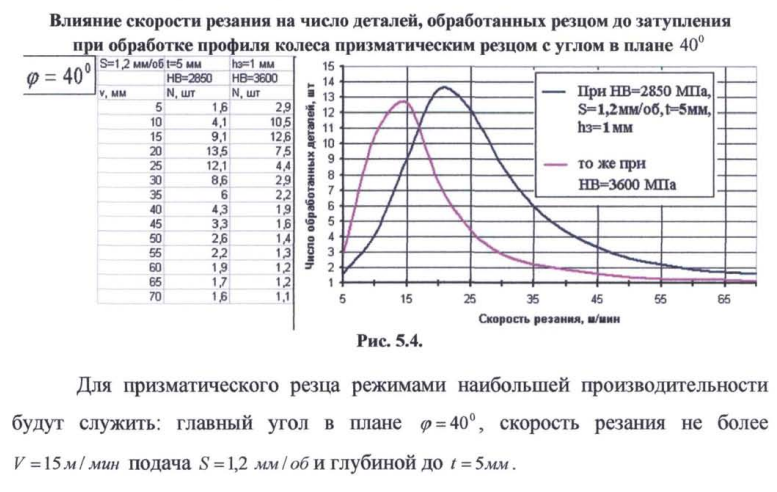
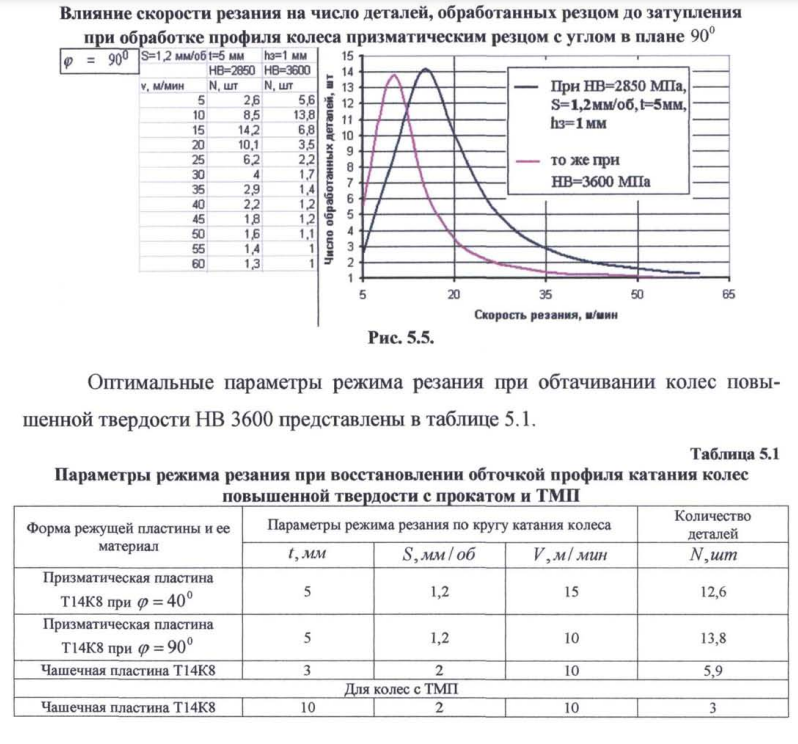
Рациональные геометрические параметры режущего инструмента
При обработке колес с дефектами в виде вертикального подреза гребня и термомеханических повреждения припуск на обработку, может достигать 2025мм. Поскольку длина призматической режущей пластины обычно равна 30 мм, действительный угол в плане при этом должен быть немного менее или равен 90°. Учитывая, что одна часть профиля обрабатываемой поверхности наклонена под углом 6°, а другая под углом около 16°, статический угол в плане (по отношению к оси вращения колеса) может быть принят равным 90° (рис.5.6). Радиус при вершине обычно у стандартных пластин принимают равным 4 мм. Однако, учитывая, что ширина пластины равна 12 мм, радиус при вершине может быть увеличен до 6 мм. Увеличение радиуса закругления вершины должно привести к уменьшению неравномерности изнашивания и за счет этого благоприятно сказаться на повышении стойкости инструмента.
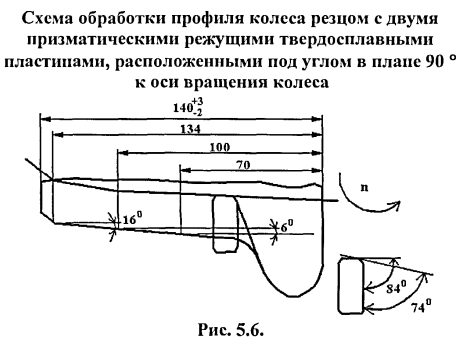
Угол X наклона режущей кромки для черновой обработки желательно задать равным около 5-6°.
Форма передней поверхности у стандартных пластин обычно выполнена в виде плоской поверхности с отрицательным передним углом и стружкозавивающим порожком (рис. 5.7.). Однако при меньших скоростях резания для обработки колес с повышенной твердостью более предпочтительна форма передней поверхности с положительным передним углом, с упрочняющей фаской, расположенной под отрицательным передним углом и со стружкозавивающей плоскостью (рис.5.7.).
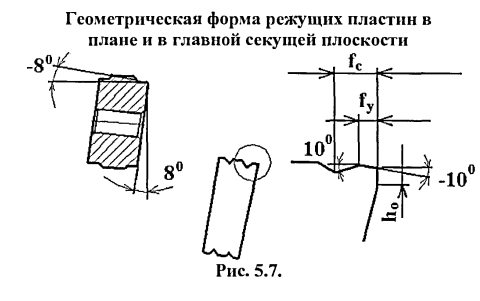
В этом случае целесообразно также предварительно затачивать фаску на задней поверхности шириной 0,2 — 0,3 мм с целью упрочнения режущего клина и уменьшения пластических деформаций в начальный период резания.
Эти данные получены на основе эксперимента и теоретических расчетов.
Модель оптимизации процесса восстановления колесных пар
При разработке модели немаловажную роль играет выбор критерия оптимизации [4-6], то есть параметра, по которому будет производиться оценка процесса резания. Критерий и выражающая его целевая функция должны обеспечить при проектировании технологического процесса или операции наименьшие затраты при максимально возможной при этом производительности или заданное количество обрабатываемых деталей [7-11].
В то же время нестабильность характеристик обрабатываемого материала, режущего инструмента, оборудования и др. и их изменение в процессе обработки приводят при работе с заранее запрограммированным режимом к неконтролируемым колебаниям тепловой и силовой нагрузок на инструмент, что резко снижает его стойкость и надежность. По этой причине детерминированный подход к оптимизации не может дать надежных результатов.
Повышение производительности обработки, эффективности использования инструмента, оборудования по обработке колес при изготовлении и ремонте может быть достигнуто путем стабилизации температурного режима обработки [12]. Для каждого сочетания параметров процесса восстановления можно обеспечить оптимальную температуру формоустойчивости, при которой будут достигнуты наибольшая стойкость инструмента и наименьший износ. Оптимальная температура формоустойчивости соответствует наиболее благоприятным условиям трения и изнашивания инструмента по контактным поверхностям.
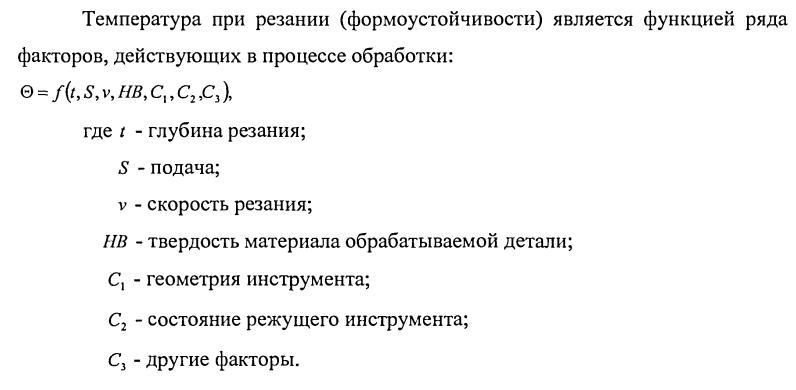
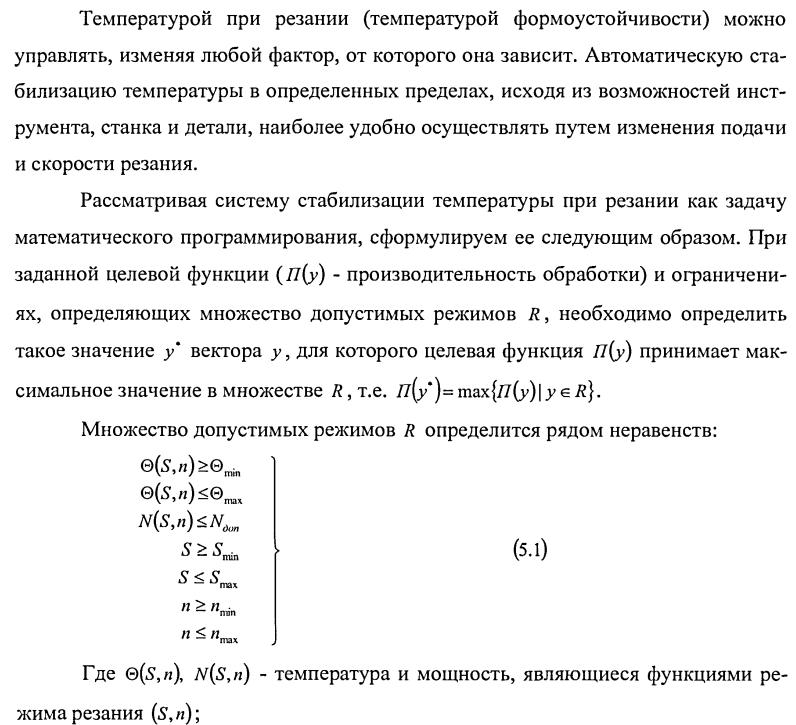
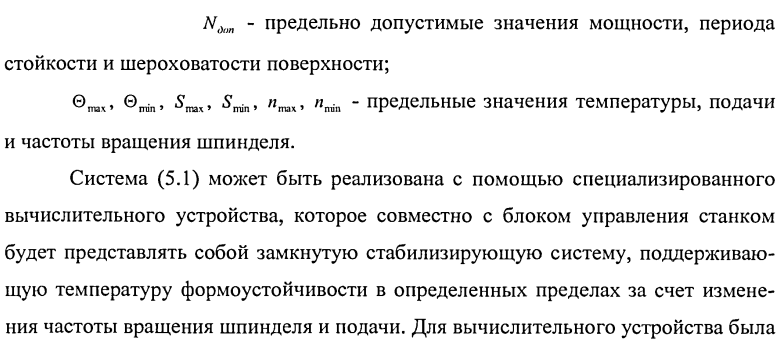
разработана прикладная программа позволяющая регулировать подачу и обороты станка при изменении температуры формоустойчивости.
Рассматривая конкретно возможности регулирования температуры на станках, используемых для изготовления колес на металлургических предприятиях (1Б502, 1Д502) и для ремонта на линейных предприятиях ОАО РЖД (1836А, ИВВ112 и др.), следует отметить, что на этих станках обработка колеса ведется одновременно несколькими суппортами. В каждый момент времени условия работы инструмента на разных суппортах отличаются друг от друга. И регулирование температуры для условий работы каждого суппорта по частоте вращения шпинделя может потребовать разных значений этой величины одновременно. При восстановлении профиля поверхности катания на колесотокарных станках 1836А, ИВВ 112 и др. та же картина: условия работы резцов правого и левого суппортов различны, т.е. для многоинструментной обработки более целесообразно регулирование температуры только за счет изменения подачи каждого суппорта. В этом случае схема системы стабилизации температуры в процессе резания значительно упрощается и не представляет особых сложностей для реализации.
Создание и внедрение адаптивной системы резания для обработки колес подвижного состава, стабилизирующей температуру формоустойчивости, позволит улучшить эффективность использования инструмента за счет повышения его стойкости и снижения износа, повысить равномерность нагрузки обрабатывающей системы, а также точность и производительность обработки.
На базе кафедры «Технология металлов» ПГУПС была разработана система управления процессом для обработки колесных пар без выкатки из-под ТПС [13]. Целью использования системы являлось повышение качества обработки поверхности катания обода колеса и увеличение срока службы инструмента за счет изменения режимов и условий резания посредством корректировки температуры резания, а следовательно и температуры формоустойчивости резца. Одна из управляющих цепей системы подключена к электродвигателю постоянного тока привода вращения колесной пары для регулирования его скоростного режима. За- датчик необходимой скорости вращения колесной пары и два суппорта с приводами, электрически соединены с системой управления станком, при этом электропривод вращения колесной пары жестко связан с колесной парой. Блок сравнения, один вход которого соединен с датчиком фактической скорости вращения колесной пары (датчиком фактической скорости может служить блок боксования стандартной электрической схемы, например тепловоза ТЭМ 7 [14- 16]), другим входом соединен с задатчиком необходимой скорости вращения колесной пары. Выход блока сравнения подключен через систему управления станком к ее цепи управления электроприводом вращения колесной пары. Датчики температуры, установлены на резцах, а выходы датчиков температуры подключены соответственно к третьему и четвертому входам блока сравнения.
Таким образом полученные результаты показали, что применяемые в настоящее время режимы восстановления профиля не целесообразны для использования и ведут к увеличению расхода дорогостоящего режущего инструмента. Рекомендуемые режимы обеспечивают рациональный расход режущего инструмента при снижении производительности применяемого оборудования. Повышение производительности можно обеспечить за счет использования новых методов обработки, например, силового шлифования.
Выводы по главе 5
- Установлены области существования оптимальных сочетаний параметров режимов восстановления колес с различной твердостью обода для чашечного
и призматической режущих пластин; - Предложены рациональные геометрические параметры режущего инст-румента для восстановления колесных пар повышенной твердости;
- Обоснована необходимость разработки системы автоматического регу-лирования по температуре формоустойчивости процесса восстановления профиля поверхности катания колесных пар. Одной из основных причин, затрудняющих рациональное использование оборудования, инструмента и оптимизацию процес¬са восстановления профиля колес, является его нестационарность. Она обуслов¬лена изменяющейся в широких пределах твердостью (выщербины, ползуны) и глубиной резания (износы гребня, фасонный профиль);
- Разработана система управления процессом восстановления колес по температуре формоустойчивости для станков, используемых при обработки колес без выкатки из под ТПС. На систему получено а. с. на полезную модель.
Список использованной литературы
- Восстановление профиля поверхности катания колесных пар / И.А. Иванов, М. Ситаж, А.Ф. Богданов; Под ред. д-ра техн. наук И.А. Иванова. — СПб: Петербург¬ский Государственный Университет Путей Сообщения, 2000. — 127 с.
- Барановский Ю.В. Режимы резания металлов. — М.: Машиностроение, 1970.
- Sandvik Coromant. Токарные инструменты. Каталог С-1000: 2-RUS, 1986.
- Горанский Г.К. Расчет режимов резания при помощи электронно- вычислительных машин. — Минск: Гос. Изд-во БССР, 1963. 192 с.
- Иванов И.А. Выбор оптимальных режимов резания при точении.: — Л.: ЛИИЖТ, 1969.-26 с.
- Иванов И.А. Повышение производительности колесных цехов ремонтных предприятий путем оптимизации режимов резания и обеспечения надежного стружкоотвода: Дис. канд. техн. наук. — Ростов на Дону: РИИЖТ, 1966. — 193 с.
- Шубин А. А. Оптимизация процесса восстановления профиля поверхности ка¬тания вагонных колесных пар. Дисс. на соиск. уч. степ. канд. тех. наук. Л.: ЛИ¬ИЖТ. 1986.
- Экономическая оптимизация процесса восстановления профиля поверхностей катания колесных пар обточкой после отжига их при нагреве токами высокой час¬тоты / М.М. Машнев, В.В. Диденко, А.П. Шифман, И.А. Иванов, Алешин// Конст-рукционно-технологическое обеспечение надежности подвижного состава: Сб, статей. — Л.: ЛИИЖТ, 1985. — с. 48-53.
- Иванов И.А., Урушев C.B., Алешин А.Д. Оптимизация параметров режимов цельнокатаных колес //Zeszyty Naukowe Politechiki Slaskiej. Ser. Transport, Z. 15. — Gliwice, 1990. — S. 79-92.
- Макаров А. Д. Оптимизация процессов резания. — M.: Машиностроение, 1976, 276 с.
- Повышение работоспособности колес рельсового транспорта при ремонте технологическими методами/И.А. Иванов, C.B. Урушев, М. Ситаж, A.M. Будю- кин: Под ред. д-ра техн. наук И.А. Иванова. — СПб.: ПГУПС. 1995. — 124 с.
- С.А.Васин, А.С.Верещака, В.С.Кушнер. Резание материалов: Термомеханиче¬ский подход к системе взаимосвязей при резании: Учеб. для техн. вузов.- М.: Изд¬’ во МГТУ им. Н.Э.Баумана, 2001. — 448 с.
- А. с. РФ № 44559 МПК 7 В 23 В 5/23. Станок для обточки колесных пар без демонтажа их с железнодорожного транспортного средства./ Иванов И.А., Соро¬кин П.Г., Воробьев A.A. Зарегистрирована 27.03.05.
- Тепловоз ТЭМ7А Описание электрических цепей /И.А. Федоринов, В.В. Гра¬чев, A.A. Воробьев// Локомотив. 2004. №8, с.36-39.
- Тепловоз ТЭМ7А Описание электрических цепей /И.А. Федоринов, В.В. Гра¬чев, A.A. Воробьев// Локомотив. 2004. №9, с.28-34.
- Тепловоз ТЭМ7А Описание электрических цепей /И.А. Федоринов, В.В. Гра¬чев, A.A. Воробьев// Локомотив. 2004. №10, с.20-24.